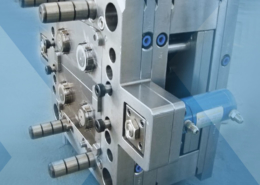
Exploring the Advantages of Metal Molds for Plastic
Author:gly Date: 2024-06-08
Metal molds for plastic injection molding are the backbone of modern manufacturing, offering a wide array of benefits and applications across industries. In this comprehensive examination, we delve into the world of metal molds for plastic, uncovering their advantages, applications, and potential for innovation.
Introduction to Metal Molds for Plastic
Metal molds for plastic injection molding represent a sophisticated manufacturing solution that enables the production of high-quality plastic parts with precision and efficiency. Unlike traditional molds made of materials like aluminum or epoxy, metal molds are crafted from durable metals such as steel or stainless steel, offering superior durability, longevity, and performance. Metal molds are widely used in various industries, including automotive, aerospace, medical, and consumer electronics, where precision and reliability are paramount.
The Evolution of Metal Molds
The use of metal molds for plastic injection molding has evolved significantly over the years, driven by advancements in materials, design technologies, and manufacturing processes. Today, metal molds are engineered to withstand high pressures, temperatures, and wear, allowing for the production of complex parts with tight tolerances and intricate geometries. From single-cavity molds to multi-cavity tools, metal molds offer versatility and scalability to meet the diverse needs of manufacturers.
The Importance of Material Selection
The choice of material for metal molds is critical to their performance and longevity. Steel alloys such as P20, H13, and S136 are commonly used for their excellent wear resistance, thermal conductivity, and machinability. Stainless steel is also favored for its corrosion resistance and ability to maintain dimensional stability over time. By selecting the appropriate material based on the specific requirements of the application, manufacturers can optimize mold performance and maximize the return on investment.
Advantages of Metal Molds
Metal molds offer a myriad of advantages over other types of molds, making them the preferred choice for many manufacturers seeking precision, reliability, and efficiency in plastic injection molding processes.
Enhanced Durability and Longevity
One of the key advantages of metal molds is their exceptional durability and longevity. Unlike aluminum or epoxy molds, which may wear out over time and require frequent replacement, metal molds are designed to withstand the rigors of high-volume production with minimal maintenance. This results in lower tooling costs and downtime, as well as improved production efficiency and overall profitability for manufacturers.
Improved Surface Finish and Part Quality
Metal molds provide superior surface finish and part quality compared to other types of molds. The smooth, polished surfaces of metal molds minimize surface defects such as sink marks, weld lines, and flash, resulting in parts with pristine aesthetics and dimensional accuracy. This is especially critical in industries where appearance and precision are paramount, such as automotive, consumer electronics, and medical devices.
Applications Across Industries
Metal molds for plastic injection molding find applications across a wide range of industries, where they play a critical role in the production of components and products that shape our daily lives.
Automotive Industry
In the automotive industry, metal molds are used to produce a variety of components, including interior trim, exterior panels, and under-the-hood parts. The durability, precision, and efficiency of metal molds make them well-suited for high-volume production of automotive parts with complex geometries and stringent quality requirements.
Medical Devices
In the medical device industry, metal molds are essential for producing critical components such as syringes, IV catheters, and surgical instruments. The precision and repeatability of metal molds are crucial for ensuring the safety and efficacy of medical devices, where even the slightest deviation can have serious consequences for patient health.
Future Directions and Innovations
As technology continues to advance, the future of metal molds for plastic injection molding holds exciting possibilities for innovation and optimization.
Advanced Materials and Coatings
Advancements in materials science and surface coatings are expected to further enhance the performance and longevity of metal molds. New alloys with improved wear resistance, thermal conductivity, and corrosion resistance will enable manufacturers to push the boundaries of mold design and production, while innovative coatings such as diamond-like carbon (DLC) and plasma nitriding will offer enhanced surface properties for improved part quality and performance.
Smart Manufacturing and Industry 4.0
The integration of smart manufacturing technologies and Industry 4.0 principles into metal mold production processes will revolutionize the way molds are designed, manufactured, and maintained. From real-time monitoring and predictive maintenance to digital twins and cloud-based analytics, these technologies will enable manufacturers to optimize mold performance, reduce downtime, and improve overall production efficiency.
Conclusion
In conclusion, metal molds for plastic injection molding represent a pinnacle of precision engineering and manufacturing excellence. With their exceptional durability, reliability, and performance, metal molds enable manufacturers to produce high-quality plastic parts with unparalleled precision and efficiency. As we look to the future, ongoing advancements in materials, technologies, and processes will continue to drive innovation and optimization in metal mold production, opening up new possibilities for manufacturers to push the boundaries of what is achievable in plastic injection molding.
GETTING A QUOTE WITH LK-MOULD IS FREE AND SIMPLE.
FIND MORE OF OUR SERVICES:
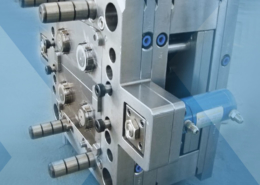
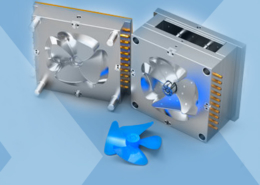
Plastic Molding

Rapid Prototyping
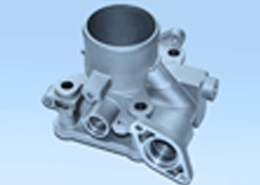
Pressure Die Casting
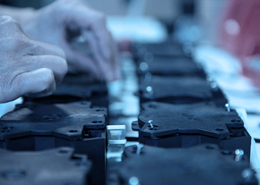
Parts Assembly
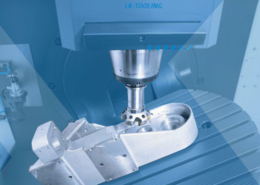