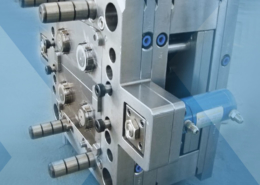
Exploring Mini Injection Molding: Revolutionizing Small-Scale Manufacturing
Author:gly Date: 2024-06-08
Introduction:
Mini injection molding has emerged as a transformative technology in the realm of small-scale manufacturing. Its ability to produce precise, high-quality parts with minimal material wastage has garnered significant attention from industries worldwide. In this article, we delve into the intricacies of mini injection molding, exploring its principles, applications, benefits, and challenges. By the end, readers will gain a comprehensive understanding of this innovative manufacturing process and its potential to reshape various industries.
Principles of Mini Injection Molding
Mini injection molding operates on the same fundamental principles as traditional injection molding but is optimized for small-scale production. The process involves melting thermoplastic materials, injecting them into a mold cavity under high pressure, and then cooling to solidify the part. Unlike conventional methods, mini injection molding utilizes smaller machines and molds, making it ideal for producing miniature components with intricate details.
The machinery involved in mini injection molding typically comprises a hopper, screw, barrel, nozzle, and mold. The thermoplastic pellets are fed into the hopper, where they are gradually melted by the screw as it rotates within the barrel. Once molten, the material is injected into the mold cavity through the nozzle, where it takes the shape of the desired part.
The mold plays a crucial role in mini injection molding, as it determines the final geometry and surface finish of the product. Precision machining and tooling are essential to ensure accurate replication of intricate features within the miniature components.
Mini injection molding offers several advantages over traditional manufacturing methods. Its ability to produce small, complex parts with high accuracy and repeatability makes it invaluable in industries such as electronics, medical devices, automotive, and consumer goods.
Applications of Mini Injection Molding
The versatility of mini injection molding extends across various industries, with applications ranging from microfluidic devices to miniature mechanical components. In the electronics sector, mini injection molding is used to produce small-scale connectors, housings, and circuit board components with precise dimensions and tight tolerances.
In the medical field, mini injection molding enables the fabrication of miniature implants, surgical instruments, and drug delivery systems. The ability to produce biocompatible materials with intricate geometries makes it ideal for manufacturing medical devices that require precise functionality and compatibility with the human body.
Automotive applications of mini injection molding include the production of miniature gears, sensors, and interior components. The process's capability to produce lightweight, durable parts with high strength-to-weight ratios contributes to fuel efficiency and overall vehicle performance.
Consumer goods such as toys, gadgets, and household appliances also benefit from mini injection molding. The process allows for the cost-effective production of small-scale products with intricate designs, enhancing their aesthetic appeal and functionality.
Benefits and Challenges
Mini injection molding offers numerous benefits, including cost-effectiveness, fast turnaround times, and design flexibility. By minimizing material wastage and reducing the need for post-processing, it enables manufacturers to achieve higher efficiency and lower production costs. Additionally, the ability to iterate designs quickly and produce custom parts on-demand enhances product development and customization capabilities.
However, mini injection molding also presents several challenges, particularly in mold design and material selection. Designing molds for miniature components requires precision machining and intricate tooling, which can increase production costs and lead times. Moreover, the limited selection of materials suitable for miniaturized applications poses challenges in achieving desired material properties and performance characteristics.
Conclusion:
In conclusion, mini injection molding represents a paradigm shift in small-scale manufacturing, offering unprecedented precision, efficiency, and versatility. Its applications span across various industries, from electronics and medical devices to automotive and consumer goods. While it presents unique benefits, such as cost-effectiveness and design flexibility, challenges in mold design and material selection persist. Nevertheless, with ongoing advancements in technology and materials, mini injection molding holds immense potential for driving innovation and reshaping the future of manufacturing.
In order to further harness the capabilities of mini injection molding, future research efforts should focus on enhancing material properties, optimizing process parameters, and developing advanced mold designs. By addressing these challenges, we can unlock new possibilities for miniaturized manufacturing and propel industries towards greater efficiency and competitiveness.
GETTING A QUOTE WITH LK-MOULD IS FREE AND SIMPLE.
FIND MORE OF OUR SERVICES:
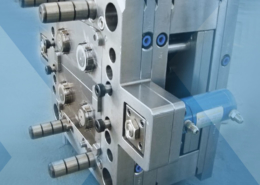
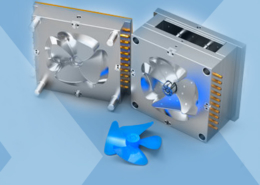
Plastic Molding

Rapid Prototyping
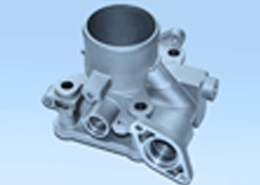
Pressure Die Casting
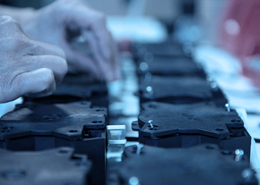
Parts Assembly
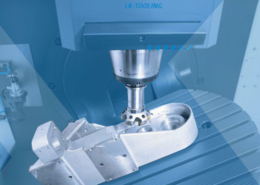