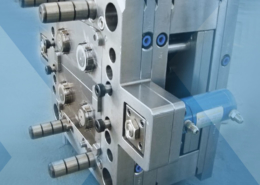
Effective Injection Molding Prototype Guide: Expert Tips - plastic molding proto
Author:gly Date: 2024-10-15
Our molding experience covers the knowledge of good Design for Manufacturability, a comprehensive understanding of all thermoplastic resin families, and custom injection-mold design expertise. Typically, we stock more than 150 varieties of resins at any given time in our 200,000-square-foot facility, conveniently located to the major markets of the Midwest and East Coast.
Ferriot’s experienced engineers are here to guide you through every critical step in your injection molding journey, from concept to completion.
If you disable this cookie, we will not be able to save your preferences. This means that every time you visit this website you will need to enable or disable cookies again.
Structural foam is a manufacturing material which pairs a foamed core with a solid outer layer. It is lightweight and flexible but maintains the good strength and stiffness compared with traditional polymers. Here is a list of the top 6 advantages when thinking about structural foam.
Ferriot’s structural foam molding process manufacturer services extend through final production, complete with custom color, cosmetic finishing, and assembly.
When the design is just right, the result is high productivity, cost savings, and lighter plastic components that are exceptionally rigid on the exterior and foamed at the core.
With our highly experienced team of engineers, we design and engineer custom structural foam solutions that didn’t exist yesterday (except in the minds of our customers).
Definition A short shot is the incomplete filling of a mold cavity which results in the production of an incomplete part. If a part short shots, the plastic does not fill the cavity. The flow freezes off before all of the flow paths have filled. To ensure the finished part is of good quality, the part must also be adequately packed with plastic. Therefore the question to ask is not only, 'Will the part fill?', but, 'Can a good quality part be made?'
Far more than the simple application of additives, the key to success in this molding type is the ability to incorporate structural foam into a custom design.
Remedies Before you try one of the methods listed below, check all of the other results, so that you know the exact cause of the short shot. Avoid hesitation Eliminate air traps If air traps do exist, they should be positioned in regions that can be easily vented or ejection pins added so that air can be removed. Increase mold & melt temperature This will decrease the viscosity of the melt, making it easier to flow through the part. Increase ram speed This can cause greater shear heating, which can decrease the viscosity of the melt, making it easier to flow through the part. Change part geometry Balance flow paths so they fill in an equal time and an equal pressure. You may need to thicken thin sections, or reduce the complexity of a flow path. Change material Select a less viscous material (higher melt flow rate). By choosing a material with a higher melt flow rate, less injection pressure will be required to fill the part. Increase the maximum injection pressure for this part Solving one problem can often introduce other problems to the injection molding process. Each option hence requires consideration of all relevant aspects of the mold design If you need high quality injection mold tooling, Contact us. If you need high quality plastic extrusion services, Pls contact us sales@viewmold.com If you need high quality sheet metal parts, Pls contact us sales@viewmold.com Injection Molding air trap issue and solution Injection Molding brittleness issue and solution Injection Molding burn issue and solution Injection Molding crack issue and solution Injection Molding delamination issue and solution Injection Molding dimensional variation issue and solution Injection Molding discoloration issue and solution Injection Molding excessive part weight issue and solution Injection Molding fish eye issue and solution Injection Molding flash issue and solution Injection Molding follow line issue and solution Injection Molding hesitation issue and solution Injection Molding high volumetric shrinkage issue and solution Injection Molding jetting issue and solution Injection Molding overpacking issue and solution Injection Molding racetrack effect issue and solution Injection Molding short shot issue and solution Injection Molding sink mark and void issue and solution Injection Molding unbalanced flow issue and solution Injection Molding underflow issue and solution Injection Molding warpage issue and solution Injection Molding weld and meld line issue and solution
Overall, structural foam molding offers a compelling combination of strength, lightweight construction, cost-effectiveness, design flexibility, and enhanced performance properties, making it a preferred choice for various industrial applications.
As one of the few “systems houses” in North America, Ferriot can step in at any point in the manufacturing process because our engineering, design, molding, and tooling, and finishing technologies can be applied to products in concept development or at any other stage of production.
This website uses Google Analytics to collect anonymous information such as the number of visitors to the site, and the most popular pages.
One of the biggest challenges in any new product development effort is identifying skilled people who can contribute significantly to the project, including the vendors who support the process. Ensuring the success of a new product demands the freedom to use new materials and new suppliers, as complex design and production challenges arise.
Indeed, the measure of Ferriot’s true capacity is our institutional expertise in resin selection to support innovative solutions.
Injection Molding defect:molding short shot All Injection molding defects>Solving molding short shot problems Definition A short shot is the incomplete filling of a mold cavity which results in the production of an incomplete part. If a part short shots, the plastic does not fill the cavity. The flow freezes off before all of the flow paths have filled. To ensure the finished part is of good quality, the part must also be adequately packed with plastic. Therefore the question to ask is not only, 'Will the part fill?', but, 'Can a good quality part be made?' Causes Flow restrictions Due to channels freezing or inadequate runner design. Hesitation and long or complex flow paths Inadequate venting Back pressure due to unvented air traps can cause a short shot. Low melt and/or mold temperatures Insufficient material entering the cavity An undersized machine, low shot volume, or inadequate ram speed. Machine defects Including an empty hopper, blocked feed throat, or a worn non-return (check) valve that causes loss of pressure or volume leakage. Remedies Before you try one of the methods listed below, check all of the other results, so that you know the exact cause of the short shot. Avoid hesitation Eliminate air traps If air traps do exist, they should be positioned in regions that can be easily vented or ejection pins added so that air can be removed. Increase mold & melt temperature This will decrease the viscosity of the melt, making it easier to flow through the part. Increase ram speed This can cause greater shear heating, which can decrease the viscosity of the melt, making it easier to flow through the part. Change part geometry Balance flow paths so they fill in an equal time and an equal pressure. You may need to thicken thin sections, or reduce the complexity of a flow path. Change material Select a less viscous material (higher melt flow rate). By choosing a material with a higher melt flow rate, less injection pressure will be required to fill the part. Increase the maximum injection pressure for this part Solving one problem can often introduce other problems to the injection molding process. Each option hence requires consideration of all relevant aspects of the mold design If you need high quality injection mold tooling, Contact us. If you need high quality plastic extrusion services, Pls contact us sales@viewmold.com If you need high quality sheet metal parts, Pls contact us sales@viewmold.com Injection Molding air trap issue and solution Injection Molding brittleness issue and solution Injection Molding burn issue and solution Injection Molding crack issue and solution Injection Molding delamination issue and solution Injection Molding dimensional variation issue and solution Injection Molding discoloration issue and solution Injection Molding excessive part weight issue and solution Injection Molding fish eye issue and solution Injection Molding flash issue and solution Injection Molding follow line issue and solution Injection Molding hesitation issue and solution Injection Molding high volumetric shrinkage issue and solution Injection Molding jetting issue and solution Injection Molding overpacking issue and solution Injection Molding racetrack effect issue and solution Injection Molding short shot issue and solution Injection Molding sink mark and void issue and solution Injection Molding unbalanced flow issue and solution Injection Molding underflow issue and solution Injection Molding warpage issue and solution Injection Molding weld and meld line issue and solution
This website uses cookies so that we can provide you with the best user experience possible. Cookie information is stored in your browser and performs functions such as recognising you when you return to our website and helping our team to understand which sections of the website you find most interesting and useful.
Back pressure due to unvented air traps can cause a short shot. Low melt and/or mold temperatures Insufficient material entering the cavity An undersized machine, low shot volume, or inadequate ram speed. Machine defects Including an empty hopper, blocked feed throat, or a worn non-return (check) valve that causes loss of pressure or volume leakage.
Contact us to discuss the advantages and benefits of a custom design for structural foam-molded components to optimize performance.
As structural foam injection molding process gains increased attention, you may be wondering whether it’s time to replace metal or traditional plastic components with lighter and stronger engineered plastics.
Causes Flow restrictions Due to channels freezing or inadequate runner design. Hesitation and long or complex flow paths Inadequate venting Back pressure due to unvented air traps can cause a short shot. Low melt and/or mold temperatures Insufficient material entering the cavity An undersized machine, low shot volume, or inadequate ram speed. Machine defects Including an empty hopper, blocked feed throat, or a worn non-return (check) valve that causes loss of pressure or volume leakage.
GETTING A QUOTE WITH LK-MOULD IS FREE AND SIMPLE.
FIND MORE OF OUR SERVICES:
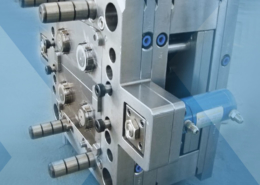
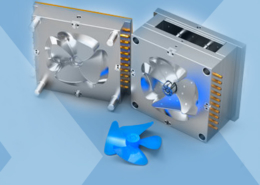
Plastic Molding

Rapid Prototyping
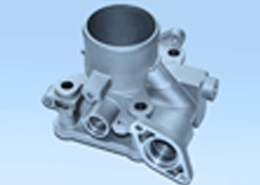
Pressure Die Casting
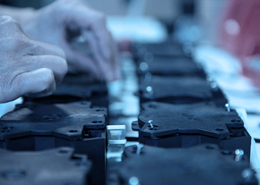
Parts Assembly
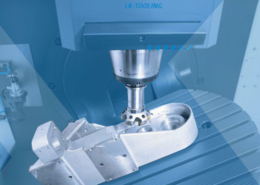