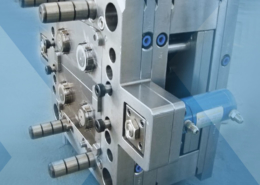
ferromatik milacron europe elektra 300 - Maszyneria - ferromatik injection mould
Author:gly Date: 2024-10-15
Structural Foam is a term commonly used to describe thermoplastic injection moulding components made by the injection moulding process which have a cellular core.
The Low Pressure Process To achieve consistent quality mouldings, it is recommended to use dedicated special purpose injection moulding machines. The machines introduce a gas into the melted plastic which when injected into the closed mould tool subsequently foams the plastic material of the component being produced.
Conventional Moulding Machines Another widely used method is the use of standard injection moulding machines with added "blowing agents" incorporated into the material. Using dry chemical blowing agents mixed in with the granules of plastic, the plastic is melted in the barrel of the machine. A measured charge is injected into the mould tool. The heat of the melted plastic causes the blowing agent to react, which forms a gas, which in turn foams the plastic.
With the low cavity fill pressures the mould tools can be made in lighter grade materials, Cast Aluminium and Cast Steel. As such the costs are cheaper than with normal injection moulding. When Structural Foam mouldings are made using Conventional Moulding Machines, invariably the mouldings are for engineering applications. In both processes, the foaming action within the material demands that the material is fed into the mould tools quickly and as such large feed gates are utilized and high injection speeds are necessary. Whilst the process has lower cavity fill pressures than conventional injection moulding, if the mouldings are being made in conventional machines, then the tools are often constructed in a more robust manner to take into account the possibility of the higher machine clamp pressures being used.
The use of the more controlled Low Pressure Process enables larger mouldings to be produced. Almost all thermoplastic materials can be foamed and wall sections at 5 -- 15 mm, are thicker than compact (normal) injection mouldings. Limited only by the size of moulding machines, mouldings of up to 40 kgs and in excess of one meter have been produced. The nature of the process leaves a rough streaky surface finish on the surface of mouldings. If this is not acceptable, then a subsequent filling and painting operation is applied. Often this painted surface is of a textured type thus minimizing any irregularities in the moulded surface.
A cellular plastic is one in which the outer surface is denser than the inner layers. The core of the moulding is of a honeycomb nature and less dense than the outer surface. The combination results in a moulding of a high stiffness ratio compared with non-structural foam (compact) mouldings.
GETTING A QUOTE WITH LK-MOULD IS FREE AND SIMPLE.
FIND MORE OF OUR SERVICES:
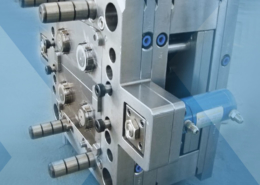
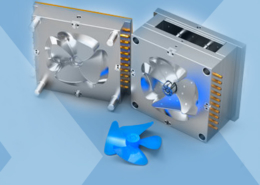
Plastic Molding

Rapid Prototyping
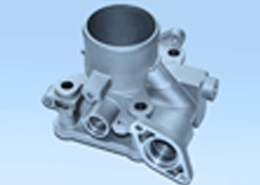
Pressure Die Casting
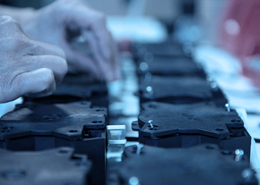
Parts Assembly
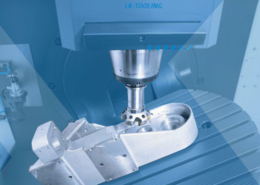