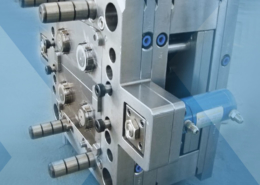
Double-Shot Injection Molding - dual shot injection molding
Author:gly Date: 2024-10-15
Injection molding offers a reliable and economical option for producing high-quality automotive components. forteq has been a leader in precision engineering and plastic molding for more than five decades.
Seaway Plastics Engineering, LLC is a company specializing in low-volume production runs. It is located in Port Richey, Florida, and has 122 employees. The company can deliver low-volume production runs on time, on spec, and within your budget. The industries they serve are Defense, packaging, aerospace, transportation, food service, industrial electronics, and consumer products.
The noted industrial marketplace IndustryNet is witnessing a surge in domestic sourcing activity, especially in the plastic injection molding sector, which recorded more than 1500 searches from industrial buyers interested in plastic molding services in 2021: year-on-year category searches, requests for quotes, and catalog downloads have seen a significant spike.
Injection molding offers a number of benefits. One of the biggest advantages is the ability to produce a part consistently at a very high quality. Quality is essential to a vehicle’s safety and reliability. Plastic injection molding using ensures consistent and repeatable tolerances and a high level of precision.
As the demand for injection-molded products continues to grow, these companies are poised to maintain their position at the forefront of the industry, driving innovation and shaping the future of manufacturing.
The top injection molding companies in the country have been identified as leaders in their field, providing high-quality products, innovative solutions, and exceptional customer service.
We offer customers the same high quality regardless of the molded part’s complexity. We are a global solution provider, with locations in Europe, the US and China. So customers can be sure of getting the same high quality around the world.
Things were going fine for China, but then the COVID-19 pandemic shook the world, forcing people to move their manufacturing units and supply chains from China.
One of the drawbacks of injection molding is that the cost of tooling and machinery can be high initially. This can make producing small runs of parts less cost-effective, especially if you only need a low volume of parts.
This Clintonville, Wisconsin, manufacturer has 75 employees and offers design and product development services to create customized solutions. Some of its products include folded towel dispensers, napkin dispensers, toilet tissue dispensers, and roll towel dispensers.
American Toll & Mold Inc is a specialized custom mold manufacturing company supplying its mold to 21 countries. This Clearwater, Florida company has 180 employees. It creates various molds depending on the applications, like 8+8 stack mold, 32 cavity single face mold, 16 cavities unscrewing mold, 8 cavities unscrewing mold, and 2*2 Two material mold.
The specialized verticals are Cosmetics, Consumer products, food & beverages, stock packaging, pharmaceutical, and personal care.
Hi-Tech Mold & Engineering, Inc. is located in Rochester Hills, Michigan, with 175 employees. It provides molding services like machining, benching, polishing, tool assembly, additive manufacturing & 3D printing, and EDM. It specializes in catering to automotive, defense, aerospace, electric vehicles, medical devices, appliances, and recreational vehicles.
Plastic components manufactured using injection molding offer greater options in terms of materials and colors. A wide range of polymers can be used, giving the designer more options and increasing the options for using plastics rather than metal.
American companies hold the quality and precision for making world-class plastic molding products. So now there’s no need to outsource our supply chains somewhere else.
Injection molding is one of the most widely used processes for making plastic components. It’s an optimal solution for producing precise, high-quality parts.
No matter where they’re located, plastic components need to be high quality and robust. One of the most reliable methods for producing high-quality plastic components is injection molding.
With injection molding it is also possible to rapidly develop and test prototypes. forteq has its own in-house tooling center and can develop its own molds, thus reducing costs and time to production.
Located in North Vernon, Indiana, the company has 110 employees and provides services like prototype tooling and tool design. It mainly produces components for the automotive, defense, and aerospace industries.
Plastek Industries Inc. is headquartered in Erie, Pennsylvania, and is its largest manufacturing facility in the US. The worldwide employee strength is 1200, with 850 located in the US. It provides services like Molding/Assembly, Package Development, and Mold Design/Manufacturing.
Plastic offers a lightweight alternative to metal in automotive applications. One of the benefits of plastic is that it reduces the vehicle’s overall weight. This improves energy efficiency. As a result, plastic components are increasingly being installed in modern cars. Such parts can be found under the hood, in the car’s interior and on its exterior.
The plastic injection molding industry is a critical manufacturing sector in the US, with a wide range of applications in various industries.
The manufacturer is located in Boyne City, Michigan. It has 325 employees domestically and provides molding services to the automotive industry. It has a few of the largest automotive companies on the list of clientele.
In 2022, the estimated size of the worldwide injection molding market was USD 261.8 billion, and it is expected to grow at a compounded annual growth rate (CAGR) of 4.8% from 2023 to 2030.
Plastic injection molding is a widespread industry in the United States. However, it’s not the global growth driver of the injection molding industry, but it’s China. This country lifted over 700 million people out of poverty within a span of thirty years. It is famously named “Worlds Factory” for an excellent reason.
These companies have demonstrated their expertise and commitment to excellence from medical devices and consumer goods to automotive and aerospace components.
Injection molding is a manufacturing process used to produce parts by injecting molten material into a mold cavity, where it cools and solidifies into the desired shape. It is commonly used to mass-produce products made of plastic, metal, and other materials.
This Louisville, Kentucky, manufacturer has 2400 employees, with 1310 in the US. The company provides services like Injection molding. Product development, tooling, value-added operations, and Paint & Hydrographics to verticals like Automobiles, Appliance, outdoor sports, household products, and power sport vehicles.
A basic plastic injection mold with a single cavity is typically priced between $1,000 and $5,000. For more intricate and larger molds, the cost can exceed $80,000. The average cost for a mold that produces a straightforward part small enough to fit in your hand is around $12,000.
Polycarbonate is one of the most durable thermoplastic materials and is highly resistant to shattering, making it a popular choice for injection molding applications.
This Ironwood, Michigan manufacturer creates molds for products with precise requirements. It has 210 employees and works on Hi-Tech engineering principles providing molding services like two-shot molding, pressure monitoring, laser scanning, reel-to-reel molding, overmolding, close tolerance molding, insert molding, and flow analysis.
Located in Saline, Michigan, MMI Engineered Solutions employs 86 people and parts from manufacturing injection molding components; it also provides services like designing, tooling, and material handling.
GETTING A QUOTE WITH LK-MOULD IS FREE AND SIMPLE.
FIND MORE OF OUR SERVICES:
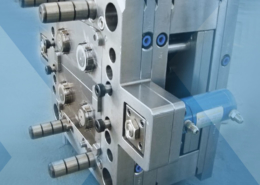
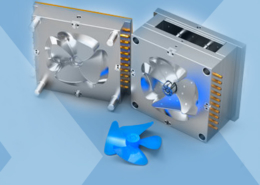
Plastic Molding

Rapid Prototyping
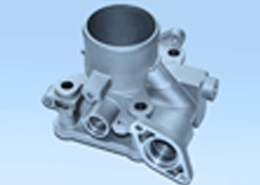
Pressure Die Casting
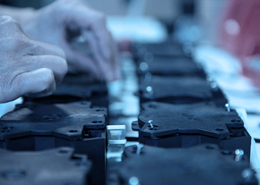
Parts Assembly
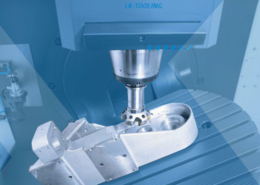