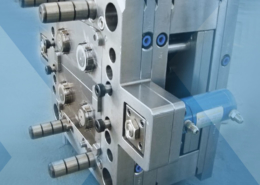
Custom ABS Injection Molds - abs plastic molding manufacturers
Author:gly Date: 2024-10-15
The possible objects we can obtain have the shape of the model, are light (float over the water) but dimensions are not precise and I don't think the obtained object can stand a big mechanical constraint
Our services include: Plastic Injection Moulding; Tool Design & Making; Custom Moulding; Plastic Product Assembly; Plastic Product Testing; Plastic Part Finishing and Plastic Part Packaging.
In fact, if the evaporation surface is small, and if the object is thick, the acetone may not be completely evaporated, and the molded object may still be soft. In this case, let the molded part into the mold and let it dry for a few more days at room temperature. In my case, my robot was 30mm thick. After one week, it was still soft. It needed 10 days for drying.
When you have the required volume of polystyrene paste (step 2) , put this paste in the mold, put a weight on it and let it dry for several days.
Then break the plaster with a screwdriver in order to extract the molded part (the robot, in my case) . The mold will be lost.
Contact us today for more information about how we can help your business. We offer free, no-obligation quotes and can discuss the best possible solution for your project.
Plaster of Paris filled in a plastic box+ WD40 + screw driver , needle, sand paper, files (in order to dig and smooth the edges of the mold)
This is the start point of this instructable : I wanted to investigate this process , realize an object, and evaluate the positive and negative points.
Polystyrene foam may be dissolved in a mix acetone (20%) + unleaded petrol (80%). In this case, the mix is liquid (Depends on the quantity of dissolved polystyrene) , and it can be reused as glue.
First of all, the molded object is shorter than the original: it measures now 77mm x 53mm x29mm whereas the model was 80mm x 55mm x 30mm
Of course, it is possible to use any other object in wood, plastic or metal or silicone or chocolate as a model.... but don't forget one thing: you have to think that this object will later be plounged in the plaster, and then it must be unmold without breaking the mold when the plaster is dry !
In a bowl or a metal can, pour a few tablespoons of acetone, and put polystyrene in it. The polystyrene will dissolve and form a white, opaque paste. DO NOT BREATHE the vapors. Add as much acetone and polystyrene as you need to get the required volume of your object.
Then, the result remains quite rough, the sides are not perfectly straight, my robot's belly swelled up, and I saw air bubbles inside the material.
At Anchor Plastics, all of our products are always assembled and packaged to the highest standards and are thoroughly tested before they are packed and sent to our customers.
Do you have plastic injection needs?Well, you’re in the right place. Plastic injection moulding and tool making and design are just some of the services that we offer.
I choosed to make a plaster mold . There are a lot of instructables showing this process. The mold will be used once only.
We offer the complete package, from tool making and design to custom moulding. We use the latest technology and have highly skilled personnel who are dedicated to producing quality products that meet customer needs.
Caution: Do not put the assembly ( mold + molded part) in your kitchen oven at 80°C in order to accelerate evaporation because of the toxic fumes of acetone.
I filed the sides in order to smooth the polystyrene of my model. The smoother the model in polystyrene is, the finest will be the result. In my case, I did not shaped the eyes and the printer of my robot. I was right: It is really easier to dig holes later in the plaster in order to get later the salients parts of the model.
The process is cold. It means that the mold may be in in wood, or concrete, or (silicone in soap), or chocolate if you want, but not any plastic wich may be dissolved with acetone (ABS plastic for example) .
Design and manufacturing of tools is an important part of many industries. By creating the perfect tool, companies can improve their production efficiency and output.
First of all, remember : the moded object you'll get at the end will never be better than the mold. Be watchful and careful.
Clean the object with a toothbrush, a metallic wire brush, a cutter, a file, screwdriver, a sandpaper, a sausage, a dream catcher, whatever you want.
My vercict is : if you are not in hurry (it last some days) , molding polystyrene with this cold process is possible, but please...don't expect miracles!
Go outside or open the window. The acetone is toxic and very bad for lungs . Don't breathe it. Never..... Unless you want holes in your lungs
When it comes to moulding, we are dedicated to providing our clients with excellent service, high quality products, and low overall costs.
I roughly shaped the robot in polystyrene, with a hot wire device (there are a lot of instructables on this subject) , because this method is easy and quick to do.
At Anchor Plastics, we understand the importance of attention to detail and focus on delivering quality products that meet customer requirements. Our commitment is to provide you with the best service and the highest quality plastic injection moulding solutions.
Smooth the edges in the mold and finish the details: Dig the details missing in the female mold ( in my case, the eyes, the buttons, and the printer of my robot) with a screw driver, a needle, a chisel point, etc.... Remember that the holes you do in the mold will be turned in relief when you will pour the liquid polystyrene paste.
Plastic injection moulding is the process in which molten plastic is injected into and aluminium, steel, or ceramic mould, which is shaped like the end product is meant to turn out. High pressure is then used to squeeze the mould until the object is solid.
But I think it is surely possible to make Ears rings , toys , keyrings or decoration objects for examples . Please post me your realizations!
When the plaster is dry, put the mold + model in an oven at 80°C during several hours. Don't do that in the oven you cook because of the possible remaining toxic fumes. The polystyrene model will reduce. It will be easy to push it out.
GETTING A QUOTE WITH LK-MOULD IS FREE AND SIMPLE.
FIND MORE OF OUR SERVICES:
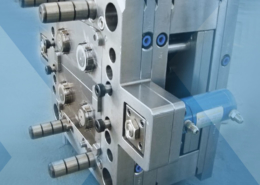
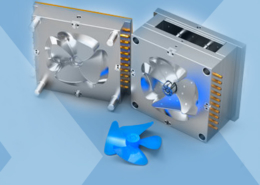
Plastic Molding

Rapid Prototyping
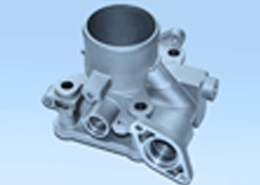
Pressure Die Casting
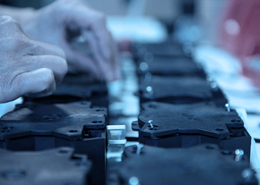
Parts Assembly
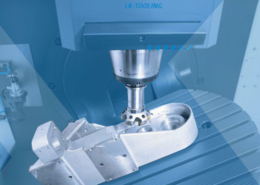