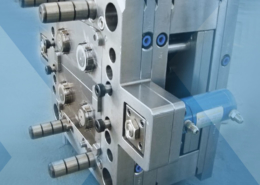
Gas Assist Molding - gas injection molding
Author:gly Date: 2024-10-15
These are general guidelines. Specific requirements may vary depending on factors such as part complexity, production volume and quality standards.
Additionally, the design of the mold and its precise dimensions are crucial for the success of injection molding. PS typically shrinks between 0.2% and 0.8% during cooling. The mold design must account for this shrinkage to ensure the final parts have the correct dimensions.
With the versatility of its craftsmanship, polystyrene injection molding is used to produce a wide range of products. These product categories include disposable cutlery, plastic cups, electronic product casings for food containers, CD cases, and toys. Whether you need to manufacture small and intricate parts or large and simple ones, PS injection molding is a reliable choice that can help you easily achieve your goals.
There are three main types of PS injection molding: general purpose polystyrene (GPPS), high-impact polystyrene (HIPS), and expandable polystyrene (EPS).
The design of the PS mold and its accurate manufacturing are critical to the success of PS injection molding.Making a mold for polystyrene (PS) injection molding involves several key considerations to ensure the process is efficient and the final parts meet the required specifications.
Due to its lightweight, low cost, and ability to be formed into rigid and foam products, PS is extensively used in the packaging industry. This includes food packaging like yogurt containers, disposable cutlery, and foam trays.
However, a problem arises if aluminum is used, as the oxide layer surrounding the aluminum particles can only be removed at extremely high temperatures. At the same time, aluminum has a relatively low melting point, which restricts the maximum sintering temperature. It is therefore impossible to remove the oxide layer on the aluminium powder before the entire metal piece has melted.
For polystyrene injection molding, Jason Mold has extensive injection molding experience, advanced machinery and skilled staff, allowing them to handle both small and large production runs, catering to a wide range of industries.
FowMould is a Chinese plastic mold manufacturer with over 40 years of experience in the injection molding industry. It was established in 1978 and specializes in producing injection molds for various materials, including polystyrene (PS).
Due to its low specific heat, PS can quickly solidify once the mold dissipates heat. Its cooling speed is faster than that of general materials, allowing for an earlier demolding time. Both the plasticizing and cooling times are shorter, resulting in a shorter molding cycle time.
Furthermore, this material can be formulated into transparent, translucent or opaque colors, making it suitable for different applications. With its unique properties, PS plastic has become a popular choice for manufacturing various consumer goods and industrial products.
In the manufacturing of plastic parts, PS injection molding is one of the most popular and efficient methods. The notable feature of this process is that it can produce parts with diverse shapes, precise dimensions, and stable quality.
PS injection molding is a complex process that combines the best of chemistry and engineering to create durable, high-quality products.PS plastics, also known as polystyrene, have unique physical and chemical properties that make them well suited for injection molding.
A solution to this problem has been succeeded in finding now. The key is in creating the correct atmosphere in the sintering furnace. A low-oxygen environment is usually used to prevent the complete oxidation of a metal powder. By contrast, with aluminium, an oxygen-rich atmosphere has been found to be beneficial. The aluminium oxide layer of the particles is so thick that the particles are protected from complete oxidation. At the same time, the oxygen aids the combustion of the carbon contents of the binder material.
Metal injection molding (MIM) is to uniformly mix the powder and the binder, and then the mixture is granulated by a granulator and then injected into a forming mold cavity to complete the desired shape. The mixed melt has good fluidity after heating, which aids in the forming of the product during injection and maintains the density uniformity of the product. The shaped product also needs to be degreased and then sintered in a sintering furnace, and some products need some post-treatment such as tapping, polishing and coating.
In conclusion,polystyrene (PS) injection molding is a versatile manufacturing process that is widely used for packaging, consumer products, electronics, medical devices, insulation, and automotive parts due to its cost-effectiveness, ease of processing, and a variety of properties such as transparency and durability.
Polystyrene, commonly known as PS, is a plastic material widely used in the injection molding process. It is a cost-effective and versatile thermoplastic that can be molded into various shapes and sizes. Due to its durability and ease of processing, PS plastic is extensively used in disposable tableware, containers, packaging materials, and other products.
At the same time, PS injection molding can accurately replicate complex geometric shapes, making it an ideal choice for manufacturing complex polystyrene parts. This is particularly applicable in industries such as electronics, automotive, and consumer goods that require complex and high-precision components.
Polystyrene can be made into a transparent material, similar to glass. Customers have the option to choose from various finishes, colors, and textures to achieve their desired appearance. General-purpose polystyrene has lower impact resistance, but in high-impact polystyrene (HIPS), its impact resistance can be significantly improved by blending it with polybutadiene during the PS injection molding process.
One of the main purposes of PS injection molding is to be able to produce parts or products in large quantities. Polystyrene is particularly suitable for this purpose because it is relatively inexpensive and easy to mold.
One of the essential components of PS mold making is the selection of the right material. The type of material used can significantly impact the final output quality and performance.
In this blog post, we will provide a detailed introduction to the characteristics of PS materials, the specific process and molding conditions of PS injection molding. This will help you gain a deeper understanding of the widespread application of PS injection molding in injection mold manufacturing.
Polystyrene (PS) is a widely used plastic material due to its combination of strength, durability, and cost-effectiveness. It finds extensive applications in various fields.
Plastic injection molding is a versatile manufacturing process that has been widely used in various industries such as automotive, medical, consumer goods, and packaging.
General-purpose polystyrene has a transparent, glass-like appearance and is commonly used in laboratory vessels and medical equipment such as petri dishes, test tubes, and diagnostic components.
Polystyrene usually has a melt temperature between 180°C and 270°C. It’s important not to exceed this range as it can cause the material to degrade.
The company offers a comprehensive service, from product and mold design to manufacturing, testing, and shipping. They have a reputation for high-quality molds, fast delivery, and excellent customer service.
Meanwhile,polystyrene is a commonly used material in the automotive industry, used to manufacture various components such as dashboards, knobs, interior decorative parts, and energy-absorbing parts. By using polystyrene injection molding, manufacturers can produce these components with high precision and efficiency, ensuring top-notch product quality.
While there are many plastic materials available for selection, few can match the unique performance and manufacturing advantages offered by PS.
Polystyrene injection molding is a process of injecting molten polystyrene into a mold under high pressure, allowing the material to cool and solidify inside the mold, resulting in a strong and uniform product.
Since the injection process is performed under precise temperature and pressure, the formed product has extremely high precision and a very uniform density. Aluminum alloy injection molding technology can process and produce extremely complex parts, with a minimum of 0.1g of small parts; the products has uniform structure, high accuracy and smooth surface; Moreover, the product quality is stable and the production efficiency is high, which is suitable for mass production.
The density of polystyrene is relatively low, ranging from 1.04 to 1.06 g/cm³, and it has a low melting point which makes it easy to liquefy. Therefore, PS injection molding is an ideal choice for creating lightweight objects and is suitable for applications with high weight requirements.
The mold temperature for polystyrene typically ranges between 20°C and 70°C. The exact temperature depends on the specific type of PS used and the desired properties of the final part.
Each PS plastic has unique properties that make it popular for a variety of applications in a wide range of industries. Injection molding technology can accurately and quickly produce these types of PS plastics, making them a readily available material for a variety of uses.
This advanced technology is suitable for the production of large-volume, complex parts, including some extremely complex three-dimensional shapes, and the products produced do not require machining or only a small amount of processing, which greatly reduces the production cost and greatly improves the work efficiency.
Therefore, it is necessary to look for a good and reliable PS injection molding company to determine the best approach for your specific application.
JasonMould Industrial Company Limited, established in October 2010, is a larger scale private manufacturing enterprise with perfect management system, precision molds and plastic products with domestic and foreign famous customers.
After this first step, the oxygen atmosphere is replaced by nitrogen and the temperature is increased further. With the additional help of magnesium, the aluminium oxide layer is finally broken and reduced. A liquid phase occurs and the aluminium particles are sintered to form a solid metal piece. This method allows to separate the two process steps; the removal of carbon residue and the sintering of the aluminium particles, thereby enabling both steps to run to completion for the first time.
Aluminum alloy injection molding (AIM) is a new type of aluminum alloy forming technology. It is similar to metal injection molding (MIM) technology, which is the main branch of powder injection molding (PIM) technology. It is developed from injection molding technology and will be the fastest growing and most widely used near-net-shape processing technology of aluminum alloy parts in the world.
Deep Mold provides comprehensive and complete project management from concept to prototyping to product, for PS injection molding, and their team has extensive manufacturing experience to deliver quality injection molded products.
Unlike other common plastics, polystyrene has a lower melting point, making it easier to mold. The injection molding process for PS can produce high-precision and repeatable parts with minimal waste.
Klarm Corporation is a professional plastic injection molding manufacturer to meet the needs of micro and macro molding manufacturers. Located in Guangzhou, China, the company provides quality injection molding services to customers worldwide.
The Powder Injection Molding process enables complex shapes to be manufactured, which cannot be realised in any other way, or only with great effort. The aluminium powder is relatively inexpensive, which means that even large components, by MIM standards, can be produced at a reasonable cost. In mass production, savings of up to 50% can therefore be expected on materials and weight compared with conventional production.
In addition to its excellent molding capabilities, PS also exhibits outstanding impact resistance and temperature resistance. These properties make it the preferred material across industries.
Polystyrene exhibits low to moderate shrinkage during cooling, typically around 0.2% to 0.8%. This factor needs to be considered during the design of the mold to ensure the final part meets the desired dimensions.
Deep Mould Co. LTD was founded in 2008, it is one of the best toolings manufactures in Dongguan, China.Deep Mould specializes in high-quality tooling area.
Polystyrene, or PS, is a common type of plastic material that has a range of uses due to its unique properties. Each of these has distinct properties that make them suitable for various applications in different industries.
This makes it an ideal material for manufacturing a wide range of products, from consumer electronics to medical devices, as well as toys and food packaging.
Polystyrene is a commonly used material in the manufacturing industry, widely applied to various consumer goods such as kitchen appliances, toys, and garden furniture. It can be molded into different shapes and sizes according to specific purposes, making it the preferred choice for many manufacturers. For products that require higher durability, high-impact polystyrene (HIPS) is usually chosen.
Polystyrene has good flowability, so the required injection pressure is generally lower compared to materials with higher viscosity. Typical injection pressures range from 70 to 150 MPa.
In recent years, PS injection molding has become an economically efficient method that can mass-produce identical parts with consistent quality. It is widely used in various industries such as automotive, electronics, and medical equipment manufacturing.
FOWMould, as a leading company in China’s injection molding industry, offers one-stop plastic injection mold services from mold design to manufacturing.
Because aluminum alloy injection molding has incomparable advantages in accuracy and efficiency, the low density of aluminum makes it of particular interest for many applications, it has been applied in many industries such as navigation, aviation, machinery, automobile, precision instruments and so on. With the continuous development of machinery industry, AIM has become the fastest growing near-net-shape processing technology of aluminum alloy parts in the world, and has been favored by more and more industries, where weight reduction is important.
Through the use of PS injection molding technology, these plastic materials can be molded into complex shapes and sizes for various purposes such as food packaging, electronic casings, and medical devices. Understanding the differences between each type of PS plastic material can help industries and consumers choose the most suitable material for their needs.
Another key point to consider is gate design.The gate is the point where molten PS enters the mold, and it can be designed as flat side gating, direct gating, fan-shaped gating, or circular overflow gating.
UP MOLD is a manufacturer specializing in the custom production of plastic injection molds and injection molded products for electronic engineering and household appliances. The company’s core business strategy is to provide one-stop and comprehensive services for product development, design, mold making, molding, assembly and packaging
PS injection molding is widely used in various industries such as automotive, pharmaceuticals, and packaging. With its efficiency, cost-effectiveness, and flexibility, PS injection molding has become an indispensable part of countless product manufacturing processes that we rely on daily.
Upmold has a team of experienced professionals to create high quality products for our customers. In addition to the technical force, the company also has high-precision and large-scale production facilities. upmold has a manufacturing center in China and an injection molding plant in Indiana, USA.
In addition, the gloss of PS products increases with the increase in mold temperature, with internal stress of the rubber parts can be immersed in 65 ~ 80 ℃ water tank for 1 ~2 hours, and then slowly cooled to room temperature, you can eliminate internal stress.
In the field of PS injection molding, FOWMould has abundant experience and mature technical expertise to deliver the highest quality PS injection molded products. If you require injection molding services, FOWMould would be your ideal choice.
However, in order to ensure the quality of the final product, it is necessary to carefully control certain conditions and make corresponding adjustments during the PS injection molding process, in order to produce high-quality plastic parts that meet customer requirements.
One of the most commonly used methods for producing PS plastic products is PS injection molding, which involves melting the material and injecting it into a mold to create various shapes of products.
ACIS®, Autodesk Inventor®, CATIA® V5,Creo™ Parametric, IGES, Parasolid®, Pro/ENGINEER®,Siemens PLM Software’s NX™, SolidEdge®, SolidWorks®, STEP
The melting point of PS is 166℃, and the recommended processing temperature is generally between 185-220℃. The decomposition temperature is approximately 280℃, so its processing temperature range is relatively wide.
The binder material, which bonds the metal powder in the MIM feedstock, is also removed by thermal processes, which only occur at increased temperatures. The overlapping of the temperature ranges for binder removal and sintering means that residues of the binding agent are incorporated into the sintered workpiece if aluminium is processed using the same technique as for other metals.
With over 11 years of experience and state-of-the-art molding equipment, we specialize in the manufacture of precision tolerance molds and large, complex injection molds for automotive, electronics, telecommunications, medical devices, home appliances, sporting goods, and general industrial OEM/ODM applications.
PS has a moderate tensile strength in the range of 35 to 55 MPa.Its flexural strength typically falls between 60 to 105 MPa, which indicates the material’s ability to resist deformation under load.
GPPS, also known as crystal polystyrene, is transparent and is commonly used in packaging and disposable tableware.HIPS has greater impact resistance and is commonly used in toys, appliances and electronics.EPS has a foam structure and is ideal for insulation, packaging and cushioning.
When melting PS, it is important to consider its relatively low viscosity and good flowability. The mold must be carefully designed and sealed to prevent leakage.
Due to the controllability of the PS injection molding process, it can produce highly consistent parts. This is crucial in many industries with strict requirements for quality and dimensional accuracy.
GETTING A QUOTE WITH LK-MOULD IS FREE AND SIMPLE.
FIND MORE OF OUR SERVICES:
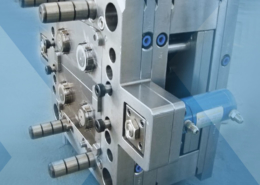
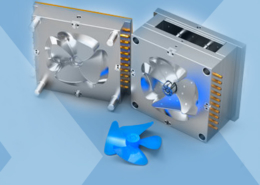
Plastic Molding

Rapid Prototyping
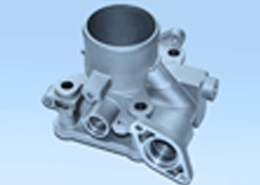
Pressure Die Casting
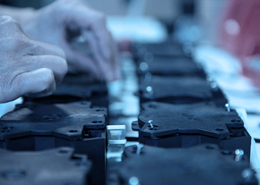
Parts Assembly
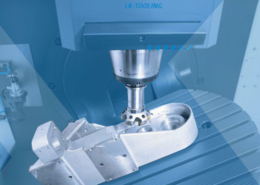