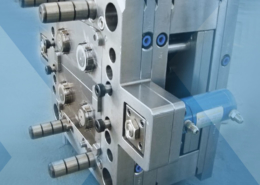
Extrusion vs. Injection Molding, What Is The Difference? - injection extrusion
Author:gly Date: 2024-10-15
Now that you’ve designed and 3D printed your mold, you can mold the parts on your benchtop plastic injection molding machine.
Turn the visibility of your current mold core off, and turn the other side on. Repeat the process to ensure that the object fully intersects with the inlet of the other half of the mold core. With your object lined up, you’re ready to subtract the area of two intersecting objects by using the “boolean difference” function in Blender.
Building a setup for DIY plastic molding does require some investment. It takes both money and time to acquire the right equipment and to master using it. However, these costs are in many cases still lower than the cost of a single metal mold, so the eventual time and cost savings, once you’re up and running, will easily offset the initial effort.
The process of low volume injection molding begins with mold creation. Mold design involves translating the part’s innovation into a 3D mold, considering factors like part ejection, gating, and cooling. Various mold fabrication methods, such as CNC machining or additive manufacturing, can be employed based on the project requirements.
Want to learn more about injection molding with 3D printed molds? Download our white paper for detailed guidelines for using 3D printed molds in the injection molding process and see real-life case studies with Braskem, Holimaker, and Novus Applications.
In this webinar, we'll show you how to use stereolithography (SLA) 3D printed molds in the injection molding process to lower costs, reduce lead times, and bring better products to market.
Quality control is paramount in low volume injection molding to ensure the production of high-quality parts. Inspection techniques, such as dimensional analysis, visual inspection, and functional testing, verify the part’s conformance to specifications. Testing procedures, including mechanical, thermal, and chemical testing, further validate the part’s performance.
Stay updated with the latest 3D printing news, interviews with experts from around the world and tutorials on how to leverage 3D printing.
A benchtop injection-molding machine, such as the Galomb Model-B100 or the Holipress. There are a number of benchtop injection molders on the market that vary in cost. Many of the lower cost molders use a hand-driven plunger, while some of the more expensive units use a screw or pneumatic system. Some of our customers have recommended systems from Minijector, Morgan, APSX, or Micromolder as well. Desktop automated molders such as the product line from Babyplast are good alternatives for mass production of small parts.
In this guide, we’ll walk you through the process of DIY injection molding and share all the tools and tips necessary to utilize plastic injection molding in-house using 3D printed molds.
Article Original From: https://www.djmolding.com/low-volume-injection-molding-cost-effective-solutions-for-small-scale-plastic-manufacturing/
High Temp Resin offers a heat deflection temperature is 238 °C @ 0.45 MPa that is suitable for injection molding. This material is more brittle, but is recommended for materials with a high molding temperature and to reduce cooling time.
Now, you can position your mold. Ensure that the object fully intersects with the inlet for the molten plastic during the injection molding process. Use orthographic mode, engaged via “toggle perspective/ortho,” to make this more straightforward.
Grey Pro Resin has a lower thermal conductivity than High Temp Resin or Rigid Resin, which leads to a longer cooling time, but it is softer and can wear hundreds of cycles.
Low volume injection molding is a manufacturing technique that involves producing small parts using injection molding processes. It combines the benefits of rapid prototyping and traditional injection molding, allowing for efficient production with reduced tooling costs and lead times.
For prototyping and low-volume production (approximately 10-1000 parts), 3D printed injection molds provide a time- and cost-efficient solution. They also enable a more agile manufacturing approach, allowing engineers and designers to test mold designs, easily modify them, and then continue to iterate on their designs much faster, while being orders of magnitude cheaper than traditional CNC machining.
Depending on the injected material, adhesion of the part to the mold can cause deterioration of the mold during extraction, in particular with flexible 3D printing materials such as TPUs or TPEs. Using a mold release agent is a good solution to help separate the part from the mold. Silicone mold release agents are compatible with Formlabs Grey Pro Resin, High Temp Resin, and Rigid 10K Resin.
Low volume injection molding finds applications in diverse industries. It benefits prototyping, allowing for iterative design improvements before full-scale production. Niche markets benefit from the flexibility of low volume production, enabling customized products for specific customer segments. Furthermore, low volume injection molding caters to limited production runs, addressing demand fluctuations and reducing inventory costs.
Download the blank mold insert design files—you’ll use them to create your injection mold design. The designs can also be easily scaled to accommodate most injection molders and mold frames. Alternatively, you can also design your own mold insert for the using the cavity diagrams of the master mold frames.
Adding two to five degrees of draft on surfaces perpendicular to the direction of pull will allow the part to be removed more easily and will minimize degradation of the mold.
Your mold is now ready for printing. Export each half, making sure to check the “Selection Only” box in the Blender exporter.
Based on internal testing and case studies with our customers, we suggest to choose the 3D printing resin based on the criteria from the table below. Three stars means the resin is highly effective, one star is less effective.
First, pick the CAD software tool of your preference to design the mold insert. We’ll use the open-source Blender, but the workflow should be fairly similar in any other CAD software.
Experience: Look for a provider with a solid track record of success in low volume injection molding. An experienced provider will likely have the expertise and knowledge to deliver high-quality products. Quality Control: Quality control is critical in injection molding, as even minor defects can result in significant production delays and costs. Ensure the provider has a robust quality control system to ensure the final product meets your specifications. Customization: Injection molding can create various products, from small components to large parts. Look for a provider that can customize their services to meet your needs, including material selection, mold design, and production volume. Communication: Good communication is key to a successful injection molding project. Look for a provider that is responsive and easy to communicate with and who keeps you informed throughout the production process. Cost: Cost is always a consideration but should not be the only factor. Look for a provider that offers competitive pricing while still delivering high-quality products and excellent customer service. Environmental Responsibility: As environmental concerns become more critical, choosing a provider committed to sustainable manufacturing practices is essential. Look for a provider that uses eco-friendly materials and processes and recycles waste materials.
In Blender, use the eye icon in the scene explorer to toggle off one half of the mold. Once your workspace is set up to your liking, set both halves of the mold to the “wire” draw type under the Object menu, as in the image below.
Download our white paper for guidelines for using 3D printed molds in the injection molding process to lower costs and lead time and see real-life case studies with Braskem, Holimaker, and Novus Applications.
Depending on the geometry and the size, multiple molds can be printed at once on a build platform to increase printing efficiency.
If you have more questions about the workflow, make make sure to check our article FAQ: Injection Molding With 3D Printed Molds.
To 3D print the mold, it’s essential to pick a material that can withstand the temperature and pressure on the mold during the injection molding process.
The exact approach to DIY injection molding will vary based on your desired design and volume, but these tips and tricks will help increase your success rate.
Injection molding is ubiquitous as a manufacturing process—in fact, the majority of plastic products in the world today are manufactured by injection molding. While it is an ideal technique for large-scale production needs, traditional CNC machined metal molds have prohibitive high costs and long lead times for low-volume production.
To reduce the visibility of print lines on the finished part, print the mold with a smaller layer height (50 or 25 microns per layer instead of the default 100). Note that this increases print time.
Select the first half of your object, and choose the boolean option under the Modifiers Menu. Select the object you’re cutting, and make sure that the “difference” operation is selected. Apply the operator, and do the same for the other side. It should look something like the image below. If you get stuck here, this tutorial on adding interlocking components to a design may be helpful.
Low volume injection molding presents a cost-effective and efficient solution for small-scale production. Its advantages over traditional manufacturing methods, such as reduced costs, shorter lead times, and increased flexibility, have become a valuable option for various industries. By understanding the process, considering materials and design aspects, and selecting the right provider, businesses can leverage low volume injection molding to optimize their production strategies and achieve success in the market.
A 3D printing material that can withstand the temperature and pressure on the mold during the injection molding process. We recommend the following materials for Formlabs SLA 3D printers:
The conversation around 3D printing and injection molding is often oppositional, but it’s not always a question of one versus the other. By directly 3D printing parts or using 3D printed molds for injection molding for prototyping and low-volume production, you can leverage the benefits of both technologies. This will make your manufacturing process more time- and cost-efficient and allow you to bring products to the market faster.
If designing for an aluminum mold frame, add .125 mm of extra thickness to the back of the mold plates to account for compression forces and to ensure a complete seal.
Creating custom molds using a stereolithography (SLA) 3D printer, like the Form 3+, is simple and convenient, allowing you to leverage the benefits of both 3D printing and traditional molding techniques.
For more about low volume injection molding: cost-effective solutions for small scale plastic manufacturing,you can pay a visit to Djmolding at https://www.djmolding.com/low-volume-injection-molding/ for more info.
Rigid 10K Resin is an industrial-grade, highly glass-filled material, which provides a solution that can cope with a wider variety of geometries and injection molding processes. It has an HDT of 218°C @ 0.45 MPa and a tensile modulus of 10,000 MPa, making it strong, extremely stiff, and thermally stable.
Choosing the right low volume injection molding provider can be daunting, as businesses must consider many factors. Here are some key points to help you make the right decision:
A high-performance desktop SLA 3D resin printer, like the Formlabs’ Form 3+. The Form 3+ can produce accurate molds with crisp features, and a smooth surface finish that will yield high-quality final molded parts. Beyond DIY plastic molding, an SLA 3D printer is also a valuable asset for prototyping and other applications throughout product development.
Regarding cost considerations, low volume injection molding offers significant advantages over traditional manufacturing methods. Let’s delve into some key points:
Low volume injection molding supports various materials, including thermoplastics, elastomers, and engineering-grade resins. Design considerations play a crucial role in achieving optimal results. Factors such as part complexity, undercuts, draft angles, and wall thickness need careful consideration. Manufacturers can make mold modifications to accommodate specific design requirements.
You have a wide variety of materials to choose from for injection molding. Formlabs and our customers have tested the following materials with 3D printed injection molds:
Setting up the print only takes a few seconds in PreForm, the print preparation software for Formlabs professional 3D printers. If your mold design requires support structures for printing, make sure to orient the mold halves in PreForm so that the cavity faces up. This will simplify post-processing and ensure a high-quality surface for your molded parts.
Once the mold is ready, the injection molding process begins. It comprises several steps, starting with material selection, where the appropriate resin is chosen based on the desired properties of the final part. The material is then heated and injected into the mold cavity, following which it undergoes a cooling phase. Finally, someone opens the mold and ejects the finished part.
Before purchase, make sure to evaluate the injection molder carefully against your production requirements. For large parts, industrial processes will still be necessary. This DIY injection molding technique is best optimized for producing small parts at low volumes.
Interested in other applications of 3D printed molds? Download our white paper that also covers thermoforming and casting with elastomers.
Consider the desired properties of your object and the capabilities of your injection molder before you make your choice. From there, simply follow the bespoke instructions on your injection molder to quickly and efficiently produce your parts.
Reduced Tooling Costs: One of the considerable cost benefits of low volume injection molding is the substantial reduction in tooling expenses. Traditional manufacturing often requires expensive molds and tooling equipment, hindering small-scale production. With low volume injection molding, businesses with limited budgets can significantly reduce the tooling cost, making it more accessible and affordable. Minimal Material Waste: Traditional manufacturing methods often result in significant material waste, especially during the initial setup and testing phases, and this can lead to increased costs and environmental concerns. Low volume injection molding minimizes material waste by precisely controlling the amount of material injected into the mold, and this not only reduces costs and aligns with sustainable manufacturing practices. Faster Time-to-Market: Time is money in the competitive business landscape. Low volume injection molding enables faster time-to-market by lowering lead times compared to traditional manufacturing. The streamlined process allows quicker iterations and adjustments, from mold creation to production. This rapid turnaround time is especially advantageous for businesses in rapidly evolving industries or those responding to changing customer demands. Customization and Flexibility: Low volume injection molding offers high customization and flexibility. Companies can easily modify designs and make adjustments to meet specific customer requirements. This level of customization minimizes the need for costly post-production modifications or rework, resulting in cost savings and improved customer satisfaction. Cost Savings for Small Production Runs: Low-volume injection molding is particularly cost-effective for limited production runs or niche market products. Instead of investing in large-scale production infrastructure, businesses can produce small quantities on demand. By adopting this approach, you can avoid holding extra inventory, lower storage expenses, and decrease the chances of making too much. Scalability and Risk Reduction: Low volume injection molding allows businesses to scale their production gradually, allowing them to test the market and validate product demand before committing to large-scale production. This scalability reduces the financial risks associated with mass production, as businesses can adjust production volumes based on market response and request. Improved Profit Margins: Low volume injection molding can improve profit margins by reducing tooling expenses, minimizing material waste, and allowing for faster time-to-market. Businesses can optimize manufacturing processes, reduce costs, and increase efficiency, improving financial outcomes.
Low volume injection molding offers several advantages over traditional manufacturing methods. It saves costs by eliminating the need for expensive tooling and minimizing material waste. The shorter lead times facilitate faster product iterations and market entry. Low volume injection molding also supports various industries, including prototyping, niche markets, and limited production runs.
Low volume injection molding offers a cost-effective solution for small-scale production, revolutionizing the manufacturing industry. With its ability to provide reduced costs, shorter lead times, and increased flexibility, low volume injection molding has gained significant importance in various sectors. In this blog post, we will explore the concept of low volume injection molding, its advantages over traditional manufacturing methods, suitable use cases, materials and design considerations, the process involved, cost considerations, and the factors to consider when choosing a low volume injection molding provider.
GETTING A QUOTE WITH LK-MOULD IS FREE AND SIMPLE.
FIND MORE OF OUR SERVICES:
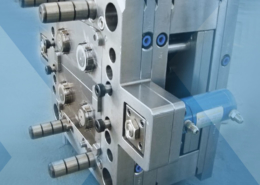
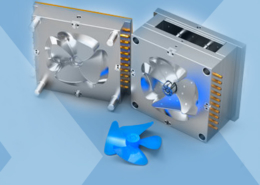
Plastic Molding

Rapid Prototyping
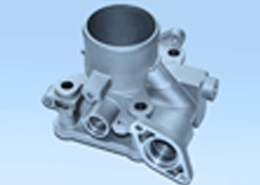
Pressure Die Casting
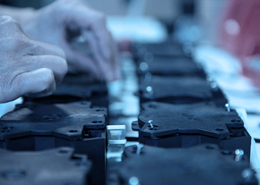
Parts Assembly
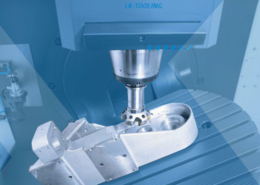