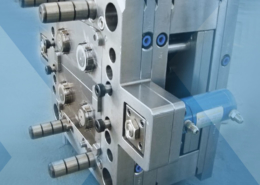
"Choosing the Right Polishing Method for Your Injection ... - injection mold pol
Author:gly Date: 2024-10-15
Moreover, we rely on various scientific methods, moulding process technologies, and analytical tools to provide custom plastic injection moulding. It allows us to meet the performance and precision needs for complex plastic components and applications. We have experience in specialised, complex design, engineering and support and can perfectly align with your specific project needs.
Overall, several factors can lead to the occurrence of short-shot defects, and they all have mutually limiting and influencing effects. Manufacturers must consider how these factors relate to one another, in order to devise a solution to reduce and correct short-shot defects. Note that It is often an ongoing process of monitoring and reviewing.
Generally, making an injection mould can cost between $10,000 to $100,000. But the cost varies depending on several factors. As plastic injection moulders, we consider many things before estimating the final price, including your order size, part complexity, labour cost, and specifications.
Nozzles, sprues, runners, gates, and thin product walls are among the parts that could obstruct melt flow. By raising the nozzle's diameter and temperature, besides utilizing a nozzle with a low flow resistance, the flow resistance of the nozzle can drop to the desired level.
Additionally, because the filling speed is excessively high, chances are that there is insufficient time to release the air via the separating surface.
Coming up with a design idea – A design idea doesn’t involve sketching up your vision but also other factors like your material preference, the environment in which you will use the product and the factors that can affect its performance, tolerance requirements etc. You can get a consultation regarding all these factors.
It offers more advantages than metallic products because of its lighter, stronger, superior, and long-lasting characteristics.
Short shots are one of the most frequent problems with plastic injection molding. There are numerous causes of them, but the primary ones are improper injection pressure and speed, including uncontrolled pressure loss brought on by resistance.
Moreover, as one of the leading plastic injection moulding manufacturers, we can develop game-changing prepositions for your business to support you throughout your journey. So, whether you want plastic product design, prototyping samples, injection moulding, mould design, mould manufacture, or plastic optimisation, we are your one-stop destination.
A "short shot," as the name suggests, occurs when the mold-forming filling stops before the mold chamber is fully filled with the melt, leaving holes or thin sections and producing a defective product.
In plastic injection molding, a flow hesitation occurs when the flow slows down or stops due to variations in mold thickness. Inconsistent mold thickness causes the flow range of the melt to be too broad and its flow resistance to be excessive.
The injection moulding process involves using an injection moulding machine, raw plastic material, and a mould. First, the raw plastic material is melted in the injection moulding machine. It is then injected into the mould. Here it is allowed to cool down and get solidified into the final part.
These holes frequently appear around the borders of the finished product or in areas where the mold wall is typically thin—these areas are the last places a mold would commonly fill.
Our team specialise in all aspects of product manufacturing. As a family owned business, we are focused on manufacturing and supplying high quality plastic injection moulded products for local Australian markets, and have been doing so for over six decades.
For more information about our manufacturing capabilities and services, get in touch with our team today. Fulfil your need for specialised moulding and product design with Sneddon & Kingston.
Injection moulding can be an expensive affair to set up, but it will prove to be a cheaper deal over the long run. In addition, it works best for large production volumes. You can speak to our consultant to discuss your requirements and the cost of injection moulding.
There are a variety of tools, procedures, and materials available for manufacturers to avoid short-shot defects. Four of the most tried-and-tested remedies are listed below:
Manufacturers can immediately notice that the choice of material affects the flow or movement of the molten plastic inside the mold chamber in the mold cavity because it is a recurring factor in many problems.
Custom plastic injection moulding is the process that helps create a unique mould. It involves listening to your particular requirements and selecting material based on your specification, and production of plastic parts or products to meet your specific needs.
Therefore, you can rely on us for mass-producing plastic components. We use a reliable and economical process to produce high-quality components with great dimensional consistency.
Flow restrictions, hesitation of flow, and inadequate venting are all common short-shot defects due to inadequate mold design. Flow restrictions often come from the positioning, dimensions of runners and their gates, and how the molten plastic is poured into the mold.
As specialist plastic injection moulders, we design, optimise, manufacture and supply plastic injection moulded products. We meet the injection moulding requirements of high-quality engineered plastics. Our plastic injected moulded products provide an ideal replacement for heavier metal items.
For instance, an oversized machine may have trouble controlling pressure if the shot size is less than 25% of its capacity, whereas an undersized machine will not have enough pressure or ram speed. Meanwhile, the barrel and mold wall should be heated to prevent the molded plastic from cooling too quickly.
Moreover, customised plastic components provide an ideal alternative for industries seeking to mass-produce high-quality, cost-effective parts. It is because they employ the moulds to replicate an item thousands of times.
Our primary services include plastic product design, prototyping for industrial interests, tooling manufacture and plastic injection moulding in Melbourne. If you would like to discuss your next project with our team, give us a call.
With many accumulated years of experience with numerous domestic and foreign clients, Flying Tiger is confident in assisting corporate customers in quickly identifying the cause of short shots and other injection molding defects, thereby assisting in cutting down on resource waste and boosting product yield.
The production line might have a resin with a high viscosity measured by the Melt Flow Index (MFI), depending on the chosen material. MFI is a good starting point, even though it may not tell the complete story since there are two other factors of concern that may also be involved.
Like any production process, plastic injection molding manufacturing can have problems and faults. Short shots, often known as "shorts," are one of the most typical quality concerns when the final product is incomplete because the mold did not entirely fill. This article will examine the most frequent causes of this issue and how plastics manufacturers can troubleshoot short shots to maintain high-quality and lean production.
Prototype Building – Building a prototype is the final step before the production procedure. It reveals possible problems in real-world applications. Thus, it allows you to hone your designs and determine the functionality and efficiency of the plastic part.
The plastic injection moulding technique necessitates incredible accuracy with maximum flexibility. This method has benefited many industries as the technology is used to produce products of different types and sizes for various purposes. Its application can be found in multiple industries like automotive, infrastructure, medical, food packaging, aerospace, household appliances, building and construction, etc.
Injection Moulding Breathes Life into Australia’s Specialist Food Market! Since the turn of the century, food packaging has undergone a quiet transformation. Partly driven by…
Sneddon & Kingston are industry professionals when it comes to plastic injection moulding in Melbourne, Sydney and all of Australia. We have the technical proficiency, the industry experience as well as access to modern facilities with automated processes to mass produce quality plastic products for various industrial needs.
The imbalanced flow in each cavity of a multi-cavity mold can generate local short shots. But when the injection molding machine's capacity is adequate, this defect is primarily brought on by the uneven flow in each gate or the uneven distribution of the mold cavities.
As one of the leading plastic injection moulding manufacturers, we can help you with a quality injection moulding process.
We consistently achieve exceptional customer satisfaction through our seamless service and innovative ways to manage processes, products, and requirements. In addition, our business insight and keen eyes for detail allow us to understand market dynamics and customers’ expectations.
It appears we’re not the only ones excited about securing our latest contract for Australia Post’s new letter trays, with the Herald Sun publishing the…
Raw plastic material melting. Injection of the molten material into a mould. Cooling of the molten material into a solid state. Removal of the hardened material from the mould.
The secret to effective manufacturing and preventing either flow or pressure concerns is to match the right part with the proper molding machine.
As a leading plastic injection moulding in Australia, we have expertise in all aspects of the processes involved in plastic product manufacturing. We are known for producing superior quality tooling designs and products. In addition, we adhere to strict process and quality control systems to ensure quality service and products. Therefore, you can rely on us for design consultation, production, and distribution.
Therefore, it is squeezed instead, leaving some partially empty spaces in the cavity and shortening the shot of the molded item. To remove the air, the process must have vents built or ejection pins installed.
Overall, it is crucial to comprehend the various varieties of plastic injection molding equipment and how varying sizes and types might be beneficial.
The most frequent cause of failure to fill the mold is the appearance of something that interferes with the flow, and one of the leading candidates for flow issues is the type of plastic polymer itself.
Learn more about our plastic injection moulding capabilities in Preston, Melbourne. We continuously invest in the most advanced processing technologies and optimise our techniques in manufacturing to ensure that we remain agile and competitive in the marketplace.
It has been a long year now; we have been helping our clients turn their design ideas into finished products. Hence, you can contact us to discuss.
Sneddon & Kingston Plastics is a Melbourne based company specialising in custom injection moulding. For over 60 years we have been a highly regarded and steadfast company supplying to many industries around the world.
Therefore, beyond the choosing material, better control of mold and melt temperatures also aids in enhancing plastic flow. Flying Tiger offers a range of mold temperature controllers that help you achieve just that.
Poor venting happens when air is trapped during filling the cavity, creating counterpressure. When the melt is first injected into the hollow, under most circumstances, it immediately seals the cavity, trapping air in the remaining local spaces.
With us, you rest assured that we will never pursue your custom injection moulding projects at the cost of material selection, part design, mould design and process control. On the contrary, we take utmost care of these key stages of the product development process to accurately achieve the type of product design you want from us. It also allows us to make you achieve your business goals.
Today, plastic injection moulding has become one of the most widely used plastic forming processes. It is known for having a wide range of manufacturing applications. In addition, the injection moulding process has many advantages, like customisability, high efficiency, speed, and affordability, which makes it different from other moulding and casting methods.
Choosing an appropriate manufacturing process – There are three main ways to manufacture a plastic part: injection moulding, CNC machining and additive processing. You will have to choose the most appropriate process depending on your requirement and budget.
The team at Sneddon & Kingston provide plastic injection moulding in Melbourne for various industrial sectors throughout Australia. We provide manufacturing solutions for; water filtration, food packaging, industrial packaging, automotive, construction, medical and pharmaceutical niches and so much more.
Another potential reason is that the vacuum condition is not suitable for molds—Molds require a place for displaced air to escape, or they will develop air traps or poor venting.
Consult Flying Tiger today if your business is looking for a partner to co-create reliable, high-quality manufacturing outputs.
GETTING A QUOTE WITH LK-MOULD IS FREE AND SIMPLE.
FIND MORE OF OUR SERVICES:
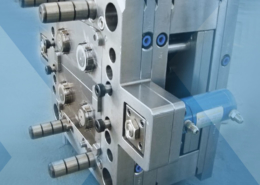
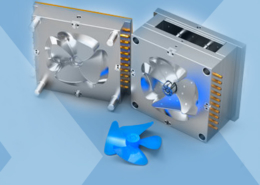
Plastic Molding

Rapid Prototyping
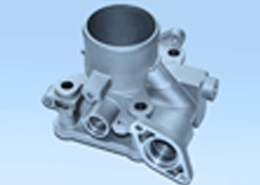
Pressure Die Casting
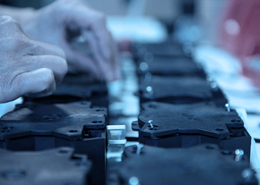
Parts Assembly
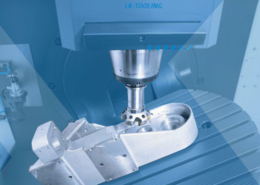