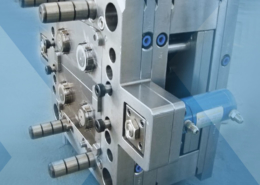
Gas Assist Injection Molding - gas injection molding
Author:gly Date: 2024-10-15
Two-component or three-component moulding in order to obtain products with different materials by colour or type of polymer. This technology for printing multi-material components is particularly used in the automotive industry for the production of lights, door panels, integrated gaskets.
Automotive is a very complex plastic moulding sector, where only technologically advanced companies can supply high-quality components required by the most prestigious car manufacturers. Thanks to the know-how acquired through years of experience and its highly qualified staff, MPS is an ideal partner for companies in the Automotive sector, in which strict quality standards and an efficient company organization are required.
Each cavity of this cap mold is designed with separate inserts, so that each cavity product in the process of injection molding maintain the same injection molding pressure, clamping force and other molding conditions, so that the product quality is more stable and reliable. Moreover, the independent insert design can make the life of the mold longer. If there is any problem with the parts, the parts can be directly replaced without affecting the production schedule.
VDA product audits are carried out regularly in different levels and samples are created according to PPAP and IMDS requirements, thanks to a team of operators that constantly stay up-to-date and care even for the most demanding requests of our customers. We are equipped with presses of the most important and recognized makes in the automotive world, such as Engel, equipped with rotary tables for the moulding of 2 or 3 components up to 800 tons. Special 2k moulding up to 2500 tons with integrated auxiliary injectors. Piece handling is carried out by Cartesian and anthropomorphic robots that allow post-moulding operations of extreme precision and repeatability.
Once again Focare Mould has successfully made another two-color flip top injection mold. It is really difficult to make two-color flip top cap mold especially for 16 cavities. Especially, the diameter of two-color cap is only 20mm and the connection between two materials is so tiny. It is arduous to adjust the connection well completely for 16 cavities. In order to achieve this goal, we must not only have professional mold technology, but also have technical injection molding skill. Focare Mould has its own team in mold design, mold making and injection molding. We have two sets of two-color injection molding machines which permit us to test two-color injection molds and help to train our customers’ engineers when it is necessary.
Plastic liquor caps are different from the ones we usually use. They are not sealed by threads or barbs like plastic caps of mineral water bottles, but by oak plugs. However, the oak plugs may cause decay or cracking after long-term and long-distance transportation or weather, plastic caps are needed to keep them sealed and protect oak plugs.
Most of the plastic flip top caps mould are designed with two-time ejection structure. The core is pushed out two times. The stripper plate and the ejector sleeve in the middle of the product are pushed out together to 14mm, and then the stripper plate push out continually until the flip top caps drops.
The general water bottles are round and sometimes take space in the bags, but these water bottles are square. If they are placed properly, they can save a lot of space inside your bag.
Spray cap molds are used in the molds for producing insecticide shells. They are made in accordance with the shape of the insecticide cover required. They are injection molded with plastic and processed into insecticide shell parts through various processes. The principle of the spray tank is that the liquid is pressed out of the valve by using air pressure. The liquid can be sprayed evenly. The direction and dose can be controlled. Any content can be easily put in and easy to use.
The plastic raw material of 5G cap is LLDPE, which has high gloss, high heat resistance and better fluidity than the general materials. In addition, the steel of mold core and cavity is S136, with a hardness of 48-52, which can better for mold life. It could be design with 12 cavities or 16 cavities, each cavity has its own independent cooling system to ensure that the products can be better shaped and cooled.
The unscrewing device of this cap mold is hydraulic motor. The ejecting sequence of this cap mold is to let the upper press plate open the mold first, and rely on the I-shaped block to drive the cavity slider to slide away. The mold is opened to a certain stroke, and the caps will be unscrewed by hydraulic unscrewing motor. The left and right thimble plates are performed simultaneously. The spring is pushed out of the barrel by the force of the spring, so that the product is firmly in the core part. After opening the mold, the oil cylinder pushes the rack, drives the central drive shaft, drives 4 product threaded shafts backward to disengage the product, and then relies on the 2 ejector rods on the outside of the machine, and the ejection plate pushes caps off from mold.
The use of 18 presses ranging from 120 up to 2500 tons satisfies the need both for small and large batches of production and, with the help of anthropomorphic and cartesian robots, we carry out automatic palletizing. Furthermore, metal details can be inserted on request.
GETTING A QUOTE WITH LK-MOULD IS FREE AND SIMPLE.
FIND MORE OF OUR SERVICES:
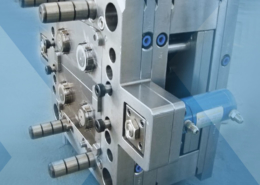
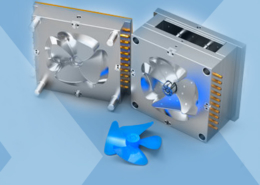
Plastic Molding

Rapid Prototyping
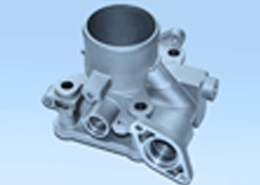
Pressure Die Casting
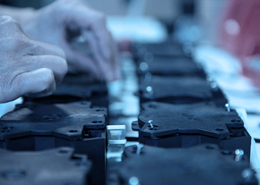
Parts Assembly
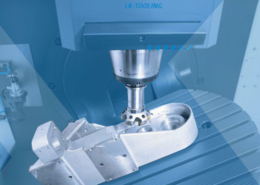