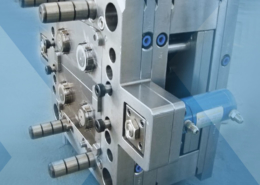
Dalal Plastics Pvt. Ltd.: India's Top injection moulding company - plastic molds
Author:gly Date: 2024-10-15
Post-curing Torlon PAI parts: Every Drake-produced Torlon PAI product goes through an engineered post-curing processes, a key factor in realizing the full performance potential of this advanced polymer. This final step before shipment achieves Torlon PAI’s typical core Tg (glass-transition temperature) midpoint value of 540°F (282°C). In our decades of experience with the material, we’ve optimized curing cycles to produce Torlon PAI parts to achieve maximum structural strength, toughness, and resistance to wear and chemicals.
Our production team’s ideas have a major impact on our reputation for superior quality. Among their initiatives: dedicated dryers for each resin to avoid cross-contamination. And they know purging can’t eliminate all residue after a run, so they do a full tear-down, polishing the screw and cleaning all components that contacted the melted polymer in the prior run before starting the next job.
Precision injection molding ultra high-performance plastics demands a solid understanding of each polymer’s unique behavior to avoid degradation and achieve optimum property and quality levels. Its melt characteristics and flow behavior must be factored into process conditions and hardware designs to preserve physical properties and achieve consistent quality in the high-pressure and high-temperature molding process.
3. Material – Polymer degradation can occur if the correct drying procedures for the specific polymer is not being followed. High moisture content of the plastic will cause the polymer to degrade faster than material that has been dried correctly. Also, if you are using regrind back into the system be sure that the quality of the regrind is sufficient for the process. Poor quality, contaminated, or multi generation regrind mixed with virgin material can promote degradation in the final melt.
Near-net shapes provide an efficient, economical bridge between machining low part quantities from stock shapes and molding high volumes that require a significant investment in tooling. These forms or blanks are molded in low-cost tools and approximate the part’s as-designed dimensions. They are then machined to exact part dimensions. Using near-net shapes when production requirements reach the right levels yields a major savings in material vs. machining from rod or plate.
With decades of experience in melt-processing ultra high-performance thermoplastics, injection molding specialists, Drake Plastics has fine-tuned process conditions, designed and built specialized components for our molding equipment and invested in the technology needed to produce consistently high-quality injection molded parts in Torlon PAI, PEEK and similar advanced polymers.
Polymer Degradation is an injection molding defect that can be defined as change in the properties—tensile strength, color, shape, etc.—of a polymer or polymer-based product under the influence of one or more environmental factors such as heat, light or chemicals. Colors usually darken when degradation occurs and may range from yellow through orange to black, depending on the severity of the degradation. In this blog we will look at some causes of polymer degradation that arises from three factors – Machine, Mold, and Material.
Drake invests in the best available molding and process equipment and control technology for materials like Torlon PAI, PEEK, Ultem PEI and other high-performance polymers. Our production team also takes extreme measures to achieve the highest levels of quality and performance in molded parts.
Insert molding integrates functional metal components into injection molded parts during the molding process. The inserts are fixed in the mold cavity, and the polymer melt flows around the metal component as the molding process takes place. Electrical conductors, threaded fasteners, structural reinforcements and protective caps made from titanium, stainless steel and other metals are only a few of the possibilities for insert molding, and the technique is incorporated into many high-performance parts made from the advanced polymers Drake routinely molds. Other advantages include reduced assembly time in the customer’s operation and more secure integration of the molded-in metal component in the part.
Our in-depth guide tells you everything you need to know about purging compounds. We want to give you the tools you need to make the best decision for your processing needs..
Drake’s extensive in-house molding and machining capabilities combine to offer customers molded parts with complex geometries and features not possible with injection molding alone. Precision finish-machining adds deep undercuts, side or angled holes or ports, zero or negative draft sidewalls and other design elements that are impossible or impractical to mold. Our CNC machining also yields tighter part tolerances than can be achieved in molding. For example, machined feature tolerances on a molded part can be held to +/-0.0005 inch (+/-0.02mm).
With over 2,000 current customers and a combined 200+ years of processing experience, we’ve seen it all. Asaclean® understands your priorities and has excellent cost savings solutions specific to your process and industry.
Use our Grade Selection Guide to receive personalized Asaclean® product recommendations based on your goals & processing information.
Drake’s process technology includes In-cavity pressure transducers and RJG Systems that monitor process parameters inside the mold cavities to maintain ideal conditions. This important control leads to high quality and exceptional repeatability in every Drake injection molded part equipped with RJG.
Our reputation as specialists stems from the millions of parts we’ve supplied in unfilled, glass, carbon fiber, bearing and wear grades of advanced polymer materials including:
2. Mold – If the shot weight of the mold is too small for the press that it is being ran in degradation can occur due to residence time in the barrel. If this is the case, the mold would need to be transferred to a machine with a smaller barrel capacity or volume.
1. Machine – The most common cause of material degradation is when the polymer in the barrel is overheated. This is the most basic cause for the defect and can be solved by reducing the melt temperature of the polymer. Temperature controllers can and will malfunction from time to time which can lead to a zone “running away” which simply means that the temperature is not being controlled correctly to the heater bands. Be sure that the correct type of thermocouple is being used for temperature control. Barrel residence time is extremely important in reducing the likelihood of polymer degradation. Obviously, the more time polymer spends in the barrel in residence the easier the polymer will degrade. Ideally you do not want your shot weight to be less than 25% of the shot capacity. Most processors shoot for 3-4 cycles for the polymer to go from feed throat to mold introduction.
Ready to reduce your production downtime to protect your profits? Learn more about how purging compounds and process efficiency work in tandem.
Purging Compounds are an easy-to-use and affordable way to dramatically reduce scrap & downtime in plastics manufacturing. But how do you know if purging compounds are right for you?
Our Purging Experts answer frequently asked questions and address topics that benefit Process Technicians, Maintenance teams, Buyers, and even Plant Managers.
Many customers describe our facility as the cleanest and most efficient they’ve experienced. Our all-electric injection presses yield precision parts from 0.03 to 20 oz. (0.85 to 570 grams). They use no hydraulics, adding to the cleanliness of our operation. Each machine is also equipped with a unique capability to compress or ‘coin’ parts during the molding cycle, enabling us to injection mold very heavy cross-sections without porosity or voids.
Drake Plastics’ Quality Management System is certified to the worldwide aerospace industry’s AS9100D(2016) as well as ISO 9001:2015 standards. These stringent requirements apply to all products we manufacture. Our ability to meet these standards stems in large measure from our team’s experience and their commitment to achieving the highest attainable levels of quality. We also support our team by investing in the best inspection technology available, including:
Drake Plastics’ support capabilities can be especially beneficial to customers transitioning from a machined plastic or metal component to injection molding:
Annealing PEEK and other ultra-high performance thermoplastic parts: Drake has extensive experience in annealing to relieve internal stresses that can impair a part’s properties or cause it to deform over time. Residual stresses occur as an advanced polymer rapidly transitions from its hot melt phase to ambient temperature. This is especially problematic for parts with heavy or varying cross-section thicknesses that cool at different rates. Annealing under controlled conditions resolves this: by heating parts above the advanced polymer’s Tg or softening point, then cooling very slowly to a point below its Tg, the polymer chains relax uniformly, relieving residual stresses. Drake offers annealing on a custom basis. It is often utilized for injection molded parts that require exceptional dimensional stability or a crystallinity level that maximizes the polymer’s strength, toughness and chemical resistance.
The best production and quality practices deliver maximum value to customers only when backed up by consistently exceptional service. Drake’s customer-centric culture is evident in our rapid response to requests for information, support and problem-solving. Drake’s on-time delivery performance is 98% or better. Our team sets 100% customer satisfaction as the norm and sustaining it determines our ongoing service-based investments.
Drake offers a diverse menu of services and capabilities to meet customer-specific requirements and industry compliance standards for injection molded parts. They include:
Asaclean® helps injection molders, extruders, and blow molders dramatically reduce scrap and downtime. Whether you’re struggling with hot runner color changeovers, costly screw pulls, or holding a bubble in blown-film extrusion, we have the solution to your problems.
Jeremy Cooley is an Asaclean Technical Service Representative & Purging Expert living in South Carolina. He's worked in injection molding & purging for over 15 years, and frequently presents at national plastics trade shows and conferences.
Certifications on all shipments: Drake Plastics provides a Certificate of Conformance with all products regardless of polymer composition at no charge. Special testing is also available at a reasonable cost.
Asaclean® Purging Compounds are engineered to tackle your hardest processing challenges and make an incredible difference in your process efficiency.
Learn how processors at over 2,000 manufacturing locations in North and South America use Asaclean® to cut scrap rates, reduce downtime, and transform their process efficiency.
GETTING A QUOTE WITH LK-MOULD IS FREE AND SIMPLE.
FIND MORE OF OUR SERVICES:
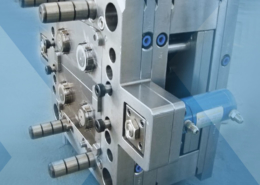
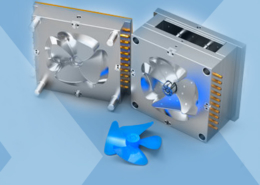
Plastic Molding

Rapid Prototyping
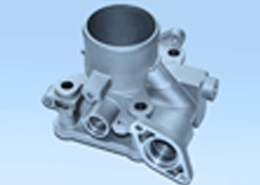
Pressure Die Casting
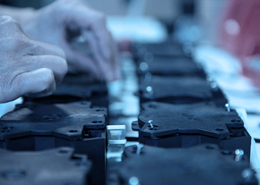
Parts Assembly
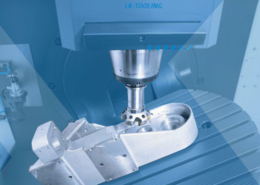