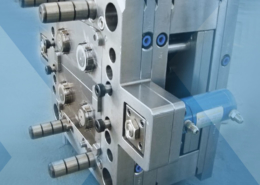
China Largest Injection Molding Companies Manufacturers ... - large plastic inje
Author:gly Date: 2024-10-15
Below is a cost comparison between Nylon, ABS and Polycarbonate (PC) for a simple injection moulded part. The table/graph also compares how the number of parts ordered affects the price and lead time.
Request your free injection moulding quote today and one of our engineers will personally review your project within 24 hours. They will then help fine-tune your project to make sure you get the best possible price and lead time for your injection moulding project.
Optimised for mass production of plastic items, our services in Plastic Injection Moulding are backed by deep expertise and industry-leading knowledge.
LorAnn sells several types of candy molds: hard plastic molds, hard plastic two-piece molds, and plastic sheet molds. The only types of candy molds that are not suitable for hard candy use are the flexible rubber molds (these are used to make cream cheese and butter mints), and the clear plastic chocolate & soap molds.
Aluminium extrusion is ideal for both single prototypes and large-scale production, offering bespoke, high-standard, consistent cross-sectional profiles.
Ready to see how much your part costs to manufacture? Request a free Injection moulding quote today, and one of our engineers will review your project within 24 hours.
For Nylon, going from quantity of 500x to 5000x has a 88% total cost per part saving for a simple injection moulded part. For volumes around 500x and below, it can often be cheaper to CNC machine or 3D Print the parts depending on the design. This is because the high tooling costs are spread over a smaller number of parts, making each part more expensive. Going from 5000x to 50,000x sees an additional cost saving of 9%. This demonstrates how increasing the part quantity significantly reduces part cost for smaller volume orders. However, as the order quantity increases, the reduction in unit price becomes less but still significant.
If you want to know more about materials options for your injection moulding project, read our article about choosing the right Injection Moulding material.
Insert sucker stick into mold*, making certain that one end extends to about the middle of the mold cavity. Pour candy into mold and allow to harden. Do not refrigerate. Your suckers should pop-out of the molds easily when the candy has hardened.*If using a two-piece plastic mold, prepare as instructed above and attach pieces together with clips provided. Pour candy into molds, and then add sucker sticks.
Choose our CNC Turning services for circular cross sections. We also offer Turn & Mill capabilities for more complex turned parts.
In this article Get It Made simulated the production for two different parts, a very simple small part, and a more complex larger part. You can see how prices vary between different common injection moulding materials and part quantities moulded.
It is essential that the design of the injection moulded parts are carefully reviewed before production. Removing unnecessary features from the parts will make the tooling easier to machine. Read our Injection Moulding Design Guide to optimise your parts and get a better price for your project.Â
The data shows a slightly different trend for a larger, more complex injection moulded part than the simple/smaller one analysed above. There is a saving of 79% going from 500x to 5000x in nylon and a further 12% going up to 50,000x. This shows that there are still substantial cost savings in manufacturing into the high thousands for larger, more complex parts. The price for 500x is comparable to 3D Printing as the tooling cost is a relatively smaller proportion of the unit cost than the small/simple injection moulded part.
Other alternatives include cutting the warm candy with well-oiled scissors or pouring the candy into a cookie sheet filled with powdered sugar and then using scissors to cut the warm candy. Using powdered sugar has two advantages: one is that the candy seems to stay warm and pliable for a longer period of time, and two - the powdered sugar acts as a cushion resulting in the cut candy being pillow-like instead of flat.
Tooling is often a key part of the economics in plastic injection moulding, this is because it is a large up-front investment. And this cost needs to be amortised into expected part volume, over a number of years. If injection moulding isn't suitable, it is very possible 3DÂ Printing or CNCÂ Machining could be a better option. Depending on the parts' features, the machining of a complex mould will require more time and expense, increasing the upfront costs of the project. This is the main reason why injection moulding is mainly used for high volumes.
For hard candy use, all molds need to be prepared before use. Hand wash all molds in warm, soapy water and dry thoroughly. After the molds have dried, lightly spray the mold cavities with cooking spray (we recommend PAM). If too much cooking spray accumulates in the cavities, simply wipe off the excess with a paper towel.
Instead of using molds, you can pour your hot candy onto a greased cookie sheet or other heat-resistant surface, then when the candy has cooled slightly, score it into a checkerboard pattern with a sharp knife. When the candy cools, it can be broken into small, square pieces.
The data again indicates that ABS is the most cost-effective to manufacture in out of the three materials, while polycarbonate is the most expensive. With an increase in quantity from 500x to 50,000x, the lead time only increases by a few days. This is primarily because most of the lead time in an injection moulding project is manufacturing the mould and sampling. Once the mould successfully produces parts to the desired specifications, the parts can be produced rapidly.
Injection moulding is a manufacturing process often used to produce high volumes of plastic parts. This manufacturing process starts by creating and machining a mould with precision to form the partâs features. Then molten plastic resin is injected into the metal mould cavity. The plastic moulded parts subsequently cool and are ejected from the mould cavity. If you want to know more about the injection moulding process, read our Injection Moulding Guide.
Below is a cost comparison between Nylon, ABS and Polycarbonate (PC) for a complex injection moulded part. There is also a comparison of how the price and lead time change according to the number of parts ordered.
Get It Made was founded in 2011 with a mission to make manufacturing simple. Based in London, UK, Get It Made provides outstanding manufacturing services to companies across the globe.
With many years of experience, sheet metal parts can be a great low-cost option for certain high and low-volume applications.
When comparing the three materials, the data shows that ABS is the cheapest material to manufacture with, and polycarbonate is the most expensive. The lead time only increases by a few days going from 500x to 50,000x. This is because the bulk of the lead time for an injection moulding project is manufacturing the mould and sampling. Once the mould produces parts to specification, part production is very fast.
Our 3D printing solutions cater to personalised needs with a diverse range of materials and colour options, perfect for intricate plastic components and small batches.
In general, injection moulding tooling can cost from £2k to £100k. Costs for moulded parts can range from a few pence to a hundreds of pounds each.
However, once you have the moulding tool, the plastic moulded parts will have a very low unit cost. And the tooling is usually CNC machined from a high quality steel, allowing more than one production run using the same tool, so it will last many years.
GETTING A QUOTE WITH LK-MOULD IS FREE AND SIMPLE.
FIND MORE OF OUR SERVICES:
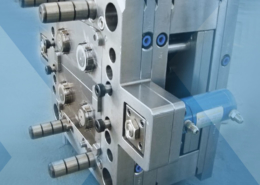
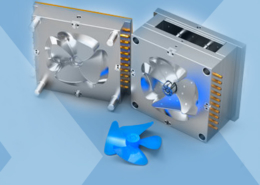
Plastic Molding

Rapid Prototyping
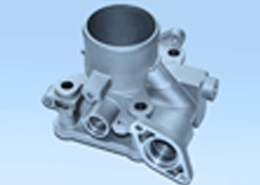
Pressure Die Casting
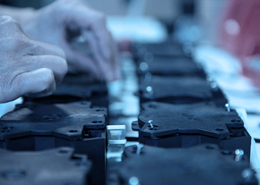
Parts Assembly
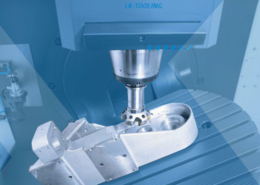