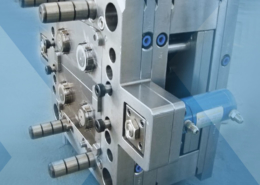
Copolyamide Promotes Bonding of Metal to Plastic In ... - overmolding metal with
Author:gly Date: 2024-10-15
Material costs and the level of production have a critical effect on the overall costs as well. Such elements are critical in effective cost management.
The larger the Part, the more materials are consumed, hence, the higher costs. Using correct size of injection molding machine and mold for these large parts is very essential.
For instance, minimizing power consumption such as using energy-efficient equipment or operational optimization will help minimize these costs.
ABS plastic injection molding has multiple benefits and applications. Since injection molding is so versatile, it is a preferred method for rapid part manufacturing. The main benefits include:
To reduce injection molding costs effectively, consider these streamlined strategies:Increase Production Volume: Distributing overhead set-up and mold costs over a larger number of units leads to reduced cost per piece, thus maximizing economies of scale for better performance.
The cost of mold manufacturing is dependent upon the material (steel or aluminum), size, and complexity. Complicated designs usually demand high skills, such as:
When it comes to plastic injection molding, the choice of material is a crucial factor that directly impacts the overall cost. The type of plastic you select will not only affect the upfront material expenses but also influence the durability, performance, and production efficiency of your final product.
In this guide, we’ll explore the key elements that influence plastic injection molding costs, helping you find the best balance between quality and cost-efficiency for your project.
Knowledge of these variables leads to effective analysis in the area of cost in plastic injection molding projects brought about by optimized design and production practices.
Low-volume injection molding usually entails making 100-1,000 parts. This kind of a production level is for the less complicated types of molds and for simpler machinery.
By choosing the most suitable material for your needs, you can enhance production efficiency and product performance, ensuring that your investment delivers long-term benefits.
This, therefore, makes high-volume production more economical for large numbers of units of a product, providing significant savings per Part. Here’s a breakdown of estimated costs for producing 100,000 to 300,000 units using ABS plastic:
This level of production uses advanced machines, which cost extra at first but drop the cost per Part significantly due to economies of scale.
Outsourcing injection molding is cheaper than buying equipment. This strategy eliminates the costs that are incurred in buying and maintaining machines.
In low-volume production, 3D-printed polymer resins or rapid tooling is often used by manufacturers, which is more cost-effective for shorter runs.
Undercut-like characteristics can make the process of molding complex. The best is to remove them if it’s feasible. If not, other methods are the use of slide shut-offs or modification of the parting line to ease mold construction.
Hi, I am Sparrow Xiang, COO of the HiTop company, me and my team would be happy to meet you and learn all about your business, requirements and expectations.
Electric machines use electro-servo motors to achieve accurate control. They are energy-saving with less operational costs. They are user-friendly. Nevertheless, they will need more upfront costs and also routine care.
The durability needed for high-volume production makes steel molds a cost-effective option, although their initial cost is higher. The costs also relate to the mold accuracy and finishing needs, where narrower tolerances contribute to increased costs.
Packaging is customized to the product, ranging from simple bulk boxes to elaborate structures that provide protection against damage during transportation. Packaging requirements vary depending on the fragility and size of the parts.
Plastic injection molding is a manufacturing process that injects melted plastic using high pressure into a pre-shaped mold to create products with particular specifications. Lerner Molded Plastics provides injection molding design services for ABS injection molding projects. We have over 35 years of experience designing injection molds and a cutting-edge injection molding facility. Here you can learn more about ABS injection molding and its benefits, applications, and considerations.
This level usually goes for injection mold and molding process outsourcing. Below is an estimated cost breakdown for a production volume of 5,000 to 10,000 units using thermoplastic materials like polypropylene:
This discussion on plastic injection molding cost aims to examine the key factors that determine the price and efficiency of the production. Key points include the material, size, and complexity that affect mold manufacturing costs and the equivalent costs of equipment types by machine type.
Processes like ultrasonic welding, heat staking, and painting or texturing are used. These processes enhance not only the aesthetic but also the functional properties of the parts.
Lerner Molded Plastics is an ISO-certified plastic molding manufacturer that can create high-quality design and tooling solutions for your project. Our custom and offshore injection molding capabilities enable us to meet small, intricate, multi-cavity, or large component specifications. We aim to ensure repeatable, reliable solutions for your applications, and we meet this challenge by adhering to the strictest industry standards.
The cost of plastic injection molding depends on several factors, including the complexity of the part, the number of cavities in the mold, the type of material used, and the production volume.
HiTop Industrial leads as a manufacturer of molds and supplier of injection molding services. Their skill guarantees customized, high-quality production. For any questions or more details, please feel free to contact HiTop Industrial.
We are committed to helping you elevate quality standards, fostering enterprise growth, and actualizing your internationalization strategy.
Mid-volume injection molding is used to produce 5000-10000 parts. This scale typically demands pre-hardened steel or aluminum molds.
For simple molds, costs can range from $1,000 to $5,000. More complex molds, especially those with multiple cavities or intricate designs, can cost between $25,000 and $75,000 or more.
Some complicated parts require the intricate molds and this is done through the use of advanced tools such as 3D printing, CNC or EDM machining. These complex molds get more material, and as a result, the costs are increased.
Hydraulic machines work with a help of a hydraulic pump. They are characterized by strength and reliable functioning. These systems are cheaper in the first instance while having a higher power consumption and a less accurate performance.
Sharp edges can inhibit the use of circular cutters to necessitate further EDM. This secondary operation is important for small features. Thin ribs more than 0.5″ (or thinner than .0625″) also require EDM.
Techniques such as laser marking and pad printing are employed for adding intricate designs or instructions to the parts and are important for functionality and compliance in industries such as medical and aerospace.
The tooling cost in injection molding depends most on part complexity. Parts that have sharp corners, thin ribs, or undercuts require more expensive tooling.
In the UK, the cost of injection molding is influenced by factors similar to those in other regions. The price per part can range from £1 to £5 for small to medium production volumes.
Inclusion of non-essential features like textures or high polish raises costs. These often need more cavities in the mold demand, thus pushing costs higher. Focus on the essentials to manage the costs well.
These additional costs are crucial for guaranteeing that the parts meet the required standards and have been prepared for the market or for further assembly. It is much more beneficial to use simple post-molding operations in some cases as it will help to control these costs efficiently.
These approaches ensure that there is no wastage and increase the efficiency of the processes of production processes, thus enable the manufacturers achieve quality with a lower cost.
Up to 90% of costs at injection molding facilities are due to energy usage, which represents a substantial part of the total operational expenses. This will result in significant cost savings.
This volume is suitable for the products that need a balance of cost efficiency and volume, and is the best for the larger batches of standardized products.
In the process of molding, post-operations can substantially increase the general cost of the project. These are assembly, finishing, and packaging, which are adapted to improve the product’s functionality and appearance.
Undercuts make the matter complicated which requires more time for design and machining. Most of the times, such features are not possible to be incorporated due to the complex side actions, larger molds are needed. All of these factors substantially increase the tooling cost at the beginning.
The completion of the entire production cycle for such quantities takes approximately three days and therefore, this method is rather effective in prototype and small batch requirements.
High-performance plastics, though initially more expensive, can reduce maintenance and replacement costs over time, providing better value in applications where durability is essential.
Installation of the injection molding machines needs accurate configurations by each production run. Preparing molds is precise work that requires time and a lot of skill.
All these three factors including set-up, repair, and operator costs are important in the total cost of producing injection molded parts. The effective management and qualified labor help to reduce these costs that come with keeping the high production standards.
General up-keep of worn parts and routine maintenance is essential for avoiding down-time and efficient operation. Therefore, such preventive maintenance addresses the issue of bigger and more expensive repairs later.
Injection molding requires multiple types of mechanical parts, which can either wear out or break, requiring frequent maintenance and some repairs once in a while. The costs are critical in making sure the operation is ongoing.
HITOP is committed to assisting customers by offering a comprehensive one-stop solution, encompassing product design enhancement, initial sample creation, mold fabrication, injection molding, and product assembly.
Polyethylene (PE) and polypropylene (PP) are among the cheapest plastics used for injection molding. They are widely available, cost-effective, and suitable for a variety of applications.
The total cost depends on factors like mold complexity, production volume, and material choice. Whether you’re producing 100 parts or 100,000, understanding these costs upfront can help you budget effectively and make informed decisions.
In ABS injection molding, ABS plastic pellets are melted and injected into the cavity of a two-part mold that forms a single part. As soon as the mold is filled, the plastic will solidify and cool into the shape of the mold.
Even with the fact that injection molding machines are automated, operators are still needed. They control the production process to make sure that everything goes fine, adding to labor costs.
Hybrid machines are a combination of electric and hydraulic technologies. They utilize servo motors and hydraulic pumps, thus, providing high accuracy and power savings.
The proper choice of an injection molding machine type is important to ensure the balance between cost and performance. Each kind has its own specific benefits and costs, which affect the general effectiveness of production.
Plastic injection molding costs can vary widely, typically ranging from $100 for simple 3D-printed molds to over $100,000 for complex steel molds used in high-volume production.
To prevent part defects, consider the mold shrinkage (0.004 to 0.007 inches) and water absorption (0.16% to 0.25%) of ABS. These properties affect curing and processing. Other properties to consider when ABS molding are:
The high volume of the process of injection molding is characterized by the production of hundreds of thousands to millions of parts, and it is accomplished in durable steel molds due to their long life.
By getting these factors, you will get the knowledge of how to reduce the costs strategically and get the efficiency and profitability of the projects of injection molding.
To learn more about plastic injection molding, visit our blog. To browse our services, check out our services page. If you’re ready to begin your custom project, request a quote today.
For mid-volume runs (5,000-10,000 parts), the cost per part can be around $3. For high-volume production (100,000-300,000 parts), the cost per part can decrease to around $1.75.
The cost of injection molding per kg of material depends on the type of plastic being used. Common plastics like polypropylene or polyethylene can cost between $1.50 and $3 per kg.
These are home costs, and unlike overhead, these are costs associated with an operating facility. These overhead costs need to be managed and optimized in an effective way for profitability to be sustained.
ABS refers to acrylonitrile butadiene styrene, a thermoplastic polymer commonly used for injection molding. The primary ingredients of acrylonitrile, butadiene, and styrene each impart specific properties to ABS injection molded parts. Acrylonitrile adds hardness and provides heat and chemical resistance. Butadiene offers added toughness and impact resistance. Styrene adds strength, gloss, and workability.
GETTING A QUOTE WITH LK-MOULD IS FREE AND SIMPLE.
FIND MORE OF OUR SERVICES:
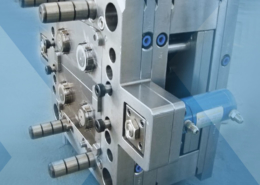
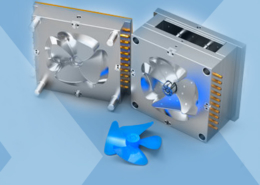
Plastic Molding

Rapid Prototyping
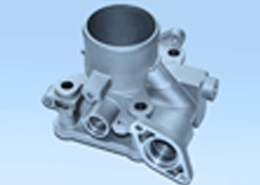
Pressure Die Casting
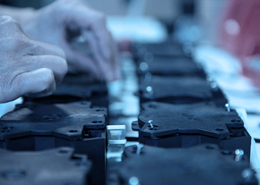
Parts Assembly
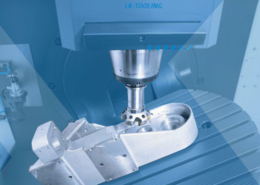