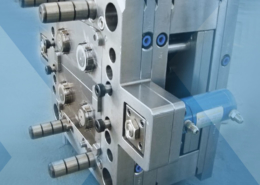
ferromatik milacron europe elektra 300 - Maszyneria - milacron injection molding
Author:gly Date: 2024-10-15
Our helpful design aid demonstrates part features that are too thin or too thick, bad bosses, right and wrong ribs, and other considerations to be mindful of while designing parts for injection molding.
HDPE is a versatile material that is used in a wide range of applications across various industries. Some common uses of HDPE include:
HDPE molding offers several advantages over other manufacturing processes. It allows for the production of complex designs and intricate shapes with high precision and consistency. It also offers high production rates and is ideal for large volume production runs. Additionally, HDPE molding is a cost-effective process, as it can reduce material waste and labor costs. 1.Versatility: HDPE is a versatile material that can be molded into various shapes and sizes, making it suitable for a wide range of applications. 2.Strength and durability: HDPE has a high strength-to-density ratio, making it strong, durable, and able to withstand harsh environments. 3.Chemical resistance: HDPE is highly resistant to chemicals, making it suitable for use in corrosive environments. 4.Recyclability: HDPE is recyclable and has a low environmental impact, making it a popular choice for sustainable manufacturing practices. 5.Cost-effective: HDPE injection molding is a cost-effective manufacturing process, allowing for the production of high-volume runs of identical parts.
HDPE injection molding has a wide range of applications due to the unique properties of HDPE plastic. Some of the common applications of HDPE injection molding include:
Sungplastic providers that offer custom HDPE plastic parts services. Our company uses HDPE injection molding to produce custom plastic parts according to our customers’ specific requirements.v. Here are some of the steps involved in custom HDPE plastic parts service:
The manufacturing process for molded parts is complex. Before your parts are even molded, we're there to help you with comprehensive manufacturability feedback and consultative design services, so you can avoid mold design pitfalls before the resin hits the mold. From there, our production process is documented and optimized using scientific molding so you get high-quality parts consistently and reliably with every production run.
It has been very enlightening to us here at HP that we are able to get parts so rapidly out of the actual materials that we're going to use in the final production.
Want to learn more about injection molding? Sign up to receive a Design Cube. This physical aid demonstrates how to properly design features commonly found on molded parts.
Sungplastic is a reputable manufacturer of high-density polyethylene (HDPE) injection molds and provides comprehensive HDPE injection molding services. Our experienced team of engineers and technicians work closely with our customers to understand their unique needs and provide solutions tailored to meet their specific requirements. We use cutting-edge technology and equipment to design and produce high-quality HDPE injection molds, consistently delivering reliable results. In addition to mold production, we also offer POM injection molding services that include the production of finished POM products such as gears, bearings, and other precision components. Our wide range of injection molded parts caters to various industries. At Sungplastic, we prioritize providing the highest quality products and services. We have strict quality control measures in place to ensure that every product leaving our facility meets the highest industry standards. Furthermore, we offer competitive pricing, guaranteeing our clients the best value for their investment. As your trusted partner for injection molding needs, Sungplastic is committed to excellence and customer satisfaction.
Custom HDPE plastic parts service providers typically work closely with our clients throughout the entire process to ensure the finished part meets their specific requirements. We provide additional services such as material selection, design optimization and prototyping to help customers achieve the best results.
High-density polyethylene (HDPE) is a type of thermoplastic polymer made from the monomer ethylene.It is a versatile material commonly used in the manufacture of a variety of products. HDPE is known for its high strength-to-density ratio, making it lightweight, strong, and durable.HDPE also has excellent chemical and weather resistance, making it suitable for use in severe environments. HDPE is a recyclable material with low environmental impact, making it a popular choice for sustainable manufacturing practices.
Injection molding is a manufacturing process that consists of filling a metal mold cavity with liquid plastic resin, which then cools and forms a plastic part.
While the molds themselves are similar, part quantities, lifetime maintenance, quality documentation, and pricing vary depending on which service option is chosen. The right one depends on your project needs.
We offer a variety of manufacturing services: Rapid Prototyping, Tool Making, Injection Molding, Product Design and Development, CNC Machining and Metal Stamping. You can choose from a variety of plastics, silicone rubber, or metal for your product. Regardless of mass production or small batch customization, Sungplastic has always been committed to providing assured, efficient and more economical one-stop processing services for your projects.
Depending on your application's requirements, you can choose from the following when requesting an injection molding quote.
We have wide selection of more than 100 thermoplastic and thermoset materials. And if you're looking for alternative material options, check out our guide to resin substitutes for ABS, PC, PP, and other commonly molded plastics.
There are various types of HDPE plastics that are used for different applications, each with their own unique characteristics. Here are some of the most common types of HDPE plastics and their applications:
By following these best practices, you can achieve high-quality HDPE injection molded parts with consistent properties and performance.
HDPE injection molding is a manufacturing process that involves injecting molten HDPE material into a customized mold cavity. The molten HDPE material is then cooled and solidified,producing precise and high-quality plastic parts. HDPE injection molding process is known for its cost-effectiveness, speed, and ability to produce complex shapes and designs with high precision and consistency.
In summary, the various types of HDPE plastics have different characteristics that make them suitable for specific applications. HDPE HMW, Marlex 9006, DOW DMDA-8007 NT 7, and DOW DMDA-8907 NT 7 are all high-density polyethylene (HDPE) resins. They are commonly used in injection molding and blow molding applications due to their excellent processability, impact strength, stiffness, toughness, and environmental stress crack resistance (ESCR).
Proto Labs, Inc. 5540 Pioneer Creek Dr. Maple Plain, MN 55359 United States P: 877-479-3680 F: 763-479-2679 E: [email protected]
Sungplastic is a plastic product manufacturer with rich experience in injection molding. According to the different product development requirements, we flexibly adjust the manufacturing process to achieve high quality, high efficiency and more economical.
No one ever said that designing and manufacturing molded parts was easy. Our goal is to get you through it quickly and with quality parts. A good starting point is our Design for Moldability Toolkit.
HDPE injection molding is a versatile manufacturing process that can be used to produce a wide range of plastic products with excellent properties and performance.
Our plastic injection molding process produces custom prototypes and end-use production parts with lead times as fast as 1 day. We use aluminum molds that offer cost-efficient tooling and accelerated manufacturing cycles, and stock about 200 different thermoplastic resins.
Resin pellets are loaded into a barrel where they will eventually be melted, compressed, and injected into the mold’s runner system. Hot resin is shot into the mold cavity through the gates and the part is molded. Ejector pins facilitate removal of the part from the mold where it falls into a loading bin. When the run is complete, parts (or the initial sample run) are boxed and shipped shortly thereafter.
There is no doubt that HDPE (High-Density Polyethylene) can be injection molded. In fact, injection molding process is one of the most common and widely used methods for manufacturing HDPE products. HDPE is a popular choice for injection molding due to its excellent strength-to-density ratio, chemical resistance, and ability to be molded into complex shapes with high precision and consistency. The process is also cost-effective, efficient, and capable of producing high-volume runs of identical parts. In short, HDPE injection molding is a versatile and efficient manufacturing method that is commonly used to produce a wide range of products, including packaging, automotive parts, medical devices, and more.
A: The most common types of HDPE molding include injection molding, blow molding, and rotational molding. Each process is used to create different types of products with unique shapes, sizes, and properties.
Plastic Mold Manufacturing Plastic Injection MoldingRapid PrototypingCNC MachiningSheet Metal StampingPressure Die CastingSilicone & Rubber PartsSurface Finishing
This complete reference guide walks you through everything from quoting, design analysis, and shipment to best practices that ensure your model is optimized for molding.
1.Limited temperature resistance: HDPE has a relatively low temperature resistance compared to other materials, making it unsuitable for high-temperature applications. 2.Limited color options: HDPE is typically only available in a limited range of colors, which may not be suitable for all applications. 3.Difficult to bond: HDPE can be difficult to bond with other materials, which may limit its use in certain applications. 4.Limited mechanical properties: HDPE has limited mechanical properties compared to other materials, such as metals, which may limit its use in certain applications where high mechanical strength is required.
It's most often used for the manufacturing plastic parts at scale due to its low material waste and low cost per part. It’s an ideal manufacturing process for industries like medical devices, consumer products, and automotive.
Critical-to-quality (CTQ) dimensions you call out on models let us know what areas are most crucial to the success of your parts. Once the parts start molding, the process and samples are qualified using automated inline CMM technology, generating a detailed FAI and process capability study with no additional lead time.
Injection molded HDPE is a durable and versatile material with excellent chemical and weather resistance, making it suitable for a wide range of applications across industries.
HDPE (High-Density Polyethylene) injection molding is a manufacturing process that involves injecting molten HDPE material into a custom-designed mold cavity. The molten HDPE material is then allowed to cool and solidify, creating a finished plastic part.The process is also efficient, cost-effective, and capable of producing complex shapes and designs with high precision and consistency.HDPE molding offers several advantages over other manufacturing processes, including the ability to produce complex and intricate designs, high production rates, and consistent quality of the finished products. It is commonly used in the production of a wide range of plastic products, including bottles, containers, pipes, automotive parts, medical devices, and more.
A: Choosing the right HDPE molding technique depends on several factors, such as the shape, size, and complexity of the product, the required production volume, the material properties, and the cost.
Our thermoplastic injection molding is a standard process involving an aluminum mold with no heating or cooling lines running through it, which means cycle times are a bit longer. As part of the scientific molding process, our molders independently optimize and monitor fill speed, hold pressure, and hold time, and periodically inspect part quality and cosmetics. During the molding process, we use an automated inline CMM to ensure dimensional accuracy, as well as generate a detailed process capability study and FAI report.
An experienced and knowledgeable partner can help optimize the manufacturing process, reduce costs, improve quality, and accelerate time-to-market, resulting in a better outcome for the client.
A: Challenges of HDPE injection molding include the hygroscopic nature of HDPE, the high melt viscosity of HDPE, and the high crystallization rate of HDPE.
Tough Black (Loctite Henkel 3843) and Ceramic-Filled (BASF 3280) are two new advanced photopolymer materials now available for 3D printing.
HDPE material properties may vary by specific grade and manufacturer. Injection molded HDPE material has some general properties:
Our basic guidelines for plastic injection molding include important design considerations to help improve part moldability, enhance cosmetic appearance, and reduce overall production time. View our design guidelines page for more details.
Tolerances: Typically, Protolabs can maintain a machining tolerance of +/- 0.003 in. (0.08mm) with an included resin tolerance that can be greater than but no less than +/- 0.002 in./in. (0.002mm/mm).
Our digital factories create prototypes and low-volume parts fast, while our manufacturing network, offers advanced capabilities and volume pricing.
Get machined parts anodized and chromate plated with our quick-turn finishing option. Eligible materials include aluminum 6061/6082 and 7075.
GETTING A QUOTE WITH LK-MOULD IS FREE AND SIMPLE.
FIND MORE OF OUR SERVICES:
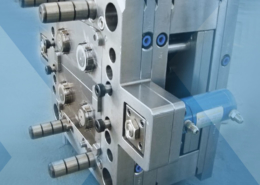
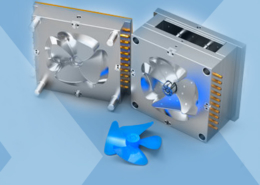
Plastic Molding

Rapid Prototyping
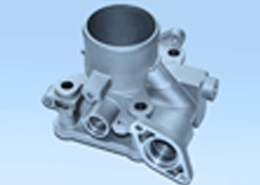
Pressure Die Casting
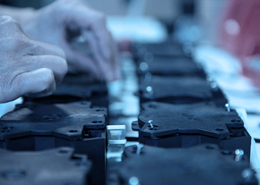
Parts Assembly
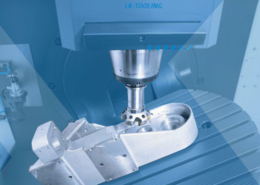