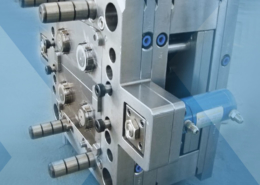
Custom ABS Injection Molds - abs plastic molding manufacturers
Author:gly Date: 2024-10-15
Overmolding, the process of molding one material over a substrate made from another material, is a highly useful form of multi-material plastic injection molding. By combining soft and hard materials, overmolding makes it possible to make durable tools with soft hand grips, industrial components with built-in seals, and parts with high-friction surfaces.
The vast majority of beauty packaging solutions are made of some kind of plastic. PET is a popular material, being recyclable, flexible and compatible with many kinds of formulations. Injection moulding allows it to be shaped into jars, rigid bottles and a host of other pack types. Here, we explain the process, its advantages and its challenges.
How is it different from blow moulding?Blow moulding is used to make thin-walled products like water bottles, for example. Injection moulding allows greater wall thicknesses, to create products with a luxurious look and feel.
The overmolding process differs from two-shot injection molding, another type of multi-material molding, in that two separate molds are used: one to form the substrate and another to form the overmold. It therefore requires more manual intervention than two-shot injection molding but can be used with cheaper equipment.
Originally, PET was mainly used in blow moulding to produce thin-walled products. Thick-walled products require injection moulding, however, and the process is more complex. The material properties have to be in perfect sync with the mould shape and design, as well as the injection moulding machine.
Nylon is a useful molding plastic due to its chemical resistance, strength, and many different varieties. Nylons like PA6, PA11, and PA12 can make good overmolding substrates for a variety of overmolded parts. Such materials can bond with various TPU varieties and also work well with a liquid silicone rubber (LSR) overmold.
The vast majority of beauty packaging solutions are made of some kind of plastic. PET is a popular material, being recyclable, flexible and compatible with many kinds of formulations. Injection moulding allows it to be shaped into jars, rigid bottles and a host of other pack types. Here, we explain the process, its advantages and its challenges.
Quadpack is a global cosmetics packaging manufacturer and provider for beauty brands. With offices and production facilities in Europe, the US and the Asia Pacific region, and a strategic network of partners, Quadpack develops sustainable and innovative packaging for skincare, make-up and fragrance customers. With extensive manufacturing expertise in airless bottles, cosmetics jars, wooden packaging and decoration, Quadpack is proud to offer complete solutions to help beauty brands perform.
3ERP has years of experience creating injection molded parts for a range of customers. We can fulfill injection molding orders of all sizes, from 100 prototypes to full production of millions of units. We also offer a reliable overmolding and insert molding service for multi-material parts. Contact us for a free quote.
ABS, highly impact-resistant and commonly used in injection molding for parts like handheld devices, is one of the best rigid thermoplastics for overmolding due to its high level of compatibility with both rigid and soft materials. When used as a substrate, it can bond well with flexible materials like TPU, TPE, and PVC, as well as other rigid materials like PC, nylon, and polystyrene.
PET is very sensitive to water and must be meticulously dried before production. It is also sensitive to high temperatures, so it is critical to adhere to the established pressures, times and temperatures, to avoid quality defects like brittleness, dullness, burns, flashes and dimensional deviations.Originally, PET was mainly used in blow moulding to produce thin-walled products. Thick-walled products require injection moulding, however, and the process is more complex. The material properties have to be in perfect sync with the mould shape and design, as well as the injection moulding machine.Is injecting rPET the same as virgin PET?More or less, but it is important to align the processes to the material’s properties. Compared to virgin PET, recycled PET (or rPET or PCR PET) has its own characteristics: the melt flow rate is different and, being reused, its appearance is inevitably affected by impurities. It is possible to use a percentage of rPET – anywhere from 5% to 100%, depending on the shape and aesthetics required. In any case, rPET must always be tested with the formula, especially when dealing with a mix.
A key advantage of overmolding is the chemical bond that can be formed between two compatible materials. By using an overmolding material that is chemically compatible with the substrate material, a strong bond will form at the the adjoining surfaces, eliminating the need for adhesives or fasteners and creating a strong, permanent bond.
What colours can a PET pack be?With virgin PET, all kinds of colours are possible. Limitations only exist with certain special colour batches, where additive separation can be visible. Colour choices depend on the purity of the material used, so they are far more restricted with rPET.
This article serves as a quick guide to overmolding material compatibility, looking at which hard materials pair well with which soft materials and vice versa.
Although PET injection moulding sounds simple and straightforward, the process involves a host of parameters. Material dryness, melt temperature, mould temperature, pressures, ventilation and injection speed must all be configured with the right values, set at the right times, to achieve perfect results.
Polypropylene is a widely used injection molding material for parts like living-hinge packaging lids due to its flexibility, impact resistance, and low cost. It is compatible with a wide range of soft overmold materials, including TPU, TPE, and TPV.
PMMA or acrylic is another versatile transparent plastic for injection molding due to its scratch resistance and optical clarity. When used as a substrate material, it can chemically bond with certain TPUs. PMMA also bonds well with ABS, which may be useful when making a partially opaque, partially transparent part.
Chemical compatibility is about more than just creating a strong bond, however. In some cases, attempting to use two incompatible materials within a mold can cause the release of toxic fumes, a dangerous buildup of pressure, or an explosion.
Polyethylene terephthalate (PET) is also known as thermoplastic polyester. It is an excellent packaging material, allowing a great deal of creative design when expertly injected.
Strong, dimensionally stable, and very resistant to impact, PC is a popular injection molding material for transparent or opaque parts like lenses and medical devices. When combined with a soft TPU overmold material, it can also be a useful substrate for overmolding. PC can also chemically bond with several hard plastics like ABS, PET, and PEI.
So which overmold materials can be used with which substrate materials? This depends on a few factors, including the type of part being made and the type of bond required between the two materials.
Overmolding is one of the most efficient molding processes for creating multi-material injection molded parts. Instead of assembling two or more components together — adding time and cost to production of the part — overmolding adds a second molding material directly over a molded substrate.
Blow moulding is used to make thin-walled products like water bottles, for example. Injection moulding allows greater wall thicknesses, to create products with a luxurious look and feel.
Creating packaging solutions through PET injection moulding is an industrial precision craftThe vast majority of beauty packaging solutions are made of some kind of plastic. PET is a popular material, being recyclable, flexible and compatible with many kinds of formulations. Injection moulding allows it to be shaped into jars, rigid bottles and a host of other pack types. Here, we explain the process, its advantages and its challenges.First of all, what is PET?Polyethylene terephthalate (PET) is also known as thermoplastic polyester. It is an excellent packaging material, allowing a great deal of creative design when expertly injected.How does PET injection moulding work?Injection moulding allows PET to be shaped into rigid packaging formats. PET initially comes in small pellet form. During the injection moulding process, the pellets are heated in the machine and the molten material is injected into a mould cavity, which then cools and solidifies to form the desired product.How is it different from blow moulding?Blow moulding is used to make thin-walled products like water bottles, for example. Injection moulding allows greater wall thicknesses, to create products with a luxurious look and feel.What are the challenges in PET injection?Although PET injection moulding sounds simple and straightforward, the process involves a host of parameters. Material dryness, melt temperature, mould temperature, pressures, ventilation and injection speed must all be configured with the right values, set at the right times, to achieve perfect results.PET is very sensitive to water and must be meticulously dried before production. It is also sensitive to high temperatures, so it is critical to adhere to the established pressures, times and temperatures, to avoid quality defects like brittleness, dullness, burns, flashes and dimensional deviations.Originally, PET was mainly used in blow moulding to produce thin-walled products. Thick-walled products require injection moulding, however, and the process is more complex. The material properties have to be in perfect sync with the mould shape and design, as well as the injection moulding machine.Is injecting rPET the same as virgin PET?More or less, but it is important to align the processes to the material’s properties. Compared to virgin PET, recycled PET (or rPET or PCR PET) has its own characteristics: the melt flow rate is different and, being reused, its appearance is inevitably affected by impurities. It is possible to use a percentage of rPET – anywhere from 5% to 100%, depending on the shape and aesthetics required. In any case, rPET must always be tested with the formula, especially when dealing with a mix.What colours can a PET pack be?With virgin PET, all kinds of colours are possible. Limitations only exist with certain special colour batches, where additive separation can be visible. Colour choices depend on the purity of the material used, so they are far more restricted with rPET.How can brands choose between recycled and virgin PET for their packaging?The choice depends on the level of sustainability and quality they require, as well as time and volume. rPET has a lower environmental impact, but has restrictions in terms of lead times and aesthetics. Brands may choose to embrace rPET’s ‘imperfections’ to visually send a message on sustainability, although these can be mitigated with the right process parameters and decoration techniques.Volume is also a consideration. The final product quantities should ideally match the available material batch quantities, to avoid variations in the process parameters and the products’ final appearance. Consult our catalogue to see our full range of beauty packaging solutions in PET.
With virgin PET, all kinds of colours are possible. Limitations only exist with certain special colour batches, where additive separation can be visible. Colour choices depend on the purity of the material used, so they are far more restricted with rPET.
Volume is also a consideration. The final product quantities should ideally match the available material batch quantities, to avoid variations in the process parameters and the products’ final appearance.
What are the challenges in PET injection?Although PET injection moulding sounds simple and straightforward, the process involves a host of parameters. Material dryness, melt temperature, mould temperature, pressures, ventilation and injection speed must all be configured with the right values, set at the right times, to achieve perfect results.
It is also possible to carry out overmolding with two materials that do not chemically bond. However, in these instances, the part must be designed so the two components will join mechanically — for example, with undercuts that will physically lock the overmold material in place. This limits design freedom and creates a less secure bond.
However, before making parts with this process, it is vital to understand overmolding material compatibility. The best overmolded parts have a strong chemical bond between the substrate material and the overmolding material, but not all overmolding material combinations can produce such a bond. Furthermore, certain materials should never be combined within a single mold, as they can cause a dangerous chemical reaction.
Injection moulding allows PET to be shaped into rigid packaging formats. PET initially comes in small pellet form. During the injection moulding process, the pellets are heated in the machine and the molten material is injected into a mould cavity, which then cools and solidifies to form the desired product.
For all overmolded parts, it is important that the substrate material has a higher glass transition temperature than the overmolding material. Otherwise, the substrate material will deform or melt within the second mold as the hot overmold material is being injected onto, into, or around the substrate.
More or less, but it is important to align the processes to the material’s properties. Compared to virgin PET, recycled PET (or rPET or PCR PET) has its own characteristics: the melt flow rate is different and, being reused, its appearance is inevitably affected by impurities. It is possible to use a percentage of rPET – anywhere from 5% to 100%, depending on the shape and aesthetics required. In any case, rPET must always be tested with the formula, especially when dealing with a mix.
How can brands choose between recycled and virgin PET for their packaging?The choice depends on the level of sustainability and quality they require, as well as time and volume. rPET has a lower environmental impact, but has restrictions in terms of lead times and aesthetics. Brands may choose to embrace rPET’s ‘imperfections’ to visually send a message on sustainability, although these can be mitigated with the right process parameters and decoration techniques.
Some injection molding materials do not bond well with other plastics and are therefore only suitable for mechanical bonding, not chemical bonding.
How does PET injection moulding work?Injection moulding allows PET to be shaped into rigid packaging formats. PET initially comes in small pellet form. During the injection moulding process, the pellets are heated in the machine and the molten material is injected into a mould cavity, which then cools and solidifies to form the desired product.
In some cases, combining materials can be dangerous. POM, for example, should never be overmolded with materials PVC or TPV, as the chemical reaction created can cause the release of deadly hydrochloric acid and an explosion.
To create a chemical bond between the two materials, a chemically compatible overmold material must be chosen. Many rigid materials will bond well with certain types of thermoplastic polyurethane (TPU), while materials like ABS and PP are compatible with a wider range of soft overmold materials.
Specialize in CNC machining, 3D printing, urethane casting, rapid tooling, injection molding, metal casting, sheet metal and extrusion
First of all, what is PET?Polyethylene terephthalate (PET) is also known as thermoplastic polyester. It is an excellent packaging material, allowing a great deal of creative design when expertly injected.
The choice depends on the level of sustainability and quality they require, as well as time and volume. rPET has a lower environmental impact, but has restrictions in terms of lead times and aesthetics. Brands may choose to embrace rPET’s ‘imperfections’ to visually send a message on sustainability, although these can be mitigated with the right process parameters and decoration techniques.
Volume is also a consideration. The final product quantities should ideally match the available material batch quantities, to avoid variations in the process parameters and the products’ final appearance.
PET is very sensitive to water and must be meticulously dried before production. It is also sensitive to high temperatures, so it is critical to adhere to the established pressures, times and temperatures, to avoid quality defects like brittleness, dullness, burns, flashes and dimensional deviations.
Some injection molding plastic substrate materials do not chemically bond well to any soft overmold materials, and are better suited to other forms of assembly such as fasteners. Likewise, some flexible materials, particularly thermosets like liquid silicone rubber, are generally better suited to mechanical bonds than chemical ones.
GETTING A QUOTE WITH LK-MOULD IS FREE AND SIMPLE.
FIND MORE OF OUR SERVICES:
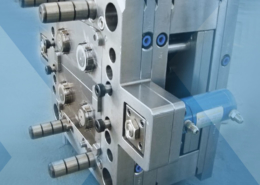
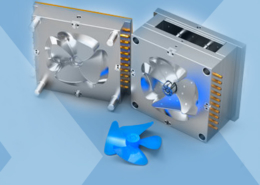
Plastic Molding

Rapid Prototyping
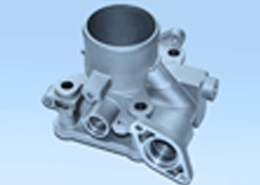
Pressure Die Casting
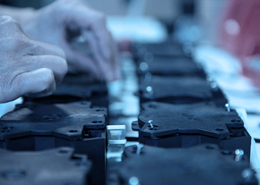
Parts Assembly
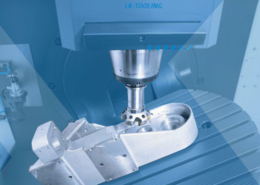