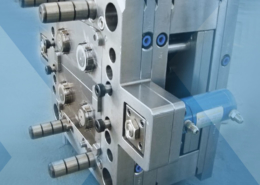
Custom Injection Molding | Sonoco Products Company - custom plastic molding comp
Author:gly Date: 2024-10-15
Ultimately, this list only scratches the surface of how many everyday injection molded objects appear in the average household. However, it shows the versatility and reliability of the injection molding process. Most people never think about how the objects they use were made, but this information is crucial if you have plans to manufacture products yourself.
There are more plastic parts in and on a toilet than you might expect, but the toilet seat is the most prominent example. With various shapes and sizes, such an injection molding product takes advantage of the same plastic properties other products do. These properties include bacterial resistance, a non-porous surface that can undergo sterilization and a high degree of long-term durability. The toilet hardware itself will likely wear out long before the seat ever does.
There are several prototype tooling options for your designs. The one you choose depends on what you expect to accomplish with the prototype. For example, will the prototype be subjected to testing? Does it need to be "dressed up" for presentation? Will it need to meet tight tolerance requirements?
Let's explore the most common prototyping options: SLA/SLS, urethane cast, soft tooling, and hard tooling. Which is right for your component? Read on to discover the advantages and disadvantages of each.
While injection molding doesn’t contribute much to the major hardware components on computer circuit boards, it touches almost every other aspect of these devices. Everyday items that undergo injection molding for use in computers include laptop shells, speaker housings, computer monitor bezels and even the keyboards you type on every day. The durability of these materials makes them well-suited to the long lifespan requirement for most computer hardware. Additionally, things such as light switches, other electronic housings, and a wide range of appliances also come from injection molds.
While the classic wooden chair still has its place in the home, a wide variety of modern furniture, especially chairs, now feature all-plastic construction. Injection molds can produce these parts to exact tolerances for consistency between production runs. At the same time, making molds large enough to create full-sized furniture or components that will undergo assembly by the user at home is also straightforward.
There are several different variations or options for soft tooling, but typically tools and samples can be turned around in a few weeks. This may be an option for early prototype builds if the parts are simple, tolerances are loose, and function and fitment are not critical requirements. Soft tools, however, have limited ability for design or dimensional changes once the tooling is complete and sampled. Processing development is also limited.
Molding works well for various kitchen products, such as plastic plates and utensils. These products must often be resistant to elevated temperatures, easy to clean, dishwasher safe, and non-toxic. Injection molds can mold materials that meet all these requirements at high volumes.
Toys for children are also among the most common injection molded plastic parts for several reasons. First, you can expect complex toy designs and true-to-life colors from injection molds. Second, the ability to combine materials allows the molding systems to produce huge volumes in a relatively brief time. Lastly, the material selection also contributes to the popularity of this method with toys, because it is easy to make non-toxic, non-porous, and easy-to-wash products.
Terracotta pots are lovely, but they’re expensive. Plastic flowerpots provide the same stable space for plants to grow while resisting breakage and lasting for a far longer time. Thanks to the tooling design, these everyday items and garden products also come out of injection molds, as it is easy to create the necessary shape while leaving drainage holes at the bottom with few to no additional manufacturing costs.
Urethane cast/mold is a low-volume production method that utilizes polyurethane plastic materials to produce prototypes. These products are ideal for marketing samples because they can be finished to look like hard-tooled plastic parts. Materials are limited and may not be able to deliver the same qualities that preferred production plastics can. Urethane cast/mold can be a cost-effective method of prototyping if there is a need for a higher quantity of parts at the fitment or proof-of-concept stage. Overall the process is fairly limited and becoming less common in the industry.
Given the uncountable number of different beverage products on the market, you are more likely to have at least one injection-molded plastic bottle in your home. PET, a common plastic material for bottle design, flows easily through injection molds and creates durable yet lightweight products for use as liquid containers. Even reusable plastic products, such as refillable water bottles, come from injection molds.
For engineered parts with tight tolerances, testing requirements, and an intention for functional use, hard tooling is most certainly the best option. The upfront cost is the most expensive, and the lead time will be the longest with this option; however, it will likely save both time and money down the road.
If you have any medical devices at home, such as heart-rate monitors, blood-pressure monitors, or even syringes, the odds are high that they came from injection molds. For a home, the injection molding machine can mean the difference between affordable medical devices that meet strict requirements versus expensive products that only businesses can afford.
Hard tooling will guarantee the ability to use production-intent resin and can accommodate design and dimensional changes after the parts have been sampled. Hard tooling also provides the opportunity for process development and verification early in the program timeline. Not only will this yield the best parts for testing and development, it will shorten the production approval process (typically when timing is the most critical). Hard tooling can also offer the opportunity to supply several hundred thousand parts, bridging the gap from prototype to production.
At Reliant Plastics, a Texas-based injection molding provider, we have decades of industry experience and cutting-edge equipment available to use for your next production run. Please consult with our team on designing, fabricating, and running the molds that will supply the products for your next major business push. Contact us to learn more and get a free quote today.
It is incredibly easy to find items around the home that are, in fact, injection-molded products. Many manufacturers prefer the injection molding production method for a few key reasons. Across large commercial manufacturing runs, injection molding offers several significant advantages, such as:
All those lids for those plastic bottles? Yes, they also come from injection molds. Since these items tend to be small, it is easy to design mold tooling to produce enormous quantities at once. With the high demand for plastic lids and caps across many industry verticals, it should be no surprise that the rapid throughput of molding machines is the manufacturing method of choice.
When it comes to prototyping, understanding what you need is important when considering what option to pursue. If you have a tight-tolerance part that is critical to the function of your system, cutting corners and costs in the development stage may not always save money over the long term. Be sure you are not just looking at cost or lead time when considering prototyping options, as there are many more factors involved.
With such a versatile process available to manufacturers, it’s no surprise these products are found everywhere. Injection molding products have only gotten more popular in recent years.
From the hangers in your wardrobe to the plastic frames of some mirrors or plastics used to house makeup, injection molds have a footprint everywhere. Since quick turnarounds and big orders are a key requirement for these industries, injection molds are the obvious best way to get it done.
Soft tooling is a very common method in the injection molding industry and provides relatively inexpensive tooling, a high number of parts, and may also allow for use of the intended production material. Soft tooling is usually built with aluminum cores and cavities.
SLS is similar to SLA except that it utilizes a carbon-dioxide laser to fuse together thin layers of powdered metal, plastic, glass, or ceramic to construct a solid product. An advantage of SLS over SLA is that it can make prototypes from a greater variety of materials that may have properties closer to production-intent materials.
So what are some of the most common injection molded objects often found in households? The average homeowner can easily find just about every single one of the following objects in their homes. Let’s consider what’s made by plastic injection molding and why.
Stereolithography (SLA) and selective laser sintering (SLS) are additive manufacturing technologies that are ideal for rapid prototyping. In SLA, an ultraviolet laser builds a solid part from a CAD pattern by solidifying and curing individual layers of a photopolymer resin. Although SLA is relatively fast, there are some size limitations, and photo-curable resins can be expensive. SLA parts can also be “dressed up” easily with paint or dye for trade shows or presentations.
To learn more about the importance of qualifying a tool in the overall scientific molding process, download our free infographic, The Process of Scientifically Qualifying a Tool.
Both processes are good for fitment exercises or early proof of concepts. Even though material options have increased over the years, SLA and SLS are still not production intent. The processes also have limitations from a functional standpoint, especially compared to higher-grade engineered resins. SLS and SLA are geared toward very low quantities but can also provide very quick turnarounds.
Have you ever wondered where the various objects in your house come from? We’re not talking about the shop or even the country of origin, but rather how these objects were made before eventually arriving in your home.With so many manufacturing methods around, you might not know that most of these products come from the design and manufacturing process for injection molded plastics. You likely have hundreds of different objects in your home created with this technique, but to emphasize how common these items are, we’ve put together a list of everyday injection molded parts.
GETTING A QUOTE WITH LK-MOULD IS FREE AND SIMPLE.
FIND MORE OF OUR SERVICES:
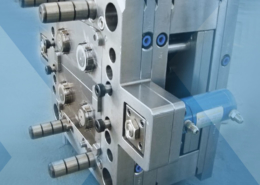
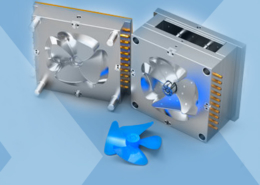
Plastic Molding

Rapid Prototyping
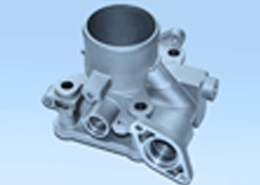
Pressure Die Casting
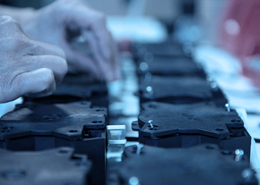
Parts Assembly
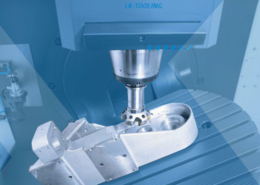