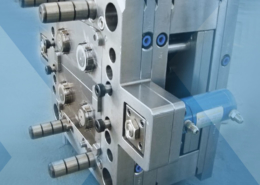
Composite (Core-Back) Injection Molding - back injection molding
Author:gly Date: 2024-10-15
The whole ABS injection molding game also hinges on the mold and gate design. You’ve got to get the wall thickness on point for even cooling, so the ABS part stays stable in shape and size. The gate needs to be spot on too, making sure the ABS flows smoothly and quickly into the mold, without putting stress on the part. It’s all about crafting top-notch quality.
In the intricate world of Medical Device Design, the selection of High-Quality Materials for Medical Injection Molding plays a pivotal role. A critical aspect of this process lies in the Importance of Biocompatible Plastics in Medical Devices, and this is where we position our expertise.
process, has transformed the medical industry. This advancement ensures more efficient operation of the mold flow analysis system, leading to more precise and consistent results. It facilitates the development of medical product components, reducing the margin of error and waste during production.
A robust system of automation also offers the advantage of improved traceability, a key aspect of regulation and compliance in the medical industry. Furthermore, companies like Marlee – Texen employ overmolding techniques, contributing to their recognition as one of the
One of the most notable challenges with ABS is its poor weathering resistance. Continuous exposure to UV light can lead to fading and a decrease in the material’s impact strength. For products meant for outdoor use or those frequently exposed to sunlight, this can be a significant drawback. Imagine a garden chair made of ABS. Over time, under the sun’s relentless rays, it might lose its vibrant color and even become brittle.
Our approach to Quality Control is exhaustive. From the initial design and injection phase of Medical Injection Molding to the final assembly and packaging of your device, our team ensures every step of the process is controlled, monitored, and optimized. We understand that the end-use of our products is in the critical healthcare sector, making the safety and functionality of each part and medical device we produce a non-negotiable priority.
After chatting about the big role temperature plays in ABS molding, it’s cool to know there are extra bits (additives) that can really help this plastic material shine even more.
As we’ve explored the pros and cons of ABS, it’s clear that while it offers many advantages, it’s not without its challenges. Let’s summarize:
The transformative impact of medical injection molding on the healthcare industry is a testament to its versatile applications. With its precision and efficiency, it caters to a multitude of sectors within the industry, enabling manufacturers like Marlee – Texen to produce top-tier medical devices. One of the significant contributions of this process is in the production of
The range of applications for medical device injection molding is extensive, stretching across diverse medical fields. From implantable medical devices and disposable medical devices to drug delivery devices, Marlee – Texen crafts each component with the utmost precision and compliance with ISO 13485 and FDA standards. They utilize cutting-edge techniques for both short-term implants and long-term implants, ensuring optimal biocompatibility and safety.
Want to make ABS even more awesome? Additives to the rescue again! By mixing in the right extras, you can make ABS stretchier and more bendy. And if you pair ABS with some metal coatings? Here! The strength and toughness of the injection mold product go way up. Like, imagine car parts made from ABS getting a metal boost. They can take hits and keep on going, making them super safe and long-lasting.
From Liquid Silicone Rubber (LSR) molding to complex micro-molding processes, we ensure that every enclosure, packaging solution, and component we create meets the highest industry standards.
Additional CNC machining is provided after thermoplastic injection molding. We can also put metal inserts into medical plastic parts by heat pressing.
In the demanding field of Medical Device Design, the choice of High-Quality Materials for Medical Injection Molding is critical. An essential consideration in this sector is the range of materials available, from Polypropylene to PEEK. At Marlee – Texen, we excel in providing a comprehensive array of materials to ensure your project’s success.
Since it is a strong plastic, ABS is everywhere! Cars love it for parts like bumpers because it’s tough. Cool gadgets and electronics wear it as a durable outfit. Toys like LEGOs brag about it because it’s strong and safe. Even the medical world gives it a thumbs up for being easy to clean and tough. ABS in injection molding is like a celebrity, famous for being amazing and versatile!
Jumping from the nitty-gritty of the ABS injection molding process to the crucial role of temperature control, it’s crystal clear that precision is king. Next, we’ll jump into how keeping the heat in check is essential for pumping out primo ABS parts.
companies is the use of automation. Leveraging advanced injection molding equipment and scientific molding principles, they ensure consistent production of high-precision medical device injection molding parts, regardless of whether it’s high-volume production or low-volume production.
Every plastic has its own playbook for how to mold it, and ABS plays by its own rules. You have to get the injection pressure and speed just so, to match ABS’s flowy nature. For a perfect fill, you crank up the injection molding pressure, and to avoid wonky defects, you keep the injection speed in check. It’s all about making sure the final ABS part comes out looking sharp, without any twists or warps.
Not all ABS is created equal. Different grades of ABS require different molding temperatures. For instance, while working on a project for household appliances, I discovered that a specific grade of ABS needed a slightly higher temperature than the standard. It’s these nuances that make the process both challenging and rewarding.
At Marlee – Texen, we are stringent about Biocompatibility Testing. Our medical-grade materials undergo rigorous testing to meet the required standards. We are adamant about quality, from the selection of polymer materials to their transformation into a functional part of a medical device.
Utilizing robust silicone and plastic materials, our advanced processes assure the traceability of every implant, mold, and micro-molded part. Our stringent quality control measures ensure that every weld and polymer application aligns with the highest industry standards. Our in-depth assessment procedures are followed by rigorous testing, guaranteeing the quality and safety of our output.
Biocompatible plastics, also known as Bio-Compatible Plastics, are essential for ensuring the safety and functionality of a medical device. They are engineered to interact with the human body without causing any adverse reaction. This feature is paramount in the industry, where patient safety and assurance of product functionality are non-negotiable.
, we prioritize Stringent Quality Control and Regulatory Compliance. Our operations underscore the importance of ensuring Patient Safety and delivering high-quality medical products through our state-of-the-art injection molding facilities.
Our team’s expertise in medical device design ensures that the selection of these materials is tailored to the specific requirements of each project. We believe that every part of the process, from initial prototype design to final delivery, is integral to the successful operation of a medical device.
Medical device injection molding, however, is not merely about the molding process but also involves detailed tooling design, stringent compliance, and rigorous regulation. In fact, Marlee – Texen has built its reputation as one of the
industry is the adoption and mastery of Micro-Molding. This highly specialized mould design has allowed a significant shift in medical molding innovations. Specifically, it has been instrumental in the production of smaller, more intricate medical components, and the high-precision manufacturing of injection molded parts.
Another significant development is the adoption of liquid silicone rubber (LSR) in the medical injection molding process. LSR is ideal for producing implantable and disposable medical devices due to its superior biocompatibility.
Two crucial developments further highlight the profound influence of micro-molding in the field. One is the refinement of two-shot injection molding that allows for simultaneous injection of two different plastics into a single mold. This technique has significantly boosted the manufacturing efficiency of complex medical device components. The other is the potential of micro-molding to pave the way for polymer-drug conjugates, a novel innovation that could revolutionize the medical injection molding process.
, Stringent Quality Control and Regulatory Compliance serve as the bedrock of our operations at Marlee – Texen. We are recognized as one of the leading
Every material used and every product produced at Marlee – Texen undergoes rigorous quality checks and verifications. Our comprehensive processes are aligned with top design and tool selection strategies to enable the effective assembly of components. Our equipment and machines are optimized for precision, allowing us to cater to diverse requirements, including surgical applications.
Temperature, ah, the unsung hero of the ABS molding process. It’s a factor that’s often underestimated, but its influence is undeniable.
in the industry, primarily due to our unwavering commitment to the highest quality standards and adherence to stringent regulations.
We provide services like pad printing and silk screening to put 2-D designs on 3-D surfaces. These designs can be customized for labeling, branding, etc. We use standard colors and Pantone matching.
ABS is like a magical mix. It’s a thermoplastic polymer that brings together three awesome ingredients: acrylonitrile, butadiene, and styrene. Acrylonitrile is like the tough guy, adding chemical resistance. Butadiene is the muscle, giving it impact resistance. And styrene is the show-off, making things shiny with a high gloss. Together, they make ABS parts sturdy and stable.
The process of injection molding is complex and requires precision at every stage. Every part we create for your medical device is injection molded to exact specifications, guaranteeing performance and safety. Our thorough selection process, extensive product development capabilities, and advanced process management set us apart in the industry.
At Marlee – Texen, we excel in high-volume production while maintaining meticulous quality control. We deploy advanced flow analysis to optimize the production process, and our commitment to creating safe, effective disposable medical products is unwavering.
Back in my earlier dayss, I remember standing in front of a massive injection molding machine, its mechanical arms moving in a dance of precision. The process begins by feeding the ABS pellets into a dry hopper. These raw materials get melted, and the molten ABS is then injected into a mold at high pressure, solidifying into the desired shape.
Cold weather? No problem! ABS doesn’t crack easily, even if it’s freezing. Think about cars – they need parts that are tough and work all the time. That’s where ABS molding steps in. It gives us safe and high-performing parts that don’t give up.
The customization process involves a collaborative approach of Design for Manufacturing (DFM). This approach ensures every part of the device – be it orthopedic, cardiovascular, or any other field – is meticulously designed and manufactured. This process not only maximizes quality and efficiency but also significantly reduces risk and time-to-market.
. This critical facet of medical device production ensures the sterile and safe transport of these crucial devices, reinforcing their commitment to overall healthcare delivery.
As a leading player in the industry, Marlee – Texen continues to embrace these technological advancements, contributing to molding industry trends and setting the bar high in terms of quality and efficiency.
in creating effective medical packaging. Their offerings ensure safety, sterility, and efficient delivery of medical devices, embodying their commitment to overall patient health and safety.
In my years of experience, I’ve seen how temperature can be both a friend and a foe. Too high, and you risk thermal degradation; too low, and the ABS might not flow properly. Achieving the right temperature ensures the ABS maintains its excellent dimensional stability and high gloss finish.
Every step, from mold design to post-molding operations, including state-of-the-art plastic welding techniques, is conducted under rigorous regulation and compliance with ISO 13485 and FDA standards. With an emphasis on medical device design and medical injection molding process, Marlee – Texen offers tailor-made medical plastic products for a diverse range of applications.
To uphold this principle, we invest in state-of-the-art biocompatibility testing protocols. Our robust testing ensures that our plastics are not only safe for patient use but also contribute to the efficient operation of the devices they form. In this way, we assure both the quality and safety of our products.
As a reliable supplier in the industry, we abide by the 13485 quality management system. Our thorough risk assessment procedures ensure the highest level of safety and reliability in our products.
Our range of biodegradable plastics and polymer materials are expertly chosen to ensure the highest grade of biocompatibility. Our offerings include:
When I first touched the world of materials, there’s one plastic type that caught my intrigue – acrylonitrile butadiene styrene, or more commonly known, ABS plastic. Now, as someone with decades under his belt in the tech industry, ABS remains one of those fascinating materials that’s everywhere, yet often overlooked. The gentle hum of my vintage record player reminds me: even musical instruments have parts made from this versatile plastic.
such as Marlee – Texen have consistently leveraged technological advancements to deliver high-quality medical injection molding services, providing a seamless blend of quality and efficiency.
Now that we’ve talked about how additives can really up the game in ABS molding, let’s tie it all together. ABS plastic is a real champ—it’s tough, flexible, and doesn’t break the bank. Even its kryptonite, UV light, can be handled with the right additives, opening up even more ways to use it.
Our Medical Injection Molding services are meticulously carried out in the confines of our advanced Cleanroom Manufacturing facilities. These environments ensure the sterility and safety of every device and medical device part we manufacture. As an industry-leading provider of plastic injection molding, our cleanroom facilities are designed to eliminate contaminants, ensuring the utmost safety for the end-user.
Next up, let’s chat about a few things ABS might not be the best at. Stick around as we dive into the not-so-awesome sides of ABS injection molding, so you get the full picture of this fab material.
Polycarbonate (PC) is quite an efficient material that is amorphous and transparent in nature. It is a type of thermoplastic used in medical plastic packaging, a wide variety of shapes and sizes of plastic. PC injection molding is one of the best choices for manufacturing custom-tailored plastic because of its highly flexible and impact-resistant qualities.
To conclude, automation and technological advancements in medical molding have made a significant impact on the medical device market. These advancements are not just about high-speed delivery and high-volume molding but also about maintaining safety and quality, ensuring each product meets the strictest medical grade standards.
Whether you require drug delivery devices, enclosures, packaging, or disposable medical components, Marlee – Texen stands as the
Marlee – Texen is committed to providing superior solutions that cater to the demanding needs of the medical device industry. We guarantee high-quality materials, stringent testing, and dedicated service to ensure we meet and exceed your expectations.
Our precision in molding extends beyond materials like polypropylene and PEEK. We are also a leading producer of micro-molding components, crucial in the development of advanced medical technologies. Our precision welding processes ensure seamless joins between components, maintaining the integrity of the overall device.
Safety is paramount in our operations. Our Cleanroom Molding and Sterilization Techniques are implemented with a deep understanding of the importance of safety in medical device manufacturing. We also offer rapid turnarounds, without ever compromising quality or safety.
. These tailor-made solutions not only maintain the sterility of medical products but also offer efficient storage and delivery of devices.
like Marlee – Texen at the forefront, the future of medical injection molding promises to deliver even greater innovation and quality analysis, optimizing flow and reducing waste. These advancements ensure that patients around the world benefit from safer, more effective medical devices, a testament to the relentless pursuit of excellence in the medical molding sector.
So, one tiny hiccup with ABS parts? They’re not best buddies with UV light. Too much sun can make them feel a bit off. But, guess what? There are some nifty additives to save the day! By adding stuff like acrylics or even slapping on coatings like glass, the surface of the product can totally block out those UV rays. This means your ABS parts, like outdoor toys or garden tools, can chill outside and still last a long time without getting all worn out by the sun.
In terms of design, we deploy state-of-the-art tools and equipment to create intricate components and assemblies. Every machine we use is operated by expert manufacturers, proficient in handling delicate materials like silicone, vital in the creation of a myriad of implants and medical device parts.
At Marlee – Texen, we adhere strictly to both ISO and FDA standards. Every regulation is taken into account, and compliance is guaranteed. Our processes are regularly audited, our tools and assembly procedures are meticulously maintained, and every component we produce is verified for accuracy using advanced equipment and machines.
are the backbone of the healthcare industry, and their production hinges on the precision and reliability of injection molding.
After diving deep into the world of ABS and all the tricks to make it even better, it’s easy to see how, with a bit of know-how, ABS molding can be top-notch. Stick around, and next, we’ll chat about the top tips for rocking ABS injection molding.
Polyethylene or polythene is the resin made from the polymerization of ethene. PE is the most versatile synthetic resin. It has a crystalline structure and can be high density (HDPE) or low density (LDPE). It is used by the medical plastic products.
But ABS isn’t just strong; it’s a powerhouse! It’s got muscle (tensile strength) and can take a hit (high impact resistance). Plus, it’s flexible and doesn’t get tired, whether it’s hot or cold. It’s like the ultimate athlete in the plastic world!
that comprehensively aligns with FDA Regulations and maintains an unwavering commitment to Medical Standards Compliance. We are proud holders of ISO 13485 certification, which underscores our commitment to quality and safety in the production of medical devices. Our Validation Process is thorough and rigorous, ensuring every part and component we produce is safe, effective, and reliable.
ABS isn’t just tough; it’s super flexible too! It’s easy to add color to it, and it stretches like a champ. From cars to toys, ABS is everywhere. Manufacturers love it because they can mold it into fancy shapes super fast with high injection molding speeds. That means making stuff quicker!
Another concern is the fatigue resistance of ABS parts. Under prolonged heavy loads, stress concentration can occur, leading to fatigue and eventual damage. As time goes on, ABS can wear out, especially if it’s subjected to repetitive stress. Moreover, the initial investment for ABS plastic molding can be high due to the complexity of certain designs. This might make small-scale production a tad expensive. For instance, producing a batch of 100 intricate ABS parts might cost 20% more than simpler designs.
Automation, combined with cutting-edge technologies like rapid prototyping, has enabled precise molding for both plastic and silicone based products. Furthermore, automation ensures enhanced cleanroom standards, paramount for medical parts production, ensuring compliance with ISO and FDA regulations.
Before diving into making cool ABS parts, you gotta prep and dry the ABS material just right. This is super important to stop any pesky moisture from messing up the final product—nobody wants bubbles or streaks in their stuff. Usually, you’d dry ABS at around 80–85 °C for a few hours to make sure it’s got good resistance to these problems.
to meet your needs. Our emphasis on quality assurance and medical component assembly sets us apart in the medical molding industry, making us a trusted partner for healthcare providers across the globe.
Our Material Selection is extensive and industry-leading. Our expertise encompasses everything from robust Plastic Medical Enclosures to flexible Liquid Silicone Rubber (LSR). Our team’s adeptness at High-Temperature Molding ensures we can work with a variety of Polymer Materials to achieve your project’s specific needs.
Medical injection molding plays a fundamental role in the healthcare industry, touching nearly every sector with its capabilities. Its breadth of application and adaptability have made it an indispensable part of medical manufacturing. For instance,
In conclusion, these technological advancements in medical device injection molding have redefined the boundaries of what’s possible in the medical industry. From the smallest micro components to the most complex medical parts, these innovations have facilitated the creation of high-quality, disposable, and durable medical devices, elevating the overall standard of healthcare.
To make sure every ABS part is a carbon copy of the last one, you gotta pay attention to the nitty-gritty. Keeping an eye on the injection process and giving the machines and molds some TLC are keys to nailing this manufacturing process. It’s about keeping customers happy with parts that are just what they expected, every single time.
Alloys like PC/ABS and TPE/TPU – PC/ABS combines the strength of PC and the flexibility of ABS, making it ideal for use by a medical plastic products manufacturer. TPE and TPU are thermoplastic elastomers. They are used for making lids, sports goods, power tools, medical device parts, etc. They are used in these industries for their abrasion resistance and elasticity.
Our team of expert manufacturers at our company is well-versed in the requirements of the industry, ensuring traceability of all parts and components, including sensitive implants. Our validation processes and quality checks make us an ideal choice for micro molding requirements in the medical industry.
To really nail ABS molding, team up with a pro injection mold maker. They’ll guide you through the ABCs of ABS, making sure you get awesome parts without spending a fortune. So, jump on the ABS bandwagon and watch your production soar!
With a clear understanding of ABS’s strengths and weaknesses, let’s delve deeper into the ABS injection molding process, ensuring we harness its potential while being aware of its limitations.
Medical device injection molding process is used in bone repair and rearrangement. It is also used for soft tissue reattachment.
When you think about plastic injection molding, ABS injection molding is like a superhero. Why? It’s got awesome tensile strength and can take a beating! This cool mix of acrylonitrile, butadiene, and styrene combines the best stuff to make something super tough. Once you mold ABS parts, they stick around and can handle a lot. They’re great for jobs where things need to stay strong and keep working hard.
, has paved the way in producing premium quality, high-performance medical device injection molding products. Their focus extends from simple disposable medical devices to more complex implantable medical devices, with a special emphasis on surgical instruments and diagnostic equipment.
As the best medical plastic injection molding company, we use medical molding in the manufacturing of caps, containers, device components, and medical parts. They are needed in high volumes in pristine conditions for patient safety.
As we keep getting better at making stuff, ABS’s popularity is only going to skyrocket. It’s already a go-to for making all kinds of plastic products. If you’re in the biz of cranking out high-quality items, ABS injection molding is your golden ticket. It’s a speedy, wallet-friendly way to pump out loads of parts, making your production line hum. In this case, ACO mold has various plastic materials, including PVC, ABS, and so on. Contact us for your injection mold project!
Polypropylene(PP) is a thermoplastic resin used for its flexibility and strength. It has a very low density and is suitable for scientific molding. Its flexibility and resistance find much application in plastic medical packaging sensitive material. PP is an “addition” polymer, made from the linking of many polypropylene monomers.
And here’s a cool fact: Even though ABS parts might not love too much sun (UV light makes them break down faster), it’s kind of a good thing for Mother Earth. They break down faster than other plastics, which means they’re easier to recycle. So, ABS is doing its part to keep our planet happy! For those intrigued by the versatile and recyclable nature of ABS and considering other materials for their injection molding projects, understanding how different materials impact the outcome is crucial. Dive deeper into the selection process with our comprehensive guide on choosing the right injection molding materials.
GETTING A QUOTE WITH LK-MOULD IS FREE AND SIMPLE.
FIND MORE OF OUR SERVICES:
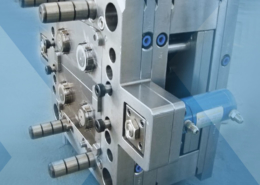
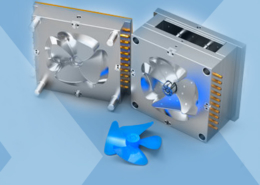
Plastic Molding

Rapid Prototyping
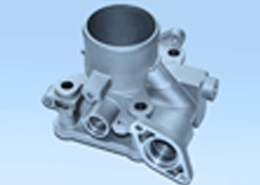
Pressure Die Casting
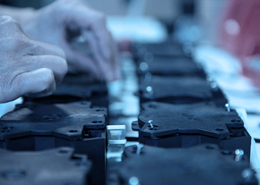
Parts Assembly
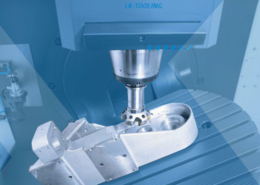