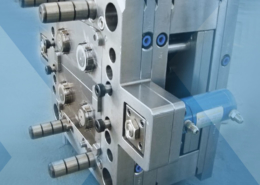
ferromatik milacron blow moulding machine - ferromatik injection moulding
Author:gly Date: 2024-10-15
We run a small, flexible toolroom with highly skilled toolmakers and machinists on hand to deliver top-quality solutions for our clients.
A racing team, for example, might rely on quick production and delivery of an injection mould tool or component for testing new setups, so partnering with a well-connected UK precision engineering company delivers a competitive edge.
Plastic injection moulding is the most common way to manufacture all types of plastic parts and is particularly effective for large orders. However, the tooling process can be expensive and require longer lead times than other methods. For small batches and prototypes, there are quicker and more affordable ways to produce plastic parts.In this article, we explore the top alternatives to injection moulding that allow cost-effective manufacturing of low-volume parts (in the tens or hundreds), enabling you to test the market, receive feedback from users, present your product to investors, run promotions, and more. Vacuum Casting(Also known as: Urethane Casting / Polyurethane Casting / Silicone Moulding / Soft Tooling)Vacuum casting is an excellent alternative to injection moulding for quantities between 10 to 50. It shares many similarities in terms of technique and final outcome—from function to aesthetics—but without the high upfront costs or long lead times of injection moulding. This method offers a wide range of resins that can mimic ‘production-grade’ materials, from soft elastomers with varying shore hardness to hard plastics like ABS. For these reasons, urethane casting is often used for end-use small production runs of a product that will eventually be injection moulded. Advantages:Lower upfront cost and faster lead times for short production runs.Wide selection of polyurethane materials and good surface finish. Limitations:Silicone tools typically only last 25 shots before the tool will need to be replaced.Higher unit price than injection moulding. 3D Printing3D printing is a very affordable and quick alternative to plastic injection moulding for early-stage prototypes and short production runs, especially for smaller-sized parts. 3D printing technologies like industrial stereolithography (SLA) requires no tooling costs and is able to give a nice surface finish that resembles injection moulded parts. Although it may lack in some aspects of strength or properties, 3D printing has come a long way and is increasingly being used in low-volume end-use applications. Advantages:Fast and cost-effective for very small production runs.Can print parts with highly complex geometries. Limitations:Material and size constraints.May lack in some aspects of strength or quality.
Ready to start your next project? Submit your 3D CAD to our contact form here to get a quote or discuss your project requirements.
CNC machining is a highly reliable process that can be a good alternative to injection moulding, especially for creating more rigid and durable parts in low-to-mid volume quantities with high precision and accuracy. In fact, the precision moulds used in the injection moulding process are made via CNC machining.
Thermoforming is a good alternative to injection moulding for ‘relatively’ simple plastic parts like packing containers, vehicle door panels, and dashboards in low-to-mid volumes. It involves creating a simple single-sided mould of the product. A thin sheet of plastic is then heated and formed using vacuum, pressure, or mechanical force.
Cobra Tool & Die utilise a full design CAD package and a full CNC machining package with an array of high-performance CNC machines to deliver the highest standards in tooling.
The role of the ejector plate is to support the ejector pins (see point 9) and to move them forward to eject the product from the injection mould tool once it has solidified.
Because all stages of tool design and manufacturing are handled in-house, there are no unnecessary transport delays, keeping your project on schedule.
Mould Tools for Plastic Injection Tool Mouldings have always been the backbone of our business. As expert toolmakers with decades of experience, our knowledge and expertise is second to none and is highly regarded by our customers.
In this article, we explore the top alternatives to injection moulding that allow cost-effective manufacturing of low-volume parts (in the tens or hundreds), enabling you to test the market, receive feedback from users, present your product to investors, run promotions, and more.
Injection mould tools must be manufactured to high quality and precision standards and must also be durable in order to produce high volumes of parts. They have to be robust and built to last.
As a UK injection moulding manufacturer, Cobra adheres to stringent standards and regulations, ensuring that the injection mould tools produced are of the highest quality. This is crucial for industries like automotive and healthcare, where quality cannot be compromised.
Cobra Tool & Die produces injection mould tools for automotive parts, electronic components, medical and pharmaceutical components, ophthalmic instruments, aerospace, plastics and rubber moulders, and more.
Director involvement also brings a wealth of experience and expertise to injection mould tool production, however simple or complex it may be. You can discuss all aspects of your project over the phone, via email or in person.
We can work with your own design or offer the support of our in-house design team who are also based at our premises in Farlington, Portsmouth, UK.
As well as facilitating easier communication, working with a local UK toolmaking company provides the advantage of proximity and shorter lead times. In case any adjustments or modifications are required at any stage of the process, these can be managed on-site.
The UK automotive sector uses injection mould tooling to produce components of all sizes, from dashboards and bumpers to complex smaller parts.
Plastic injection moulding is the most common way to manufacture all types of plastic parts and is particularly effective for large orders. However, the tooling process can be expensive and require longer lead times than other methods. For small batches and prototypes, there are quicker and more affordable ways to produce plastic parts.
A recommended maintenance schedule for the injection mould tool involves regular inspection, cleaning, and repair to ensure the optimal performance and longevity of the tool. This process includes checking for wear and tear on critical parts like cavities, cores, and ejector pins. Injection mould tool maintenance could involve lubricating moving components, removing residue, and checking that channels are free from blockages. Any damage, such as cracks or deformations, must be repaired promptly to prevent defects in components and keep your operations running optimally.
Vacuum casting is an excellent alternative to injection moulding for quantities between 10 to 50. It shares many similarities in terms of technique and final outcome—from function to aesthetics—but without the high upfront costs or long lead times of injection moulding. This method offers a wide range of resins that can mimic ‘production-grade’ materials, from soft elastomers with varying shore hardness to hard plastics like ABS. For these reasons, urethane casting is often used for end-use small production runs of a product that will eventually be injection moulded.
The location ring locates the tool in the press. This makes sure that the mould is positioned correctly and aligned with the nozzle of the injection moulding machine.
At HLH Rapid, we help mechanical engineers, industrial designers, and R&D teams bring their products to market faster through our rapid tooling and injection moulding, CNC machining, 3D printing, and a range of other in-house manufacturing services. Whether you need a single part or mid-to-high production volumes, we can cater to your needs.
The production time for an injection mould tool can be from around 2 to 10 weeks depending on the complexity and the volume involved.
Mould tools produced in-house are overseen by us at all stages of production to ensure optimum performance and longevity. They are designed and manufactured to deliver many years of productivity.
We have decades of experience, knowledge and expertise in toolmaking. We also offer a rapid refurbishment service to ensure that downtime is kept to a minimum as and when required.
Having direct communication with our tool room means that decisions are made quickly and with your input. Any delays are reduced or avoided altogether, and your project progresses smoothly and efficiently.
The back plate is a mounting surface for the components of the injection mould, attaching the mould to the injection moulding machine. The mould halves need to come together accurately during the injection moulding process, so the back plate serves to provide stability, aligning the halves correctly.
The cavity is the hollow part of the injection mould that shapes the product. The upper half of the mould forms the cavity, which is where the molten plastic is injected. The cavity of the plastic injection mould must be designed and finished to a high standard in order to produce high-quality components.
When it comes to motorsport, performance, reliability and safety are crucial, and on top of this, our industry partners are often working to extremely tight schedules.
Many of the industries we serve operate to strict standards, and therefore precision and finish are essential in order to maintain the integrity and performance of components.
Maintenance is usually done during regular servicing of the injection mould tool. We generally recommend servicing regular tools every three months, or every 50000 cycles.
Injection mould tool production is a core part of our business. A range of machinery for CNC milling, wire erosion and spark erosion (EDM) is used to produce injection mould tooling.
Yes, we can offer bespoke product design from concept to completion, including 3D printing for prototypes and R&D. All stages of the process can be handled on-site, from concept to fully hardened production tooling.
Having a director-level contact means that your project receives personal attention at all stages of the tool manufacturing process. Direct communication channels ensure a clear understanding of your requirements and adherence to key deadlines for delivery of your finished injection mould tooling. You can call us or visit in person.
When it comes to injection mould tool maintenance, a regular servicing schedule is always recommended to ensure optimum performance and productivity.
If you would like to discuss your toolmaking needs, whether that’s innovation, concept design, new tooling or repairs, get in touch with us to find out more about what we can offer you. Give us a call, or why not pop in and see us!
The product is the final component that is produced by the injection moulding process. The product can be a small, intricate part or a larger, complex component; products manufactured from moulds produced at Cobra Tool & Die range from high-spec seals and gaskets to consumer goods.
The core makes up the internal shape of the product and is part of the lower half of the mould tool. It works together with the cavity to define the final shape of the product during plastic injection moulding. If there are internal features or hollow parts of the product, the core is the part of the mould tool that forms these.
For quick and efficient tool maintenance and repair, we stock many grades of hardened steel, which we offer clients to repair broken/worn inserts.
This maintains the required distance between mould plates during the plastic injection moulding process. The mould must close uniformly, with all parts correctly aligned.
For production at scale, cost per unit is kept low. At the same time, the process of injection moulding is also suitable for producing detailed and complex components.
Molten plastic enters the mould via the sprue, also known as the feed. This is the channel that connects the injection moulding machine nozzle to the runner system. The flow rate and pressure of the injected material is affected by the design of the sprue itself.
As UK-based precision engineers, Cobra Tool & Die have the capacity to handle part or all of the production process for injection mould tools on-site.
3D Printed Moulds3D printed moulds are the latest trending technique in mould making. They offer a cost-effective and rapid alternative to traditional injection moulding, suitable for 30 to 100 units or more (depending on the material being injection moulded). The key limitations of 3D printed moulds are accuracy constraints, as well as lower durability and heat resistance compared to metal moulds. Advantages:Cost-effective for small batches of parts.Less commitment and facilitate quicker iterations. Limitations:Size and accuracy constraints.Temperature and pressure limitations of plastic moulds. Thermoforming ManufacturingThermoforming is a good alternative to injection moulding for ‘relatively’ simple plastic parts like packing containers, vehicle door panels, and dashboards in low-to-mid volumes. It involves creating a simple single-sided mould of the product. A thin sheet of plastic is then heated and formed using vacuum, pressure, or mechanical force. Advantages:Cost effective for low-to-mid volumes.Efficient for simple plastic parts. Limitations:Achieving consistent wall thickness can be challenging.Not suitable for highly complex parts. CNC MachiningCNC machining is a highly reliable process that can be a good alternative to injection moulding, especially for creating more rigid and durable parts in low-to-mid volume quantities with high precision and accuracy. In fact, the precision moulds used in the injection moulding process are made via CNC machining. Advantages:Excellent for high precision, high tolerance parts.Fast turnaround time for low-volume production parts. Limitations:Not compatible with rubber, silicone and other soft plastics.Can be time-consuming and expensive for very complex geometries. Source Custom Plastic Parts With HLH RapidAt HLH Rapid, we help mechanical engineers, industrial designers, and R&D teams bring their products to market faster through our rapid tooling and injection moulding, CNC machining, 3D printing, and a range of other in-house manufacturing services. Whether you need a single part or mid-to-high production volumes, we can cater to your needs.Ready to start your next project? Submit your 3D CAD to our contact form here to get a quote or discuss your project requirements.
In the UK, injection moulding is the most widely used method for manufacturing plastic components, offering efficiency and precision.
Because of the high level of precision it offers, as well as the durability of the finished tooling, injection moulding enables manufacturers to meet production criteria consistently and at scale.
Each stage of your project can be managed in-house at our premises in Portsmouth, from product development, product design and prototype tooling to production tooling, servicing and rapid repairs.
3D printing is a very affordable and quick alternative to plastic injection moulding for early-stage prototypes and short production runs, especially for smaller-sized parts. 3D printing technologies like industrial stereolithography (SLA) requires no tooling costs and is able to give a nice surface finish that resembles injection moulded parts. Although it may lack in some aspects of strength or properties, 3D printing has come a long way and is increasingly being used in low-volume end-use applications.
3D printed moulds are the latest trending technique in mould making. They offer a cost-effective and rapid alternative to traditional injection moulding, suitable for 30 to 100 units or more (depending on the material being injection moulded). The key limitations of 3D printed moulds are accuracy constraints, as well as lower durability and heat resistance compared to metal moulds.
GETTING A QUOTE WITH LK-MOULD IS FREE AND SIMPLE.
FIND MORE OF OUR SERVICES:
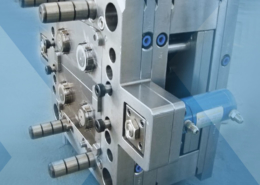
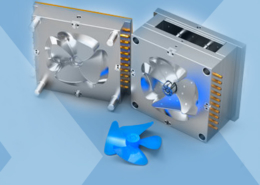
Plastic Molding

Rapid Prototyping
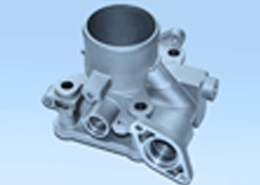
Pressure Die Casting
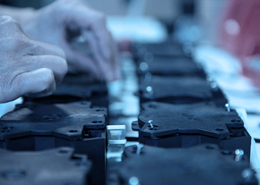
Parts Assembly
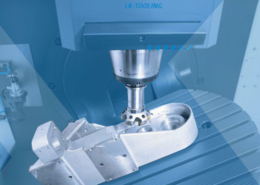