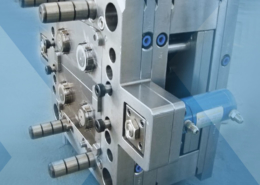
Drake Plastics: Torlon and PEEK Manufacturing | Stock ... - peek injection moldi
Author:gly Date: 2024-10-15
Now that you understand the benefits of plastic injection molding for medical components and devices as well as the specific requirements these components must meet, we’ll take a look at some of the specific materials that fit the bill. In general, plastics offer benefits over other materials and processes in the areas of design flexibility, overall cost-effectiveness and speed of production. Consider the following materials for your project:
As technology continues to evolve, all-electric injection molding machines stand as a testament to the industry’s commitment to progress, precision, and sustainability.
These are just a few of the ways medical device plastic injection molding is used. The process of plastic injection molding medical parts can be applied to nearly any area where durable, sterilization-friendly parts are required at high volume and with exceptional accuracy in production.
However, it’s essential to weigh these benefits against their higher costs, technical requirements, and certain operational limitations. Understanding the offerings of leading brands, both domestic and international, can further guide decision-makers in choosing the right equipment for their specific production needs.
These machines are especially beneficial in sectors where high precision and consistent replication are critical, such as in the production of medical devices and precision electronics. Overall, all-electric injection molding machines signify a progressive step in injection molding technology, embodying efficiency, precision, and environmental sustainability.
Overall, the shift to all-electric injection molding machines represents a significant leap in manufacturing efficiency and precision, aligning with modern demands for high-quality, cost-effective, and environmentally friendly production.
All-electric injection molding machines represent a significant innovation in the field of injection molding, distinguished by their use of electric servo motors to control all operational movements. This is a departure from traditional hydraulic injection molding machines, which rely on hydraulic systems to perform key functions such as mold opening and closing, plastic injection, and product ejection.
These brands, with their diverse range of all-electric injection molding machines, cater to various industrial needs, emphasizing innovation, efficiency, and precision. Their contributions significantly shape the landscape of modern manufacturing technology.
In drawing upon injection molding, medical industry suppliers and manufacturers gain access to several benefits inherent to the process and the materials available. These benefits include:
With these tips in hand, you’ll be able to make an informed decision about the material and process that’s best for your medical device or component manufacturing.
Understanding these drawbacks is crucial for manufacturers considering an investment in all-electric injection molding machines, ensuring a balanced assessment of their potential in various production environments.
Below is a comparison chart that outlines the main differences between traditional hydraulic injection molding machines and all-electric injection molding machines, focusing on their essential characteristics.
It’s essential for users to grasp what these machines are and the appropriate scenarios for their use. This article aims to explain these aspects in an uncomplicated and precise manner.
Injection molding is a widely used manufacturing process in the medical industry, offering numerous advantages for a variety of applications. Medical-grade plastics injection molding is used for medical devices, components, laboratory and facility equipment, and more. Among the key advantages of the injection molding process are its ability to meet the exacting specifications and regulatory needs of the medical industry, which we’ll discuss in further detail below.
In conclusion, the journey into the world of all-electric injection molding machines reveals a landscape rich in innovation and efficiency. These machines offer a multitude of advantages, including precision, energy efficiency, and environmental friendliness, making them an increasingly popular choice in various manufacturing sectors.
In all-electric machines, servo motors replace these hydraulic systems. This change brings about notable benefits, including enhanced precision and speed in each action. Additionally, the integration of pressure and temperature sensors facilitates closed-loop control, significantly elevating manufacturing accuracy.
Servo motors make these machines more energy-efficient compared to traditional hydraulic counterparts. They consume energy only when necessary, leading to electricity savings of 40-60%.
Plastic injection molding for medical devices is a critical process where the stakes of failure are very high. As such, several considerations must be taken into account during the design, planning and manufacturing processes. These include:
Despite their numerous benefits, all-electric injection molding machines also present certain challenges and limitations, including:
For many individuals, the term “all-electric injection molding machine” might be relatively unknown or perceived as a complex, high-end technology. However, this technology, which originated in the 1980s, experienced significant advancements in the 1990s.
Medical suppliers have found that plastic injection molding medical parts, components and devices is one of the most effective ways to attain the quality and specifications they need in a cost-effective and efficient manner. Medical device plastic injection molding is used for applications such as:
The realm of all-electric injection molding machines is marked by the presence of both prominent domestic and global manufacturers, each bringing their own expertise and innovations to the field.
GETTING A QUOTE WITH LK-MOULD IS FREE AND SIMPLE.
FIND MORE OF OUR SERVICES:
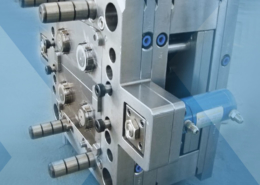
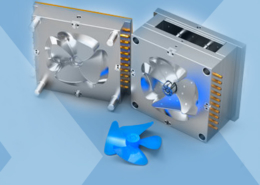
Plastic Molding

Rapid Prototyping
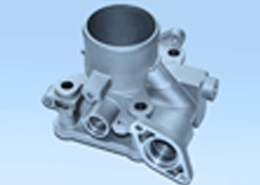
Pressure Die Casting
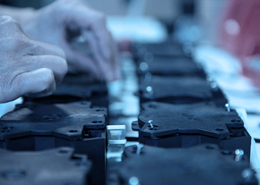
Parts Assembly
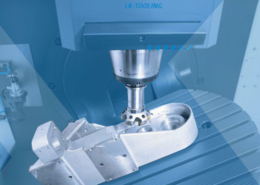