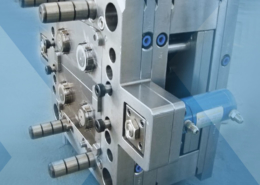
Color Plastic Angle Moulding - plastic molding for wire 1 2
Author:gly Date: 2024-10-15
Structural foam molding is the ideal manufacturing process for creating large, thick-walled parts and products. The low-pressure process allows these large parts to be created in a single cycle and prevents damage and warpage during the process.
The solid exterior of the product gives it durability and strength while the honeycomb interior makes these products more lightweight than their injection molded counterparts. This is especially advantageous for large parts.
Structural foam molding is done by mixing a melted polymer with nitrogen gas and/or a chemical blowing agent. This mixture is then injected into a mold under low pressure and, as the polymer mixture touches the walls of the mold, it cools, forming a solid outer layer with a honeycomb interior.
The injection molding process is high-pressure which allows the molten polymer to get into all of the nooks of the mold. This pressure allows for the creation of products with highly detailed and complex designs.
Because injection molded parts are completely solid they are very durable. This also gives them uniform strength throughout the product.
The honeycomb-like interior of structural foam molded products reduces their weight when compared to their injection-molded counterparts, allowing them to be used in a wide range of industries and applications.
The low-pressure process of structural foam molding puts significantly less stress on the parts during the molding process. This leads to less warping and damage during manufacturing, which saves you time and money.
Many times parts come out of the injection mold with good aesthetics and will require little to no finishing. Since you won’t need hardly any finishing services, you will save money on your manufacturing costs.
When designing your plastic project, it is important to choose the right manufacturing process. Ensuring you take your product’s application, size, and material into consideration before starting the manufacturing process will save you time and money while yielding a higher-quality product. Deciding on what process is best for your application can be tricky, so if you are wondering which is better for you — structural foam molding vs injection molding — we have outlined each below.
Injection molding is one of the fastest plastic manufacturing processes available. It is possible to create many parts in a short period of time through the injection molding process, allowing the manufacturing process to be completed faster.
Since structural foam molding is a low-pressure process the materials used to create the tooling and molds do not need to be as durable as those for injection molding. This lowers the cost of your tooling production. Additionally, less raw materials are used in the process since the product isn’t entirely solid resin.
Our engineers will work with you and your design to decide which process is best for your application — structural foam molding or injection molding. Since both processes happen under the same roof, there is no difference in start time regardless of what process is chosen for your part.
With over 70 years of experience, Port Erie Plastics has the expertise needed to create high-quality, large parts through both low-pressure structural foam molding and high-pressure injection molding. Our structural foam molding machines go up to 500 tons and our injection molding machines can go up to 1650 tons.
Ready to see what process is right for you? Contact our team today to get started on your structural foam or injection molding process.
During the injection molding process, a polymer is melted inside the injection molding machine’s heated barrel. The machine is then closed and the mold halves close together and are held together under high clamp pressure. The screw in the barrel then pushes the molten polymer under very high pressure into the mold. Once all material is in the mold, the screw pulls back and starts cooling. When it is cooled entirely, the product is released from the mold.
GETTING A QUOTE WITH LK-MOULD IS FREE AND SIMPLE.
FIND MORE OF OUR SERVICES:
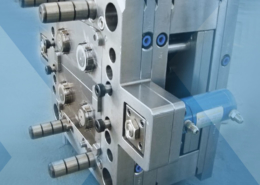
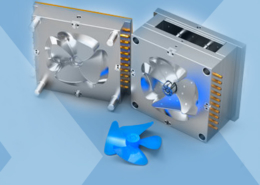
Plastic Molding

Rapid Prototyping
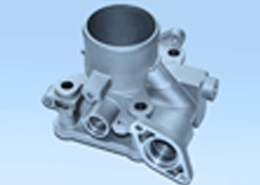
Pressure Die Casting
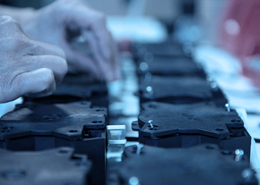
Parts Assembly
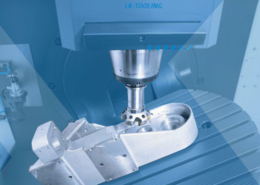