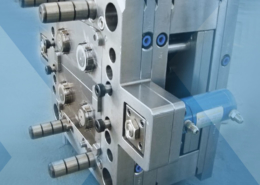
Everest Precision | Manufacturing Of Mould For Mould ... - precision moulding an
Author:gly Date: 2024-10-15
Indeed, OUCO’s state-of-the-art machines seamlessly handle multi-color and multi-material parts production. Contact us to delve deeper into these capabilities.
Material cost is determined by the design of a product, the material utilized, and the quantity of material needed to complete the injection molding process.
For injection molding, special-purpose equipment ranging from tiny personal molding machines that enterprises may use in-house to big industrial injection molding equipment primarily handled by providers, contractors, and major manufacturers is utilized.
To maximize the lifespan and performance of our machines, the automatic lubrication system guarantees regular and accurate distribution of lubricant to all moving parts. This feature reduces wear and tear, prolonging operational capacity while minimizing maintenance demands.
The vertical turntable in OUCO’s multi-component injection molding machines allows quick and precise component alignment, ensuring flawless multi-material integration during the molding process. This feature enables efficient production flow, making the process of complex assembly easier and more reliable.
Injection molding, the major cost driver is generally mold or tooling expenses. Molds for injection molding are typically created in one of three ways:
By streamlining production, reducing labor, and minimizing part assembly, OUCO’s machines significantly boost cost efficiency. Interested in optimizing your production? Contact us.
If a plastic injection mold factory has the tools and materials, creating molds in-house may be the most cost-effective option if the technical expertise is also accessible. If the tools required for injection molding are not easily accessible, outsourcing lowers the cost of developing a mold.
OUCO offers comprehensive support—from installation guidance to operational training and regular maintenance. Need our support? We’re just a message away.
Optimized for superior performance, OUCO’s high-pressure oil cylinders deliver precise, swift, and stable operations for our multi-component injection molding machines. This ensures increased efficiency and accuracy in molding complex, multi-material products.
Creating more sophisticated molds necessitates technical knowledge. As a result, companies typically outsource specific aspects of injection molding, for instance, mold design and production.
By opting for OUCO’s multi-component injection molding machines, you simplify complex assembly tasks while streamlining your manufacturing process. With our machines’ versatile bi-mix injection capabilities, you can efficiently produce a diverse array of intricate products without sacrificing quality. Experience the advantages of OUCO’s multi-component injection molding machines, and propel your production capabilities to new heights.
Depending on the needs of the finished products, a broad range of polymers can be utilized for injection molding. The cost involved when you buy plastic injection mold materials varies depending on the material selected. Thermoplastic pellets range in price from $1 to $5 per kilogram.
3D printers can manufacture basic low volume 3D printed molds for as cheap as $100. A metal mold for a mid-volume service life of 1,000-5,000 units costs between $2,000 and $5,000. Mold costs can range from $5,000 to $100,000 for molds with more complicated shapes and prepared for higher production runs of 10,000+ pieces.
Typically, the cost of the mold, also referred to as the tooling cost, is the major cost driver in injection molding. Let’s take a look at some of the elements that influence the price of an injection mold.
With advanced control systems and high-grade components, OUCO machines ensure the highest precision in multi-component molding. Let’s connect for more insights into our technology.
With small desktop injection molding equipment and 3D printed molds, creating modest volumes of components with injection molding is the most cost-effective. Small-scale automated injection molding machines are viable options for medium-series manufacturing of small components.Large industrial injection molding machines can range in price from $50,000 to more than $200,000. These machines also have more strict facility requirements and the need for specialized staff for operations, upkeep, and monitoring. As a result, although injection molding is a core competency, most businesses outsource mass manufacturing to service providers and contract manufacturers, with equipment expenses included in the service prices.
The simple answer is that plastic injection molds range in price from $100 for a 3D printed injection mold to $100,000 plus for a sophisticated multi-cavity steel mold for greater manufacturing loads, which is typically the most important fixed start-up cost in injection molding. However, because these expenses are spread across hundreds or thousands of components, injection molding is a suitable method for mass-producing plastic parts at a low cost.
When it comes to injection molding prices, basic plastic injection molds might range from $3,000 to $6,000. A big, more sophisticated high-production, cross-cavity mold can cost between $25,000 and $50,000 or more. Although it may seem obvious, several factors contribute to the cost of injection molding.
Offering an adjustable pitch parallel injection table, OUCO ensures utmost flexibility in your production line. This feature allows the accommodation of varying mold sizes and designs, allowing your business to cater to a wide array of product specifications with ease.
OUCO’s multi-component machines accommodate a diverse range of thermoplastics, providing you with wide-ranging production options. To discuss your material specifics, feel free to get in touch.
OUCO’s machines demonstrate remarkable adaptability to various industry needs, thanks to their advanced features and versatile design. Share your requirements and let’s discuss tailored solutions.
At OUCO, our multi-component injection molding machines are designed to bring unmatched flexibility and precision to your production process. Equipped with cutting-edge technology, our machines enable seamless multi-material integration and high-quality multi-color molding, ensuring your products stand out in a competitive market. Our multi-component injection molding machines cater to a wide range of industries, delivering unparalleled solutions for complex product designs.
Mold manufacturer location: This was also mentioned while researching how mold size may affect your total injection molding expenses. To have your mold wherever it needs to go, an off-site plastic injection mold maker will charge you extra for shipping and handling.
To a certain degree, asking for the costs of plastic injection molds cost is similar to questioning how much a car costs. Is your mold going to be a Pinto or a Porsche? Also, keep in mind that the cost of a mold is only the beginning. To calculate complete plastic injection molding costs for any projects, you must also include raw material, operating, and maintenance expenses in the future. These costs are a result of the aforementioned contributing factors.
OUCO’s machines are designed to reduce material waste and optimize energy efficiency, contributing to a greener production process. If you’re interested in our sustainability initiatives, let’s have a conversation.
GETTING A QUOTE WITH LK-MOULD IS FREE AND SIMPLE.
FIND MORE OF OUR SERVICES:
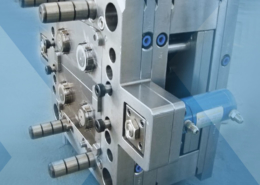
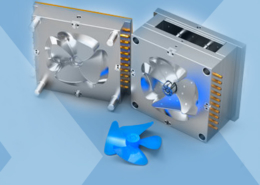
Plastic Molding

Rapid Prototyping
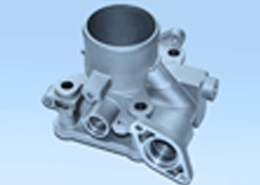
Pressure Die Casting
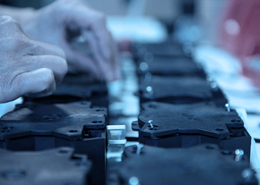
Parts Assembly
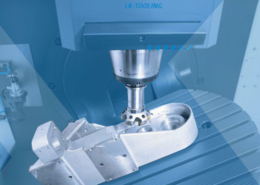