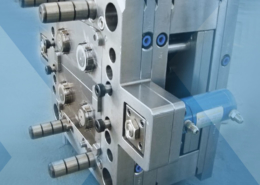
Custom Polycarbonate Parts - molded polycarbonate
Author:gly Date: 2024-10-15
PCS is presenting the state-of-the-art Polimold system which enables more control at the opening and closing of hot runner valve gate pins.
PCS Moldshields, clear plastic “curtains,” help contain molded parts once ejected from the mold, enabling fewer damaged or contaminated parts, and thus less waste.
Catch up on the latest business partnerships within the moldmaking community from Hurco Companies, Inc., iD Additives, Inc., PCS Company, RJG and HRSflow.
The new award gives all domestic and internationally active students, collegiate or apprentices in pursuit of Journey-level credentials as a moldmaker, mold designer or mold repair technician a chance to be recognized.
Steel supplier discusses high thermal conductivity metal powders that also address the skills gaps via user-friendly materials and promote sustainability via durability and higher cycle counts.
Steel supplier discusses high thermal conductivity metal powders that also address the skills gaps via user-friendly materials and promote sustainability via durability and higher cycle counts.
This month’s roundup features products, processes and services involved with additive manufacturing, maintenance and repair, mold components and more. To learn more about the products, read on.
Airtect plastic leak protection systems from PCS company provides round-the-clock, direct protection of injection molding machine nozzles and manifold systems.
The need for data to track information and the history of the mold-building process is ever-increasing, and mold component solutions can help.
Featured in this technology roundup are products, processes and services related to cutting tools, hot runners and more for the next-level mold builder.
Next Chapter Manufacturing, Muskegon Community College, PCS Company and Concept Molds chat about a coalition they formed to produce face shields to help fight COVID-19.
MoldMaking Technology's Christina Fuges and Tony Deligio with Plastics Technology were onsite together at the Dynamic Group in Ramsey, Minnesota, to see how its moldmaking and molding capabilities come together to grow the business as part of an AMBA Facility Tour.
In this most recent roundup, MMT continues to present the breadth of new or proven technologies that target the moldmaking industry, from cutting tools to software to hot runner products, that have been shared this month.
Love was in the air in more ways than one in February. Take a look at what articles our readers loved based on Google Analytics.
PCS Company offers beryllium free copper alloy Performance Core Pins® as the alternative for steel pins or copper alloy pins ...
Solid bronze guided ejector bushings from PCS Company offer superior performance for toughness, tensile strength and low coefficient of friction.
PCS Company’s MoldXChecker and CableXChecker offerings detect open and shorted circuits and troubleshoots faulty temperature control cables respectively.
This roundup focuses on maintenance, repair and surface treatment for mold equipment. Utilizing these helpful products and services can help save time and money.
Plastics industry veteran Mark Casey brings his management and engineering service repertoire to establish new business for PCS and enhance current customer operations.
Use of a new conformally cooled sprue bushing helped solve Midwest Mold Services’ problem with a big sprue that was hard to cool and preventing faster ejection times.
Join MoldMaking Technology Editorial Director Christina Fuges as she gets the latest news on this mold builder's use of VR for mold design education.
This technology roundup covers everything from laser repair and mold protection coatings to in-house maintenance services and education tools for learning best practices behind taking care of injection molds.
PCS Company offers Bolexp Metric Ball Guided Side Lock - Bar in 10 standard sizes. Bar lengths range from 25mm up to 112mm.
NPE2024: PCS Company introduces several new products, including the MCS system, hot runner alarm systems, sprue bushings, a micro-TIG welder and its full Smartflow product line.
Injection molding is a specialized and complex manufacturing process. If you have not fully understood and tested these intricacies, you could open yourselves up to failure down the road. Parts manufactured via injection mold tooling can help you understand how the product will perform in the production process, validating the manufacturability of the design and identifying any issues related to tooling, parting lines, gate locations, and other aspects crucial for mass production.
Reducing cycle time and costs while also freeing up your machines for other projects are advantages gained by using hot runners that no one can ignore. But where does one begin transitioning from cold to hot runners?
This webinar will provide an overview of new developments in hot runners, controllers, mold components, predesigned molds, process monitoring and mold maintenance equipment. These advancements are designed with the goals of lowering scrap rates, optimizing process temperatures and managing energy consumption. The solutions also aim to support productivity and may contribute to extending the operational lifespan of tooling equipment. Agenda: Innovative undercut and thread-forming components Predesign mold bases and plate control Melt delivery and control solutions Process monitoring and maintenance
MoldMaking Technology’s editorial team recaps some highlights from the show floor at NPE2018, including a technology slideshow, seven podcasts recorded live from the event and a video.
Latest addition to PCS’ line of ejector pins features high carbon content for higher wear resistance in high-speed steel pins.
Explore the standout articles of September, featuring innovations, expert insights, and strategies to boost efficiency and quality for your moldmaking needs.
It’s easy to imagine the advantages automation offers the moldmaking process, but it's challenging to change one’s mindset, develop a plan and invest.
Join this webinar where Hexagon will explore how state-of-the-art CAD/CAM technology can drive your business forward. Learn how to optimize tool paths, enhance design accuracy and reduce lead times with advanced simulation. Discover the power of automation and real-time data for continuous improvement. Tailored for mold and die manufacturers, this session offers actionable insights to boost productivity and quality. Don’t miss this opportunity to gain a competitive edge in progressive die manufacturing. Agenda: Key challenges in progressive die manufacturing Optimizing tool paths Enhancing mold and die design accuracy Reducing lead times with simulation Automating processes for greater efficiency Leveraging real-time data for continuous improvement
In ISO 9001 quality management systems, the Management Representative (MR) plays a crucial role. While the 2015 version of ISO 9001 no longer mandates this position, having a trusted management member serve as an MR remains vital for streamlining operations and maintaining quality standards.
Understanding and facing the moldmaking industry’s obstacles to growth requires a strategy focused on increased profitability.
Nano-formulated mold coatings can address the part fill and release challenges that come with highly complicated design requirements, expedited manufacturing expectations and high raw material prices for molds and resins.
After attending IMTS, it's clear that the integration of advanced technologies is ready to enhance precision, efficiency and automation in mold manufacturing processes. It’s a massive event, so here’s a glimpse of what the MMT team experienced firsthand.
Prototype injection molding is just one of the many prototyping and production services offered at HLH Rapid. We also provide CNC machining, 3D printing, and vacuum casting services. Not sure which method is best suited for your project? Get a free quote for each rapid prototyping technique by submitting your CAD and project details on our website contact form.
Smart sensors and sophisticated process and measurement data management are driving intelligent moldmaking to new heights.
In this most recent roundup, MMT has curated a variety of new or proven technologies that target the moldmaking industry that have been shared on the website this month.
MoldMaking Technology addresses the complete lifecycle of the manufacture and maintenance of a mold—from design to first shot—by providing solutions and strategies to moldmaking professionals charged with designing, building and repairing molds. About Us
Discover how to enhance your mold design process with CAD/CAM software specifically tailored for the moldmaking industry. In part two of this webinar series, Cimatron will demonstrate how to intelligently design mold components, such as slides and lifters, using powerful CAD/CAM tools to accelerate the design process. Additionally, it will cover how to avoid errors and ensure design accuracy for ejector pins by checking clearance distances, calculating cutoff heights correctly, and thoroughly documenting all ejector components. Agenda: Slides Lifters Inserts Ejection pins and charts
Latest technology used in PCS’ MSC Hot Runner Control Systems advances its analysis, diagnosis and reporting functions, ensuring fast control response and more intuitive operation.
Angela Elsey, President of PCS Company, shares her journey into moldmaking, perspective on the industry and plans for the business.
Simple-to-install device by PCS gives injection molders, blow molders and extruders the ability to prevent machine shutdowns due to empty hoppers.
Another tech roundup is here to provide an overview of technologies and services on the market for moldmakers. Featured in this roundup are cutting tools, mold components and more.
Identify pain points, tackle each one strategically and maintain flexibility to keep your moldmaking business on a path to growth.
Realize time and cost saving benefits from the use of integrated systems when compared to traditional hot runner manufacturing methods
Take a look at this week's slideshow to see products that make building and/or maintaining molds more efficient and cost-effective.
Join MoldMaking Technology Editorial Director Christina Fuges as she gets the latest news on this mold builder's use of VR for mold design education.
Continued investment in new technologies and automation has enabled this moldmaker to maintain shorter lead times no matter how large or complex the mold build.
A focus on electrode design and automation helps toolroom improve efficiency, reduce tooling costs and deliver higher quality products.
Moldmaking can be a complex business, but things can be simplified with the right hot runner and mold component technologies and services.
Kelly Beauchamp joins the product marketing team as a product manager, and Ken Berger is appointed to application engineer.
As the parts are essentially the same as production components, you can use them in early builds for market testing or even introduce them to the market place and start selling. Just because it is called ‘prototype injection molding’ doesn’t mean that it can only be used for prototyping purposes. It is also a viable and competitive option for low-volume production of 100 and over.
Gerardo (Jerry) Miranda III, former global tooling manager for Oakley sunglasses, reshares his complete mold design checklist, an essential part of the product time and cost-to-market process.
Discover how to enhance your mold design process with the right CAD/CAM tool for parting and cavity design. This webinar will explore CAD/CAM capabilities including how hybrid solid/surface modeling can streamline workflow and improve accuracy. Learn how to confidently tackle parting, runoff, and shutoff, ensuring precision and efficiency in your designs. Agenda: Part analysis QuickSplit techniques Parting and runoff strategies Shutoff solutions
Prototype injection molding, also known as rapid injection molding, is a process that incorporates rapid tooling (RT) method to produce injection-molded parts quicker than standard tooling times. This acceleration is achieved from using aluminium tools, eliminating certain complicated elements, or simplifying the tooling and manufacturing process. Due to the nature of the tool, it is also less expensive to make, which makes it suitable for rapid prototyping project budgets.
When used for conformal cooling in plastic injection, 3D printing opens a wide range of design freedom. This design freedom enables designers to develop highly-efficient thermal regulation networks. However, this blessing also comes at the expense of not only higher manufacturing cost but also higher design cost as the designer could spend weeks to develop optimal cooling channels. This webinar will explore strategies and tools — including SimForm, a front-end thermal simulation app — to help tool designers and tooling managers maximize the benefits of 3D printing while minimizing manufacturing and design costs. Agenda: 3D printing applied to the plastic injection industry 3D printing pros and cons Tools and methods to facilitate the integration of 3D printing
Adam Conley of Omega Tool Inc. was recognized as the Apprentice of the Year – Moldmaking by the Society of Plastics Engineers (SPE) Mold Technologies Div. (MTD).
PCS is now distributing the CoolingCare Systems from Fado Group, an end-to-end solution with intelligent tutorial, cleaning and maintenance functions.
The Mold Technologies Division of the Society of Plastics Engineers Inc. is pleased to announce the call for nominations for its four prestigious International Awards, recognizing outstanding contributions to the moldmaking industry. Deadline: February 15!
After attending IMTS, it's clear that the integration of advanced technologies is ready to enhance precision, efficiency and automation in mold manufacturing processes. It’s a massive event, so here’s a glimpse of what the MMT team experienced firsthand.
A connected software solution streamlines the moldmaking process by providing a unified source of design data, enhancing efficiency and reducing errors, with five key steps benefiting from this integration.
This roundup is full of products and services that help answer concerns and meet needs for the industry. Featured in this roundup are hot runners, mold components, mold materials and more.
MMT shares the five top-viewed technologies, equipment and services of 2022 in each Engineer, Build, Maintain and Manage tenet based on Google Analytics.
MoldMaking Technology Editorial Director Christina Fuges sits down with Murphy Forsyth, GM – Injection Molding and Director Of Marketing for Zero Tolerance LLC in Clinton Township, MI.
That was the sentiment of every person who came up to the MoldMaking Technology booth during last week’s Plastics Technology Expo to grab their giveaway “Molds Make” t-shirt after working the aisles seeking technology and process solutions and making new business connections.
PCS has released their new company website with features to help customers find exactly what they need, the company says.
Looking for local opportunities to see what's new in products and technologies for mold building and molding? Then mark your calendar for two events hitting the Northeast this fall, and MoldMaking Technology will be there to catch up on what's happening.
Giving the versatility of both ultrasonic and mechanical polishing, the PCS Company Ultramax DF unit enables users to polish right up to the wall, or finish to an edge.
For 40+ years, Dynamic Tool Corp. has offered precision tooling, emphasizing education, mentoring and innovation. The company is committed to excellence, integrity, safety and customer service, as well as inspiring growth and quality in manufacturing.
MoldMaking Technology’s annual Technology Review and Sourcing Guide is an accurate, comprehensive, easy-to-read and easy-to-use use guide for researching today’s technology, equipment, products and services. The year’s latest moldmaking product developments within mold engineering/design, build and maintenance/repair are broken down into 10 sections, including mold components.
PCS Co. says its new ProLifter is self-aligning and compensates for any misalignment from cumulative manufacturing tolerances and compound angles.
While processes like vacuum casting does a great job at simulating injection molding resin properties, it cannot compare to ‘true’ injection molding materials. SLA-printed prototypes may also be fine for many parts, especially if they are mainly cosmetic. However, with prototype injection molding, you can use the same materials that will be used in the final production process. This ensures that the prototype accurately represents the material properties, including strength, flexibility, and durability, this is especially critical for functional parts.
Advancements in mold components, hot runner temperature control and custom manifold configuration that address cycle time, quality and sustainability issues.
After attending IMTS, it's clear that the integration of advanced technologies is ready to enhance precision, efficiency and automation in mold manufacturing processes. It’s a massive event, so here’s a glimpse of what the MMT team experienced firsthand.
PCS Company’s Mold Storage Racks enable shop personnel to work safely and efficiently, while also providing support and protection for molds, dies and other equipment.
A water-based, eco-friendly plastic mold cleaning system helps Rankine-Hinman Manufacturing restore flow rates and avoid big-ticket failures on complex and costly molds.
There’s no doubt mold components and hot runners are important parts of the moldmaking industry. This preview gives mold buyers, mold builders and injection molders a look into PTXPO exhibitors displaying these technologies at the show.
Released earlier, this video remains a valuable recruitment tool and is being re-promoted in celebration of Manufacturing Day 2024.
In this most recent roundup, MMT continues to present a variety of innovative and proven technologies, mold materials and services to target the ever-evolving moldmaking industry.
Looking for an opportunity to see what’s new in products and technologies for mold building and molding? Then join MMT on October 3rd in Grand Island, Nebraska.
In this most recent roundup, MMT continues to present a variety of innovative and proven technologies, services and resources to target the ever-evolving moldmaking industry.
By using production-grade materials and manufacturing processes, these prototypes closely mimic the properties and performance of the final production parts. This enables engineers and designers to assess how the product functions in real-world conditions and identify design issues before committing to hard tooling.
The Mold Technologies Division of the Society of Plastics Engineers will announce the recipients of four awards at NPE on May 8 at the MoldMaking Technology Booth.
Angela Elsey, who has served as director of finance for PCS Company since 2019, has been promoted to president of the company.
While prototyping via injection molding may seem like an additional step, it often leads to time and cost savings in the long run. If anything is wrong, you can fix it before investing time and money into full-scale production tooling. ‘Fail early’ is a mantra of many production design development teams, and prototype injection molding allows you to do this in a relatively risk-free and inexpensive manner.
After attending IMTS, it's clear that the integration of advanced technologies is ready to enhance precision, efficiency and automation in mold manufacturing processes. It’s a massive event, so here’s a glimpse of what the MMT team experienced firsthand.
Steps to improve data-driven decision-making and key features of a cloud-based system for mold monitoring and asset management.
While prototype injection molding offers cost and time advantages over standard tooling methods when compared with other rapid prototyping techniques like 3D printing, CNC machining, or vacuum casting, it becomes more time-consuming and costly for production quantities below 100. Project budgets are generally tight and deadlines are even tighter, so why would you invest in prototyping via injection molding? Why not go straight from you 3D printed prototype to production tooling?
34500 Doreka Dr. Fraser, MI 48026 US 800-521-0546 | 800-521-0546 sales@pcs-company.com pcs-company.com
PCS Company will be exhibiting its oil filtration technologies dedicated to quality, clean oil to improve the performance and life expectancy of all components at Amerimold 2021.
What is prototype injection molding?Prototype injection molding, also known as rapid injection molding, is a process that incorporates rapid tooling (RT) method to produce injection-molded parts quicker than standard tooling times. This acceleration is achieved from using aluminium tools, eliminating certain complicated elements, or simplifying the tooling and manufacturing process. Due to the nature of the tool, it is also less expensive to make, which makes it suitable for rapid prototyping project budgets. While prototype injection molding offers cost and time advantages over standard tooling methods when compared with other rapid prototyping techniques like 3D printing, CNC machining, or vacuum casting, it becomes more time-consuming and costly for production quantities below 100. Project budgets are generally tight and deadlines are even tighter, so why would you invest in prototyping via injection molding? Why not go straight from you 3D printed prototype to production tooling? Why use prototype injection molding (over other rapid prototyping techniques)?Prototype via injection molding is a crucial step for several reasons, even when project budgets and deadlines are tight. While 3D printing and other rapid prototyping techniques offers a quick and cost-effective method for creating prototypes, transitioning directly from 3D printing to production tooling without injection molding prototypes can lead to various challenges. Here are six key reasons why prototyping via injection molding is essential: 1. Allows testing of parts in the production-intent materialWhile processes like vacuum casting does a great job at simulating injection molding resin properties, it cannot compare to ‘true’ injection molding materials. SLA-printed prototypes may also be fine for many parts, especially if they are mainly cosmetic. However, with prototype injection molding, you can use the same materials that will be used in the final production process. This ensures that the prototype accurately represents the material properties, including strength, flexibility, and durability, this is especially critical for functional parts. 2. Enables validation of the production process Injection molding is a specialized and complex manufacturing process. If you have not fully understood and tested these intricacies, you could open yourselves up to failure down the road. Parts manufactured via injection mold tooling can help you understand how the product will perform in the production process, validating the manufacturability of the design and identifying any issues related to tooling, parting lines, gate locations, and other aspects crucial for mass production. 3. Facilitates the testing of part buildsBy using production-grade materials and manufacturing processes, these prototypes closely mimic the properties and performance of the final production parts. This enables engineers and designers to assess how the product functions in real-world conditions and identify design issues before committing to hard tooling. 4. Enables low volume production runs and market testingAs the parts are essentially the same as production components, you can use them in early builds for market testing or even introduce them to the market place and start selling. Just because it is called ‘prototype injection molding’ doesn’t mean that it can only be used for prototyping purposes. It is also a viable and competitive option for low-volume production of 100 and over. 5. Allows satisfaction of initial demand while production tooling is being madeProduction tooling can take many months to have built. Even then it takes time to ship to the injection mold and get up and running. Instead of waiting and losing that valuable time you could use the prototype tooling to supply parts for initial demand. And it is a good backup should your production tool be out of action for whatever reason. 6. Helps save on time and costsWhile prototyping via injection molding may seem like an additional step, it often leads to time and cost savings in the long run. If anything is wrong, you can fix it before investing time and money into full-scale production tooling. ‘Fail early’ is a mantra of many production design development teams, and prototype injection molding allows you to do this in a relatively risk-free and inexpensive manner. How to choose a prototyping methodPrototype injection molding is just one of the many prototyping and production services offered at HLH Rapid. We also provide CNC machining, 3D printing, and vacuum casting services. Not sure which method is best suited for your project? Get a free quote for each rapid prototyping technique by submitting your CAD and project details on our website contact form.
March was a big month for MoldMaking Technology. Not only did we celebrate our 25th Anniversary, PTXPO, and announced the return of the Leadtime Leader award, we also continued to cover some of your favorite topics. Take a look at what you might have missed in March.
Discover how CAD/CAM functionality tailored for the mold industry can significantly enhance the mold design process. In part three of the webinar series, Cimatron will focus on designing waterlines and cooling components. It will demonstrate how CAD/CAM tools can verify drill line depths for water lines and baffles, ensure that minimum steel requirements are met while placing water lines, and provide a complete list of all baffle cutoff lengths. Additionally, it will explore how to confidently design runners and gates using CAD functionality specifically developed for these aspects of mold design. Agenda: Waterlines and verification Conformal cooling Baffles and charts Runners and gates
Moldmakers aren't the only ones reducing leadtimes. Component and hot runner suppliers are delivering their equipment and supplies faster to accommodate industry demand.
Production tooling can take many months to have built. Even then it takes time to ship to the injection mold and get up and running. Instead of waiting and losing that valuable time you could use the prototype tooling to supply parts for initial demand. And it is a good backup should your production tool be out of action for whatever reason.
PCS Company is a team of industry experts providing solutions and innovative products for the plastic injection molding, mold making, and die casting industries
PCS Company offers Karcher Dry Ice Blasters in 4 models that are tailored specifically for long term or short-term cleaning of ...
Whether it’s purchase quoting, mold cleaning and tracking or intuitive process control, the following new or improved technologies could potentially keep your shop on the cutting edge.
PCS Company's MCS hot runner temperature controllers offer reliable and precise control of the hot runner system with the ...
PCS Company's Codipro Mold Lifting Rings are said to provide more efficient material handling and moving of molds and dies in any shop or molding facility.
MoldMaking Technology’s 2019 Technology Review and Sourcing Guide offers some of the latest highlighted products and services from supplier companies from a variety of categories, including mold components.
With Molding 2020 only a couple weeks away, catch up on who will be attending and what you can learn from this educational conference.
Prototype via injection molding is a crucial step for several reasons, even when project budgets and deadlines are tight. While 3D printing and other rapid prototyping techniques offers a quick and cost-effective method for creating prototypes, transitioning directly from 3D printing to production tooling without injection molding prototypes can lead to various challenges. Here are six key reasons why prototyping via injection molding is essential:
MoldMaking Technology’s annual Technology Review and Sourcing Guide is an accurate, comprehensive, easy-to-read and easy-to-use use guide for researching today’s technology, equipment, products and services. The year’s latest moldmaking product developments within mold engineering/design, build and maintenance/repair are broken down into 10 sections, including hot runners.
The Mold Technologies Division of the Society of Plastics Engineers (SPE) honored recipients of four awards at NPE, recognizing excellence in moldmaking and supporting the next generation with a new Apprentice of the Year award. Each winner receives a $1,000 stipend for their training program.
PCS Company’s new chrome high-pressure oil filters come in three units for use with hydraulic and hybrid injection molding machines.
Correct alignment lock selection can reduce maintenance costs and molding downtime, as well as increase part quality over the mold’s entire life.
With all the technology joining the market, moldmaking is a versatile, ever-evolving industry. As such, this technology roundup has no specific theme — it features a variety of products for applications and solutions across the industry.
Hot runner suppliers are developing solutions that remove complexities from the way that moldmakers and molders design, control and maintain their processes.
In ISO 9001 quality management systems, the Management Representative (MR) plays a crucial role. While the 2015 version of ISO 9001 no longer mandates this position, having a trusted management member serve as an MR remains vital for streamlining operations and maintaining quality standards.
PCS Company’s Nozzle Leak Detector (NLD) can sense plastic leakage between the mold and the machine nozzle, catching the problem before major maintenance is required.
Diamond compounds, with their varied grades, colors and base options, provide a comprehensive solution for mold builders in need of precise and superior polishing across diverse materials and applications.
Formnext Chicago is an industrial additive manufacturing expo taking place April 8-10, 2025 at McCormick Place in Chicago, Illinois. Formnext Chicago is the second in a series of Formnext events in the U.S. being produced by Mesago Messe Frankfurt, AMT – The Association For Manufacturing Technology, and Gardner Business Media (our publisher).
Intralox's integration of the Alpha Laser ALFlak has significantly improved their tool room efficiency when it comes to difficult welds and urgent repairs.
In the midst of exhibitors breaking down at the close of Amerimold 2019, the MoldMaking Technology editorial team set up shop at the MMT booth to do a live Manufacturing Alliance Podcast, sharing some immediate insight and feedback on this annual event.
Engineers use properly preloaded bolts, blocks, springs and side-action cores to enhance functionality and reliability in various mechanical systems.
This week’s highlighted mold component products can provide simple solutions for identification, prevent mold damage, offer time-saving advantages and monitor exact cavity pressure for your business’s production needs.
iD Additives, Inc. has named PCS Company of Fraser, Michigan, as its exclusive distributor to injection molders and moldmakers in the U.S.A. for its iD Eco-Pro 360 rust removal systems.
PCS Company presents Min-Lube, an advance grease offering thermal, oxidative and mechanical stability for high-wear, high-temperature applications.
GETTING A QUOTE WITH LK-MOULD IS FREE AND SIMPLE.
FIND MORE OF OUR SERVICES:
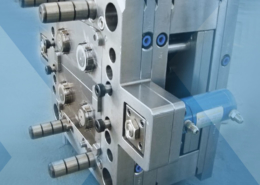
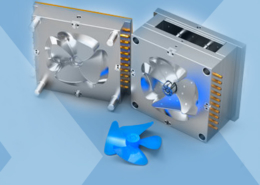
Plastic Molding

Rapid Prototyping
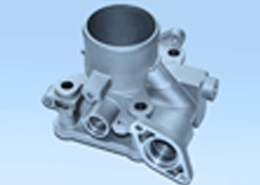
Pressure Die Casting
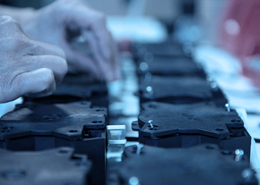
Parts Assembly
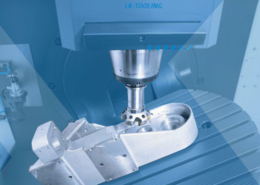