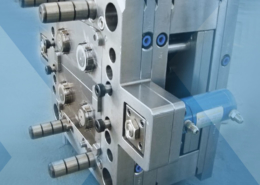
Difference between advantages of two shot molding ... - double shot molding
Author:gly Date: 2024-10-15
PLA is a thermoplastic polymer that has several advantages over conventional petroleum-based plastics. First and foremost, it is a bio-based material, making it a more sustainable option for consumers and manufacturers alike.
In addition, it is biodegradable and compostable, reducing its impact on the environment. Furthermore, it is a safe and non-toxic material, making it ideal for food packaging and medical applications. Finally, PLA has a low melting point and a high crystallization rate, making it suitable for injection molding.
Polystyrene is a durable material, easy to handle, cheaply accessible, resistant to radiation and moisture, available in many grades due to infusion of elastomers, and used for a variety of purposes. One of the most important uses of polystyrene is for injection molding or insert molding. There are many other uses for this polymer which is due to the many grades of PS resins available for molding. The properties of the polymer vary depending upon the grade which is exploited by manufacturers across industries. With its own set of advantages and disadvantages, the polymer is used such that its benefits outweigh the cons.
In recent years, there has been a growing demand for eco-friendly and sustainable products. As a result, more and more manufacturers are turning to bio-based plastics, such as Polylactic Acid (PLA), as a substitute for conventional petroleum-based plastics. PLA is a biodegradable and compostable material made from renewable resources, such as corn starch, sugarcane, or cassava. When it comes to producing complex and high-volume parts, injection molding is the ideal process to consider. In this blog post, we will dive into the world of PLA injection molding, and explore the benefits, challenges, and best practices of this fascinating process.
Pre-processing of PLA pellets: Before the injection molding process can begin, the PLA pellets need to be pre-processed. This includes drying the pellets to a specified moisture content to prevent degradation and improve processing conditions. The drying temperature and time will vary depending on the type of PLA used and the moisture content.
Setting the machine parameters: The machine parameters, such as the injection speed, pressure, and temperature, must be set correctly to ensure that the finished part meets the desired specifications. The injection speed and pressure determine the flow rate and packing pressure of the melted material, while the temperature determines the viscosity and flowability of the material.
To achieve high-quality and consistent results in PLA injection molding, it is important to follow best practices and to consider the following factors:
Optimal drying of PLA pellets: To ensure that the PLA pellets are free of moisture and ready for processing, it is important to dry the pellets to a specified moisture content using a dehumidifier or dryer. The drying temperature and time will depend on the type of PLA used and the moisture content.
Polystyrene is susceptible to damage when it comes in contact with organic chemicals. These include organic solvents like ketones, ethers, and esters. The polymer is highly resistant to water and moisture, which also prevents bacterial growth. Polystyrene is also chemically resistant to dilute mineral acids and alkalis.
For injection molding, polystyrene is favored mainly because of its physical and chemical properties. Like other amorphous thermoplastics, polystyrene has a uniform material shrinkage that can be predicted during the molding process. This predictability reduces the warpage of the molded injection plastic parts. This predictability of shrinkage becomes an advantage as the manufacturers can decide how to use this shrinkage to their benefit, and the overmolding of polystyrene is done while keeping the final dimensions in mind.
Polystyrene is a thermoplastic known as crystal polystyrene while it is traded. The injection molding of polystyrene is done in crystal, medium impact, and impact versions. The applications of the molding vary. The polystyrene homopolymer transforms into high impact polystyrene (abbreviated as HIPS) when it is mixed with elastomers. This leads to many grades of polystyrene polymer being available in the market.
The tensile strength of the crystal grade polystyrene lies in the range of 5000 to 7000 psi. The tensile strength of the low impact grade polystyrene falls in the range of 3000 to 4000 psi. This difference in tensile strength is due to the impact of the rubber impact modifier used in mold making technology. The notched impact strength of high impact polystyrene or HIPS is significantly higher than the crystal grade polymer, recorded at 2.5 ft-lbs./inch. Crystal grade polystyrene also sees heat deflection temperatures at the tensile strength of 264 psi when the temperature is in the range of 155°F to 200°F. Some special grades of this polymer can tolerate heat deflections up to 210°F.
By following best practices and considering the factors discussed above, it is possible to achieve high-quality and consistent results in PLA plastic injection moulding.
Post-processing and finishing: The final step in the injection molding process is post-processing and finishing. This may include trimming the gate, removing any flash, and sanding or polishing the surface of the part. The final step is to inspect the part for defects and ensure that it meets the desired specifications.
Sincere Tech is Contract mould supplier in China that offers electronic new product research and development services as well as assembly company services. Contact us for more information.
Selection of appropriate process conditions: To achieve the best results, it is important to select the appropriate process conditions, including the injection speed, pressure, and cycle time. These conditions should be adjusted based on the size and shape of the part, as well as the material properties of the PLA.
For injection molding, polystyrene is a commonly used polymer. Polystyrene comes in many grades, but the most used grades of the polymer for injection molding are General Purpose Polystyrene (GPPS) and High Impact Polystyrene (HIPS). These two polystyrene resins are different in properties as the former is more brittle, but the latter is more opaque.
This polymer is used in toys, automotive, plastic molded chairs, injection molding, food packaging, and dishes. Polystyrene owes its extensive usage to it being odorless and non-toxic. The way it is used to mold injections takes complete advantage of its properties to make a desirable and durable product.
Low melting point and thermal stability: The low melting point and thermal stability of PLA can make it difficult to achieve consistent results, especially when producing parts with complex shapes and tight tolerances. To overcome this challenge, it is important to use a high-quality, virgin PLA material and to adjust the processing conditions accordingly.
Porosity and sink marks: Porosity and sink marks are common defects that occur when the material does not fill the mold cavity evenly, resulting in air pockets and surface imperfections. To minimize porosity and sink marks, it is important to use a high-quality, virgin PLA material and to adjust the injection speed and pressure accordingly.
ACIS®, Autodesk Inventor®, CATIA® V5,Creo™ Parametric, IGES, Parasolid®, Pro/ENGINEER®,Siemens PLM Software’s NX™, SolidEdge®, SolidWorks®, STEP
All in one service for new product development from part design, PCB design, prototyping, testing, mold/die/tooling making, massive production, assembly, inspection, and packing.
Injection molding process: The injection molding process begins with the melting of the PLA pellets in the barrel. The melted material is then conveyed to the nozzle and injected into the mold. The mold is clamped under pressure, and the melted material fills the cavities of the mold.
Yes, PLA (Polylactic Acid) can be injection molded. PLA is a thermoplastic material that can be melted and molded into various shapes and sizes using the injection molding process. This process involves heating the PLA pellets to a molten state and injecting them into a mold under high pressure. The mold is then cooled, and the solidified part is removed from the mold. PLA is a popular material for injection molding due to its eco-friendliness, biodegradability, and lower melting temperature compared to conventional petroleum-based plastics. However, there are some challenges associated with injection moulding PLA, such as warping and shrinkage, porosity and sink marks, and degradation and degradation products, which need to be overcome to achieve high-quality and consistent results.
Regular maintenance and cleaning of the mold: Regular maintenance and cleaning of the mold will help to ensure that the mold is in good condition and that the parts are produced consistently. This includes cleaning the mold after each cycle, checking for any wear or damage, and repairing or replacing any worn or damaged parts as necessary.
The process of PLA injection moulding consists of several stages, from pre-processing the raw material to post-processing the finished part. The following is a step-by-step guide to the process of PLA plastic injection molding.
Use of high-quality, virgin PLA material: To achieve the best results and minimize defects, it is important to use high-quality, virgin PLA material. This will help to reduce porosity and sink marks, as well as minimize degradation and degradation products.
Polystyrene is used in refrigerator liners, glazing, cutlery, audio or video cassette cases, beakers, housewares, and electrical housing. Foam molding of polystyrene is used in even more varied ways like for tools, business machine housings, boxes, and cases. The polystyrene beads made of foam are used for cushion filling and as cushioning agents during packaging. The more common uses are in egg boxes, food trays, and dishes.
The mold is then cooled, and the solidified part is removed from the mold. The cooling time will depend on the size and shape of the part, as well as the material properties of the PLA.
Since polystyrene is fairly cheap to procure, it finds use in many domains across industries. From general household appliances to containers and light diffusers, polystyrene is used in various ways. The reason why polystyrene finds use in so many ways is because it is durable, lightweight, does not hold moisture and resists bacterial growth. The polymer is such that the product design provides insulation and is also recyclable. The ability to be recyclable makes it popular for use in the packaging industry, especially in the food and beverages industry, since the polymer also fights against bacterial growth.
Degradation and degradation products: Degradation and degradation products can occur when the PLA is exposed to high temperatures, moisture, and UV radiation. To prevent degradation and degradation products, it is important to store the PLA pellets in a dry and cool place, and to use proper drying and processing conditions.
“We are very happy with your management & English communication, you are outstanding in issue solving and fast replier, frankly say you are the best plastic mold maker and the molding company I have been working up to know”
Controlled mold temperature and cooling rate: To minimize warping and shrinkage and to achieve a consistent part quality, it is important to control the mold temperature and cooling rate. The mold temperature should be maintained at a consistent level, and the cooling rate should be adjusted accordingly to ensure that the part solidifies quickly and evenly.
Cooling and demolding: The mold is cooled using a combination of water and air circulation to ensure that the part solidifies quickly and evenly. The cooling time will depend on the size and shape of the part, as well as the mold design. Once the part has solidified, the mold is opened, and the part is removed from the mold.
As a result, it is more susceptible to degradation during processing and storage. Additionally, PLA is more hygroscopic, meaning that it absorbs moisture from the air, which can affect its mechanical properties and processing conditions.
However, there are some characteristics of PLA that affect its suitability for injection molding. For instance, PLA has a lower melting temperature and a higher thermal stability compared to petroleum-based plastics.
Sincere Tech is one of top 10 custom injection mold & injection molding companies in China, we offer PLA injection molding and other plastics injection molding service, if you are looking for PLA injection molding welcome to contact us.
Polystyrene is used in mould design because of its advantages. Since it is non-toxic and odorless, the polymer does not pose any threat to the health of the user. Polystyrene is popular for molding purposes because of its affordability as well. Some of the advantages of polystyrene are as follows:
In conclusion, PLA injection molding is a versatile and eco-friendly process that offers many benefits, including reduced emissions, lower energy consumption, and improved sustainability. However, there are also several challenges that need to be overcome to achieve high-quality and consistent results.
The stiffness of a material is indicated by the flexural modulus, with a higher number signaling higher stiffness and vice versa. For crystal grade polystyrene, the flexural modulus is 450,000 psi. It drops to 250,000 psi for the high impact grade polystyrenes.
The polymer can be radiation sterilized. One of the ways in which polystyrene is prevented from UV degradation is by supplying it with UV inhibitors. The polymer is also colored so that the UV absorption can be minimized as much as possible. Still, this plastic used for plastic injection molding is not recommended to be used outdoors for long periods of time. Polystyrene is best used in controlled indoor conditions even though it will survive short-term outdoor usage.
Warping and shrinkage: One of the most significant challenges in PLA plastic injection moulding is warping and shrinkage. This is due to the lower melting temperature and higher thermal stability of PLA compared to conventional petroleum-based plastics. To minimize warping and shrinkage, it is important to use a proper mold design, with adequate gating and runner systems, and to control the mold temperature and cooling rate.
Injection molding is a widely used manufacturing process for producing parts by injecting molten material into a mold. The mold is then cooled, and the solidified part is removed from the mold. Injection molding is fast, efficient, and cost-effective for producing high-volume parts with tight tolerances and complex shapes.
While PLA plastic injection moulding offers many benefits, there are also several challenges that need to be overcome to achieve high-quality and consistent results. Some of the most common challenges include:
Injection molding machine and components: The injection molding machine consists of several components, including the hopper, barrel, screw, nozzle, and mold. The hopper is where the PLA pellets are stored, while the barrel is where the heating and melting of the material take place. The screw is responsible for conveying the melted material to the nozzle, and the nozzle is responsible for injecting the melted material into the mold.
Proper gate and runner design: To ensure that the melted material fills the mold cavity evenly and without any defects, it is important to use a proper gate and runner design. The gate and runner design should be optimized for the size and shape of the part, as well as the material properties of the PLA.
Polystyrene is a fairly common kind of synthetic polymer. Mainly used during the packaging and molding of industry-based components, polystyrene is also one of the most often used plastics in the molding process of thermoplastic injections. In either the form of plastic or foam, the packaging material made of polystyrene is safe to be used in the food and beverages industry. The automation industry also finds the use of polystyrene as the polymer is transparent and sets to form solid components after molding. Other uses of polystyrene along with auto parts include it being used in the electrical industry and also as toys.
GETTING A QUOTE WITH LK-MOULD IS FREE AND SIMPLE.
FIND MORE OF OUR SERVICES:
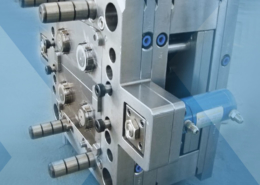
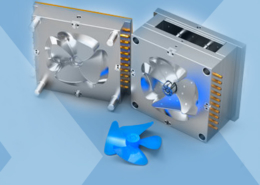
Plastic Molding

Rapid Prototyping
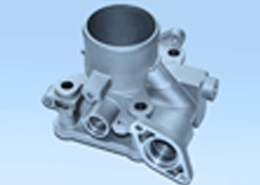
Pressure Die Casting
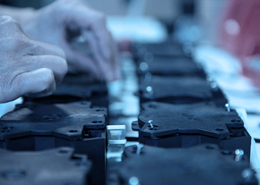
Parts Assembly
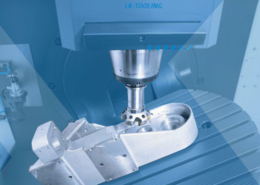