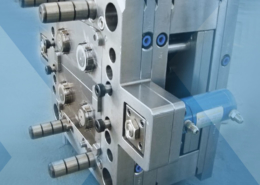
Custom Molding Services - molding services
Author:gly Date: 2024-10-15
Rotational molding, or "roto-molding," involves pouring melted plastic into a mold, which is then rotated at a high speed. This coats the plastic evenly along the walls of the heated metal mold, leaving the interior hollow. This method is primarily used for large, hollow-walled containers, storage bins, and even kayaks.
Compression molding is most often used with thermoset plastics whose chemical structure changes when melted and cooled to create a hard, rigid final product. Plastic resin is heated to a soft, almost "putty" state where it's not quite liquid, then it's placed into a heated mold. The putty is then pressed into shape by the mold and allowed to cool.
When designing plastic products and components, one of the most challenging decisions is determining the right method of manufacturing them. Your goal is to have a durable, high-quality finished product while minimizing costs and speeding up efficiency and the right manufacturing method is key to meeting these goals. There are six main types of plastic manufacturing, and our thermoforming company in North Carolina is looking at each type and the associated benefits they offer.
Blow molding is similar to injection molding as the plastic is heated to a liquid state and injected into a mold. However, once the plastic is placed in the mold, air is injected into the plastic, inflating it so that it presses against the walls of the mold and achieves the desired shape.
Since 1988, Advanced Plastiform, Inc., has been providing superior custom plastic molding and fabrication services to companies in North Carolina, South Carolina, Maryland, Georgia and Pennsylvania. Contact us to make an appointment Mon-Fri 8-5.
At Advanced Plastiform, Inc., we specialize in heavy-gauge thermoforming and injection molding. Our experienced team includes engineers and designers as well as manufacturers, all of whom are dedicated to helping you meet your goals. Our company works with industries across the Mid-Atlantic and Southeast, including North Carolina, South Carolina, Pennsylvania, Maryland, Tennessee, Georgia, and Virginia. To learn more, call us at 919-404-2080 or fill out the contact form to get started.
At Sonoco, we believe in harnessing the power of process to drive innovation. Our proprietary i6 Innovation Process leverages market insights with advanced technical expertise to fully imagine, test, produce and deliver 360-degree solutions. While innovation demands creativity, free-thinking and imagination, the i6 Innovation process gives it direction, power and purpose. Adhering to this disciplined approach is vital to helping solve problems and consistently deliver repeatable, scalable custom plastic injection molding services for our customers.
Extrusion molding is primarily used to manufacture long, straight pieces, such as tubing, hoses, or pipes. This method involves forcing liquid plastic into a die to form a shape. While round pieces are common, t-shapes, l-shapes, and squares are also achieved, depending on the shape of the die. Many thermoplastics can be used during extrusion molding.
Sonoco provides custom injection molding services to make plastic parts and components for virtually any product application across a range of industries. Businesses who demand the best use our custom injection-molded plastics in a wide variety of products, from surgical-grade medical devices to highly technical automotive components.
Injection molding is a plastic manufacturing method in which a thermoplastic is melted to a liquid, then injected into a double-sided mold using a highly pressurized injector. The plastic coats and fills the mold to create the needed shape, and is then cooled and ejected for finishing.
Guiding customers through every stage of a custom precision molding project, our comprehensive approach includes advanced design and engineering assistance, mold making, prototyping, real-world testing and automated assembly services.
Thermoforming involves heating a large sheet of plastic until it is soft and flexible, then stretching it over a single-sided, custom mold. Vacuum pressure or compressed air presses the thermoplastic tightly against the mold, creating the desired shape.
Whether you’re using custom plastic injection molding to manufacture medical devices more efficiently, to prevent contamination of apparel products, or to reduce the weight of car parts and components, Sonoco has the experience, expertise, and craftsmanship to ensure the success of your project.
GETTING A QUOTE WITH LK-MOULD IS FREE AND SIMPLE.
FIND MORE OF OUR SERVICES:
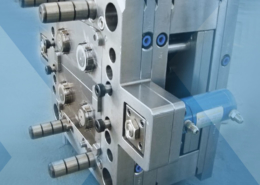
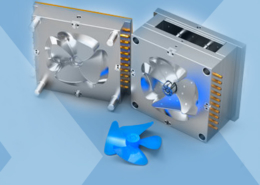
Plastic Molding

Rapid Prototyping
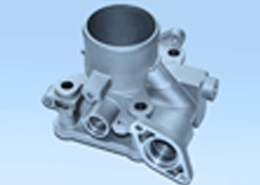
Pressure Die Casting
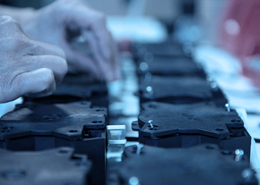
Parts Assembly
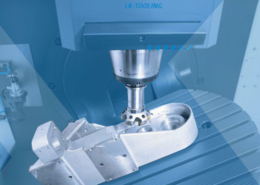