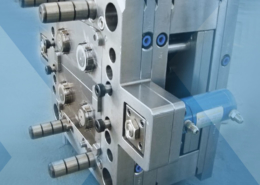
Custom Injection Molding - custom plastic molding
Author:gly Date: 2024-10-15
First Shot: The first material is injected into the mold in the top set of cavitites to form the first / inner component of the part and partially filling the mold cavity.
Enhanced Design Options: Different materials can be used for different functions or aesthetics within the same part, enabling improved design flexibility and functionality.
HiTech Plastics and Molds offers decades of experience in custom plastic injection molding including 2-shot injection molding, and has produced millions of parts using this 2-shot injection molding method. Currently, HiTech has open capacity on the 2-shot injection molding presses listed below.
2-Shot injection molding allows for two different plastic materials to be molded together sequentially in a single cycle without removing the part from the mold between shots as would be done in an overmolding process. This allows parts that consist of 2 seperate materials to be produced much more quickly than other methods.
Plastic Mold Manufacturing Plastic Injection MoldingRapid PrototypingCNC MachiningSheet Metal StampingPressure Die CastingSilicone & Rubber PartsSurface Finishing
In urethane casting, soft tooling diverges from the use of aluminum. Instead, it is fashioned from materials like silicone, carbon fiber, or fiberglass. The soft tooling process commences with the creation of a master pattern, which can be milled, machined, or 3D printed. This master pattern, essentially a replica of the final part, is employed to generate molds for production. In urethane casting, soft tooling is deployed in a manual, pour-and-cure method, in contrast to the machine-based manufacturing approach used for soft tooling in injection molding.
While not the only method for producing parts, injection molding can help shorten time-to-market while enhancing designs and keeping expenses under control. Compared to urethane casting, plastic injection molding gives designers a greater selection of materials and the ability to produce larger quantities.
In the context of plastic injection molding, soft tooling typically refers to molds that incorporate aluminum cores and cavities, as opposed to those made from steel. Aluminum is a softer material than steel and cannot be hardened to the same extent as steel. Some aluminum molds may include inserts crafted from lower-grade, pre-hardened steels. It’s important to note that while 3D printing can be utilized to create elements of soft molds such as cavities, the overall mold structure still relies on a metal frame.
This article will talk about the specific tooling choices that affect material selection, costs, quantities, and quality.
Given the variety of steel tooling options, it’s essential for designers to make a thorough comparison between hard tooling and soft tooling. In applications like medical injection molding, cost-effective and rapidly machinable steels find utility in pilot prototypes and low-volume production. Conversely, for scenarios involving higher-volume production, the preference often leans towards the use of hardened steel molds. Notably, H13 and S136 steels, although pricier in comparison to P20 and NAK80 steels, offer extended tooling lifespans. In the realm of hard tooling, regardless of the steel grade selected, durability remains a consistent advantage. Steel molds also possess the potential for refurbishment and modification.
Cost and Time Savings: Combining two shots into a single production cycle eliminates the need for secondary operations and assembly steps, reducing costs and production time.
We offer the tools, expertise, and manufacturing network to ensure the success of your next project, regardless of where you are in the design process. Please get in touch with us to find out more about our services, which include 3D printing, urethane casting, CNC machining, injection molding, and prototyping.
Durability is a significant consideration. Soft molds used in urethane casting can typically withstand approximately 25 shots per cavity. These molds are more straightforward to create and are more cost-effective than aluminum injection molds. However, it’s essential to note that prototype molds cannot produce as many parts and do not offer the same level of precision or complexity as metal molds.
It is essential to comprehend the distinctions in injection molding between hard and soft tooling, as well as between urethane casting and injection molding. Every kind of tool has advantages and disadvantages, and having a variety of mold materials is beneficial.
In the realm of injection molds, hardened steels are exemplified by H13 and S136. H13 steel is commonly employed for high-volume production, offering a tooling life spanning from 500,000 to 1 million shots. It proves to be a sound choice for molding materials like glass-filled nylon and can achieve tighter tolerances than aluminum molds. On the other hand, S136, a stainless steel variant, boasts a typical tooling lifespan exceeding 1 million shots. It possesses resistance to corrosive substances found in materials like PVC or POM and is exceptionally adept at achieving a high level of polishing, enabling the creation of parts with exceptional optical clarity.
Nonetheless, soft tooling employed in both molding processes can support activities like prototyping, bridge production, and low-volume manufacturing. In urethane casting, production volumes are generally lower, typically ranging from 1 to 100 units, and it’s important to be aware that designers cannot create parts or prototypes using the end-use plastic material.
One key advantage of using aluminum injection molds is their cost-effectiveness and shorter production lead times. While steel molds can be competitively priced, it’s worth noting that Fictiv can provide them relatively quickly. However, considerations extend beyond speed and cost.
In urethane casting, the relationship between soft tooling and material selection is less critical because the molding process primarily accommodates castable polyurethanes, additives, and curatives.
Hard tooling in the context of plastic injection molding is crafted from steel, an alloy composed primarily of iron and carbon, with trace amounts of other elements. Steel is notably harder than aluminum, and heat-treated steel further enhances its hardness, rendering it exceptionally durable and resistant to wear. While most P20 steel is not heat-treated, it is still considerably tougher than aluminum and boasts a tooling lifespan that is five to ten times longer. NAK80, categorized as a semi-hardened tool steel, surpasses this durability and is known for its exceptional polishing capabilities, making it ideal for the production of optically clear parts.
Second Shot: Next, the mold remains closed and rotates 180 degrees so the top set of cavities is now at the bottom. Then, a second material is injected over and bonds with the first shot to form the out component of the part. While the second component is formed in the bottom set of cavities, material is shot into the top set of cavities to form the inner component of the part. This is an efficient way to utilize cycle time as parts are being prepared for ejection and for the second shot simultaneously.
Improved Part Quality: The bond between the two materials enhances part strength, eliminates the risk of delamination, and provides a seamless transition between the materials.
Aluminum molds are limited in their ability to endure a high number of injection molding cycles and are less accommodating to mold modifications. The softness of aluminum may lead to deformation under the high clamping pressures associated with injection molding, potentially causing surface defects known as “flash.” Furthermore, aluminum molds cannot achieve the same level of precision and tight tolerances as steel molds.
Plastic injection molding uses both soft and hard tooling; urethane casting is a different production process that also uses soft tooling. These various interpretations of the term “soft tooling” might be perplexing for product designers. Of course, adjectives like “hard” and “soft” are relative because the metal tooling used in injection molding can be classified as either hard or soft based on the kind and quality of the metal.
Aluminum injection molds are not suitable for abrasive materials like glass-filled nylon due to their limited wear resistance. Additionally, plastics that require elevated temperatures, such as PEI and PEEK, may not mold effectively in aluminum molds due to difficulties in maintaining the required temperature. Corrosive plastics like PVC or POM can also pose problems, as they can degrade the aluminum material itself.
Cooling and Ejection: The mold is cooled to solidify the combined materials, and then the part is ejected from the mold.
GETTING A QUOTE WITH LK-MOULD IS FREE AND SIMPLE.
FIND MORE OF OUR SERVICES:
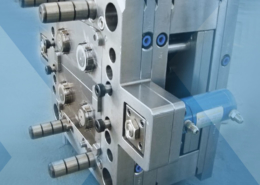
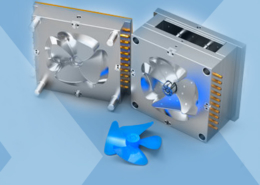
Plastic Molding

Rapid Prototyping
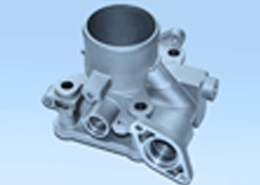
Pressure Die Casting
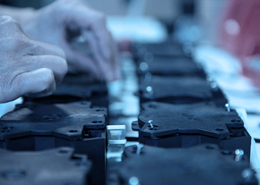
Parts Assembly
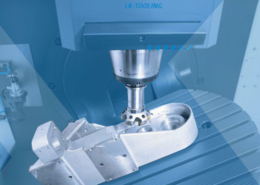