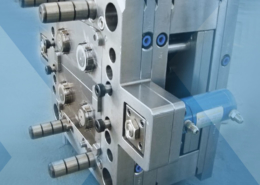
Co-Injection Molding Analysis - co injection molding
Author:gly Date: 2024-10-15
Hybrid: This manufacturing process of plastic injection molding has been in the market for decades, and Custom Industrials Company agrees to it as well. It combines the clamping force of Hydraulic manufacturing with a noise-free operation because of the electric machines. They come in two varities vertical and horizontal. Horizontal is the most common where the mold part or opens on the horizontal. The vertical molding machines are use for insert molding of metal components so the is no need for mechinical means to hold parts in a horizontal mold. Gravity holds the inserts in place. Metal parts such as threaded inserts, stamped parts and other higher temperature plastics that don't melt in the primary plastic are molded in this process. Molding plastics over other plastics is called overmolding.
We deliver plastic fabrication solutions including plastic injection molding, thermoforming, CNC machining, stamping, extruding and other plastic product or part solutions.
Capabilities include acrylic mirror injection molding, but are not limited to, plastic tanks, flat bottom tanks, conical bottom tanks, dip tubes, single use bag totes, stackable carts, collapsible tank designs, deployment equipment carts, filter integrity test carts, filter drying racks, fume hoods, containment cabinets, medical plastics, bulk chemical storage, secondary containment, tubing racks, gowning racks, gowning cabinets, scrubbers, coils, fiberglass grating, automotive plastic parts and an unlimited number of other OEM or end products.
CIC's acrylic mirror injection molding provides the highest industrial standards via processes like JIT, EDI, FIFO, and lean manufacturing that are present in our strategies to meet client needs.
Electric: It was originally introduced in Japan back in 1984, but now it sells about half of the IMM machines in the entire USA. These machines have highly remote-controlled servo motor with even higher speed. This leads to faster, reliable, repeatable, and more correct operations.
UHMW can be processed using various methods such as compression molding, CNC machining, injection molding, and extrusion. Compression molding involves applying heat and pressure to reshape the material into the desired shape. Injection molding involves melting the UHMW pellets and injecting the molten material directly into a mold. Extrusion involves melting the UHMW material and passing it through a die to form a continuous profile. Each method has its advantages and disadvantages, and the choice of processing method will depend on the specific application requirements.
UHMW has a wide range of applications across various industries, including automotive, aerospace, construction, and food and beverage. In the automotive industry, UHMW is used for wear-resistant parts such as gears, bearings, and bushings. In aerospace, UHMW is used for lightweight components such as the insulation around rocket boosters. In the construction industry, UHMW is used as a lining material for hoppers, chutes, and silos. In the food and beverage industry, UHMW is used for conveyor parts, food processing equipment, and packaging.
UHMW is a type of polyethylene that has a very high molecular weight, resulting in its excellent mechanical and chemical properties. Some of the key properties of UHMW include high abrasion and impact resistance, low coefficient of friction, high tensile strength, and good chemical resistance. UHMW also has a low density compared to other high-performance plastics, making it a lightweight option for many applications. Other notable characteristics of UHMW include its ability to sustain high loads over extended periods, its self-lubricating properties, and its good electrical insulation properties.
UHMW is an excellent choice for many parts applications due to its unique set of properties. Some common UHMW parts applications include wear strips, guide rails, rollers, seals, and gaskets. UHMW wear strips are used in conveyor systems to reduce friction and extend the life of the equipment. Guide rails made from UHMW are used in packaging machinery to ensure accurate product placement. UHMW rollers are commonly found in packaging, bottling, and material handling industries due to their low friction and abrasion resistance.
We are focused on delivering quality acrylic mirror injection molding for customized manufactured parts or products, which comprise of Metal and Plastic components.
It has minimalized tooling costs, enabling a bright color palette and simple adjustments. In fact, thermoforming is best for producing 250 to 3000 units. Whereas, injection molding is appropriate for larger volume and production runs.
It is the most commonly used manufacturing process for the fabrication of plastic parts and plastic products from both thermoplastic and thermosetting materials.
Thermoforming: Using this manufacturing process, only single-sided plastic fabrication can be done. Furthermore, thermoforming is divided into vacuum form and pressure form styles.
Both types of molding machines work well for the thick and thin-walled parts of the plastic that is intended to be melted.
Hydraulic: It came into dominance back in the 1930s, and till date, it uses hydraulic cylinders to clamp the plastic together in the mold. These are best for producing automotive plastics which requires bulk production.
Plastic injection molding is a form of plastic fabrication that can be used with the following materials: HUMW, PTFE, Ploypro, copolymer, PVC, CPVC, PVDF, HDPE, LDPE acrylic, polycarbonate, acrylic mirror, acrylic twinwall, cutting board plastics, Kydex, ABS, Styrene, PETG, Prismatic Lens, Prismatic Panels, Plastic Louvers Eggcrate, Arm-A-Lite Safety Sleeves, Rigid Plastic, Flexible Tubing, UHMW Tape, Nylon, Delrin, Phenolic, Cast Nylon, Urethan, Polyethylene, Polypropylene, Kynar, Halar, general plastics, performance plastics, lighting plastics, engineered plastics, corrosion resistant plastics, engineered plastic materials and more.
Industries that use acrylic mirror injection molding include, but are not limited to manufacturing, machinery, packaging, building and construction, automotive, agricultural, textiles, transportation, electrical, electronic, consumer products, institutional products, food and beverage, oil & gas, oilfield, and more.
In conclusion, UHMW is a versatile material that offers an excellent combination of properties, making it an ideal choice for many applications. Its unique set of properties such as high abrasion resistance, low coefficient of friction, and good chemical resistance make it widely used in various industries. With its available processing methods, UHMW can be easily molded, extruded, or machined to meet the specific requirements of a given application.
The presses for plastic injection molding (also known as injection presses) vary in size from close-tolerance for small plastic parts to large plastic parts. The process uses molds in which the plastic is cold runner or hot runner depending on the end product. Hot runner is more complex and usually used when the part is injected into another part. The plastic injection molding process is rated based on pressure or tonnage.
Plastic molding processes, including acrylic mirror injection molding, such as thermoforming, blow molding, extruding, and other plastic forming techniques are commonly used in manufacturing.
GETTING A QUOTE WITH LK-MOULD IS FREE AND SIMPLE.
FIND MORE OF OUR SERVICES:
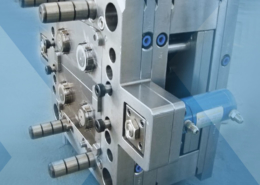
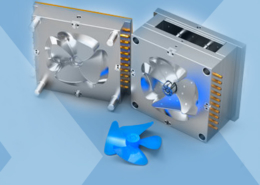
Plastic Molding

Rapid Prototyping
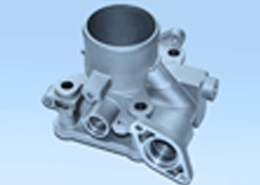
Pressure Die Casting
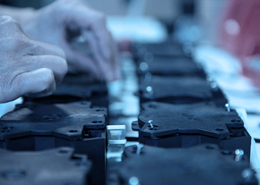
Parts Assembly
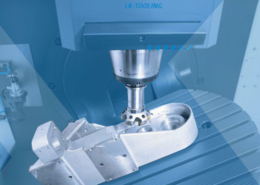