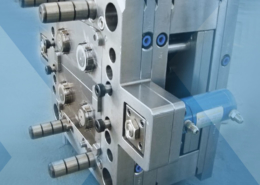
Chen Hsong International Injection Molding Machine ... - injection manufacturers
Author:gly Date: 2024-10-15
It provides an inherent space for polymers to form their orientation stresses (both initial and residual) in a way that the orientation stresses are not only symmetrical to center line of part thickness layer to layer, but are also with same distributed proportions on different levels of orientation stresses across part thickness everywhere at the whole molded part, reducing the risk of part deformation and warpage caused by different amounts of local residual stress relaxation after part ejected.
(4) As much as possible, set injection speed for part filling with only one-stage to reduce the complexity of initial orientation stress distribution across the whole part.
KSNP PRABHU In the comment area of my latest post, you mentioned that you experience flow instability in long & big parts end up at times facing issues such as tiger stripes, which I think more proper to discuss along with this article. When the melt in the part cavity flows across the local area in an unstable speed, such as fast-slow-fast-slow or flow-stop-flow-stop pattern, the tiger stripes could appear. Therefore, the key to dealing with this issue is to ensure a consistent linear melt filling velocity across the concerned areas. This issue should be the consequence of an uneven part thickness design, an imbalanced positioning designs in mold runner/gate/cooling channel, or an unnecessarily multi-step-profile injection molding condition. If you have a simulation software and can correctly model the part/mold design systems, you might be able to evaluate the probability of this issue by the melt front advancement contours from the Cool-Fill analysis output.
The difference of filling velocity differential from layer to layer causes different degree of shear effect from layer to layer as well, resulting in different degrees of polymer orientation along the filling direction and polymer stretch conditions layer to layer respectively. From individual polymer point of view, Fig. 2 illustrates the comparatively different polymer stretched conditions layer to layer from mold walls (part surfaces) inwards to the center of part thickness while polymer melt is filling in mold cavity. From polymer group point of view, Fig. 3 illustrates the comparatively different polymer groups with different stretched conditions layer to layer across part thickness. And Fig. 4 more realistically illustrates what the micro-structure of a filled part looks like at cross section parallel with filling direction in injection molding process, which is composed of unstretched polymers at central region and more or less stretched polymers from near central region outwards to part surfaces.
Fig. 3 also represents the condition of polymers being stretched right at the instant when polymer melt filling stage finishes. At that time, the stretched polymers are at tensile stress conditions and that is the so-called orientation stress (or flow stress, filling stress). Right after the instant when polymer melt stop filling, the force that drives polymers to orient and stretch is gone and the stretched polymers tend to release back to their original unstretched and curly conditions before they solidify during cooling stage. However, the possibility is quite remote that all the stretched polymers get enough time to complete the relaxation being back to the unstretched and curly conditions. Therefore, when polymers solidify, there are those still with stretched and tensile stress conditions and that is called residual orientation stress (or residual flow stress, residual filling stress).
(3) Describe the loading direction on the part at its application environment for mold design in gate number and position.
(2) In general, compared to thicker part, thinner part has polymer-oriented layer with larger proportion in thickness and more apparently behaves itself in anisotropic manner.
Plastic material is the material made of lots of chain-like polymers. Its molten condition can be imagined as a lump of “spaghetti”. Imagining ourselves as individual polymer chains in the one-shot lump of plastic material helps us understand what polymers experience and how they behave through the whole injection molding process, resulting in the part quality molded.
(2) Design cooling system (cooling channel size, position and layout) that creates balanced cooling effect at both sides of part and uniform cooling effect across the whole part.
In injection molding process, orientation is an inherent behavior, or phenomenon, of polymers within the molded part. Polymer orientation happens at melt filling stage and the driving force is the differential melt filling velocity layer to layer across part thickness. Fig. 1 illustrates the typical velocity distribution of filling melt (polymers) across part thickness. The bigger layer-to-layer velocity difference near mold wall (part surface) drives more polymer orientation, meaning that polymers are stretched more along the direction of filling. The smaller and smaller layer-to-layer velocity difference towards central region drives less and less polymer orientation, meaning that polymers are stretched less and less. At central region, where there is no layer-to-layer velocity difference, the polymers remain unstretched, curly and entangled as their original molten condition while filling.
Great info and good description. Could you please specify the following statement a bit further? (2) In general, compared to thicker part, thinner part has polymer-oriented layer with larger proportion in thickness and more apparently behaves itself in anisotropic manner. Would you say that a "thicker" part is 5+ mm or are you referring to 8-10 mm ? My experience is that a too thick part could cause warpage/deformation based on other problems maybe not directly correlated to the polymer orientation.
Having the basic understanding to the cause and effect of polymer orientation, some ideas are figured out as follows for part designers, mold designers and molders’ reference to make quality injection molding part from polymer point of view.
It provides an inherent cooling environment for polymers to cool under the same cooling rate at both sides of part and across the whole part, which allows the polymers cooled and solidified with symmetrical orientation stress relaxation and residual orientation stresses at thickness section all over the part, reducing the risk of part deformation and warpage caused by different amounts of residual stress relaxation at the two sides of part, or different amounts of local residual stress relaxation, after part ejected .
For multiple gates on a single part, the balanced melt filling pattern means that the filling melts from different gates meet each other and reach the extremities of part at the same time, creating the same degree of initial orientation stress all over the part. For multi-cavity mold, the balanced melt filling pattern means that, in addition to the filling balance within individual cavities, the filling melts in different cavities reach the extremities of individual cavities at the same time, creating the same degree of initial orientation stress on the molded parts from cavity to cavity.
Polymer’s orientation condition is the complicated effect caused by temperature, filling velocity and cooling rate exerted on the molded polymers.
The existence of polymer orientation effect within an injection molding part creates anisotropy on the molded part, meaning that the material properties are different from direction to direction on the molded part. For example, in general, the tensile strength of an injection molding part is higher in the direction parallel with polymer melt filling direction than that in the direction perpendicular to polymer melt filling.
(5) Keep the process conditions exerted on polymers - temperature, filling velocity and cooling rate - same so that the resulting polymer orientation stress within molded part is also the same from production to production.
(#InjectionMolding #Plastics #Polymer #PolymerOrientation #MoldDesign #MoldingProcessCondition #PartDesign #PlasticMaterial)
(3) With the loading direction of the part at its application environment assigned by part designers, mold design in gate number and position should make melt fills and polymers orient in the direction that is advantageous to the loading application at the finished part; or otherwise make it if polymer orientation effect is not preferred on the molded part.
GETTING A QUOTE WITH LK-MOULD IS FREE AND SIMPLE.
FIND MORE OF OUR SERVICES:
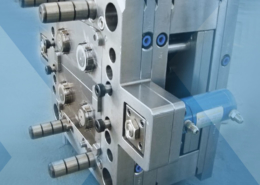
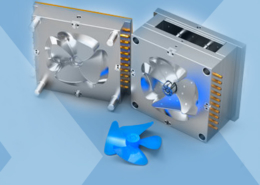
Plastic Molding

Rapid Prototyping
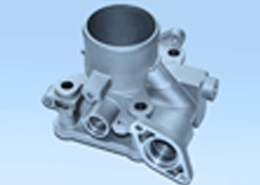
Pressure Die Casting
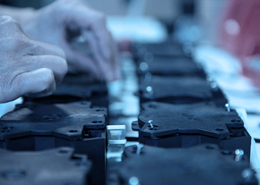
Parts Assembly
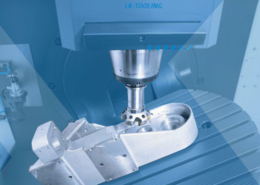