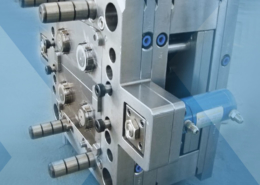
DIY Injection moulding or short run moulds/sprues - short run molding
Author:gly Date: 2024-10-15
© 2021 © MASPI S.R.L. | Via Castegnate, 86 - 24030 Terno d'Isola (BG) | Tel. +39.035.4944117 | P.IVA IT00781490164 Web Horizondesign
ICOMold’s fast-turn, low-cost, high-value injection molding enhanced by joining Fathom’s manufacturing platform. Learn More
The experts at ICOMold by Fathom are here to answer all of your questions about injection mold cost. Feel free to use our online quote system as a mold cost calculator or reach out to one of our plastic injection molding experts.
Thermoplastic resins with different qualities can be used in the injection molding process. The type of plastic will also be a major factor when doing injection mold cost calculations. Choosing the right plastic resin will depend on what the part is designed to do. The cost of plastic resins will range from $2 to $20 per pound. The amount of plastic used in each injection will depend on the mold size and complexity. Some of the plastic characteristics that can affect cost are:
ICOMold by Fathom uses only high-quality, pre-hardened steel for injection mold tooling. Using steel may have a slightly higher upfront cost but the steel molds will last longer, resist danger better, and save the customer money in the long run.
ICOMold by Fathom offers an online quote system for custom plastic injection molding, CNC machining, or urethane casting projects. There is no software to download – just upload the CAD model to the online portal and select the desired options like part quantity, material, and finish.
In many cases, in the traditional transformation process, some points of the article are subjected to too much pressure during the process, thus causing possible deformation of the final article. However, in Co-injection since the articles are thicker, they are able to withstand higher pressures without generating any type of distortion. The articles obtained have thicknesses from 15 to 40 mm.
Injection mold cost estimates will also depend on the proprietary technology used by each mold manufacturer. Ask questions to ensure the mold making process matches the output and budget for your project.
Yes! ICOMold by Fathom offers an online quote system. The process of calculating mold costs can be rather complex. The final cost of the project will depend on several factors; the mold size, type, and complexity, the plastic material being used, and the production run numbers. Contact the experts at ICOMold to learn more about plastic injection molding costs or to get guidance for your next project.
The last factor to consider is the number of injection cavities machined into the mold. High-production molds can have multiple, identical injection cavities. These are typically referred to as muti-cavity Molds. Family molds are molds that have two or more similar cavities that aren’t necessarily identical. An example would be the right and left side of part that snaps together. These molds will have multiple cavities that will produce the same part or related parts in just one pressing, reducing the number of times the mold needs to be opened and closed while increasing production efficiency.
Plastic injection molds are usually made of steel or aluminum. Aluminum has several benefits over steel. Aluminum is typically cheaper than steel and can better dissipate heat, which will lower cycle time and help increase efficiency. While Aluminum may have lower up front costs, it does have issues with durability. Injection molds made of steel are slightly more expensive, but will last longer, ultimately lowering the per-piece-price for each part. Steel injection molds should be used for production runs, as they will hold up to the heat and pressure better than molds made of aluminum. Steel molds can also be easily modified by welding or reworked for changes in design or for repairs. Aluminum molds wear down quickly and cannot be repaired or modified.
Simple, single cavity injection molds can cost as little as a couple thousand dollars. Larger, more complex, high-production, multi-cavity molds can cost upwards of $25,000 to $50,000 or more. The typical injection mold cost will be between $4,500 and $16,000.
The first great advantage of this technique is the reduction of CO2 emissions, obtaining articles with recycled material of great aesthetics, the second is the possibility to have larger thicknesses of the article reducing the risk of deformation.
The Restylon technology allows the realization of Co-injection products with the use of second life material, producing high quality articles without deformation.
A business owner or project manager will seek out several injection molding quotes from competing companies. It is important to know the details behind the price since each mold manufacturer may use a different approach. Customers should ask about the mold material and how it will be machined. Conventional machining can be slow and expensive. Molds made with Computer Numerical Control (CNC) machining or Electrical Discharge Machining (EDM) can be produced much quicker and with a higher degree of detail.
There are several things you can do to help control and lower costs when it comes to injection molding. Some of the more common items are:
Traditional molding is the injection transformation technique for the production of items with small to medium thicknesses. The process starts with the insertion of virgin material through the injection metering zone into the machine, which once melted, is injected into the mold. The machine has a single plasticizing metering zone that brings the plastic into the melt and injects it into the mold. This is followed by a cooling time and subsequent extraction of the piece by an automated arm. On average, articles with a maximum thickness of 6/8 mm are produced. Co-injection molding differs from the previous process in that the material injection metering zone become two and no longer one.The two materials are divided into the body (core) and the skin of the article. This innovative process allows to melt together recycled materials, obtaining an aesthetic of the product equal to the traditional molding with virgin material. In the process, the recycled material forms the core of the article, which is covered by the virgin material that makes up the skin. Moreover, in most cases the core is added with expanding granules to avoid the deformation of the article. The first great advantage of this technique is the reduction of CO2 emissions, obtaining articles with recycled material of great aesthetics, the second is the possibility to have larger thicknesses of the article reducing the risk of deformation. In many cases, in the traditional transformation process, some points of the article are subjected to too much pressure during the process, thus causing possible deformation of the final article. However, in Co-injection since the articles are thicker, they are able to withstand higher pressures without generating any type of distortion. The articles obtained have thicknesses from 15 to 40 mm. The Restylon technology allows the realization of Co-injection products with the use of second life material, producing high quality articles without deformation.
The plastic injection molding process can cost anywhere from $3,000 to $100,000 or more. Simple molds are typically in the $3,000 and $6,000 range while the price for large, more complex, high-production, or multi-cavity molds can cost $25,000 to $50,000 or more. Considering all the variables involved will help determine the overall injection mold cost. It is very important to weigh the cost of the mold against the number of parts being produced. Higher production numbers will lower the final per-piece cost of each part as the total injection mold cost can be spread out over hundreds or thousands of parts. While the upfront cost for injection molding can be significant, it is still the fastest, most economical way to produce large quantities of plastic parts.
Co-injection molding differs from the previous process in that the material injection metering zone become two and no longer one.The two materials are divided into the body (core) and the skin of the article. This innovative process allows to melt together recycled materials, obtaining an aesthetic of the product equal to the traditional molding with virgin material. In the process, the recycled material forms the core of the article, which is covered by the virgin material that makes up the skin. Moreover, in most cases the core is added with expanding granules to avoid the deformation of the article.
Parts that do not need these special qualities can be made with cheaper plastic resin, which may result in significant savings.
Traditional molding is the injection transformation technique for the production of items with small to medium thicknesses. The process starts with the insertion of virgin material through the injection metering zone into the machine, which once melted, is injected into the mold. The machine has a single plasticizing metering zone that brings the plastic into the melt and injects it into the mold. This is followed by a cooling time and subsequent extraction of the piece by an automated arm. On average, articles with a maximum thickness of 6/8 mm are produced.
The majority of the cost for plastic injection molding will be the machining of the injection mold. Injection molding costs are calculated based on several factors. The first and most important factor is the size, followed by the complexity of the mold. Large, complex molds will cost more than smaller, simple molds. The type of mold will also help determine price. Prototype injection molds will cost less than molds used for production runs. Molds built specifically for long production runs will be more expensive. Molds made for extended production will need to be made of high-strength steel that can stand up to repeated use.
GETTING A QUOTE WITH LK-MOULD IS FREE AND SIMPLE.
FIND MORE OF OUR SERVICES:
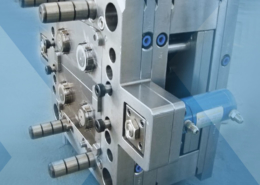
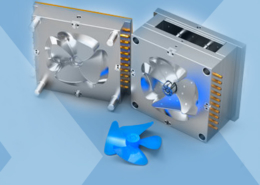
Plastic Molding

Rapid Prototyping
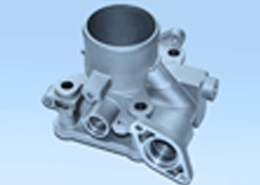
Pressure Die Casting
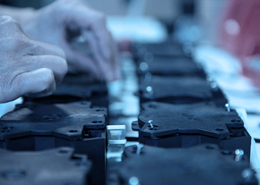
Parts Assembly
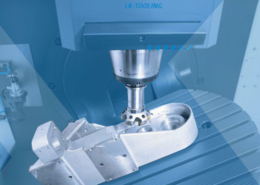