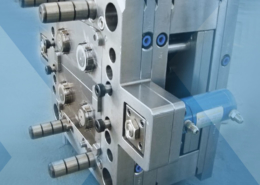
Expert Plastics Training Online | Plastics Training - paulson injection molding
Author:gly Date: 2024-10-15
Choosing the right material is crucial for the success of large part injection molding. Commonly used materials include:
The two-platen injection molding machine is ideal for medium—and large-sized machines. It features a unique design with two platens holding the mold halves during injection. Unlike traditional three-platen machines, this design is compact and efficient, ensuring precision and efficiency in molding large plastic products.
During molding, different colored melts are plasticized in barrels 1 and 5, gear 3 rotates the rotating shaft 4, and different colored melts alternately enter the mold cavity to obtain different colors and colors. A patterned plastic product that radiates from the center to the periphery.
Widen the contact area, make grooves to increase adhesion, use core pull on the first shot, inject the material of the second shot into the first shot, mold the first shot Make the surface of the surface as rough as possible.
Small lens double shot design: The first shot is opaque, the second shot is the lens, the first shot is as high as possible and the second shot is PMMA.
There must be a constant temperature difference between the melting points of the two materials. Normally 60 ° C is recommended, and at least 30 ° C is recommended. The material of the first shot has a high melting point temperature. Usually, the first shot is a PC. Or on PC / ABS, the second shot is TPU or TPE. , PC thickness is 0.6-0.7mm, the software is over 0.4mm.
Transparent and opaque dual shot design for decoration: the first shot is an opaque material, the second shot is a transparent material, the opaque material is usually hot PC, the second shot transparent material is PMMA or PC. Your PC should be sprayed with UV to protect it. PMMA can be UV or enhanced. If there are letters on the surface, you need to select UV.
During molding, after the melt is plasticized in the barrel, open/close valves 2 and 4 control the order of the melt entering the nozzle and the proportion of material discharged, then the nozzle is injected into the mold cavity increase. Various plastic injection molding products with different color mixing effects can be obtained.
You can improve the practicality and aesthetics of plastic parts by displaying them in two different colors, or by displaying regular patterns or irregular moire-like patterns on plastic parts.
There are two barrels, and the structure and usage of each barrel are the same as a normal injection-molded barrel. Each barrel has its own passageway that connects to the nozzle, and on-off valves 2 and 4 are also attached to the nozzle passageway.
Large-part injection molding finds extensive applications across various industries, offering unparalleled advantages in producing oversized plastic components.
Gas-assisted injection molding (GAIM) is a technique that uses an inert gas, typically nitrogen, to help with the injection molding process. In GAIM, the gas is injected through air holes in the mold or the nozzle of the injection machine into the molten plastic within the mold, creating hollow sections in the part. This assists in pushing the molten plastic into the mold cavities, ensuring uniform filling and reducing internal stresses. By incorporating gas-assisted injection molding into their processes, manufacturers can achieve higher efficiency, better product quality, and reduced production costs, making it a valuable technique in large-part injection molding.
Two-color mold: A mold that injects two plastic materials into two molding machines with the same injection molding machine, but the product is injected only once.
Huarong's innovative approach to two-platen machine design has resulted in several patents that optimize machine efficiency and performance. Their patented technologies include the Suspended Tie-bar Bearing Module, Patented Inner Supporting Sliding Module, Patented Moving Platen Positioning Device, and Optional Patented Tie-bar Disassemble Function, which won the prestigious Taiwan Excellence Award.
Matching materials for two-shot injection molding must meet two basic compatibility requirements: adhesive compatibility and process compatibility.
Large-tonnage injection molding machines are vital for producing large parts. These machines, rated by their clamping force, ensure the mold halves remain securely closed during injection. Proper tonnage calculation is crucial to prevent defects and ensure high-quality output.
Large-part injection molding, also known as large-tonnage injection molding, shares similarities with standard injection molding but requires higher-tonnage injection molding machines (500 tons or more) to manage the increased clamping force needed for larger surface areas. Understanding the differences helps in selecting the right equipment and processes.
Double Injection, sometimes known as 2 material 2 shot molding or 2K molding, is an innovative manufacturing process used to produce complicated molded parts from two different materials.
Also, there are two barrels 1 and 5, and the nozzle structure is a little special. In addition to the normal nozzle function, it can also be rotated by gear 3 attached to the rear.
Next news : Success Stories: How Elevate South African Manufacturer's Manufacturing Capabilities with Cutting-edge Two-platen Machine
This type of molding process, also commonly referred to as two-component injection molding, is usually completed with a set of molds and requires a special two-color injection molding machine. Generally, there are the following requirements:
Several factors must be considered when deciding whether your part requires a large-ton machine. These factors include size, material, and safety considerations. Experts recommend adding a 10% safety factor to the clamping force calculation to accommodate potential defects. Key considerations to consider are part size and complexity, material type, projected annual volume, quality requirements, mold design, and seeking expert consultation.
Today, we talk about the 2K injection molding technology, a molding method in which two different colored plastics are injected into the same mold.
DGMF Mold Clamps Co., Ltd mainly offers a wide range of Mold Clamps and Mold Components. Used in processing machinery especially on plastic injection molding machines, and pressure dies casting machines.
Large-part injection molding is a sophisticated manufacturing process for creating precision large-scale plastic components. This article delves into the details of this process, exploring various techniques, materials, and industry applications.
Large part injection molding is an indispensable process in modern manufacturing, offering numerous benefits across various industries. By understanding the techniques, machinery, and materials involved, businesses can enhance their production capabilities and achieve superior product quality. As the leading plastic injection molding machine manufacturer, Huarong is committed to providing all our clients with precision, custom plastic injection molding services that deliver premium quality components. If you have any further questions or machine needs, please don't hesitate to contact Huarong.
These machines offer cost-effectiveness, space efficiency, energy efficiency, suitability for large mold sizes, and flexibility in mold configurations. They have a smaller footprint than three-platen machines, making them ideal for limited-space environments.
GETTING A QUOTE WITH LK-MOULD IS FREE AND SIMPLE.
FIND MORE OF OUR SERVICES:
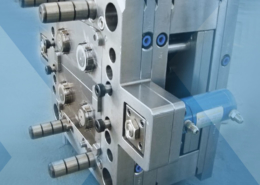
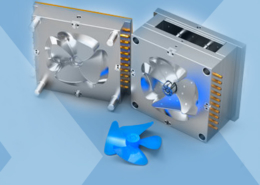
Plastic Molding

Rapid Prototyping
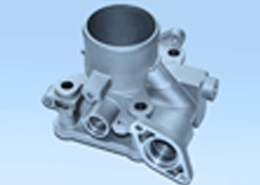
Pressure Die Casting
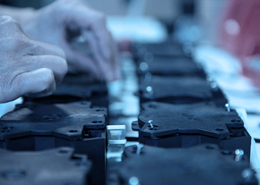
Parts Assembly
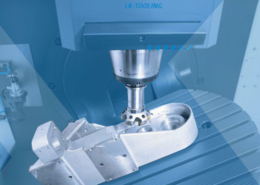