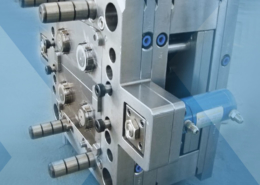
Double injection molding | Two Shot Injection Moulding - double shot injection m
Author:gly Date: 2024-10-15
Through UnitedHealthcare, UMR creates and publishes the Machine-Readable Files on behalf of Crescent Industries, Inc. To link to the Machine-Readable Files, please click on the URL provided: https://transparency-in-coverage.uhc.com/
Rubber molding is a process of transforming uncured rubber or an elastomer into a usable product by transferring, compressing, or injecting raw rubber material into a metal mold cavity...
Forging is a metal working process that manipulates, shapes, deforms, and compresses metal to achieve a desired form, configuration, or appearance outlined by a metal processing design or diagram...
Plastic processes differ greatly in both the way they form plastic products and in the shape and structural integrity of the products they manufacture. Blow molding, for example, is nearly the sole method by which plastic bottles for beverages, household cleaners, and cosmetic products are made, as well as a range of low-cost toys and parts with low to medium performance. The extrusion process creates linear profiles, strips, and sheets with high structural integrity useful in many construction siding, trim, and furniture applications. Vacuum forming, or thermoforming, forms trays, linings, and thin plastic packaging from heated plastic sheets, while dip molding forms a variety of soft molds and plastic coatings. Other plastic molding processes use casts, or dies; injection molding squeezes melted (or plasticized) plastic resin into a closed mold, forming a solid plastic object, while rotational molding uses a type of gyroscope to evenly coat the inside of a mold, creating hollow parts with high impact resistance.
Plastic has revolutionized the production of medical equipment since the 1930s. The plastic injection molding of medical parts has played a crucial role in creating essential components to help the medical field stay safe and sanitary, improving the quality of the healthcare industry worldwide. So, here is a thorough dive into the importance of plastic injection molding in the medical industry and some common applications.
This diagnostic equipment includes test kits, blood/fluid monitoring, and infectious disease diagnostics. Plastic injection molding produces test housings, sample wells, and reagent containers with precise dimensions for these products. It also enables integrating features like reaction zones, mixing channels, and test strip holders. All of this helps to create medical devices that offer reliable results.
Custom injection molding makes these tools lightweight and durable, ensuring comfort and reliability for doctors and patients.
Utilizing injection molding services enables diagnostic equipment and disposable items to be made cost-effectively while maintaining reliability.
The manufactured demand definition, often known as on-demand manufacturing or manufacturing on demand (MOD), is a relatively new idea in the manufacturing industry. In an on-demand manufacturing system, goods are only...
Plastic injection molding enables the production of medical components used in labware equipment and instrumentation, diagnostic disposables, imaging components, patient care devices, pharmaceutical packaging, and more!
From knee and hip replacements to dental implants, the plastic molding manufacturing technique creates customized, patient-specific solutions that guarantee patients' comfort, functionality, and safety.
Screw machined parts are complex pieces that are typically cylindrical and threaded and a screw machined product is a family of automatic lathes for small to medium-sized components. Screws, bolts, pins, fittings...
Medical device injection molding offers numerous advantages, contributing to the efficiency, precision, and cost-effectiveness of creating and manufacturing medical components. Some of the key benefits are:
Our website has all the information you need to get started on your next medical device project. Explore our resources and find out how we can help bring your idea to life.
Plastic molding processes vary greatly in cost. High-end plastic molding processes, such as rotational molding and injection molding, provide precision three-dimensional plastic parts with structural integrity and impact resistance a few other processes or materials can provide. On the other end of the spectrum, blow molding and dip molding processes offer very affordable options for long runs and mass production of containers and household commodity items. A wide range of plastic materials is molded through these processes, although some processes are more effective with certain polymers than others.
Finally, specimen containers are also made using plastic injection molding. This includes collecting and storing biological samples, which requires reliably leak-proof seals and compatible materials that won't affect the specimen in any way.
Medical device contract manufacturers supply the healthcare industry with countless plastic products. Here are some common types of injection molded medical parts.
When producing medical parts through plastic injection molding, partnering with a trusted, experienced medical injection molding company is paramount. Crescent Industries offers specialized expertise that ensures your medical equipment and components are precise, safe, sanitary, and precisely what you need.
Plastic Molding Manufacturing Companies | Contract Manufacturing Companies | Home | Request for Quote | Photo Gallery | Privacy Policy/Terms of use | List of Companies | Sitemap
Die casting is a high pressure metal casting process that forces molten metal into a mold. It produces dimensionally accurate precision metal parts that have a flawless smooth finish...
Metal fabrication is the process of turning sheet metal and other flat metals into predetermined forms. The process begins with sheet metal no thicker than a quarter inch. The metal is malleable enough to take on various shapes at...
Surgical and dental instruments heavily rely on plastic injection molding for their production. Plastic injection molding creates instruments with ergonomic designs, which enhances usability and comfort for healthcare professionals and patients alike.
Lab consumables, such as microplates, pipette tips, and centrifuge tubes, are also created using injection molding. This also allows for high precision and consistency. The ability to manufacture consumables in large quantities at a lower cost also makes them widely accessible in research, diagnostics, and clinical laboratories.
Plastic injection molding medical parts also creates drug-delivery and tamper-evident packaging for pharmaceutical products. These products rely on the precision and consistency provided by injection molding:
Plastic injection molding, or commonly referred to as injection molding, is a manufacturing process used in the mass fabrication of plastic parts. It involves an injection of molten plastic material into the mold where it cools and...
Contract manufacturing is a business model in which a company hires a contract manufacturer to produce its products or components of its products. It is a strategic action widely adopted by companies to save extensive resources and...
Medical device components must meet strict regulatory requirements by the FDA to ensure the safety of patients. Manufacturing these plastic components with consistent accuracy is crucial for their functionality and reliability.
Each requires customized medical plastics produced by professional injection molding services to ensure the highest quality and patient satisfaction.
Metal stamping is a coldworking process that transforms sheets of metal into specific, preset shapes. It uses specialized tooling which involves the stroke of the punch that brings conformational change to the metal sheet...
GETTING A QUOTE WITH LK-MOULD IS FREE AND SIMPLE.
FIND MORE OF OUR SERVICES:
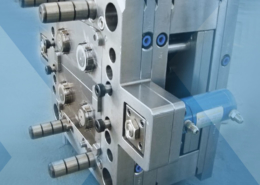
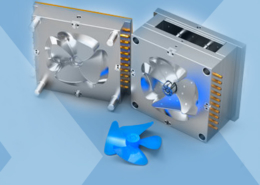
Plastic Molding

Rapid Prototyping
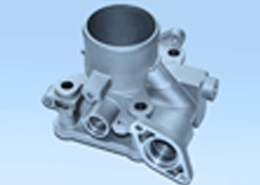
Pressure Die Casting
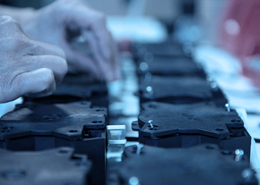
Parts Assembly
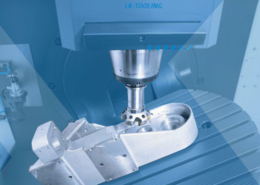