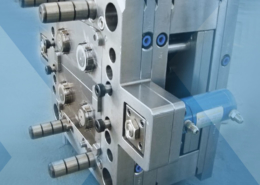
Unraveling the Potential of PEEK Molding
Author:gly Date: 2024-06-08
In the realm of advanced materials and manufacturing, PEEK (Polyether Ether Ketone) stands out as a versatile thermoplastic known for its exceptional properties and applications across various industries. PEEK molding, the process of shaping PEEK material into desired forms using injection molding techniques, embodies innovation and precision. This article delves into the intricacies of PEEK molding, exploring its significance, applications, and future prospects.
Introduction
PEEK, a high-performance engineering polymer, has gained widespread acclaim for its remarkable combination of mechanical strength, chemical resistance, and thermal stability. Its unique properties make it an ideal candidate for demanding applications in aerospace, automotive, medical, and other industries. PEEK molding harnesses the inherent advantages of this material, enabling the production of complex components with unparalleled precision and efficiency.
Material Properties
Mechanical Strength
PEEK exhibits exceptional mechanical properties, including high tensile strength, modulus of elasticity, and impact resistance. Its robustness and durability make it suitable for applications subjected to heavy loads, dynamic forces, and harsh environments. From structural components in aerospace engineering to orthopedic implants in medical devices, PEEK's mechanical strength ensures reliability and longevity.
Chemical Resistance
One of PEEK's most notable attributes is its resistance to a wide range of chemicals, solvents, and oils. This property makes it suitable for applications where exposure to corrosive substances is a concern, such as chemical processing equipment, oil and gas exploration tools, and automotive components. PEEK's chemical resistance ensures long-term performance and reduces maintenance requirements, enhancing operational efficiency.
Thermal Stability
PEEK exhibits exceptional thermal stability, retaining its mechanical properties at high temperatures up to 250°C (482°F) continuously and up to 300°C (572°F) for short durations. This thermal resistance makes it ideal for applications subjected to elevated temperatures, such as automotive under-the-hood components, electrical insulation, and aerospace components exposed to engine heat. PEEK's thermal stability ensures dimensional stability and performance under extreme conditions.
Applications
Medical Devices
In the medical industry, PEEK has emerged as a material of choice for various implantable and non-implantable medical devices. Its biocompatibility, radiolucency, and sterilizability make it suitable for applications ranging from spinal implants and orthopedic implants to surgical instruments and dental components. PEEK molding facilitates the production of complex medical device components with precise geometries and tight tolerances, meeting the stringent requirements of the healthcare sector.
Electronics and Electrical Engineering
PEEK finds extensive use in electronics and electrical engineering due to its excellent dielectric properties, thermal stability, and flame retardancy. It serves as an insulating material for connectors, sockets, and circuit boards in electronic devices, ensuring electrical reliability and safety. PEEK molding enables the fabrication of intricate electrical components with high precision, contributing to the performance and longevity of electronic systems.
Oil and Gas Industry
In the oil and gas industry, PEEK plays a vital role in downhole drilling tools, seals, and connectors subjected to extreme pressure, temperature, and corrosive environments. Its chemical resistance, mechanical strength, and thermal stability make it well-suited for demanding oilfield applications, where equipment reliability is paramount. PEEK molding enables the production of robust components capable of withstanding the rigors of downhole operations, enhancing efficiency and safety in oil and gas exploration and production.
Future Outlook
Advancements in Material Science
Ongoing research and development in material science aim to further enhance the properties and performance of PEEK and its derivatives. From alloying and nanostructuring to additive manufacturing techniques, scientists and engineers are exploring novel approaches to optimize PEEK for specific applications. These advancements hold the potential to expand the scope of PEEK molding and unlock new opportunities across industries.
Integration of Digital Technologies
The integration of digital technologies such as computer-aided design (CAD), simulation, and machine learning augments the capabilities of PEEK molding processes. Virtual prototyping and predictive modeling enable engineers to optimize part designs, tooling configurations, and processing parameters, reducing time-to-market and minimizing production costs. The convergence of digitalization and PEEK molding promises to revolutionize manufacturing practices and accelerate innovation in the years to come.
Sustainability and Circular Economy
As sustainability gains prominence in global manufacturing, PEEK molding companies are exploring eco-friendly alternatives and recycling solutions to minimize environmental impact. From renewable feedstocks and biodegradable additives to closed-loop recycling systems, efforts are underway to promote sustainability throughout the product lifecycle. Embracing circular economy principles, PEEK molding contributes to resource conservation and waste reduction, paving the way for a more sustainable future.
Conclusion
In conclusion, PEEK molding represents a pinnacle of advanced manufacturing, harnessing the exceptional properties of PEEK to create high-performance components across diverse industries. Its mechanical strength, chemical resistance, and thermal stability make it indispensable for critical applications in healthcare, aerospace, electronics, and beyond. As research and innovation continue to propel the field of PEEK molding forward, the potential for groundbreaking advancements and new discoveries remains boundless.
In summary, PEEK molding epitomizes the intersection of material science, engineering excellence, and innovation, offering solutions to complex challenges and driving progress across industries. By leveraging the inherent advantages of PEEK and embracing technological advancements, PEEK molding companies pave the way for transformative developments and sustainable growth. Looking ahead, continued investment in research, collaboration, and sustainability initiatives will shape the future of PEEK molding, unlocking new possibilities and shaping the course of industrial evolution.
GETTING A QUOTE WITH LK-MOULD IS FREE AND SIMPLE.
FIND MORE OF OUR SERVICES:
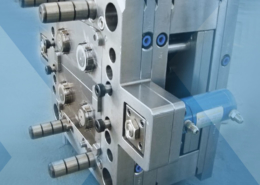
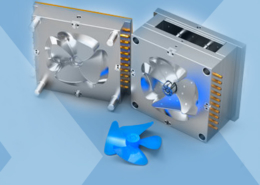
Plastic Molding

Rapid Prototyping
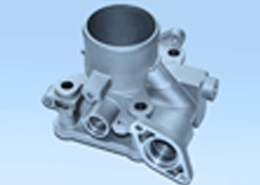
Pressure Die Casting
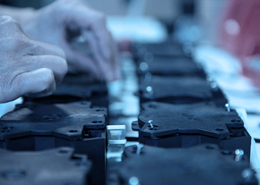
Parts Assembly
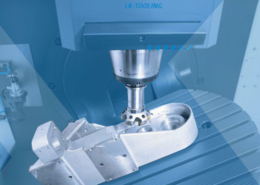