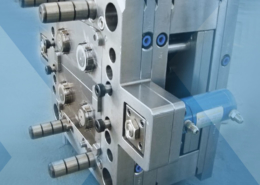
DIY Injection Molding: How to Do Injection Molding In-House - wire plastic moldi
Author:gly Date: 2024-10-15
ISO stands for International Standard Organization which comprises various organizations from different countries. These countries work together to develop and publish standards that are internationally valid and thus, need to be adhered to across borders.
I have other molds that are MUCH thicker bodied baits and therefore should have more of a problem with denting and I almost can't make them screw up but those stick molds are just a pain in my anus haha! I do use the HDA instead of salt, don't know if that would make a difference or not??
Has anyone used the 5 inch Basstackle injection stick bait mold ? If you have , what were the results ( good and bad .)
I bought them in the last year but they were used (from two different sellers) so I have no idea how old they are. The fact that the molds are not the same size leads me to believe they were made at significantly different times.
I have 2 of the 4" stick molds from Bass Tackle. They are the most problematic molds I have. Obviously it's just me if everyone else doesn't have problems. I just can't seem to get 4 nice baits ever. Always one or more that dent or not shaped right. But as I said, it must just be me.
1. Positive Air Flow: Both Class 7 and Class 8 cleanrooms utilize positive air flow systems to ensure air purity and maintain strict control over particulate levels.2. Masking Requirements: In a Class 7 Cleanroom, engineers and operators are required to be fully covered, including wearing shoe covers, full-body gowns, and hair covers when entering the cleanroom. Masking requirements may be slightly less stringent in a Class 8 Cleanroom.3. Electric Machines: To minimize the generation of airborne particles, electric machines are preferred over hydraulic machines in cleanroom environments.4. Packaging Restrictions: Cleanrooms impose limitations on packaging materials that may introduce additional particulates. Certain types of corrugated materials, known for generating particles, are generally not allowed. Instead, coated cardboard or plastic packaging materials are commonly used in cleanrooms.
Class III Devices: Class III devices, such as pacemakers and breast implants, carry the highest risk and complexity. These devices typically require the most stringent regulatory controls and are assembled and molded in cleanrooms, aiming to minimize contamination from airborne particles.
Contamination Control: The controlled environment of a clean room minimizes the risk of contamination, ensuring the production of components that meet the highest cleanliness requirements. This is crucial in industries such as medical and healthcare, where sterility is essential.
I can shoot BJ's longer as it takes them longer to get too hot while on the older ones I have to cease after 60-70 sticks, too hot and incomplete baits.
Case Study 2: Pharmaceutical Packaging: A pharmaceutical company needed sterile plastic containers for packaging sensitive medications. Clean room injection molding was employed to ensure the cleanliness and sterility of the containers. The controlled environment minimized the presence of contaminants, ensuring the integrity and safety of the pharmaceutical products. The precise molding process allowed for consistent dimensions and closure mechanisms, enhancing the overall functionality and usability of the packaging.
I have them, 6 to be exact. compared to BJ's new Stickem molds, no comparison I am afraid. Then venting on BJ's is amazing.
Class II Devices: Class II devices present a higher risk as they come into sustained contact with patients. Examples include catheters, blood pressure cuffs, and syringes. Cleanroom injection molding in an ISO 8 environment is often suitable for these devices, ensuring sterility and regulatory compliance.
I have to ease up on the injection on his as the molds are vented so well. I need to cull the older ones and obtain more of BJ's Stickem. Shooting bot brand of molds at a time throws my rhythm off in the area of pressure.
Since 2001, the cleanroom classification of classes ISO 1 – ISO 9 of ISO 14644-1 has been in effect. ISO 14644-1 defines the degree of purity of the air by determining limit values. ISO classification is upon the basis of particle concentration per m³. The highest purity in ISO 14644-1 is in ISO class 1, whereas the lowest is classified as ISO class 9. ISO Class 9 is also categorized as Room air. The table below depicts the ISO 14644-1 Cleanroom
Case Study 1: Medical Device Manufacturing: A medical device manufacturer required the production of intricate plastic components for a surgical instrument. Clean room injection molding was implemented to achieve the necessary level of sterility and precision. The controlled environment eliminated the risk of contamination, ensuring the production of sterile components with tight tolerances and excellent repeatability. This resulted in high-quality medical devices that met the stringent regulatory requirements and delivered exceptional performance.
Cleanroom injection molding is particularly relevant in the manufacturing of medical devices, which are categorized based on the level of risk they pose to patients and users:Class I Devices: These devices have minimal contact with patients and a low impact on overall health. Examples include electric toothbrushes, tongue depressors, and bandages. Cleanroom injection molding may not be required for such devices due to their minimal risk level.
Clean room injection molding is a critical manufacturing process that ensures precision, quality, and cleanliness in the production of components for various industries. We will delve into the concept of clean room injection molding, highlight its benefits, and examine real-world case studies that demonstrate its effectiveness in achieving superior results. Discover how clean room injection molding has transformed manufacturing processes across different sectors.
Regulatory Compliance: Industries with stringent regulatory standards, such as medical, pharmaceutical, and aerospace, benefit from clean room injection molding. Compliance with regulations ensures that components meet the necessary certifications and approvals
Improved Quality Assurance: Clean room conditions significantly reduce the potential for defects caused by environmental contaminants. The controlled environment allows for consistent manufacturing processes, resulting in tighter tolerances, improved part-to-part consistency, and reduced rework or rejection rates.
By adhering to these requirements and maintaining a cleanroom environment, manufacturers can ensure the integrity and quality of plastic injection molding processes, particularly for applications that demand a high level of cleanliness and sterility.
BTs are good molds, they make a stick that will catch fish but it is like comparing a Lexus with a Toyota, a caddy to a chevy.
Case Study 3: Biotechnology Research: A biotechnology company required microfluidic chips for laboratory research purposes. Clean room injection molding was utilized to produce the intricate channels and structures of the chips. The controlled environment prevented the introduction of contaminants, ensuring the reliability and accuracy of the research results. The precise molding process enabled the production of consistent and high-quality microfluidic chips, facilitating advanced experimentation and analysis.
You can post now and register later. If you have an account, sign in now to post with your account. Note: Your post will require moderator approval before it will be visible.
I have 2 of the 4" stick molds from Bass Tackle. They are the most problematic molds I have. Obviously it's just me if everyone else doesn't have problems. I just can't seem to get 4 nice baits ever. Always one or more that dent or not shaped right. But as I said, it must just be me.
maybe try lower temps? hold pressure an make sure u top off molds. Sounds like you have an older mold from when bob was there and a newer model that kevin made. I don't personally have experiebce with newer model but i have 9 older ones anywhere from 3" to 5" and they all shoot good. Some one that used to work there told me that bt stick molds have to small of a gate . But i never had a problem.maybe open it up some?
I have herd that guys have had the same issue you are talking about! Most have said the gates are to small. Some have said that the nice shape at the top of the bait is great , but the small gate causes the dents .
GETTING A QUOTE WITH LK-MOULD IS FREE AND SIMPLE.
FIND MORE OF OUR SERVICES:
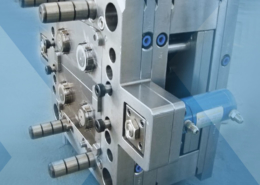
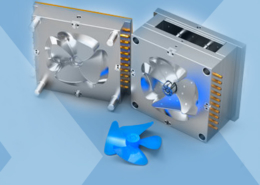
Plastic Molding

Rapid Prototyping
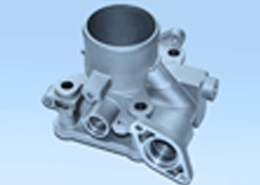
Pressure Die Casting
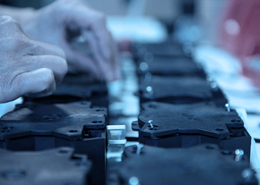
Parts Assembly
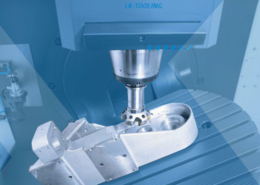