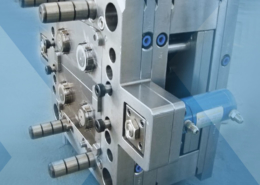
Expanded Polystyrene Molding Process, The Foaming ... - molding polystyrene
Author:gly Date: 2024-10-15
Polycarbonate (PC): Polycarbonate, a durable and transparent thermoplastic material, finds widespread application in the medical industry. Its remarkable impact resistance and optical clarity make it ideal for medical device housings, connectors, and containers.
The injection molding process ensures an exceptional level of consistency in the final products. Each molded part exhibits near-perfect similarity, thereby minimizing variations and mitigating the risk of defects. This unwavering consistency proves to be crucial, particularly in medical applications where precision and utmost quality play a pivotal role in ensuring patient safety and reliable performance.
Our in-house mold making capabilities allow us to create bespoke molds tailored to the exact needs of each project, resulting in perfect fits and impeccable quality.
Standards serve as essential guidelines for the manufacturing process, materials used, and quality control procedures of medical devices. Adhering to these standards ensures consistent and dependable production, maintaining a high level of product quality. The importance of consistency becomes paramount in mass production scenarios, where it guarantees that every device performs reliably and consistently.
YOMURA TECHNOLOGIES: Unmatched precision in creating complex, multi-material components with superb craftsmanship and innovative double injection molding expertise.
Two-Shot Injection Molding: Two-shot injection molding, also referred to as overmolding, combines two different materials into a single mold. This technique enables the production of medical devices with multiple colors, textures, or material properties within one manufacturing cycle. It finds common application in creating ergonomic grips for medical instruments and incorporating soft-touch components onto rigid devices.
Plastic mold injection has revolutionized various industries, including the medical sector. This innovative technology has transformed the production of medical devices and equipment, bringing about significant benefits that have reshaped healthcare practices.
International standards, like ISO 13485 (Medical Devices – Quality Management Systems), hold global recognition. Adhering to these standards allows medical device manufacturers to expand their market reach since numerous countries require compliance with internationally recognized benchmarks for importing and distributing products.
Once the initial mold is created, producing medical devices in large quantities significantly reduces the cost per part. This cost-effectiveness has numerous advantages for both healthcare providers and patients as it enhances accessibility and affordability of these devices.
In the field of manufacturing, plastic mold injection stands out as an economically viable method. It proves to be cost-effective when producing medical devices in large quantities. This advantageous technique enables a seamless increase in production without compromising on quality. Consequently, it promotes greater accessibility to essential medical equipment worldwide, ultimately reducing healthcare costs and enhancing patient care on a global scale.
Plastic mold injection is a precise and efficient process used to manufacture complex medical components and devices. It involves injecting molten plastic into a pre-designed mold. This technique enables the creation of intricate and customized products that meet the specific requirements of medical applications. From simple syringes to sophisticated surgical instruments and implantable devices, plastic mold injection plays a crucial role in producing high-quality medical equipment.
Create components with unique characteristics by combining hard and soft materials, resulting in exceptional quality and distinct functionalities.
Collaborative efforts between engineers and customers refine designs for optimal product performance and manufacturing efficiency.
Plastic injection molding supports a wide range of medical-grade plastics, each with unique properties suitable for various medical applications. These materials offer tailored solutions to cater to different medical needs, ranging from biocompatible options for implants to transparent plastics used in medical packaging and durable polymers utilized in surgical tools. The versatility of the materials enables healthcare professionals to address specific requirements effectively.
Standards play a crucial role in ensuring the safety of medical devices during their design and production phases. Manufacturers are obligated to carefully assess potential risks associated with their products and take proactive measures to minimize them. This diligent approach not only helps prevent any hazards but also safeguards patients from potential harm.
Plastic injection molding for medical parts requires materials that adhere to strict regulatory and safety standards, while also possessing the required properties for specific medical applications. Here are several commonly employed materials in plastic injection molding for medical components:
Combine various resins to create rich textures and colors, offering a sensory advantage that makes your products stand out.
Robust and elegant, our automotive components meet high-performance standards while contributing to luxurious aesthetics.
Plastic injection molding simplifies the process of creating prototypes, allowing medical professionals and manufacturers to swiftly refine their designs. This speeds up the development cycle, resulting in quicker market entry for new medical devices and equipment.
Yes. Plastic injection molded parts find widespread usage in surgical procedures. They are essential components of surgical instruments, implantable devices, and various medical equipment.
Plastic injection molding offers many benefits for medical applications, making it the preferred manufacturing method for producing medical devices and equipment. Here are some of the key advantages:
Complying with FDA regulations and ISO standards is vital in medical injection molding. This ensures the safety, effectiveness, and quality of medical devices and components. The U.S. Food and Drug Administration (FDA) regulates medical devices under the Federal Food, Drug, and Cosmetic Act (FD&C Act). Manufacturers must adhere to the FDA’s Current Good Manufacturing Practices (CGMP) requirements. These guidelines cover various aspects including design, manufacturing, labeling, and quality control.
From ergonomic gadgets to wearables, YOMURA is instrumental in producing intrinsically designed parts for the tech-savvy consumer.
Liquid Silicone Rubber (LSR): LSR is a biocompatible and flexible material that is extensively used in injection molding for various medical parts. It is particularly suited for applications that need soft-touch properties like gaskets, seals, and medical implants.
To ensure regulatory compliance, you must adhere to applicable standards like ISO 13485. This involves rigorous testing and documentation of the manufacturing process. Additionally, seeking necessary approvals from health authorities such as the FDA is essential for entering the global market.
Liquid Silicone Rubber (LSR) Molding: Liquid Silicone Rubber (LSR) molding is a commonly used manufacturing technique for producing medical products that require biocompatibility, flexibility, and heat resistance. It involves injecting liquid silicone into a mold cavity and curing it to create a solid, elastic component. Some examples of medical applications using LSR molding include the production of medical-grade seals, gaskets, and silicone catheters.
Standards play a vital role in providing clear guidelines and fostering innovation. By establishing frameworks for new technologies and materials, they create opportunities for manufacturers to push the boundaries of medical device development while still adhering to the set standards.
Polyethylene Terephthalate (PET): PET is a durable and see-through thermoplastic material that has widespread use in the field of medical packaging. It is commonly used for creating blister packs and medication bottles.
The medical industry’s integration of plastic mold injection technology has produced numerous advantages that surpass conventional manufacturing methods. This innovative technique facilitates rapid prototyping, reducing the time required for product development and enhancing the efficiency of the design process. This means that medical professionals can promptly refine and optimize their product designs, ultimately leading to safer and more effective medical solutions.
Not just aesthetically superior, our molding techniques ensure your components serve their purpose with added distinction and market appeal.
Implementing cutting-edge manufacturing techniques, our team transforms innovative concepts into tangible, high-quality solutions.
Medical devices must adhere to strict regulatory requirements set by health authorities, such as the United States Food and Drug Administration (FDA) or the European Medicines Agency (EMA) in the European Union. Compliance with relevant standards is vital in securing regulatory approvals, certifications, and market clearance for these devices.
Design with innovation. Embrace a wide array of design possibilities and incorporate features that set your products apart.
Reaction Injection Molding (RIM): Reaction injection molding involves the use of a reactive liquid mixture that undergoes polymerization and solidification inside a mold. This method, often referred to as RIM, is commonly employed for manufacturing robust and impact-resistant medical equipment and components. Examples include wheelchair parts and housing for medical devices.
Many plastics used in medical-grade injection molding are designed to be compatible with the human body, ensuring safety. Additionally, these materials can withstand various sterilization processes without compromising their properties. This guarantees that medical devices remain hygienic and safe for patient use.
Maintaining control over the entire manufacturing process from mold creation to part production ensures efficiency and a rapid turnaround for our clients.
Due to the delicate nature of medical devices, the medical industry uses various intricate injection molding techniques alongside conventional ones. These include micro injection molding, two-shot injection molding, Liquid Silicone Rubber injection molding and reaction injection molding.
In the medical industry, seamless collaboration between different devices and components is crucial. Standards play a vital role in ensuring that medical devices are designed and manufactured with compatibility and interoperability in mind. This approach simplifies the integration of these devices into existing systems and workflows for healthcare professionals.
ISO standards, with ISO 13485:2016 and ISO 9001:2015 being particularly significant, govern the quality management systems for medical devices. When manufacturers comply with ISO standards, they adhere to globally recognized best practices that include risk management, traceability, and process validation.
Plastic injection molding is a highly efficient process for producing intricate and complex medical components with exceptional precision. By using accurately designed molds, the manufacturing of medical devices can achieve tight tolerances and intricate geometries while ensuring adherence to exact specifications.
Standards in plastic injection molding establish the specifications and requirements that medical devices must meet to ensure patient safety. Complying with these standards minimizes the risk of defects, malfunctions, and adverse events, guaranteeing that medical devices perform as intended and do not endanger patients.
Standards in plastic injection molding for medical devices play a crucial role in guaranteeing the safety, quality, and reliability of medical equipment used in healthcare settings. When it comes to medical applications, where patients’ lives and well-being are at stake, adhering to high standards becomes essential. Some key reasons why these standards are indispensable in the field of plastic injection molding for medical devices include:
Thermoplastic Elastomers (TPE): TPEs, or thermoplastic elastomers, are a versatile family of materials that possess the combined properties of rubber and plastic. These unique materials find extensive usage in various medical applications where flexibility is crucial. They are commonly employed for creating grips, seals, and medical tubing.
Environmental concerns can arise due to the generation of plastic waste during manufacturing. To avoid this, manufacturers should adopt recycling and sustainable practices in order to minimize their environmental impact.
Your vision realized through our tailored double injection molding solutions; together, we can turn innovative ideas into market successes.
Plastic injection molding has several benefits. However, it is important to note some limitations, including design complexity, high initial tooling costs, and material selection challenges for specific medical applications.
Injection molding often produces fully formed parts without needing additional assembly or secondary operations. This streamlined manufacturing process minimizes the risk of contamination and human error during assembly, making it more efficient and reliable.
Choose from a vast selection of suitable materials, guided by YOMURA's profound expertise to meet your unique application needs.
Polyethylene (PE): Polyethylene, a commonly used thermoplastic material in the medical industry, offers excellent biocompatibility, flexibility, and chemical resistance. It finds extensive applications in medical tubing, bags, and containers.
Compliance with regulations and standards is crucial for medical injection molding companies seeking FDA approval or clearance for their devices. It not only enables market access but also builds trust among healthcare professionals and patients. Adhering to these guidelines allows companies to reliably produce safe and high-quality medical products, enhancing patient care and the overall healthcare sector.
Polypropylene (PP): Polypropylene is a thermoplastic material known for its versatility. It offers excellent chemical resistance and boasts a low density. This makes it highly suitable for various medical applications including syringes, test tubes, and medical packaging.
Join forces with a globally recognized leader in high-precision molding, and make a lasting impact on your industry with YOMURA.
The production time for a custom-made medical device using plastic injection molding can vary based on the complexity and volume. Typically, it ranges from a few weeks to a few months.
Micro Injection Molding: Micro injection molding is a process used to create highly precise and tiny medical components, often with features that are smaller than a millimeter. This technique finds its strength in manufacturing miniature medical parts like microfluidic devices and micro-needles. The production requires specialized equipment and precision tooling to attain the desired outcomes.
Molecular co-polymerization provides unmatched strength, ensuring the long-lasting integrity of your products through rigorous usage.
Our advanced molding process allows for vibrant, eye-catching components that enhance visual and tactile enjoyment, elevating user experience.
Plastic injection molding provides design flexibility, enabling medical professionals and engineers to develop innovative and user-friendly medical devices. By incorporating textured surfaces, grips, and multi-component assemblies, it enhances the usability and performance of medical products.
Rigorous maintenance practices guarantee the longevity and precision of our molds, contributing to the sustainability of our operations and products.
Become a part of our integrated client process, where we work with you from conception to production, ensuring that each step adds value to the final product.
Standards often require manufacturers to maintain proper records and traceability throughout the manufacturing process. This involves documenting details such as materials used, manufacturing procedures, inspections conducted, and testing outcomes. Comprehensive documentation is essential as it facilitates actions like product recalls, investigations, and quality audits if necessary.
GETTING A QUOTE WITH LK-MOULD IS FREE AND SIMPLE.
FIND MORE OF OUR SERVICES:
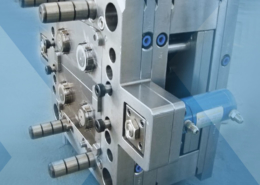
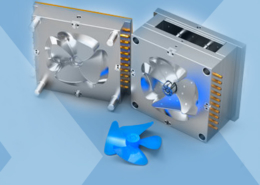
Plastic Molding

Rapid Prototyping
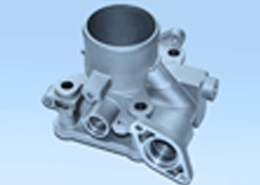
Pressure Die Casting
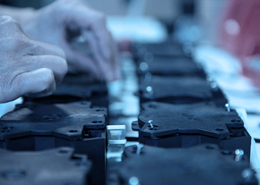
Parts Assembly
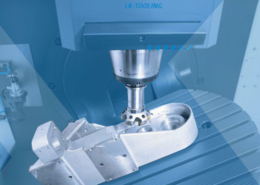