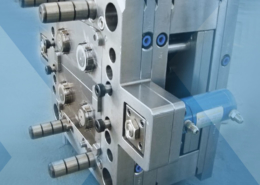
DIY injection molding : r/InjectionMolding - casting plastic at home
Author:gly Date: 2024-10-15
Tough Black (Loctite Henkel 3843) and Ceramic-Filled (BASF 3280) are two new advanced photopolymer materials now available for 3D printing.
Pretty parts are nice, but they often require bead blasting, EDM, or high mold polish to achieve an elevated level of cosmetic appearance. This drives up tooling costs. Anything greater than a PM-F0 (as machined) finish requires some level of hand work, up to an SPI-A2 mirror finish using Grade #2 diamond buff. Avoid fine finishes such as these unless they’re required for the job. One thing to consider regarding cosmetics is to let Protolabs know if you need the entire half of the mold polished or maybe just one small area. You could save costs by only polishing the area needed versus the entire side of a mold. When requesting a custom finish, just send Protolabs a color-coded image of the critical areas and desired finish level for each area.
Our helpful design aid demonstrates part features that are too thin or too thick, bad bosses, right and wrong ribs, and other considerations to be mindful of while designing parts for injection molding.
OEM or Original Equipment Manufacturer refers to a process or system of manufacturing a component that is a part of a larger project. Here at Fischer Plastic Products, we refer to OEM work as manufacturing plastic products for a client base that then utilises this part in a secondary production line to become a key component of their larger product.
Fischer Plastics has state of the art machinery and staff to ensure that you receive great customer service and assistance for custom manufacturing as well as transitioning your products to Australian manufacturing or other materials.
It is relatively easy to remove metal from an existing metal mold. Adding metal, on the other hand, can be difficult or, for all practical purposes, impossible with rapid injection molding. To look at this from the part perspective, you can add plastic, but you can’t take it away. Designing with this in mind is called “metal safe.”
For over 50 years, Fischer Plastic Products has been manufacturing a variety of storage products that are focused on quality and made to last in a variety of applications.
Undercut features complicate and, in some cases, prevent part ejection. Get rid of them if you can, but maybe that’s not possible, if, for example, you need a side action, sliding shutoff or pick out. One alternative may be using sliding shutoffs and pass-through cores, or by changing the parting line and draft angles to provide an easier mold build. These reduce tooling costs as you avoid additional pieces to the mold that add to manufacturing costs. In addition to the rise in manufacturing costs of using hand-loaded inserts, this also may have an impact on your piece part price because of longer cycle times and manual mold operation.
Still another way to reduce molding costs, depending on your part volumes, is to consider on-demand manufacturing. At Protolabs, two injection molding service options are available (see table below). One is best suited for those who need smaller part quantities, usually associated with prototyping. The other option, Protolabs calls it on-demand manufacturing, is a good fit for those who require slightly larger part quantities, typically up to 10,000-plus parts from aluminum molds. On-demand production can be a great option to manage demand volatility of your parts, reduce total cost of ownership, and leverage cost-efficient bridge tooling.
If you need an electronics housing or similar box-shaped part, you can either sink the wall cavities deep into the mold base, requiring long thin tools to machine ribs into the mold, or machine the aluminum material down around the core and mold the part around it. The latter approach is known as a core cavity, and is a far more cost-effective method of molding tall walls and ribbed surfaces. Better yet, this makes it easier to provide smooth surface finishes, adequate venting, improved ejection, and can eliminate the need for super-steep draft angles.
Textured surfaces, molded part numbers, and company logos look cool, but be prepared to pay a bit extra for these and other non-mission critical features. That said, permanent part numbers are a requirement for many aerospace and military applications. Use a mill-friendly font such as Century Gothic Bold, Arial, or Verdana (san-serif fonts), keep it above 20 pt., and don’t go much deeper than 0.010 to 0.015 inch. Also, be prepared to increase draft if part ejection is a concern.
Proto Labs, Inc. 5540 Pioneer Creek Dr. Maple Plain, MN 55359 United States P: 877-479-3680 F: 763-479-2679 E: [email protected]
When you choose to manufacture with Fischer Plastics and their expert team, you can rest assured that you will be producing the products you want at the highest quality.
We know the ins and outs of plastic manufacturing and injection moulding and work with the best local partners where need be.
In addition to per-unit costs, consider the material. Many plastics overlap in strength and functionality, but some are inherently easier to mold, driving down part costs. You can experiment with different materials in the interactive quote you receive when you upload your design to Protolabs.
Whether you want to transition a product to a sustainable recycled material or incorporate anti-static properties, we can assist you in this process.
While injection molding may seem costly compared to processes like CNC machining and 3D printing, the ability to scale and manufacture thousands of parts makes it a cost-effective solution for mass production. Determining the cost of injection molding is a combination of several factors. The main determinant of molding cost is the amount of time it takes to produce the tooling. This means, the more complex the part's geometry, the higher your manufacturing costs will be. Simple parts, without undercuts or more advanced surface finishes, will be the most affordable.
Every quote for an injection-molded part at Protolabs is accompanied by a free design for manufacturability (DFM) analysis. This identifies potential problem areas, or opportunities for design improvement. Insufficient draft angles, “un-machinable” features, impossible geometries—these are just a few examples in which part designs can and should be improved before clicking the “accept” button. Be sure to review these suggestions thoroughly, and contact an applications engineer at Protolabs with any design-related questions.
Got a family of parts that all fit together? How about multiple molding projects at one time? There’s no reason to build a mold for each individual part, provided A) everything is made of the same plastic, B) each part is roughly the same size (e.g., have similar processing times), and C) can all be squeezed into the same cavity, while still allowing for proper mold functioning.
Everyone wants to save money on manufactured parts. It sounds simple, but one of the easiest ways to reduce price-per-piece cost in injection molding is by increasing part quantity. That is because the initial upfront cost to design and machine the mold amortizes over more parts. At Protolabs, for example, up to 25,000 parts or more can be molded from the same tool.
In addition, maybe you can join some of those parts with a living hinge? This method is a great way, for example, to mold two halves of a clamshell-style container. These parts would otherwise need a pin-type assembly to open and close. The only caveat here is that a flexible and tough material must be used, such as polypropylene (PP).
For over 50 years, Fischer Plastic Products has been manufacturing a variety of plastic storage solution products that are made to last. We ensure that all products are made from the highest quality grade virgin material in Australia to service your needs as a customer.For our complete range of ready-made plastic storage products and more, fill out your details to get our catalogue.
Our in-house capabilities and areas of expertise in injection moulding and the broader plastics industry are extremely in-depth.
When it comes to the manufacturing of plastic products for your various business needs it is important to look at the overall process and how you can build something that will last. There are a number of ways something can be created and often cost is the determining factor. From 3D Printed parts through to the premium injection moulding, you need to take into account the needs and timeframe around what you are creating.
Always consider part extents. In molding-speak, that means how big is the part, and will it fit comfortably in the mold while allowing for sprues, runners, ejector pins, and all the other considerations needed to make a mold work. Protolabs’ maximum part size for injection molding is currently 18.9 in. (480mm) by 29.6 in. (751mm) with a maximum depth from the parting line of 4 in. (101mm) deep. However, larger parts like these, in turn, require a larger mold. This may have an impact on your mold and part costs.
Fischer Plastic Products is a proudly 100% family owned Australian company. All of our plastic storage solution products are produced onsite at our Mulgrave, Victoria Head Office manufacturing facility. Fischer Plastic Products design, tool and manufactured our full range of plastic storage solution products exclusively in-house, i.e. from design concept to reality.
As industry continues to become saturated with competition and many companies offering the same solutions for their market, we are seeing a rise in professional methods to differ you from the pack. Fischer Plastics and other local Australian manufacturers offer a personalised approach to helping you tailor-make products to not only continue to enhance your industry but make them in a way that is recognisable to the individual company.
1. Eliminate undercuts 2. Get rid of unnecessary features 3. Use a core cavity approach 4. Reduce cosmetic finishes and appearances 5. Design self-mating parts 6. Modify and reuse molds 7. Pay attention to DFM analysis 8. Use a multi-cavity or family mold9. Choose on-demand production option10. Consider part size11. Use overmolding
We consult with you at every step of the process to ensure that everything is tracking in the right direction for your specific needs.
Maybe you’re designing a snap-together case for some medical components, or two interlocking halves of a portable radio. Why build two mating parts when you can make one? Redesign the snaps so that the halves can be fit together from either direction, thus building a so-called “universal” part. Only one mold is needed, saving production expenses up front. And you can now mold twice as many of one part, instead of half the quantities of two.
Whether you already have CAD drawings or at the first step of design, Fischer Plastics can convert your idea to a formalised design.
In the firsts stage of custom manufacturing we look at your overall needs and discuss whether Injection Moulding is right for you.
Our digital factories create prototypes and low-volume parts fast, while our manufacturing network, offers advanced capabilities and volume pricing.
For over 50 years, Fischer Plastic Products has been manufacturing a variety of plastic storage solutions for a variety of industries across both Australia and New Zealand.
For any areas that are outside our usual areas of business or simply outside of our capacity, we work with the best manufacturers and tool makers to collaborate on projects.
Some injection-molded parts go through multiple iterations until a final, workable design emerges. Instead of purchasing a new mold for every revision, a little clever planning will allow the same mold to be used multiple times. Starting with the smallest, most basic part design, mold as many pieces as needed, then re-machine the mold to include additional part features, or a larger, taller version of the same part, and mold again. This is not an exact science, but given the right part, this re-use approach can save dollars on tooling development.
However, maybe your molding project calls for only a handful of parts. No worries. Protolabs builds cost-effective molds for production quantities as low as 25 pieces, often within a few days of ordering.
Toolmaking is an intricate process and can take a number of weeks. Fischer's leading tool room can also modify and service tools to the highest standard.
Maybe you are after a higher volume of parts? You can still achieve high volumes using aluminum tooling with two-, four-, or eight-cavity molds depending on size and part geometry that can reduce your piece part price, although this would impact your tooling costs.
Get machined parts anodized and chromate plated with our quick-turn finishing option. Eligible materials include aluminum 6061/6082 and 7075.
Once you have built a tool with Fischer we can also provide a premium moulding facility at our Mulgrave, Melbourne headquarters. We offer efficient supply times and utilise the best quality materials and masterbatch for all our processing.
Finally, consider an overmolding option. Depending on the part, it might cost you more upfront, but could potentially save you money later. For example, overmolding a gasket on a part upfront might be an added cost, but it can save costs later from having someone install a gasket manually.
GETTING A QUOTE WITH LK-MOULD IS FREE AND SIMPLE.
FIND MORE OF OUR SERVICES:
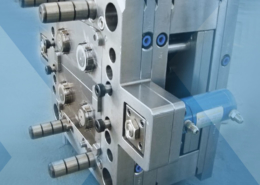
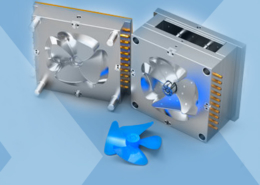
Plastic Molding

Rapid Prototyping
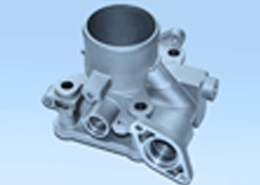
Pressure Die Casting
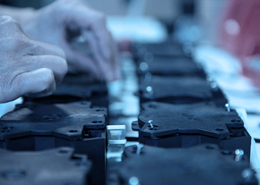
Parts Assembly
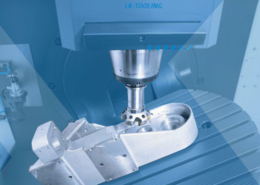