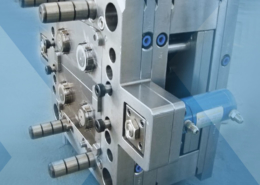
Contact Us - custom molded plastics
Author:gly Date: 2024-10-15
The most common way to produce plastic parts is via the injection molding process. When the process uses raw materials that can be heated to soften or melt, it is called thermoplastic injection molding. Many plastic parts are made from thermoplastic materials including Nylon, Polycarbonate, and ABS. When the process uses materials that permanently solidify through a chemical reaction, it is called thermoset molding. Thermoplastic injection molding, which relies on the rapid cooling of the melted plastic material inside the mold, typically results in a much faster processing cycle than thermoset molding. Typical thermoset materials include DAP, Phenolic, and Epoxy.
Ensure that you’re using heat-resistant gloves or potholders. Touching the sheet at this high temperature can burn your hands.
Thermoset Compression molding uses a loose, powdery molding material that must be weighed before an operator or automated equipment places the material into an open mold cavity. The press applies heat and pressure until the part is cured.
You already know the wide range of applications of acrylic sheets. Because of their DIY-friendly nature, people love to use them and make various items at home. You don’t need fancy tools or high expertise to get around with acrylic sheets.
You can mold a clear acrylic sheet and make them into various shapes and structures. And no, you don’t need to have fancy tools or prior experience. How do you do it?
If you’re using a heat gun, you’ll want to place your sheet over the mold, like your bowl or mug, and then slowly heat up the sheet by running it slowly over the surface.
Whether you have a drawing, a sample, or simply an idea, our team can design the part and select the material which best fits your needs, perform 3D modeling, create full-size prototypes, design and create the molds, perform first article inspection and then produce production quantities. We are ITAR registered and ISO 9001 certified.
Using modern, state-of-the-art primary and auxiliary processing equipment enables Rebling to provide the highest quality molded parts available anywhere. To ensure part consistency and minimize machine downtime, all processing equipment is serviced using an extensive preventative maintenance program. This includes all the Customer-owned molds and fixtures which undergo routine maintenance during and after production runs. Every mold is tracked for a number of cycles in our ERP system to ensure maintenance is performed at the proper interval.
UVACRYLIC is a subsidiary of UVPLASTIC, which is the top supplier of acrylic sheet in China, meantime, provides machining acrylic services to global clients.
Since our founding in 1962, we've offered many types of plastic molding processes to meet our Customers’ diverse needs including thermoplastic injection molding, insert molding, wire over-molding, thermoset injection, compression, and transfer molding. No matter the process, we can recommend and manufacture plastic parts in the appropriate material for any project.
Before you dye the object, it’s necessary to make it clean thoroughly. Get dishwasher soap to make your object clean and remove any strains.
While both of these methods are more labor-intensive than injection molding, some thermoset materials are only available in transfer and compression grades. In order to achieve some of the special properties of thermoset materials, compression and transfer molding processes are sometimes necessary.
Now the most crucial step. Use the tongs to place your sheet into the dye. Move around your object into the wye to ensure it absorbs the dye evenly.
After the dye is dissolved and water is boiled enough, make the water cool down slightly. If the pot or pressure cooker is too small, pour the water into a larger bucket.
First, decide what you want to make and cut acrylic sheet accordingly. If you’re planning to make a bowl or mug, mark the sheet into the right size and then cut it. Maybe here, you want to know more about machining custom acrylic.
Use a pressure cooker or pot and stove to boil the water. Hot water works best for this as plastic absorbs hot water better.
UVPLASTIC Material Technology Co., Ltd is a ONE-STOP SUPPLIER of Polycarbonate and Acrylic Sheets. Meantime, we provide INTEGRATED FABRICATION SOLUTIONS in the plastic field, established in 2003 in Suzhou, China. Today, we are so honored to provide high-quality polycarbonate and acrylic sheets and superior fabrication service to more than 2000 clients from more than 40 countries in the world.
You might not get it right at the first pass. But that’s not a problem. Just reheat the sheet, like you previously did, and start pressing until you’re fully satisfied with the shape.
Now that you have the desired color, you want to let it dry. Often people use lukewarm and soapy water right after dyeing. But I’ll refer you to let it dry first then use soapy water to make the finishing better.
Thermoset materials are typically used in applications where retention of mechanical properties at extremely elevated temperatures is a requirement. The thermoset manufacturing process requires significant experience with plastic injection molding. Whether using thermoplastic or thermoset material, injection molding is the most cost-effective method because it can be automated, eliminating labor-intensive preliminary or secondary operations.
If you disable this cookie, we will not be able to save your preferences. This means that every time you visit this website you will need to enable or disable cookies again.
We produce thermoplastic and thermoset custom molded parts using hundreds of different standard and custom plastic formulations (see alphabetical listing below) and offer a wide spectrum of insert-molding (plastic molded around metal parts), over-molding (plastic molded around plastic parts), and post-molding services (machining, assembly, printing, laser marking, ultrasonic welding, heat staking, etc). We specialize in a wide spectrum of molding services, including insert molding and over-molding services. 95% of the parts we produce are smaller in size than a gallon jug of milk, weigh less than one pound, and have a maximum dimension shorter than 12 inches.
The Thermoset Transfer molding process starts with pre-forming a cylindrical “pill” of material of the proper weight. The pill is usually hand loaded into a mold, where a plunger pushes the material into the cavity, and the thermoset material cures, through a chemical reaction, under heat and pressure.
Maybe you want to know more about custom plexiglass. If you have any questions or suggestions, please reach out to us through our chatbox and contact page.
You need to do this for a couple of minutes. Once the sheet temperature reaches 320F, it will become malleable and ready for molding. And if you’re using an oven, let it inside for 7-8 minutes and often check if it became pliable enough. Once you’re satisfied with the sheet’s softness, bring it out and place it over the mold.
UVPLASTIC is one of the leading manufacturers of polycarbonate. Along with providing world-class material for people worldwide, we’ve taken a mission to provide as much information and guides about our products.
Until you get the desired color, you’ll need to dip the object into the dye and rinse it with a continuous cycle. When you have the color you want, lift the plastic from the water.
Once it has become pliable enough and ready to mold, you’ll want to place it over the bowl, mug, or structure you’re using as a mold. And start pressing in the center of the sheet. It will slowly begin to mold into the mold shape.
No matter which molding method is used, processing parameters for each part are documented and stored in machine memory to insure lot-to-lot consistency.
We aim to provide the most useful information and DIY ideas and how-to guide our readers to make your life easier and make the work fun. Let us know how you like this guide and share it with your friends and family.
This website uses cookies so that we can provide you with the best user experience possible. Cookie information is stored in your browser and performs functions such as recognising you when you return to our website and helping our team to understand which sections of the website you find most interesting and useful.
We produce custom-molded plastic parts for OEMs in the Defense, Avionics, Instrumentation, Medical, Consumer Products, Energy, and Transportation industries. ISO 9001 certified ITAR Registered, DoD Certified Munitions Supplier, QPL Approved, FDA Class I, II, and III medical devices. The parts we create range from dime-sized to gallon-sized, from parts designed to last 50 years to those designed as disposables, in quantities from 500 pieces to 20,000,000 pieces per year, and for environments as pleasant as an air-conditioned office to as unforgiving as an oil drilling borehole.
One specialized type of plastic injection molding performed at Rebling is called insert molding. This process involves molding plastic around another part, which could be made of metal or another plastic material. Wire over-molding, or wire plastic molding, is a special type of insert molding where plastic is molded over different sizes of wires to form a plug or strain relief.
GETTING A QUOTE WITH LK-MOULD IS FREE AND SIMPLE.
FIND MORE OF OUR SERVICES:
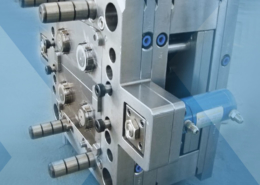
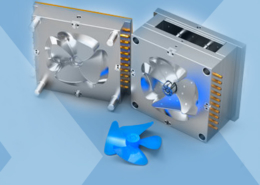
Plastic Molding

Rapid Prototyping
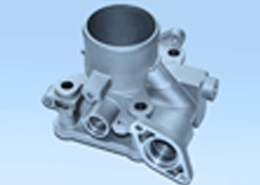
Pressure Die Casting
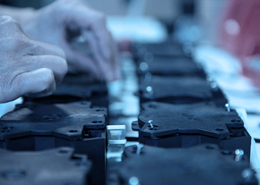
Parts Assembly
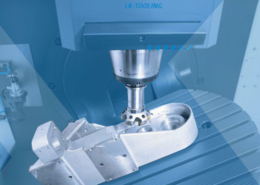