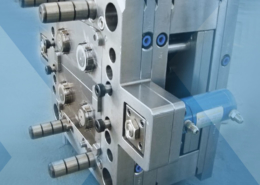
Exploring the Versatility and Impact of Plastic Injection Products
Author:gly Date: 2024-06-08
Introduction
Plastic injection products have become ubiquitous in our daily lives, serving as essential components in various industries and applications. From household items to automotive parts, the versatility and reliability of plastic injection products have revolutionized manufacturing processes worldwide. This article aims to delve into the intricacies of plastic injection products, shedding light on their applications, manufacturing process, advantages, and future prospects.
Understanding Plastic Injection Products
Composition and Manufacturing Process:
Plastic injection products are manufactured using a process called injection molding, wherein molten plastic material is injected into a mold cavity under high pressure. Once the material cools and solidifies, the mold opens, and the finished product is ejected. This highly efficient and repeatable process allows for the production of complex geometries with precise tolerances.
Types and Varieties:
Plastic injection products come in a wide range of types and varieties, each tailored to specific applications and industries. Common types include thermoplastics, thermosets, and elastomers, with variations in properties such as strength, flexibility, and chemical resistance. From consumer goods to industrial components, plastic injection products cater to diverse needs and requirements.
Applications Across Industries
Automotive Sector:
In the automotive sector, plastic injection products play a vital role in the production of interior and exterior components, including dashboards, bumpers, and door panels. The lightweight nature of plastic materials, combined with their durability and design flexibility, makes them ideal for automotive applications, contributing to improved fuel efficiency and vehicle performance.
Consumer Electronics:
In the realm of consumer electronics, plastic injection products are used to manufacture a myriad of components, from casings and buttons to internal circuitry. The ability to produce intricate shapes with tight tolerances ensures seamless integration of components, while the cost-effectiveness of plastic materials allows for the mass production of electronic devices at scale.
Advantages and Challenges
Advantages of Plastic Injection Products:
Plastic injection products offer several key advantages, including cost-effectiveness, design flexibility, and rapid production cycles. The ability to mold complex geometries with high precision allows for innovative product designs, while the scalability of injection molding enables manufacturers to meet demand fluctuations efficiently.
Challenges and Considerations:
Despite their numerous advantages, plastic injection products also present certain challenges, such as environmental sustainability and material selection. Addressing these challenges requires a holistic approach that considers factors such as material recyclability, waste reduction, and the development of eco-friendly alternatives.
Future Prospects and Innovations
Technological Advancements:
Looking ahead, technological advancements in plastic injection molding are poised to further enhance the efficiency and capabilities of plastic injection products. Innovations such as additive manufacturing, advanced materials, and smart manufacturing technologies hold the potential to revolutionize the industry, paving the way for new applications and opportunities.
Sustainability Initiatives:
Furthermore, sustainability initiatives will play a crucial role in shaping the future of plastic injection products. Manufacturers, policymakers, and consumers must collaborate to develop and implement strategies that promote resource conservation, waste reduction, and the adoption of eco-friendly materials. By embracing sustainability as a guiding principle, the industry can mitigate its environmental impact while driving innovation and growth.
Conclusion
In conclusion, plastic injection products represent a cornerstone of modern manufacturing, offering unparalleled versatility, efficiency, and reliability. Their widespread applications across industries highlight their importance in our daily lives, while ongoing advancements in technology and sustainability initiatives promise to further enhance their impact in the years to come. Embracing innovation and sustainability will be essential in unlocking the full potential of plastic injection products and shaping a more sustainable future for generations to come.
GETTING A QUOTE WITH LK-MOULD IS FREE AND SIMPLE.
FIND MORE OF OUR SERVICES:
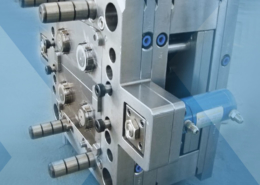
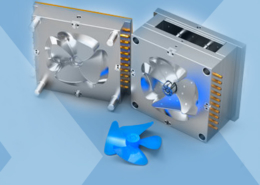
Plastic Molding

Rapid Prototyping
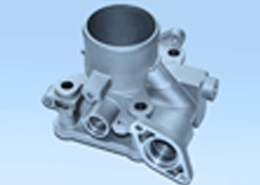
Pressure Die Casting
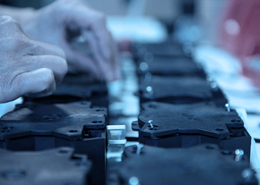
Parts Assembly
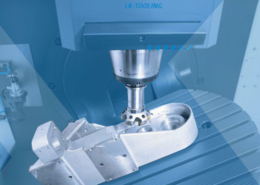