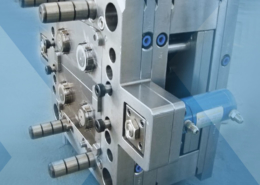
Custom Plastic Injection Molding - custom injection
Author:gly Date: 2024-10-15
Polystyrene is a widely used thermoplastic with a melt temperature typically around 356°F to 464°F. This ensures efficient processing inside the injection molding equipment. It is known for its transparency, ease of molding, and affordability. PS can be categorized into two main types: general-purpose polystyrene (GPPS) and high-impact polystyrene (HIPS). PS is prone to cracking instead of deforming.
ABS is a thermoplastic polymer known for its exceptional impact resistance, toughness, and dimensional stability. It has a molding temperature around 410°F to 527°F, which ensures proper flow and mold filling during injection molding.
Plastic Molded Concepts is a U.S based company that uniquely specializes in molding with engineered resins. We have been thriving in the plastic molding business for 45 years. We have the experience and certified in-house Master Molders, allowing us to take on projects of any complexity.
One of the most important decisions you’ll make is selecting the appropriate injection molding materials for your part. Material selection significantly influences your product’s performance, durability, and cost. In this guide, we explore the most common materials, their strengths, molding temperatures, common applications, and other important properties. By the end of this guide, you’ll be able to make an informed decision for your project.
Polycarbonate is a transparent thermoplastic known for its exceptional impact resistance, optical clarity, and high-temperature resistance. PC should reach a molding temperature around 518°F to 608°F, ensuring the material flows smoothly into the mold cavities.
PPS is a high-performance thermoplastic known for its exceptional chemical resistance, flame retardancy, and high-temperature stability. It has a molding temperature around 536°F to 626°F. Although these melt temperatures are achievable on most molding machines, the molds themselves often require running at temperatures above 212 degrees F. Hot oil temperature controllers may be required.
PBT is another commonly used thermoplastic for injection molding. Its molding temperature range is 428°F to 500°F, allowing for efficient processing in various injection molding machines.
If you’re unsure what material is best, contact us to consult with one of our material experts. We’ll ensure you choose the most suitable material that aligns with your project goals and other requirements. With the right material and proper molding technique, you can create high-quality, durable products that meet or exceed your expectations.
PET is a strong, lightweight thermoplastic with a relatively high melt temperature, typically around 500°F to 554°F. Although these melt temperatures are achievable on most molding machines, the molds themselves often require running at temperatures above 212 degrees F. Hot oil temperature controllers may be required when using injection molding materials like this.
Polyamides are commonly known as nylon. They are one of the most used engineering thermoplastics. Nylon is extensively used for wire coatings and other electrical components. Glass filled nylon is the preferred choice when you need a tougher material, as it makes the nylon considerably stronger.
POM, also known as acetal, is a high-performance engineering thermoplastic with excellent dimensional stability and low friction. Its molding temperature ranges from 347°F to 410°F. This is critical to achieve desired flow consistency during injection molding.
Polyvinyl chloride is a thermoplastic polymer known for its excellent chemical resistance and flame retardancy. It’s typical molding temperature ranges from 320°F to 410°F, allowing for the production of a wide range of products.
Polypropylene is a versatile thermoplastic known for its excellent chemical resistance. It has a melt temperature from 320°F to 464°F, making it suitable for both low and high-volume production processes.
The addition of glass powder or fibers to nylon resin creates this engineering grade resin. Glass is added to polyamides to increase their mechanical strength, rigidity, and hardness. It also makes them more resistant to creep, wear, chemical exposure, and high temperatures.
Scientific plastic molding design, material processing, and process control are advancing. Glass filled nylon injection molding can create molded parts that replace metal parts. This is beneficial for applications that require a reduction in weight or noise.
Nylon, also known as polyamide, is a popular thermoplastic renowned for its high strength, toughness, and excellent wear resistance. The molding temperature typically ranges from 446°F to 572°F, depending on the specific type of nylon being processed.
PMMA, commonly known as acrylic, is a transparent thermoplastic known for its optical clarity, UV resistance, and weatherability. Its molding temperature is on the lower end when compared to other injection molding materials. Typically molded around 464°F to 518°F, this allows it to be processed in a variety of molding machines.
Plastic Molded Concepts has expertise in molding with many different engineering-grade resins, including glass filled nylon.
Since the glass filled material is nonconductive, it is ideal for applications within the automotive and electrical industries. It is also a practical choice for manufacturing parts that handle electrical currents.
Glass filled nylon injection molding is a practical choice for creating durable molded parts that will encounter friction and wear. The main characteristics and benefits of molding with this material compared to general purpose nylon include:
We provide a comprehensive range of plastic molding services including mold design assistance, modeling, prototyping, manufacturing, and testing.
These qualities make glass-reinforced polyamides superior to general purpose polyamides. The engineered resin has advantageous mechanical properties. It is suitable for injection molded parts that need to endure high static loads over long periods in high temperature environments.
Selecting the right injection molding materials can make or break your injection molding project. As you can see, each material has its unique properties, advantages, and limitations. Remember, the material you choose not only impacts the performance of the final product but also manufacturing costs and the environment.
Polyethylene is a thermoplastic polymer known for its excellent chemical resistance, low cost, and ease of processing. Melt temperatures start around 375 F, but generally have a wide range from there. PE is categorized into different types based on its density. Low-density polyethylene (LDPE), high-density polyethylene (HDPE), and ultra-high-molecular-weight polyethylene (UHMWPE).
GETTING A QUOTE WITH LK-MOULD IS FREE AND SIMPLE.
FIND MORE OF OUR SERVICES:
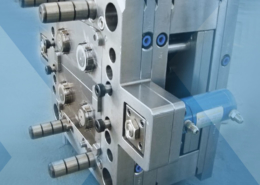
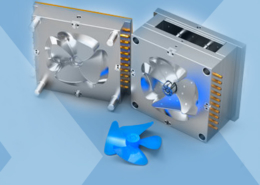
Plastic Molding

Rapid Prototyping
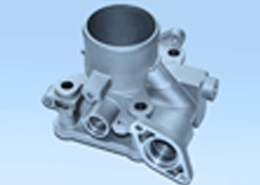
Pressure Die Casting
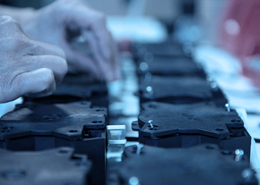
Parts Assembly
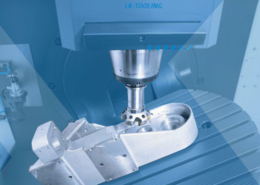