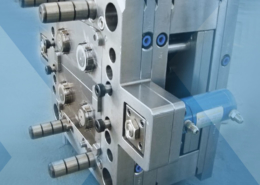
Custom Plastic Injection Molding Services - custom molded plastics
Author:gly Date: 2024-10-15
We set up work instruction for whatever in-housing manufacturing process or outsourcing to ensure our are always the right foot to customer's specification.
Inno Manufacturing, a high quality contract manufacturer in Shenzhen China. We specialize in one-stop custom contract manufacturing services from parts to finished products.
Our sophisticated team brings a vast experience for a variety of industries including medical & beauty, home appliance, consumer electronics, sports & outdoor, automotive, etc.
Compared to single-shot injection molding. The use of two shots can make more complex designs possible. Some designs may not be possible by injection of the melt into the mold in a single shot. These are possible by using two shots. For example, achieving double layers with different colors.
The following are some of the advantages of using 2 shot injection molding. Note that these are as well as the general advantage of injection molding.
Golden sample with customer's signature will set aside of work station, so that our QC, technician, or operator can have standard reference.
The process has some similarities with other overmolding processes like insert injection molding. The difference here is that an insert is not placed in the mold. The substrate is molded in the same mold. Also, the 2 shot system uses two injection units feeding different materials. This is unlike conventional systems where one injection unit feeds the same material. This process requires an initial shot, followed by a second shot. Hence the name 2 shot injection molding. This process uses two injection units.
Our project manager outlines all of critical checkpoints that used for process QC inspection. This process inspection is avoid defective parts to be produced.
This has the advantage of giving better aesthetics. In some cases, it also contributes to the better functioning of the product. For example, joining by welding or gluing introduces vulnerable points in a product. The 2 shoot process creates a more uniform appearance and better joining.
The fact that two parts get processed at once reduces the time required. It also reduces the need for more stages or equipment for joining. The joining 2 shot injection molding machine achieves might otherwise need complex machinery. Processes like micro-welding or laser welding add cost and time to the process.
The conventional injection molding process manufactures products that meet diverse industry needs. But some products need some modifications to the conventional injection molding process. This could be to achieve a more complex design or to make the production process more efficient. Such advancement could result in significant cost reduction and time-saving.
2 shot injection molding is one of such advances in conventional injection molding. It is adaptable to the production of complex designs using a wide range of materials. 2 shot injection molding achieves high quality of products. It is a well-established technology in the manufacturing industry.
The 2 shot injection molding process is a step up to the conventional injection molding. Of course, there are products produced fine without 2 shot injection molding. When deciding if 2 shot molding is the right process, the following are factors to consider. This article presents them as sort of boxes to tick when deciding.
The injection units could be a combination of horizontal and vertical injection molding. In such a process, the first shot is from the horizontal injection unit. The second is from the vertical. This way the process takes advantage of the vertical injection process. In this combination of orientation, the injection of the overmold is easier. The image below is an illustration.
All of critical dimensions must be measured every 30 minutes with AQL lot standard, and we also provide SPC data to clients for any mass production.
Our engineering team reviews and evaluates each project deeply with profound experience and knowledge. A comprehensive DFM report will be provided to customer for review.
The figure below gives an example process illustration. In the illustration, the first shot is an injection of thermoplastic. The second shot is liquid silicone rubber. The thermoplastic will melt to the softening point of the plastic. When injected into the mold, it hardens through cooling only. The silicone rubber can harden either at room temperature or at elevated temperature. Elevating the temperature could increase the rate of hardening of the silicone rubber. How the silicone hardens depends a lot on the chemistry of the specific silicone. The silicone rubber overmold also takes some heat from the hardened thermoplastic. This is if injected at a lower temperature. The thermoplastic could have hardened but still is hot.
In the 2 shot injection molding, a two-part product gets made in a single cycle. This is compared to when a cycle is only making half of the part. This means more done in one cycle. Even where this makes one cycle longer. It is faster than the time it takes to run two separate cycles. At the very least the cooling of the parts occurs at the same time. The few seconds saved per cycle adds up. When for instance where over a thousand cycles run in a day.
Based on quoted cost, timing, and other manufacturing terms, customers would confirm the order by issuing a PO and pre-payment. Normally we do 50%-50% of payment term for all of clients.
The more components introduced, the more complex the product. This means more cost of the material. For products such as thermoplastics, this makes recycling difficult. A 2 shot recycling process makes separation easier. A part of the material that can easily separate from the other part. For example, one part can dissolve away in a type of solvent which the other is insoluble. Separation could also be by melting point and density. One part of the product melts at a lower temperature this way the higher melting part can float or filter off. Such processes are more mass reproducible. This is compared to recyclers fiddling with glued parts by hand.
The process where two shots inject into the same mold during a cycle requires modifying. Two shots fill at the same time into two separate cavities of the same mold. So the 2 shot injection molding requires more machinery. These are a second injection unit and a rotating mold mechanism. This does not mean having to buy a second injection molding machine. Two injection units integrate into the same machine. This way two separate feed hoppers channel to respective injection units. This feeding of the substrate and the overmold materials through different paths. The filling is manual or automated depending on the scale and type of process. It is possible to use the same ancillary systems to operate the two injection units. For example, connecting the injection units to the same temperature control units. This depends on the required setting for the types of materials used. For example the melting points and melt viscosity of the materials.
Different materials get processed in 2 shot injection molding processes. In a different product other than in the image above the materials could vary. For example, silicone rubber is replaced by thermoplastic. This should be one with a lower melting point than the substrate. The substrate could be injection-molded material other than plastic. For example metal or glass. To determine what goes in the first or second shot, the thermal properties are important. If a material with a lower softening temperature as the substrate poses a problem. If the second shot has a higher melt temperature this softens the substrate. This leads to a distortion of the structure of the substrate. It could also cause the mixing of the two materials since they are both now soft. So at the very least, the melt temperature of the substrate should be much higher than that of the second shot.
With in-house mold making and injection molding shop, we work from mold tool making to plastic product contract manufacturing, available for parts weight from 0.5~2.0 KG with peace of mind at product quality, cost, and dead-time
The second shot is next. The screw begins to rotate and move back again as more material mixes and melts in the barrel. In this time it takes to refill the melt chamber, the first shot in the mold(s) cools, the mold also rotates. This is in such a way that the filled mold cavity moves to another point replaced by an empty cavity. Once the melt chamber fills, the screw reciprocates in the same manner as before and fills the empty mold. At the same time, a separate injection unit then fires a second shot. Usually with a different material, over the first shot of the filled mold. This second shot fills over the first shot which by now has hardened. The first shot serves as the substrate while the second shot serves as the overmold. An example of substrate material is for example a thermoplastic. The overmold can then be a thermoplastic or thermoset elastomer.
The mold rotation mechanism is in such a way that it happens after the first shot. It then rotates for the second shot to fill the mold while a first shot fills into the empty molds. So each mold gets two shots. The timing of the rotation allows time for solidification or hardening of the first shot. This requires the engineer to have a good knowledge of the properties of the material. Factors such as crystallization temperature and shrinkage are important. For example in determining the point at which the second shot fills. This aids in the proper timing of the mold rotation. The usual design is a two-plate mold system where the mold opens in half after cooling. The base half of the mold then rotates. The half closer to the injection unit remains stationary. This is because of the simplest design. This half of the mold attaches to the injection unit. Opening the mold is quicker than detaching the two injection units from the molds. This saves cycle time. Since the mold rotates after opening and closing, the fit is important. The rotated half must match the other half with precision. If when rotated the mold is not identical, it either doesn’t close well or leaks.
Our on-line QC(IPQC) check out parts appearance comprehensively to avoid any flash, sink mark, short shot, deformation, scratch, dirty, marks, and so on.
You might find 2 shot injection molding also called other names. It is also called twin shot injection molding. Other names are, overmolding, multi-component molding, or assembly injection molding. In a sense, it is a variation of the overmolding injection molding. Although you will find both terms used in some publications. Understanding what distinguishes one from the other is important. 2 shot injection molding requires the same main components as the conventional type. An injection unit, a clamp unit comprising the runner, the sprue, gate, and mold are the main components. The process begins in the same way as conventional injection molding. The starting feed for the material passes into the hopper. For thermoplastic, this is the pellets of plastics. These then mix and melt in the heated barrel as the screw applies shearing force. The screw pushes the melt forward into the melt chamber. The melt reaches the set shot size when the reciprocating screw reaches the limit switch. This triggers the screw to move forward at high velocity powered by a hydraulic cylinder. This action forces the melt into the mold(s). This is the first shot. As the mold cools, the machine begins the second phase of the cycle.
Our experienced logistics team schedules and arranges each shipment to be delivered to customer punctually, cost effectively, and safely.
To cater to customer's one-stop mold making and injection molding services, We combined mold making shop and plastic injection molding facility together, it enables us to make new mold and modify old mold tool conveniently and quickly. Inno manufacturing has over 20 years of mold making experience in making diverse kinds of mold tools. We make high precision, durable, and cost effective mold tools based on customers' requirement.
One crucial factor here is timing. The timing of the screw rotation must synchronize with one another. The rotation of the screws and the firing of shots must also synchronize with the mold rotation. The shot sizes for the different injection units are often different. This depends on the design need of a specific product. The difference in shot sizes makes it more challenging to synchronize the processes. The 2 shot injection molding system means that there are more processes in one cycle. The success of the process depends on how seamless the repeated sequence of steps is.
We assembled parts with whole unit to simulate product function that verify if our part structure or property function accordingly.
Our production team plans, performs, and monitors customer order that takes over from marketing team. Ensuring each order would be completed on-schedule, high quality, and within budget.
The 2 shot injection molding is a variation of injection molding. It allows for the production of more complex designs in a single cycle. With this type of injection molding, extra processes to join parts are not needed. Application of 2 shot injection molding cuts across several industries.
Plastic injection molding is the most common manufacturing process to obtain plastic products with large scale of volume. Inno manufacturing engaged in plastic injection molding contract manufacturing service since 2001. Over 20 years of experience, we accumulated skillful engineers, technicians, and operators that enabled us to provide customer high precision, consistent quality, and professional services. Here below are our capabilities:
Our state-of-the-art plastic injection molding shop located in Shenzhen China provides cost-effective mold tooling and plastic injection molding services.
Clients send us project information(stp file, parts material, parts color, and manufacturing volume) upon signing up NDA via email, Skype, or phone. We provide free quotation and project evaluation within 24 hours.
Our QC team work throughout each project from start to shipping. IPQC inspects and monitor when production starts to run. and FQC double-check the finished products based on AQL standard.
Starting from raw material sourcing, injection molding, until full assembled products, our on-site QC inspect and monitor the whole manufacturing process to ensure a high quality molded products to be made at us. We perform 100% of parts inspection with CMM, projector, and micrometer, our goal is to make zero defect rate for each orders.
GETTING A QUOTE WITH LK-MOULD IS FREE AND SIMPLE.
FIND MORE OF OUR SERVICES:
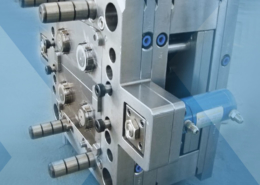
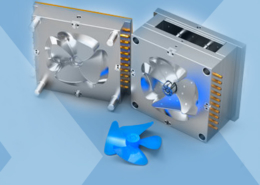
Plastic Molding

Rapid Prototyping
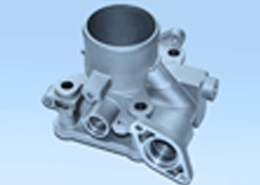
Pressure Die Casting
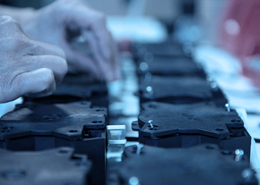
Parts Assembly
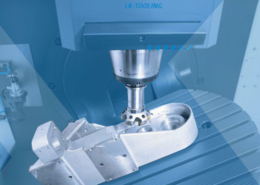