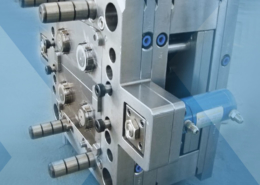
Debunking a Myth: Co-injection Molding is Too Complex ... - co injection molding
Author:gly Date: 2024-10-15
Including a dangling benzene ring in polystyrene’s unusual molecular structure adds to its fast transition temperature behavior. As a result, for optimum flow during thermoplastic styrene molding, polystyrene requires adequate energy absorption close to its melting point.
In this regard, a thermoset plastic would burn if heated to a high temperature a second time. Because of this property, thermoset materials are poor choices for recycling.
Packaging foams are one of the most common applications for polystyrene injection molding. These foams, such as refrigerators, laptop computers, and tablets, are often used to protect fragile objects and appliances during shipment and handling.
This feature is handy for products with sophisticated design features since little shrinkage assures the exact duplication of the desired pattern. Furthermore, reduced shrinkage streamlines the mold release process, allowing for more efficient manufacture of high-quality parts.
Now, the base material for the enclosures is polystyrene resin, which was selected because it can be molded with relative simplicity and is quite inexpensive.
Having said that, PS injection molding resins come in various grades, allowing for various applications beyond simple injection molding. Various sectors use polymers today because their qualities differ depending on their grade.
Polystyrene injection molding is at the vanguard of modern manufacturing, providing an unrivaled mix of adaptability, cost-effectiveness, and ease of use. Polystyrene is a great example of the art of molding because it can be made into many different shapes, such as wrapping foams.
One distinguishing feature is its unusually high melting temperature compared to other common plastics, beginning to soften at about 205°C and fully melting at around 270°C. As a result, polystyrene injection molding necessitates the utilization of greater temperatures, resulting in a higher energy input during the molding process.
Beyond packaging, PS has found application as a living hinge material and is known for its thermoforming capabilities. Here are some key properties of PS that you should consider before opting for polystyrene injection molding:
Electronics enclosures have been finished; they are subjected to a comprehensive inspection for quality assurance. After that, they go through a thorough packaging process before being made ready for transport to the company’s/business’s production line.
Polystyrene, a common thermoplastic used in thermoplastic injection molding with polystyrene, has unique qualities that make it appropriate and problematic for this manufacturing technique.
After being put into the hopper of the injection molding machine, the polystyrene pellets are subjected to heat and melted into a liquid state to make the molten plastic.
Polystyrene is a versatile material with numerous applications since it is strong, lightweight, inexpensive, readily available, resistant to radiation and moisture, and comes in various grades thanks to incorporating elastomers. Injection molding and insert molding both make extensive use of polystyrene.
The intrinsic brittleness of polystyrene presents a difficulty during the ejection phase of injection molding. The design of ejector pins must be carefully considered to avoid any breakage.
Furthermore, structural foam molding, a type of injection molding, uses polystyrene’s qualities to manufacture foams with outstanding rigidity and cushioning properties. Polystyrene foam effectively absorbs stresses by keeping enough stiffness in its porous structure, ensuring optimal protection for the enclosed goods.
In this process, molten polystyrene is forced under high pressure into the mold. It conforms to the contour of the cavity, completing the enclosure for the electronic components. After the mold has been filled, the process of chilling will start.
The melt flow index of the material, which ranges from 12.0 to 16.0 g/10min, is relatively low when compared to plastics such as polyethylene. Because of its unique characteristic, polystyrene changes fast from a hard solid to a molten state within a narrower temperature range.
After a speedy inspection to check for quality and conformity per the product’s production requirements, any surplus of material, also known as flash, is removed. Then the enclosures are then put through the assembly process.
At Prototool, we first design criteria for the electronics enclosure during polystyrene injection molding. This includes dimensions, features, and aesthetics considerations.
In this regard, a production company like Prototool can satisfy its production demands and reduce the time it takes to bring its smart home automation system to market because of the effectiveness of the injection molding process. As a result, they receive a consistent supply of enclosures.
Adopting appropriate screw designs that focus on compressing the melt towards the end of the barrel, maintaining optimal flow and molding efficiency, is required to properly handle this melt behavior.
The ability of thermoplastics to be heated to their melting point, chilled, then reheated without significant degradation is a major advantage. Instead of burning, thermoplastics liquefy, allowing them to be easily injection molded and recycled. Thermoset polymers, however, will not reliquify once they have been “set” in solid form.
But before you consider using PS injection molding to get your desired plastic products, it’s important to be familiar with the parameters, use cases, and different production considerations using PS. We hope this in-depth guide will help you get familiar with the PS injection molding manufacturing process.
One of its primary advantages is the low shrinkage rate of polystyrene in injection molding. Compared to other polymers, which can have shrinkage percentages as high as 3%, polystyrene has a shrinkage percentage of roughly 0.5%.
Mold Fabrication is the second step, which begins after the business has reviewed and approved the 3D model. During this step, the mold is being fabricated. The mold is made from high-grade steel and undergoes precision machining to ensure its durability and effectiveness over time.
Polystyrene is usually (but not always) a homopolymer, which means it is made up entirely of the monomer styrene in conjunction with itself. Depending on the type, PS can be categorized as a “thermoplastic” or a “thermoset” material.
Nave ISK-8, Parque Industrial y Logístico Sky Plus, Avenida Mineral de Cinco Señores No.100, del Parque Industrial Santa Fe, Silao de la Victoria, Guanajuato, México
After sufficient time for the polystyrene to solidify and cool, the mold will open, and the freshly created enclosures will be discharged.
The mold’s design includes cavities and cores, which create the enclosure’s final form and characteristics. Because a company/business needs a large number of enclosures, professional manufacturers also employ a mold with several cavities so that they may enhance the efficiency of their production.
Polystyrene (PS) is a widely used manufacturing plastic material known for its distinctive application as foam, particularly in packaging. It is a popular choice in various classic plastic applications and has been utilized extensively in prototyping due to its cost-effectiveness and ease of handling.
The thermoplastic styrene molding machine guarantees that the mold cools evenly throughout, eliminating the possibility of the finished product having any faults or deformations.
The term refers to how the plastic reacts to heat. Thermoplastic materials are fully liquid at their melting points (210-249 degrees Celsius for Polystyrene) but begin to flow at their glass transition points (100 degrees Celsius for PS).
Ensuring an equal force distribution on thinner structures minimizes flexural stress, allowing the finished product to be ejected from the mold smoothly and successfully.
A group of talented engineers and designers working for the thermoplastic styrene molding service provider utilize computer-aided design (CAD) software to generate a three-dimensional enclosure model.
On the other hand, thermoset plastics can undergo heating just once, typically during the injection molding procedure. This initial heating prompts thermoset substances to solidify (comparable to a two-part epoxy), inducing an irreversible chemical transformation.
GETTING A QUOTE WITH LK-MOULD IS FREE AND SIMPLE.
FIND MORE OF OUR SERVICES:
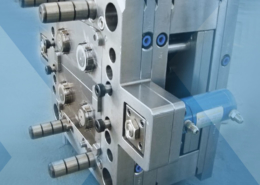
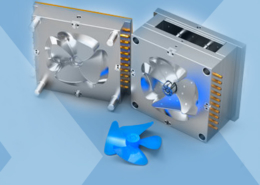
Plastic Molding

Rapid Prototyping
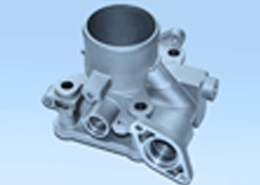
Pressure Die Casting
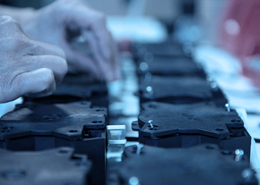
Parts Assembly
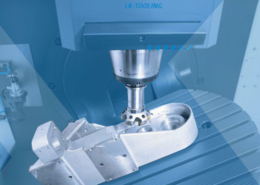