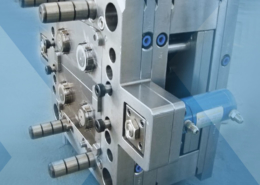
Gas Assisted Injection Molding | Structural Foam Molding - gas assist injection
Author:gly Date: 2024-10-15
We use a range of CNC and manually operated machinery to precision engineer the finished mould. Most of our injection moulds are made from steel, although it’s possible to use aluminium. We start with a solid block of metal (or billet), creating one or more cavities in it using various cutting, milling and eroding tools. These cavities are filled with molten plastic during the injection moulding process.
Toolâs down? We might be able to get it up and about again! Send us some details of your issue or arrange a one-on-one with a tooling technician today.
Have your productâs plastic components mapped out in CAD but scratching your head on how to get the moulds made? Shopped around and found only extraordinarily long wait lists? At NDC Plastic Moulding, youâll find the tooling design and manufacturing services you need to mould your vision on your schedule.
Often, we’ll use a combination of technologies to create custom injection moulds. For example, for optimum results where an extra deep cavity is required, we might opt for spark erosion EDM. This requires machining a custom electrode (often copper) which creates an impression in the billet in its own shape. To engineer the electrode, we might use a combination of CNC milling and wirecut EDM, if any perfectly square corners are required.
Overmolding is a more expensive project due to the two injection processes. Aside from that, insert molding reduces assemblage cost and improves project productivity, especially in high-volume production. They are, however, costlier than injection molding.
The process for designing custom tooling typically involves several stages, including concept development, design and engineering, prototyping, testing, and final production. During the concept development stage, our design team works with the client to identify their specific needs and requirements. From there, weâll create detailed design plans and 3D models, which will be used to create prototypes for testing and refinement. Once the final design has been approved, we’ll manufacture injection moulds ready for mass production.
Insert molding has wide applications due to its advantages. Below are a few reasons you should consider the process for your project.
Both processes are similar. However, there are many differences that you have to take note of before choosing the right one for your project. The overmolding vs insert molding difference entails the following:
Once designs have been finalised for required components, we can begin the precision engineering of your custom injection mould/s (also known as âtoolingâ). Our CNC machining expertise and access to the latest equipment enable us to provide precise, professional tool manufacturing services 100% in-house.
Insert molding is a part manufacturing process applicable in molding plastic over a non-plastic part (usually metal, also known as inserts). The process follows the normal injection molding procedure with the addition of an insert. It involves placing an insert in a mold and injecting molten plastic into the mold. As a result, the insert becomes encapsulated with plastic material. Afterward, ejection occurs.
Has your product design evolved, requiring changes to its components? Slight defect in an otherwise functional mould? Sometimes our masters of mould machining can modify the size and shape of the mouldâs cavities to accommodate design changes, or rectify minor structural issues, avoiding the cost and time involved in starting from scratch.
Overmolding has wide applications due to its advantages. Below are a few reasons you should consider the process for your project.
On the one hand, overmolded parts come from plastic parts that can form chemical bonds with each other. However, not all plastic materials are compatible with each other. For example, ABS is compatible with ABS, Polycarbonate, and Polyethylene but not with POM. On the other hand, most plastic materials are compatible with non-plastic parts. As a result, insert molding has broader material compatibility.
Our custom mould makers take your overall product design, break it down into required components, then create the required CNC-compatible files needed to machine your injection mould. Considering factors like component complexity and scale of production, weâll optimise your tooling to match your manufacturing needs.
Inserts are non-plastic parts that are important in insert molding. They are placed in the mold and injected with plastic material. Most commonly, they are simple objects, e.g., thread or rod. However, they can also be complex, e.g., battery.
Overmolding is suitable for several products. However, it is not suitable for others. Below are a few disadvantages of the process.
Insert molding is common in aerospace, medical, electronic, and defense industries. Common insert molding examples are products such as screwdrivers, spring contacts, clips, and pins.
Once the cavities are created, we’ll carry out manual processes like surface grinding the outer surface of the mould to ensure its completely flat.
Both processes take time. However, insert molding is relatively more time-consuming due to the molding of another layer on the product, i.e., the total product encapsulation of the insert. In contrast, the overmolding injection molding process entails partial encapsulation. Aside from that, insert molding does not require separate production of the two plastic parts, unlike overmolding, which has the substrate and overmold.
The overmolding injection molding process has a wide application (even synonymous to insert molding) in many industrial and commercial industries. Overmolded parts are applicable in the following ways:
Overmolding involves injecting the plastic into a mold to form the first plastic part (also known as the substrate). Then, on solidification, the substrate is placed in another mold and injected with the second plastic material (overmold). Finally, the substrate becomes encapsulated with the overmold. Afterwards, ejection then occurs.
In most cases, yes, we do all the tool design and manufacture 100% in -house. If an especially large injection mould is needed, we may recommend outsourcing to a specialised toolmaker. Our modern toolroom and injection moulding experts are well equipped to handle most tooling requests.
Keynote: Both processes take place simultaneously, i.e., the formation of the substrate and overmold is not separate. This ensures that both plastic materials fuses.
As you can see, tooling design and production demand diverse skills and equipment. With NDC Plastics you can be confident that we’ll devise the most efficient and effect plan for creating custom tooling that meets your specifications and project requirements.
Overmolding is another common injection molding process that involves molding a plastic material over another plastic material. It is a double injection molding process. As a result, it is called two-shot molding.
Overmolding and insert molding are two injection molding processes used in making commercial and industrial products. Both use the same concept, i.e., they involve molding a plastic part over another part. However, both differ regarding the properties and functions of the “other part.” As a result, they have different applications.
The right process between insert molding and overmolding depends on the application. However, it is impossible to choose any for your project. Nevertheless, you can judge from the plethora of insert molded and overmolded parts to determine the right process. Consider the factors below:
Keynote: Ensure you are familiar with many injection molding materials before selecting any process. Better, you should seek the advice of an injection molding service provider on the right material to choose.
Two-shot molding is another name for overmolding. Also known as dual-shot, multi-shot, or double-shot molding, it simply involves simultaneously molding a plastic part (overmold) on another plastic part (substrate). The process takes place simultaneously and allows engineers to create multi-material or multi-colored parts without assembly.
Using the two processes without proper understanding can lead to several adverse effects. Common ones are product failure, wastage of time materials, and increased production costs. As a result, this article does an insert molding vs overmolding comparison to help you choose the right process for your project.
Depending on your project parameters, we can create multiple cavities on the same mould to scale up your output. Employing such efficiency-enhancing strategies means we can measure up to manufacturing metrics more quickly.
Do you need high-quality insert molded or overmolded parts? Let WayKen help you get started. WayKen offers high-quality injection molding services with the help of our experts. Our team can help you choose the best injection molding process for your project. So, you can be confident to get cost-effective and quality molded parts. We also offer other manufacturing services such as CNC machining, vacuum casting, and 3D printing. Upload your design file today to get an instant quote!
Weâre keen to get working on a mould that will go from our toolroom âstraight to the pool room!â Send us a message, give us a call, or arrange a time for an obligation-free consultation with an expert.
Let us write the rules for the tools you need to create custom components. Get in touch or book a meeting with our team.
Overmolding and insert molding are injection processes that use the same concept, i.e., molding a plastic part over another. However, they differed based on processes, cost, speed, and material selection. Before you choose any of them, you need a proper understanding of the process. As a result, this article did an insert molding vs overmolding comparison to help you choose.
The major insert molding vs overmolding difference is the molding process. On the one hand, overmolding is a two-step manufacturing process (hence the name two-shot molding) that involves molding a plastic (overmold) on another plastic (substrate). On the other hand, insert molding involves molding plastic on a non-plastic material. Unlike the overmolding process, it is a one-step manufacturing process (the insert is manufactured separately)
Insert molding can occur in two ways: manual and automated. On the one hand, a manual process is less costly and gives the operator easier control. On the other hand, the automatic process ensures repeatability, reduction of error, and overall production efficiency.
GETTING A QUOTE WITH LK-MOULD IS FREE AND SIMPLE.
FIND MORE OF OUR SERVICES:
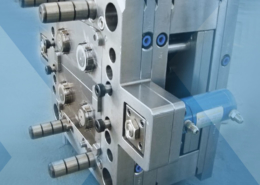
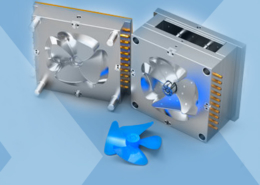
Plastic Molding

Rapid Prototyping
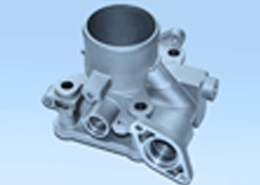
Pressure Die Casting
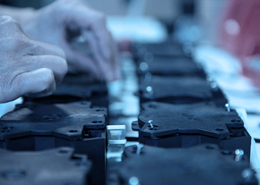
Parts Assembly
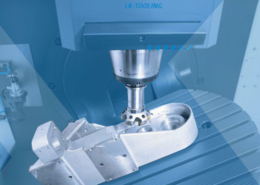