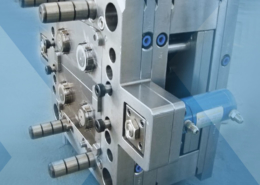
Flexible Plastic Tubing & Injection Moulding - flexible injection molded plastic
Author:gly Date: 2024-10-15
Medical devices must adhere to strict regulatory requirements set by health authorities, such as the United States Food and Drug Administration (FDA) or the European Medicines Agency (EMA) in the European Union. Compliance with relevant standards is vital in securing regulatory approvals, certifications, and market clearance for these devices.
Liquid Silicone Rubber (LSR) Molding: Liquid Silicone Rubber (LSR) molding is a commonly used manufacturing technique for producing medical products that require biocompatibility, flexibility, and heat resistance. It involves injecting liquid silicone into a mold cavity and curing it to create a solid, elastic component. Some examples of medical applications using LSR molding include the production of medical-grade seals, gaskets, and silicone catheters.
Pauline, injecting wax should be easier than plastic. With the much lower melting point, your mold will experience much less stress, should last longer, and not require as much engineering consideration.
Plastic injection molding for medical parts requires materials that adhere to strict regulatory and safety standards, while also possessing the required properties for specific medical applications. Here are several commonly employed materials in plastic injection molding for medical components:
In the field of manufacturing, plastic mold injection stands out as an economically viable method. It proves to be cost-effective when producing medical devices in large quantities. This advantageous technique enables a seamless increase in production without compromising on quality. Consequently, it promotes greater accessibility to essential medical equipment worldwide, ultimately reducing healthcare costs and enhancing patient care on a global scale.
ISO standards, with ISO 13485:2016 and ISO 9001:2015 being particularly significant, govern the quality management systems for medical devices. When manufacturers comply with ISO standards, they adhere to globally recognized best practices that include risk management, traceability, and process validation.
I sent in a ticket to Formlabs and they are checking for me to see if there would be a reaction between Polyurethane resin and the Formlabs resin as I was thinking of using the tough or Flexible resin as a Mold and just pour in the Poly replacing the need for Silicone Molds. (I use Smooth-On 321 and a few others) If a person can get more then 50 parts from a printed mold this may be a viable alternative. Main reason I am thinking is I do a lot of thin parts and experience a lot warping whereas a printed mold can have a thicker outer wall thus eliminating the warping. Here is a couple of screen shots of one of the items what I make for the hobby industry.
Standards serve as essential guidelines for the manufacturing process, materials used, and quality control procedures of medical devices. Adhering to these standards ensures consistent and dependable production, maintaining a high level of product quality. The importance of consistency becomes paramount in mass production scenarios, where it guarantees that every device performs reliably and consistently.
Plastic injection molding supports a wide range of medical-grade plastics, each with unique properties suitable for various medical applications. These materials offer tailored solutions to cater to different medical needs, ranging from biocompatible options for implants to transparent plastics used in medical packaging and durable polymers utilized in surgical tools. The versatility of the materials enables healthcare professionals to address specific requirements effectively.
How difficult would it be to DIY rapid injection mold (plastic parts)? My understanding is that rapid injection molding means injecting hot plastic into a mold which was 3D printed. Seems this would be possible with a machine like this:
3D printed molds can be used for injection molding low-volume production plastic parts. Learn how with the Formlabs white paper.
Two-Shot Injection Molding: Two-shot injection molding, also referred to as overmolding, combines two different materials into a single mold. This technique enables the production of medical devices with multiple colors, textures, or material properties within one manufacturing cycle. It finds common application in creating ergonomic grips for medical instruments and incorporating soft-touch components onto rigid devices.
Polypropylene (PP): Polypropylene is a thermoplastic material known for its versatility. It offers excellent chemical resistance and boasts a low density. This makes it highly suitable for various medical applications including syringes, test tubes, and medical packaging.
Hand operated injection molders for DIY injection molding. Ideal for R&D, materials testing, STEM programs. 3D print your own molds.
Definitely interested to see how others want to push this forward and try more elaborate things so please share your results on the forums! Happy to talk more about your specific application if you need any help figuring out the best approach.
I made the mistake of not releasing my first mold for simpact because I’d molded silicone parts a bunch of times in printed molds, and they came right out. With simpact, and no release agent, I had to basically break the mold off with a hammer!
Plastic injection molding simplifies the process of creating prototypes, allowing medical professionals and manufacturers to swiftly refine their designs. This speeds up the development cycle, resulting in quicker market entry for new medical devices and equipment.
Complying with FDA regulations and ISO standards is vital in medical injection molding. This ensures the safety, effectiveness, and quality of medical devices and components. The U.S. Food and Drug Administration (FDA) regulates medical devices under the Federal Food, Drug, and Cosmetic Act (FD&C Act). Manufacturers must adhere to the FDA’s Current Good Manufacturing Practices (CGMP) requirements. These guidelines cover various aspects including design, manufacturing, labeling, and quality control.
The injection molding process ensures an exceptional level of consistency in the final products. Each molded part exhibits near-perfect similarity, thereby minimizing variations and mitigating the risk of defects. This unwavering consistency proves to be crucial, particularly in medical applications where precision and utmost quality play a pivotal role in ensuring patient safety and reliable performance.
To ensure regulatory compliance, you must adhere to applicable standards like ISO 13485. This involves rigorous testing and documentation of the manufacturing process. Additionally, seeking necessary approvals from health authorities such as the FDA is essential for entering the global market.
Standards often require manufacturers to maintain proper records and traceability throughout the manufacturing process. This involves documenting details such as materials used, manufacturing procedures, inspections conducted, and testing outcomes. Comprehensive documentation is essential as it facilitates actions like product recalls, investigations, and quality audits if necessary.
I made a big gasket for my champaign bucket vacuum chamber using a four-section printed mold. IMG_20150521_161846.jpg3264×2448 1.54 MB IMG_20160902_225718.jpg2448×3264 1.06 MB I’ve since added another stick-on seal to the urethane, as busting it out of the mold was not too kind to it, and it had a couple rough spots that leaked a bit…
Due to the delicate nature of medical devices, the medical industry uses various intricate injection molding techniques alongside conventional ones. These include micro injection molding, two-shot injection molding, Liquid Silicone Rubber injection molding and reaction injection molding.
Plastic injection molding has several benefits. However, it is important to note some limitations, including design complexity, high initial tooling costs, and material selection challenges for specific medical applications.
Polyethylene (PE): Polyethylene, a commonly used thermoplastic material in the medical industry, offers excellent biocompatibility, flexibility, and chemical resistance. It finds extensive applications in medical tubing, bags, and containers.
Liquid Silicone Rubber (LSR): LSR is a biocompatible and flexible material that is extensively used in injection molding for various medical parts. It is particularly suited for applications that need soft-touch properties like gaskets, seals, and medical implants.
This can save you a boatload of cash if you don’t need parts that are extra rigid or fiber reinforced. It’s urethane so it’s reasonably safe to work with also.
Polyethylene Terephthalate (PET): PET is a durable and see-through thermoplastic material that has widespread use in the field of medical packaging. It is commonly used for creating blister packs and medication bottles.
International standards, like ISO 13485 (Medical Devices – Quality Management Systems), hold global recognition. Adhering to these standards allows medical device manufacturers to expand their market reach since numerous countries require compliance with internationally recognized benchmarks for importing and distributing products.
Thermoplastic Elastomers (TPE): TPEs, or thermoplastic elastomers, are a versatile family of materials that possess the combined properties of rubber and plastic. These unique materials find extensive usage in various medical applications where flexibility is crucial. They are commonly employed for creating grips, seals, and medical tubing.
Reaction Injection Molding (RIM): Reaction injection molding involves the use of a reactive liquid mixture that undergoes polymerization and solidification inside a mold. This method, often referred to as RIM, is commonly employed for manufacturing robust and impact-resistant medical equipment and components. Examples include wheelchair parts and housing for medical devices.
Plastic mold injection is a precise and efficient process used to manufacture complex medical components and devices. It involves injecting molten plastic into a pre-designed mold. This technique enables the creation of intricate and customized products that meet the specific requirements of medical applications. From simple syringes to sophisticated surgical instruments and implantable devices, plastic mold injection plays a crucial role in producing high-quality medical equipment.
Yes it can be done. How difficult? No clue, but let us know if you try!! I assume outsourcing to someone like Fathom who already has this set up would be a good use of outsourcing. If you think you will be doing this sort of development a lot though, then I am sure bringing in a manual machine would be beneficial. I wouldn’t expect it to be as plug n play as a Form 2 though.
The production time for a custom-made medical device using plastic injection molding can vary based on the complexity and volume. Typically, it ranges from a few weeks to a few months.
Plastic injection molding offers many benefits for medical applications, making it the preferred manufacturing method for producing medical devices and equipment. Here are some of the key advantages:
The medical industry’s integration of plastic mold injection technology has produced numerous advantages that surpass conventional manufacturing methods. This innovative technique facilitates rapid prototyping, reducing the time required for product development and enhancing the efficiency of the design process. This means that medical professionals can promptly refine and optimize their product designs, ultimately leading to safer and more effective medical solutions.
Standards in plastic injection molding establish the specifications and requirements that medical devices must meet to ensure patient safety. Complying with these standards minimizes the risk of defects, malfunctions, and adverse events, guaranteeing that medical devices perform as intended and do not endanger patients.
Many plastics used in medical-grade injection molding are designed to be compatible with the human body, ensuring safety. Additionally, these materials can withstand various sterilization processes without compromising their properties. This guarantees that medical devices remain hygienic and safe for patient use.
I’m thinking this would be helpful to do in-house, after functional prototype tests and before short runs with a service like QuickParts or ProtoLabs. I think I’ve only seen one example of this with a Formlabs printer:
Yes. Plastic injection molded parts find widespread usage in surgical procedures. They are essential components of surgical instruments, implantable devices, and various medical equipment.
I’ve molded smooth-on simpact urethane resins (Shore A 60 and 85 IIRC) in printed molds before. You MUST really, really, really release them well prior, polish up the released surfaces with a soft cloth, and re-release/polish before every pour.
Plastic injection molding is a highly efficient process for producing intricate and complex medical components with exceptional precision. By using accurately designed molds, the manufacturing of medical devices can achieve tight tolerances and intricate geometries while ensuring adherence to exact specifications.
Standards in plastic injection molding for medical devices play a crucial role in guaranteeing the safety, quality, and reliability of medical equipment used in healthcare settings. When it comes to medical applications, where patients’ lives and well-being are at stake, adhering to high standards becomes essential. Some key reasons why these standards are indispensable in the field of plastic injection molding for medical devices include:
Plastic injection molding provides design flexibility, enabling medical professionals and engineers to develop innovative and user-friendly medical devices. By incorporating textured surfaces, grips, and multi-component assemblies, it enhances the usability and performance of medical products.
Standards play a vital role in providing clear guidelines and fostering innovation. By establishing frameworks for new technologies and materials, they create opportunities for manufacturers to push the boundaries of medical device development while still adhering to the set standards.
Micro Injection Molding: Micro injection molding is a process used to create highly precise and tiny medical components, often with features that are smaller than a millimeter. This technique finds its strength in manufacturing miniature medical parts like microfluidic devices and micro-needles. The production requires specialized equipment and precision tooling to attain the desired outcomes.
Compliance with regulations and standards is crucial for medical injection molding companies seeking FDA approval or clearance for their devices. It not only enables market access but also builds trust among healthcare professionals and patients. Adhering to these guidelines allows companies to reliably produce safe and high-quality medical products, enhancing patient care and the overall healthcare sector.
Polycarbonate (PC): Polycarbonate, a durable and transparent thermoplastic material, finds widespread application in the medical industry. Its remarkable impact resistance and optical clarity make it ideal for medical device housings, connectors, and containers.
Standards play a crucial role in ensuring the safety of medical devices during their design and production phases. Manufacturers are obligated to carefully assess potential risks associated with their products and take proactive measures to minimize them. This diligent approach not only helps prevent any hazards but also safeguards patients from potential harm.
Once the initial mold is created, producing medical devices in large quantities significantly reduces the cost per part. This cost-effectiveness has numerous advantages for both healthcare providers and patients as it enhances accessibility and affordability of these devices.
it’s surprisingly easy for small parts! We just finished up a collaboration with Galomb Inc and shared our findings in the whitepaper which went out today.
Home Injection Molding: This Instructable explains how to make real injection molded plastic parts using a simple hand-operated machine. I realize most of you reading this don't have one of these machines, but I decided to post here anyway just to...
Wow, great replies! Thanks everyone. Looks like my timing was perfect too, seeing as the white paper was release just days later.
Injection molding often produces fully formed parts without needing additional assembly or secondary operations. This streamlined manufacturing process minimizes the risk of contamination and human error during assembly, making it more efficient and reliable.
Plastic mold injection has revolutionized various industries, including the medical sector. This innovative technology has transformed the production of medical devices and equipment, bringing about significant benefits that have reshaped healthcare practices.
It is not difficult to do the injection molding - you can see this under https://plasticlabs.wordpress.com/2016/09/06/how-to-bring-a-3d-printed-2-cavity-injection-mold-to-life-part-1/
In the medical industry, seamless collaboration between different devices and components is crucial. Standards play a vital role in ensuring that medical devices are designed and manufactured with compatibility and interoperability in mind. This approach simplifies the integration of these devices into existing systems and workflows for healthcare professionals.
Environmental concerns can arise due to the generation of plastic waste during manufacturing. To avoid this, manufacturers should adopt recycling and sustainable practices in order to minimize their environmental impact.
GETTING A QUOTE WITH LK-MOULD IS FREE AND SIMPLE.
FIND MORE OF OUR SERVICES:
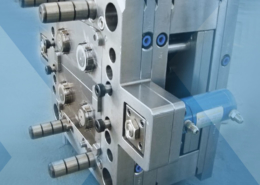
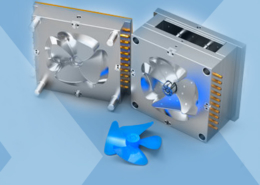
Plastic Molding

Rapid Prototyping
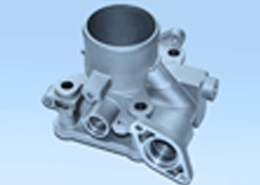
Pressure Die Casting
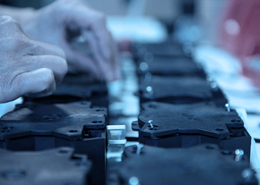
Parts Assembly
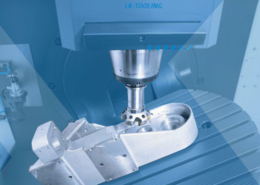