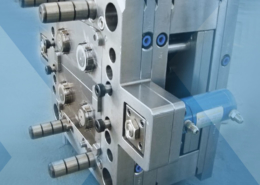
Exploring the Marvels of Molded Parts: A Comprehensive Overview
Author:gly Date: 2024-06-08
Molded parts serve as the backbone of modern manufacturing, encompassing a diverse array of components vital to industries ranging from automotive and aerospace to healthcare and consumer goods. From intricate geometries to high-performance materials, molded parts epitomize the convergence of precision engineering, innovative materials science, and advanced manufacturing technologies. In this comprehensive exploration, we delve into the multifaceted world of molded parts, unraveling their significance, applications, and impact on industries worldwide.
The Essence of Molded Parts
Molded parts represent a cornerstone of industrial production, embodying the seamless integration of design, engineering, and manufacturing principles. Through the process of injection molding, compression molding, or other specialized techniques, raw materials such as plastics, metals, and composites are transformed into precision-engineered components with unparalleled efficiency and accuracy. From automotive interior panels to medical devices and consumer electronics, molded parts permeate every aspect of modern life, driving innovation, functionality, and performance across diverse sectors.
Applications Across Industries
The versatility of molded parts transcends industry boundaries, catering to a myriad of applications with varying performance requirements and design complexities. In the automotive sector, molded parts play a pivotal role in vehicle interiors, exteriors, and under-the-hood components, offering lightweight, durable solutions that enhance fuel efficiency, safety, and aesthetics. Similarly, in the aerospace industry, molded composite components enable the construction of lightweight, high-strength structures critical to aircraft performance and efficiency.
Material Innovation and Performance
Advancements in materials science have revolutionized the capabilities and performance characteristics of molded parts, enabling manufacturers to meet the evolving demands of customers and markets. From engineering-grade thermoplastics to advanced composites and biodegradable polymers, the range of materials available for molding applications continues to expand, offering tailored solutions for specific performance requirements, such as strength, stiffness, heat resistance, and chemical compatibility.
Design Optimization and Efficiency
The design of molded parts plays a pivotal role in determining their functionality, manufacturability, and cost-effectiveness. By leveraging computer-aided design (CAD) software, finite element analysis (FEA), and mold flow simulation tools, engineers can optimize part geometries, wall thicknesses, and gating systems to minimize material usage, reduce cycle times, and enhance overall production efficiency. Moreover, the integration of features such as ribs, bosses, and snap fits facilitates assembly, reduces weight, and improves structural integrity, further enhancing the value proposition of molded parts.
Quality Assurance and Regulatory Compliance
Ensuring the quality and reliability of molded parts is paramount in industries where safety, performance, and regulatory compliance are non-negotiable. Rigorous quality control measures, including dimensional inspection, material testing, and functional validation, are integral to the manufacturing process, enabling manufacturers to meet stringent quality standards and customer specifications. Moreover, adherence to regulatory requirements, such as ISO certifications and industry-specific standards, instills confidence in the reliability and traceability of molded parts, fostering trust and credibility in the marketplace.
Economic Considerations and Market Dynamics
The economic viability of molded parts hinges on a complex interplay of factors, including material costs, production volumes, labor rates, and supply chain dynamics. While economies of scale and automation technologies can drive down unit costs for high-volume production runs, niche markets and specialized applications may necessitate higher upfront investments and customization costs. Furthermore, fluctuations in raw material prices, currency exchange rates, and geopolitical factors can impact the cost competitiveness and profitability of molded part manufacturing operations, underscoring the importance of strategic planning and risk management.
Conclusion: Pioneering the Future of Manufacturing
In conclusion, molded parts represent a testament to human ingenuity, technological innovation, and the relentless pursuit of excellence in manufacturing. From revolutionizing product design and functionality to enabling sustainable solutions and cost-effective production processes, molded parts continue to redefine the boundaries of what's possible across industries. As we embark on a journey towards a future characterized by smart manufacturing, digitalization, and sustainability, the role of molded parts will only continue to grow in significance, shaping the products, industries, and economies of tomorrow.
By embracing a holistic approach to design, materials selection, manufacturing processes, and quality assurance, stakeholders across the manufacturing ecosystem can unlock new opportunities for innovation, growth, and competitiveness. Moreover, by fostering collaboration, knowledge-sharing, and investment in research and development, we can pave the way for breakthroughs in materials science, manufacturing technologies, and product innovation, driving sustainable progress and prosperity for generations to come.
GETTING A QUOTE WITH LK-MOULD IS FREE AND SIMPLE.
FIND MORE OF OUR SERVICES:
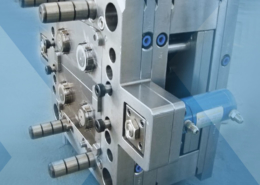
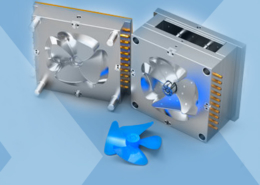
Plastic Molding

Rapid Prototyping
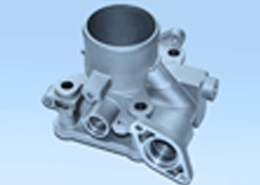
Pressure Die Casting
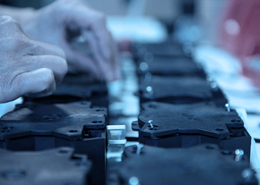
Parts Assembly
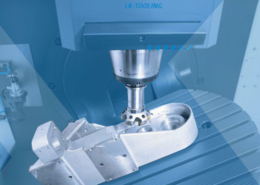