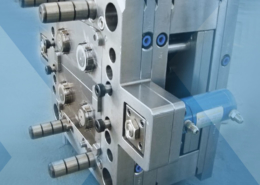
Custom Injection Molding | Sonoco Products Company - custom injection molding co
Author:gly Date: 2024-10-15
Unfortunately, PTFE cannot be injected because it has a high viscosity when in a liquid state, i.e. this material will not slide on a surface when in a liquid state. This problem is one of the major drawbacks of PTFE, especially when it comes to large volumes. Under these conditions, manufacturers are turning to other fluorinated polymers that can be injected.
Polytetrafluoroethylene can therefore only be transformed by cold compression molding (sintering) or extrusion. These processes result in excellent quality products but the processing costs are higher.
Due to their obvious properties, polymer materials called PPS or polyphenylene sulfides are frequently used in the manufacture of... read more
SPN specializes in fluorinated polymers and produces molded or extruded PTFE components for all types of industrial applications operating in severe and critical environments.
ETFE, also known as ethylene tetrafluoroethylene, is a material widely used in the chemical industry, architecture and construction. It... read more
Demgy SPN, Société des Plastiques Nobles 75-79 rue Rateau – ZI URBAPARC 4 – Bat. 5 93120 LA COURNEUVE Phone: +33(0) 1 48 45 49 79 commerciale.spn@demgy.com
Tefzel™ is a brand of ETFE or ethylene tetrafluoroethylene resins produced by Dupont. This material is also known under... read more
We provide one stop shop precision plastic solution from pre-manufacturing, development to post process for finishing goods.
PTFE has several outstanding properties at an affordable material cost. For example, it has good chemical resistance to acids, bases, alcohols, ketones and hydrocarbons. This material is also chemically inert and flame retardant. It is one of the least adhesive thermoplastics and is used in kitchen utensils such as cooking pans. It resists efficiently to UV rays and is non-toxic. Its coefficient of friction is particularly low, which allows it to be used for glide pads. PTFE is used in the manufacture of various industrial parts such as plumbing pipes or gun ball casings. In the industrial sector, this polymer is used to manufacture seals, bearings, electrical insulation parts and kitchen utensil coatings.
Voltalef® 302, also known as PCTFE, belongs to the family of fluoropolymers and is used in the manufacture of... read more
Among the commercial names of polyvinylidene fluoride or PVDF, we distinguish Kynar®. It is the brand name of the... read more
We provide one stop shop precision plastic solution from pre-manufacturing, development to post process for finishing goods.
For more than 80 years, SPN has been developing innovative products from high-performance polymers. Among a dozen materials processed,... read more
We are amongst the leading plastic parts manufacturing and customized injection molding in Malaysia, and always persist in:
Most plastic components are produced by injection molding. This production process allows the component manufacturer to produce complex geometries at low unit cost. Polymer injection molding is the most widely used production process for plastic components.
Center Console Panel, Climate Control Device, Snow Chain Anti-Skid, Key Button, Interior Decorative Panel, Cyclist Headlight.
A technically know-how in polymer processing parameter setting and monitoring parts finishing with value added enhancement processes.
We are always working hard not only to develop quality products and services, but also constantly striving to improve our various operational standards. Quality and customer satisfaction are our top priorities.
At SPN, we process and machine many high performance plastic materials. One of these materials is polyvinylidene fluoride, more... read more
In cryogenic environments, PTFE (polytetrafluoroethylene) and PCTFE (polychlorotrifluoroethylene) are the most commonly used fluoropolymers. Fluoropolymers are polymers where the... read more
Information on the PCTFE molding at SPN SPN performs PCTFE molding operations for the production of blanks, semi-products (plates, tubes,... read more
Our team of motivated and competent employees are fully committed towards our company’s mission of “Continuous Improvement in Challenging Customers’ Satisfaction”.
We provide one stop shop precision plastic solution from pre-manufacturing, development to post process for finishing goods.
GETTING A QUOTE WITH LK-MOULD IS FREE AND SIMPLE.
FIND MORE OF OUR SERVICES:
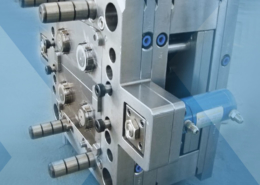
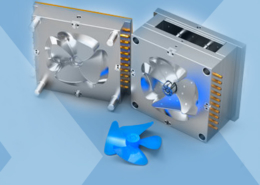
Plastic Molding

Rapid Prototyping
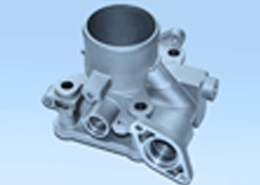
Pressure Die Casting
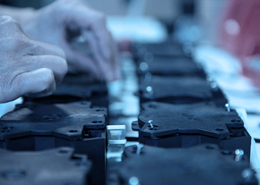
Parts Assembly
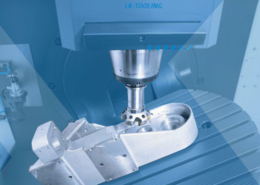