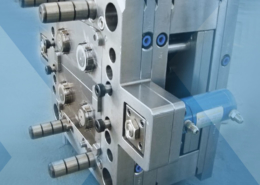
CNMOULD: Plastic Mould|Mould Company|Mould Maker ... - mould manufacturing compa
Author:gly Date: 2024-10-15
Micro molding is an advanced and highly specialized manufacturing method that can produce tiny plastic components with extreme intricate geometries. This process can manufacture parts weighing from 0.1gm to 1gm and tolerance levels of 10 to 100 microns.
Even while using 3d printed injection mold for the MIM process, most of the rules are similar to the plastic injection molding. But, here are some additions that engineers need to follow:
Improved Mold Clamping Mechanism Improving the mold clamping mechanism, such as optimizing heat transfer, can eliminate the non-parallelism of the template caused by temperature variations, maintaining the precision of the mold.
Additionally, the temperature of the mold is equally important, making mold temperature sensors a key to ensuring injection molding quality. Precise temperature control ensures that plastic materials are injected in their optimal state, leading to the production of products with stable quality and precise dimensions.
Needs Less Post-Production: Since the parts typically have good aesthetic post-production, you will typically need very little post-production. You can create an injection moulding tool with a unique finish that will be immediately visible on the finished product.
In practical applications, such as in the manufacturing of smartphone lenses, these precise controls and optimizations can significantly enhance product quality. For example, they can reduce the offset of the geometric center of the top and bottom surfaces, reportedly to less than 1.12um. The fine control of mold clamping accuracy in precision injection molding is key to ensuring products meet high-quality standards.
B-grade parts have a slightly rougher polish than A-grade parts due to the application of grit sandpaper. B-grade finished custom-moulded plastic components have quite a matte surface texture.
Several industries including, medical, automotive, and electronics manufacturing, require small injection molding processes to create minuscule parts. Following are some of the sectors using micro molding:
Industries use several rubber molding solutions to accomplish respective structure and properties in the final product. There are majorly three types of rubber molding that are:
High Detail: Under extremely high pressure, molten plastic is injected into the mould during the procedure. This forces the plastic firmly against the moulds, enabling the creation of detailed and complex shapes with lots of detail.
The rubber molding machine creates molded rubber parts by hard pressing a rubber's block into a molding metal cavity. When the rubber is exposed to heat, it activates a chemical reaction, and there are several variations in this process to achieve the desired quality. The most popular variation methods are compression molding, transfer molding, and injection molding.
To further enhance accuracy, some high-end molds are equipped with pressure and temperature sensors. These sensors can monitor key parameters during the injection molding process, such as pressure and temperature inside the mold cavity, and precisely control injection molding parameters to ensure product quality. This intelligent control not only improves product consistency and repeatability but also makes the production process more efficient and reliable.
Enhancing Template Rigidity Utilizing high-rigidity templates can effectively improve the stability and durability of the mold, reducing deformation during high-pressure injection molding.
Next, the powder is molded utilising the same machine and tooling that engineers use in plastic injection molding. But in this method, the cavities are 20% larger to manage the part shrinkage during the sintering process. In the process, the machine first melts the feedstock and injects it into the mold cavity, where it cools and gets the desired shape.
The precision of injection and holding pressure control can reach within 0.1Mpa, ensuring precise application of pressure and high-quality molding.
Through these high-precision design and technical means, the importance of mold accuracy in injection molding production is further emphasized, providing a reliable guarantee for the production of high-quality precision components.
In this process, engineers keep a fixed amount of rubber compound into the mold cavity and then compress it into the shape of the cavity by closing both sides of the mold. In this process, the pressure remains the same while the heat is added to cure the product. Once the process is complete, engineers remove the final product from the mold.
Using Large Linear Rails Employing large linear rails ensures the smooth and precise movement of the mold, thereby enhancing the accuracy of mold clamping.
Precision injection molding sets higher quality standards in multiple aspects compared to conventional injection molding. These include the application of high speed and high pressure, precise segmented control of speed and pressure, as well as precise temperature control. Additionally, in terms of screw design and mold clamping mechanisms, precision injection molding demonstrates standards that surpass those of conventional injection molding.
The final step of this process includes sintering the remaining part at high temperatures (up to 1350°C) to reduce the space by around 1% to 5%, and it results in a high-density metal part. The furnace leverages inert gas to attaint's temperature of about 85% of the metal's melting point. This process helps remove pores and causes the part to shrink by 80% of its molded volume. The final part retains the original shape with higher tolerance levels.
Being a leading provider of injection molding service, we offer a wide range of manufacturing services to OEMs. From gears to brackets, enclosures, knobs, pulleys, automobile parts, toy parts, robot parts, etc., we make thousands of molded plastic parts. We also offer an online injection molding service for which you just need to load your 2D or 3D CAD file on our website for an instant free quote. We provide free design assistance for our clients who needs alteration in the design of their product for Injection Molding.
The wall thickness should be minimal, and it should be uniform throughout the part production. Minimising the wall thickness helps in reducing material volume and sintering times.
In rubber transfer molding, the rubber compound is placed at a specific part of a mold called a pot before being pushed against a cavity to get the desired shape. Once the curing process is done, the mold is split while relating the product.
Extensive Material Support: Zeal 3D offers specialized 3D engineering services that cater to the client's needs and requirements using more than 45 different materials.
The foam injection molding machine then injected the material through the nozzle into the mold in a lower volume than the amount required to mold an object. Injection expansion and pressure of the polymer and gas then fills the mold. A porous surface is formed when the melt comes in contact with the cold surface of the mold. Then the foam injection molding expanding polymer mixture forms the cellular core.
High-end Service Provider: Zeal 3D, a provider of 3D engineering and modern digital manufacturing services, is dedicated to constantly providing products and customized services that satisfy customers' expectations and adhere to regulatory requirements.
Automobile plastic injection moulding is a crucial production technique in the automotive sector, where reliability, stability, and quality are of the highest importance. It is used to produce auto parts like,
Purchasing high-quality construction components, including injection moulded plastic building products and assemblies, is one of the keys to the success of architecture projects.
Typically, the mould's surface preparation is finished throughout the manufacturing process. After the injection moulding is accomplished, we will give the end product-specific surface treatments in accordance with your specifications. Some of the high-end surface finishes are,
In this step, the machine removes the polymer binder from the metal, and in many cases, engineers use solvent debinding to dissolve most of the binder. Once this step is complete, engineers perform the thermal debinding process. In this process, the molds are heated at a low temperature, and it helps in removing the polymer binder through evaporation.
In precision injection molding, the accuracy of mold clamping plays a crucial role in determining product quality. It requires the stationary mold (fixed template) and the moving mold (moving template) to have very precise repeat positioning, with the parallelism between them typically controlled within 0.06-0.08mm. To achieve such precision, several measures are adopted:
If you are launching a new automobile and need custom product designs, we have the best custom injection molding expertise and services. Our industrial plastic parts designs are also utilized by building and construction, food packaging, and medical industries. Whenever think about Injection Molding services, think of the largest plastic injection molding company in the world i.e Zeal 3D.
This process is ideal for producing high-volume small metal parts with complex geometric designs. Metal injection molding can efficiently create objects with thin walls. Engineers can use a variety of ferrous and non-ferrous alloys and get the desired material properties. Our metal injection molding machine offers a tolerance level of up to ± 0.005 in and Max wall thickness of 0.04 to 0.25 in.
Zeal 3D Services excels in plastic injection moulding, offering high-quality, cost-effective parts for industries like defence, automotive, medical, and aerospace. With advanced machines and expert skills, we provide comprehensive services, including free design assistance and instant online quotes. Trust Zeal 3D for all your injection moulding needs.
Zeal 3D's engineering department uses state-of-the-art CAM programming equipment to send tool path instructions to our machines that will produce your desired part accurately. The quality is tested using automatic testers that ensure dimensional specifications are maintained right on target without any change.
However, if there is a need to enhance the process accuracy of the injection molding machine as well, the challenge increases significantly. This would mean longer timeframes to resolve issues and increased costs. In short, the difficulty and cost of precision injection molding are closely tied to its accuracy requirements.
High-speed injection molding brings not only faster production efficiency but also higher injection pressure. This means that when using high-speed injection molding machines, one must confront challenges associated with high injection pressure. High-speed molding helps improve production efficiency and can effectively resolve certain defects in the injection process, such as flow lines and warping, thereby enhancing the overall quality of the product.
Zeal is a leading company offering you on-demand plastic injection molding services. Regardless of your industry, Zeal offers you full-fledged plastic injection molding solutions to cater to all your manufacturing requirements.
Zeal Injection Molding Services and plastic molding manufacturing services additionally offer its clients an extensive variety of auxiliary administration alternatives that incorporate machining, powder covering, silk screening, painting, and ultrasonic welding. Zeal Injection Molding Services utilizes the most recent machines to deliver high-quality plastic products.
Effects on Production Cost While ultra-high pressure can reduce the shrinkage of plastic products and enhance their density and weight, it also means increased energy consumption and greater mold wear, leading to higher overall production costs.
Mobile phone lenses, showcasing precision injection molding, incorporate advanced technologies to ensure high-quality production. Key techniques include:
Cost-Effective: Numerous copies of the same products can be produced. When you require parts with tight tolerances and high levels of dependability, injection moulding is the best option.
We have a wide range of materials available for injection molding. The selection of material from the wide range of different grades of these materials can be a challenging task but our team of expert engineers will help you to select the most suitable material for your application.
Most of the components used in the aircraft sector are manufactured using aerospace plastic injection moulding because of the number of advantages they provide.
Rubber molding is a molding process that manufactures usable rubber items produced from uncured elastomers or rubber. Elastomer is any rubber molding materials that have good resilience for returning to the original shape when applied.
In the manufacturing process known as plastic injection moulding, plastic in a barrel is heated until it melts, at which point it is shot into a mould to create a finished thermoplastic item suitable for production. We are experts at designing and producing a variety of plastic injection moulds tailored to specific tolerance and budget with our expertise and cutting-edge equipment.
2. Secondly, injection-molded products often exhibit various molding defects, such as bubbles, flow lines, white and black spots, and so forth. These defects not only affect the appearance of the product but can also weaken its performance. To avoid these issues, it’s crucial to strictly control multiple factors in the injection molding process, including the material, injection speed, temperature, and pressure.
With Zeal 3D services, we can support any of your injection molding needs and provide you with the best service and products at every step of your project. This ranges from design assistance to prototype verification or full-scale production, all by the highest quality standards.
Several industries including automotive, aerospace, and medical use robust metal parts manufactured using the metal injection molding process. Below are some of the commonly used metals used in MIM parts:
Application of Segmented Control Different product requirements necessitate varying injection speeds. Simple structures might need only one or two speed segments, while complex, high-requirement products may require multiple segments.
In precision injection molding machines, the design of the screw is particularly crucial. These machines typically use screws designed for low shear to reduce shear heat in the material, effectively preventing excessive material overheating. To meet this design requirement, precision injection molding machine screws generally have a larger length-to-diameter ratio, usually between 24-30, resulting in a more slender form. This design helps enhance the screw’s processing capacity and the uniformity of the material. Additionally, these screws need to operate at higher rotational speeds.
Temperature control is a crucial aspect of precision injection molding that cannot be overlooked. During the injection molding process, the temperatures of the barrel and nozzle need to be strictly controlled, often using a closed-loop control system to enhance precision. Currently, the temperature of the screw and barrel is frequently controlled using PID (Proportional, Integral, Differential) control, with an accuracy that can be maintained within ±1℃.
In this process, manufacturers utilize a standard injection molding machine, and the powder is melted before injecting into the mold. The powder cools down and solidifies into the desired shape during this process. After this, the heating process removes the unnecessary polymer to produce high-density metal objects.
Efficient High Production: The cost per part for large volume production runs is quite cheap. By employing plastic moulds rather than metal ones, you may save costs even for medium volumes, or between 10,000 and 25,000 pieces.
Injection speed is a crucial metric for assessing the performance of injection molding machines. Conventional injection molding machines typically operate at speeds around 100mm/s, while high-speed machines far exceed this range, reaching speeds of 300mm/s to 1000mm/s, with some models even achieving higher speeds and an acceleration of the plunger exceeding 20G.
Using a platinum catalyst, a thermoset method called liquid silicone rubber moulding heat-cures a two-component compound in the mould to create the finished object.
Strengthening Base Rigidity Using a high-rigidity base, such as one made from a single casting, can improve the stability and precision of the entire injection molding machine, maintaining high accuracy over long-term use.
The first step of metal injection molding is to form a powder mixture of metal and polymer, and the metal used in this process is much more refined (under 20 microns). The powdered metal is mixed with a heated thermoplastic binder, cooled, and then pulverised into a feedstock in pellets. The end feedstock consists of 60% of metal and 40% polymer.
In summary, precision injection molding is not just about dimensional accuracy. It also involves material selection, optimization of the production process, enhancement of equipment precision, and strict control of the production environment. Only by considering these factors comprehensively can we ensure the high quality and high performance of the final product.
Furthermore, to better accommodate high injection pressures, the screws in precision injection molding machines are often made of alloy steel, ensuring their strength and durability under high pressure. In contrast, screws in conventional injection molding machines are commonly made of stainless steel. Overall, the role of the screw in precision injection molding machines is vital, as its design and material selection directly affect the quality of the products and the efficiency of production.
In summary, precise segmented control of speed, pressure, and flow is an indispensable technology in precision injection molding. By finely adjusting these key parameters, product quality and production efficiency can be significantly enhanced, meeting the production needs of various complex and high-standard requirements.
Be it automotive, construction, computing, electrical, and electronics, Zeal offers clients a wide variety of molding processes to produce the best quality plastic products. We have a proven track record of supplying high-quality parts that meet each client's distinct requirements in terms of design, dimensions, and surface finish.
Therefore, without specific requirements, ultra-high-pressure injection molding technology is not typically adopted casually. Instead, the choice of injection molding machine should be based on the actual needs of the product and the cost budget. The selection in precision injection molding should consider an integration of product requirements, cost-effectiveness, and technical feasibility.
3. Additionally, controlling the wall thickness and the flow-length ratio is another challenge. Some products require very thin wall thicknesses, while others require thicker walls, posing higher demands on the precision of the injection molding machine. Especially when producing large or complex-shaped products, ensuring uniform wall thickness and flow-length ratio becomes a technical challenge.
Zeal 3D is an expert in injection molding and has the capacity to join fast prototyping procedures with ultimate ease. From high customization to complex design manufacturing, we do it all for you. We offer the best plastic mold manufacturing services for your every need. Search plastic injection molding companies near me and you will find Zeal to helping you about everything which you need to know about it.
By using different speeds at various stages of injection, one can optimize the filling process according to product characteristics and mold design, reducing defects such as weld lines, deformation, flash, and cracks, while also minimizing internal stress.
Metal injection molding process consists of four significant production steps that turn powder from raw materials into a robust solid object. The process has the following steps:
1. Firstly, controlling dimensional accuracy is a technical challenge. This includes the tolerance of part dimensions and geometric dimensioning and tolerancing (GD&T). This is primarily due to the shrinkage of plastic products during injection molding, which can also cause warping and lead to deviations in shape.
C-grade finishes provide a rough, uneven surface using grit sanding stones. C-grade finished injection plastic components have a matte surface texture.
When precision injection molding is mentioned, many people first think of the accuracy in product dimensions. Indeed, ensuring dimensional accuracy is a core element in precision injection molding, but that’s not all there is to it. In the process of precision injection molding, we are faced with a series of challenges and tests.
Metal injection molding is an advanced variation of conventional plastic injection molding that allows engineers to perform fabrication of solid metal parts. In this metal molding process, the raw material called feedstock is the powder of metal and polymer.
Zeal 3D Services offers comprehensive services for prototyping and producing parts through a plastic injection molding process. We have advanced plastic moulding injection machines, skills, and experience to design and manufacture injection-molded plastic parts. Our plastic injection molding services are suitable for a variety of industries for designing and manufacturing high-quality plastic products for both high-volume and low-quantity parts production. We manufacture and supply durable, functional, and cost-effective plastic injection molded products defence, automotive, medical, aerospace, and consumer industries. We are among the best plastic injection molding companies that offer an amazing range of services for the Australian and overseas markets.
One of the many industries that manufacture parts using the plastic injection moulding technique is defence. The injection moulding process is used in numerous applications in the defense sector for creating desired end-products.
Precision injection molding machines are typically equipped with high-precision displacement sensors, ensuring speed control accuracy within 0.1mm, covering a wide range from very high to very low speeds.
High-Quality Assurance: In order to reach the highest level of customer satisfaction, Zeal 3D makes a significant effort to ensure quality assurance and continuously delivers high-quality goods with strict tolerances.
Australia Wide Fastest Delivery: In Australia, including Melbourne, Perth, Sydney, Brisbane, Canberra, Adelaide, Tasmania, and New Zealand, Zeal 3D offers the quickest delivery options for 3D metal printing.
Zeal 3D is among the leading metal injection molding companies that cater to all your bespoke manufacturing requirements with ease.
Role of Pressure Sensors Pressure sensors can be installed in multiple locations on the injection molding machine, such as the nozzle, hot runner system, cold runner system, and mold cavity, to measure and control the plastic pressure in real time. These data can be recorded and adjusted in real time, ensuring the appropriate pressure at each step, reducing defects, and facilitating post-molding inspection and troubleshooting.
There is a wide range of rubber molding materials available in the market to accomplish different tasks. Some of the popular ones are:
Micro-injection molding products represent the pinnacle of precision molding technology. As products become increasingly miniature, the demands for their accuracy intensify. This technique requires extremely high machining precision and advanced equipment support to ensure that each tiny component meets the expected dimensional and functional standards. In this field, even the smallest improvement can significantly enhance product performance.
By using this form you agree with the storage and handling of your data by this website. And agreed to get promotional emails.
The foam molding process is an ideal process for producing high-strength, lightweight parts. Many large-sized objects require thick walls than conventional injection molding, making the production more accessible. The structural foam brings a quick turnaround while working with thicker parts.
Manufacture At Any Scale: Zeal 3D works with manufacturers to create tools and equipment in any quantity, from 1 to 10,000 pieces, enabling high or low-volume manufacturing at the most competitive pricing.
It is an ideal method for producing tiny components with higher design precision and accuracy. This mini injection molding begins with creating smaller cavities to form the desired shape. Resin or thermoplastics are rapidly injected into the cavity to form components at a higher speed.
For products and materials with special requirements, precision injection molding machines often use specialized screws, while conventional injection molding machines tend to use more general-purpose screws.
By using this form you agree with the storage and handling of your data by this website. And agreed to get promotional emails.
However, the specific precision injection molding techniques required vary for different products. The principles discussed in this article are just basic guidelines. A deeper understanding and application of precision injection molding require analysis and research based on specific product cases. This means that precision injection molding is not just a fixed set of technical specifications but a complex process that needs to be flexibly adjusted and optimized according to specific application scenarios.
Accuracy of final injection molded products depends upon the various factors like material, tooling, the geometry of the product, and surface finishes. The possible tolerance of most thermoplastic is ±0.2 to 0.5mm.in few specialized applications tolerances are low as ±5 µm on both diameters and linear features are achieved in mass production Surface finishes of 0.0500 to 0.1000 µm or better can be obtained. Rough or pebbled surfaces are also possible.
Impacts on Plastic Molds Ultra-high-pressure injection molding imposes stringent requirements on molds. Not only do molds need to have smaller gaps to prevent flashing, but they also require higher processing precision and a good venting system. Moreover, the wear and tear on molds increases, necessitating higher hardness and wear resistance, which directly raises the manufacturing costs of the molds.
Zeal 3D is a leading rubber and silicone injection molding company that brings in the complete range of molding across industries.
No MOQ Needed: Without needing a minimum order quantity, our staff will make the required effort to locate the supplies if you need manufacturing services utilizing materials that are not on the material list.
Another benefit of leveraging this technology is that it's a very cost-effective molding process that produces robust products. With minimum warpage, the parts have superior durability.
In mold manufacturing, the use of high-precision techniques such as high-speed milling, slow wire EDM (Electrical Discharge Machining), and mirror EDM ensures the quality and accuracy of mold processing. These methods eliminate the need for additional manual grinding or complex fitting processes. They make the mold surface smooth and highly accurate in fitting, effectively preventing defects like flash, even under high injection pressures.
Multi-stage Holding Pressure Strategy The holding pressure in injection molding is typically divided into several stages:
While performing sintering, the MIM parts need robust support, or the parts will get distorted as they shrink during the process. Engineering can use standard flat support trays or use custom supports if required.
In some demanding injection molding processes, conformal cooling technology can cool products more precisely and efficiently. This technique uses special cooling channels inside the mold that closely conform to the shape of the product, achieving rapid and uniform cooling. This ensures dimensional accuracy of the product and improves production efficiency.
Conclusion: Although ultra-high-pressure injection molding is a method to achieve precision in injection molding and indeed can provide higher dimensional accuracy and product quality, it comes at the cost of higher production expenses and technical demands.
Grading of Injection Pressure The pressure in conventional injection molding machines typically ranges between 147~177Mpa, whereas precision injection molding machines operate at higher pressures of 216~243 Mpa, and even ultra-high-pressure injection molding machines can reach 243~392 MPa. Ultra-high-pressure injection molding greatly enhances the dimensional accuracy of the product by reducing the shrinkage rate to almost zero, but it also places higher demands on both the molds and the machines.
Sometimes, merely enhancing the precision of injection molds is not enough to meet the product requirements. In such cases, precision injection molding machines are employed to improve product quality.
Low Waste: In comparison to several other manufacturing techniques, injection moulding generates a very little amount of waste. Even if there is any leftover or trash plastic, it can be recycled and used again.
Accurate control of speed, pressure, and flow in the injection molding process is key to ensuring product quality. Segmental control of these parameters allows full utilization of their advantages and compensates for deficiencies, especially when dealing with complex or high-requirement products.
High-Precision Nozzle Contact Mechanism Optimizing the nozzle contact mechanism prevents movement of the stationary mold caused by nozzle contact during the injection process, ensuring injection accuracy.
We are proud of being one of the top custom injection molding suppliers for manufacturers whose injection molding cost is lower than any market. Our team is skilled in producing high-precision and durable plastic injection molded parts. We work with advanced machines to handle our customers' needs for injection-molded parts from low to moderate, and large quantities in any 2D and 3D shapes. Whether you want to turn concepts into reality, enhance product design, or conduct injection molding and testing, we can provide a high degree of precision and aesthetic appearance to meet international standards.
This is a sample text. You can click on it to edit it inline or open the element options to access additional options for this element.
Injection molding is a robust manufacturing process used to make an enormous variety of products. It is a large-scale production method that is cost-effective for mid-volume production runs. In addition, it gives the manufacturer the ability to create complex items with fine detail accurately and efficiently. It is why injection molding has become so popular recently, as manufacturers are increasingly looking towards innovative processes to stay competitive in today's global market.
This process offers several advantages to manufacturers. To begin with, it is a highly versatile process for manufacturing all kinds of plastic parts. It is ideal for producing items that range in size from fractions of millimetres up to several metres in length and creating them with amazing intricacy and detail.
By using this form you agree with the storage and handling of your data by this website. And agreed to get promotional emails.
Generally, high-precision molds use hard materials with a hardness above HRC48, such as H13, S136, SKD61, 1.2344, etc. These materials not only ensure the durability and stability of the mold but also maintain high precision over long-term use, making them suitable for producing precision parts.
Plastic injection molding is a faster and low-cost manufacturing process for quality and functional plastic products for a variety of uses across all industries. Our designers are experts in creating 3D CAD models with complex features and using laser-based rapid prototyping methods. We recommend all our clients to get injection molding to test fitting and functionality before going for production. Easy testing, assembling, and manufacturing are various advantages of rapid prototyping.
Grit and dry glass beads are used in D-grade finishes to provide a highly rough textured finish. Products might have a smooth or dull finish based on the type of material utilized.
Two-part injection moulding techniques called overmolding and insert moulding combine one material with a secondary substrate part or metallic insert to produce a single component. Our overmolding process shortens assembly time and increases the strength and flexibility of your parts by covering plastic, metal, and rubber over one another via chemical bonding.
Zeal 3d is a leading micro injection molding company that caters to all industrial requirements with higher accuracy and shorter turnaround time.
Unlike the traditional plastic molding process, MPM parts don't require any draft. The polymer binder that is used in the powder material releases quickly from the mold.
Effects of Injection Pressure One common issue with ultra-high-pressure injection molding is the potential backflow of molten plastic within the screw, which can degrade the quality of the plastic and the performance of the injection molded parts. To prevent this, ultra-high-pressure injection molding machines might adopt separated injection screws and plungers or special non-return valves. Additionally, higher injection pressures require greater clamping force, especially for larger-sized products.
An injection moulded part's shiny and glossy surfaces are produced by A-grade finishes, which are created by involving a buffing process.
These technologies not only improve the lens quality but also demonstrate the manufacturing industry’s focus on precision and reliability.
If only an improvement in mold accuracy is required, and standard processes of a regular injection molding machine are used, it might suffice for the product’s requirements. This approach is usually less costly and less complex.
However, not all products are suitable for high-speed injection molding. The appropriate injection speed depends on the specific requirements of the product, including material properties, design complexity, and quality standards. Higher speed is not always better; the right speed selection should be based on a comprehensive consideration of product characteristics and production needs.
There are significant differences between precision injection molding machines and conventional ones, and these differences directly impact the quality and cost of the products.
The foam injection molding process is a low-pressure injection molding process in which the machine introduces inter gases into the melted polymer to reduce the density of the product. The structural foam molding creates products that have cellular cores surrounded by integral and rigid skin. While making the homogenous mixture of polymer and gas, engineers use foaming agents, including NI, CO2, or CBA.
In this process, the rubber is heated to a liquid stage before injecting it into the mold. The final product is obtained by opening the mod and then closing it to get the following injection process for producing molding rubber.
GETTING A QUOTE WITH LK-MOULD IS FREE AND SIMPLE.
FIND MORE OF OUR SERVICES:
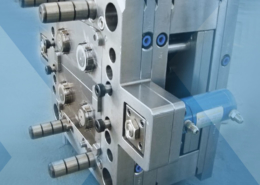
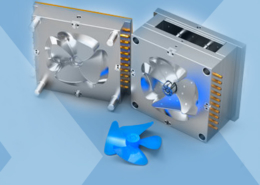
Plastic Molding

Rapid Prototyping
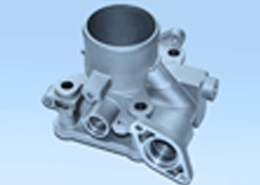
Pressure Die Casting
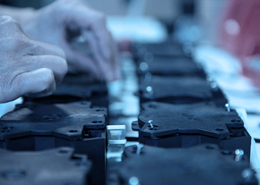
Parts Assembly
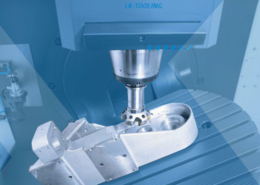