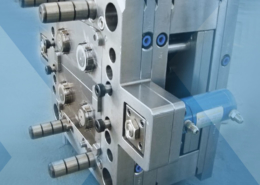
Custom molds - Soft Plastics - custom soft plastic molds
Author:gly Date: 2024-10-15
This method drives things through a die to form shapes with consistent cross-sections such as window parts, drinking straws, pipelines, and seals. This approach is used to create two-dimensional shapes. The extrusion machine’s motor spins a screw that pushes plastic via a heater.
This is among the most used ways of molding polymers into 3D forms. It is founded on the molten die casting process and comprises a clamping unit and an injection unit.
Because of the intricacy of the mold construction, injection molding generally has a higher initial design cost. Its cyclical manufacturing, on the other hand, usually results in a completed component that does not require additional assembly or secondary processing.
In comparison to other manufacturing practices, plastic injection molding for medical devices is very flexible and allows for full customization of components. It is used in high volume situations to fulfill injection molded medical device and drug delivery devices with high accuracy and precision. From an operational perspective, plastic injection molded medical devices are produced with low labor costs, are positioned to be scalable as the client grows in sales, and are more environmentally friendly due to the extended life of the product and reduction of waste.
The choice between plastic extrusion and injection molding does not have to be a contest. Both of these technologies serve distinct functions and have distinct advantages, and both are beneficial to plastic producers. Extrusion cannot generate the intricate 3D forms that injection molding can, nor can injection molding produce the unusual cross-sections that extrusion can. Each technique has a distinct position in the plastic production process.With that knowledge, we believe you’re well off on your journey to understanding the plastic molding process and can choose a molding form or manufacturer wisely. If not, do remember to read again, for valuable insights into the issue.
Among industrial producers, injection molding and/or extrusion processes are defined to create items of various forms and sizes. The injection molding technique is built on the melted die-casting technology. The clamp and the injection unit comprise the injection-molding unit. Injection molding, as opposed to extrusion, produces three-dimensional structures.
Our facility utilizes high-precision plastic injection molding and injection mold tool building equipment. In-house injection molding machines range in tonnage from 30-Ton to 250-Ton. Injection molding capabilities range from single cavity, pre-production injection molds to high cavitation molding using a hot runner system. The injection molding equipment used by Medacys is manufactured by some of the most trusted brands in the industry, including Sumitomo (SHI) Demag, Toyo Machinery, and Haitian International.
In 1795, Joseph Brahman patented the first hydraulic press. However, the method was more thoroughly refined in 1820, when Thomas Burr invented the first hydraulically driven press for manufacturing firms. The method was not developed until 1894 to incorporate brass and metal alloys for non-continuous extrusion of final components. The injection molding method as we recognize it now would be eventually created in the 1930s.
Located in Shenzhen, China, is Medacys – Gilero’s joint venture toolmaking and medical injection molder. This state-of-the-art injection molding facility spans 36,000 square feet and is staffed by manufacturing technicians, tooling designers, quality engineers, and engineering project managers. The expertise of the Medacys team focuses largely on the medtech and biomedical industries. With dedicated tooling, molding, assembly, and lab areas, along with environmentally monitored and controlled cleanrooms, our Shenzhen facility provides plastic injection molding services for companies across the globe.
In terms of plastic extrusion, this method was first used to process rubber in 1836. This is a technique in which molten plastic or a variety of alternative materials are constantly forced into a two-dimensional die aperture by feed screws. The molten form is then passed through a succession of templates or blocks, where it preserves the correct shape as it cools.
The plastic resin is placed in the hopper, which causes the plastic out from the feed portion to be released into the compressing area, where friction heat is applied. A reciprocating screw pushes the plastic through a long chamber. Melting, or molten plastic, is pushed via the injector into a sealed, cooled/hot mold. The melt may be readily shaped into the mold’s desired form and size.
Gilero provides a range of manufacturing services, including plastic injection molding and injection mold tool building. We focus solely on the medical device and drug delivery markets. Our medical injection molding facilities follow strict design protocols and process controls to ensure that all products meet the required specifications. Depending on client needs and product requirements, we can offer manual or fully automated production lines for molding and assembly.
Injection molding and extrusion molding are two prominent plastic molding processes used throughout the industrial and manufacturing sectors to create items of various shapes and sizes. Both approaches offer distinct advantages based on the products and the consumer. Let’s look at the distinctions between injection molding and extrusion molding to help you decide which is ideal for your manufacturing needs.
Extrusion is capable of producing complicated cross-sections, including such multi-lumen tubing used in medical equipment or food processing. Extruded materials have flat surfaces that do not necessitate post-production “clean-up.”
When a range of lengths of the same profile shape is required, extrusion is appropriate. Setup and design expenses for comparable products are minimized by creating a stock product with a continual production chain and cutting to length post-process per order.
The polymer granules melt into fluid, which is then forced through a 2D die open tool. This pushes the materials into a hollow tube based on the die’s particular geometry. After chilling, the material solidifies into a tube shape. This item is now waiting to be cut into the desired sizes.
The choice of material will depend on the specific requirements of the part being produced, such as its mechanical properties, chemical resistance, and environmental factors like temperature and humidity.
Gilero stands out as an excellent choice for medical device injection molding manufacturing. Medacys, our joint-venture facility in Shenzhen, China, spans 36,000 square feet and is equipped with cutting-edge technology. The skilled team, comprising manufacturing technicians, tooling designers, quality engineers, and engineering project managers, specializes in the medtech and biomedical sectors. This specialization ensures a deep understanding of the unique requirements and regulatory standards in these fields. Gilero offers dedicated areas for various manufacturing processes, including tooling, molding, assembly, and laboratories. We maintain environmentally controlled cleanrooms for precision. Our in-house injection molding machines range from 30-Ton to 250-Ton, and they use equipment from trusted brands like Sumitomo (SHI) Demag, Toyo Machinery, and Haitian International.
Plastic molding is generally accomplished through two processes used by plastic producers. Plastic injection molding is the first method, in which producers “inject” molten polymer material into a mold and allow it to settle and cool into a specified form. Manufacturers push molten plastic through a die to generate the required form in the second process, plastic extrusion.
The completed result from the extrusion process has a two-dimensional shape that is continuous in length. Extrusion creates linear forms that may be cut to different lengths and/or notched, punched, or otherwise produced, frequently while the process is running.Extrusion and injection molding both have benefits. The capacity to generate complicated cross-sections is one advantage of employing the extrusion technique over other approaches. Furthermore, as compared to other techniques, both rigid and soft materials may be molded into any shape, and the final products have a flawless surface finish. There is little waste in both the injection molding and extrusion operations since the debris may be recycled again.
GETTING A QUOTE WITH LK-MOULD IS FREE AND SIMPLE.
FIND MORE OF OUR SERVICES:
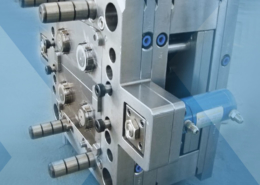
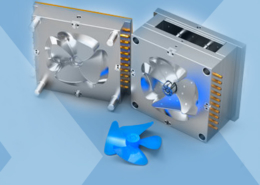
Plastic Molding

Rapid Prototyping
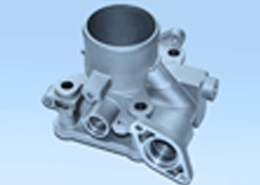
Pressure Die Casting
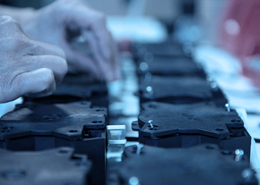
Parts Assembly
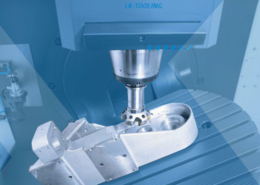