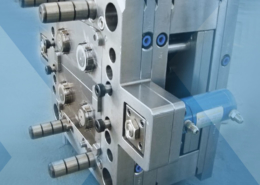
Car Bumper Injection Molding Machine - bumper injection molding
Author:gly Date: 2024-10-15
To achieve the ultimate capability and level of productivity from your wire EDM on a consistent, repeatable and reliable basis, regular maintenance is a required task.
As for plate thickness, leave at least 0.5in of steel between the upper and lowermost cavity extremities and the backsides of the cavity plates/cores. Depending on part geometry, you might need up to one full inch above and below the cavities for water lines.
Much needed information about the cost of plastic injection molds as knowing the price details are greatly helpful for the business.
I was wondering how many times your molds can be used? if i were to get a basic insert tooling mold would you be able to give me an estimate of how many times it could be used?
The need for data to track information and the history of the mold-building process is ever-increasing, and mold component solutions can help.
After attending IMTS, it's clear that the integration of advanced technologies is ready to enhance precision, efficiency and automation in mold manufacturing processes. It’s a massive event, so here’s a glimpse of what the MMT team experienced firsthand.
Formnext Chicago is an industrial additive manufacturing expo taking place April 8-10, 2025 at McCormick Place in Chicago, Illinois. Formnext Chicago is the second in a series of Formnext events in the U.S. being produced by Mesago Messe Frankfurt, AMT – The Association For Manufacturing Technology, and Gardner Business Media (our publisher).
Diamond compounds, with their varied grades, colors and base options, provide a comprehensive solution for mold builders in need of precise and superior polishing across diverse materials and applications.
Thank you for the inquiry. Mold balancing plays an important role in injection molding, because of that we would recommend a 24 cavity mold. The parts are divisible in pairs with that amount and will run much better. The ballpark estimate for a cold runner mold that size would be $15-$20,000, and the part price would be under $.09 each for 20,000 parts ordered.
However, needing 100,000 Xbox controllers every month is a different story. For this requirement, we would recommend building a 12-cavity hardened “family” mold, which would make four Fronts, four Backs, and four Button Trees every cycle. Of course, this type of mold comes with a cost. You’d better have $60-$80,000 or more to invest!
The most important reason to properly schedule and perform this routine wire EDM maintenance is to ensure consistent and repeatable machining results for the aforementioned machine traits of speed, accuracy and surface finish. This level of maintenance also prevents machine failure and unexpected machine downtime.
Hi, Thank you for all the valuable information laid out on your site. My company has created molds and manufactured exclusively overseas, but I have tried to bring my business back stateside many times and have always found it difficult, biggest issue being MOQs. When creating a new product as a small business it’s difficult to run thousands or tens of thousands of units on a first run for an unproven product. My question is, after the mold is produced what is the average MOQ? What is your typical floor? What are the determining factors for the MOQ?
If you wouldn’t mind, how much would you ball park the cost to produce the mold, and the parts, of a standard size plastic shopping cart? Needing 100,000-500,000 units per year. I appreciate your time.
Explore the standout articles of September, featuring innovations, expert insights, and strategies to boost efficiency and quality for your moldmaking needs.
A water-based, eco-friendly plastic mold cleaning system helps Rankine-Hinman Manufacturing restore flow rates and avoid big-ticket failures on complex and costly molds.
The EDM process priority refers to the desired metal removal rate, electrode wear and surface finish. This information helps the operator determine the best approach to the job. However, regardless of what is identified as the main priority, electrode size, detail and shape must be known in order to determine the appropriate machine parameters, including amperage, on time, off time, voltage and polarity.
If you’re thinking of outsourcing your mold-making overseas, consider all of the factors in bringing the mold to optimum production standards outlined in this American Mold Builders Association article. You might be surprised to learn the true cost of off-shoring!
EDM stands for Electrical Discharge Machining. A good way to describe the material erosion process of an electrical discharge machine is to think of the EDM spark as a shovel. Whether you are digging a hole or electrically removing material to form a cavity with an EDM, you remove material one shovel, or one spark, at a time. To dig a hole/cavity faster, you can use a bigger shovel (more power) or shovel faster (shorter pauses between sparks) or use a different-shaped shovel (electrical waveform).
We do not have minimum order quantities, but there are set up fees amortized into each order so the cost effectiveness of low quantity orders is a decision left to our customers.
These examples are extreme, but they illustrate the range of costs to anticipate. Your particular part will most likely fall somewhere in between that. At Rex Plastics, our molds average around $12,000.
Join MoldMaking Technology Editorial Director Christina Fuges as she gets the latest news on this mold builder's use of VR for mold design education.
Taking advantage of the latest EDM technology will allow you to remain competitive while improving surface finishes and accuracy—in addition to reducing cycle times in your shop.
In order to reduce downtime on its EDM and CNC machines when setting up new jobs, moldmaker Kavia Tooling turned to a coordinate measuring machine from Hexagon Manufacturing Intelligence to create an offline zero transfer system ahead of the manufacturing process for parts and electrodes.
The EDM process, much like other metal-removal processes, presents two main difficulties that must be overcome: heat and contamination. Each tiny spark creates heat, and the more power and the higher the frequency of the spark, the more heat is created. A good spark should take a large shovel out of the workpiece and a very small piece of the electrode.
hi I’m doing a school project and I need to know how much it will cost to make a simple 3,109 volumed container 12×14 container for the base and 12×14 for 2 sides and 14×20 for the other so 12=l 14=w 20=h
Identify pain points, tackle each one strategically and maintain flexibility to keep your moldmaking business on a path to growth.
Jake, That is impossible to say without looking at the design, but as a general rule of thumb if you need 1,000 or more per year injection molding is worth looking at.
Thank you for the request for quote, we appreciate the opportunity. Unfortunately this product is too large for us. The largest footprint we can mold is approximately 100 square inches.
Smart sensors and sophisticated process and measurement data management are driving intelligent moldmaking to new heights.
Intralox's integration of the Alpha Laser ALFlak has significantly improved their tool room efficiency when it comes to difficult welds and urgent repairs.
Thanks for this post, somewhat it helped me understand more about plastic injection mold and an estimation on how much it costs.
Nicole, Thank you for the inquiry. A Jackson Pratt bulb is blow molded, not injection molded. Please see this article for more explanation. https://rexplastics.com/plastic-injection-molding/the-many-processes-of-plastic-part-manufacturing
This webinar will provide an overview of new developments in hot runners, controllers, mold components, predesigned molds, process monitoring and mold maintenance equipment. These advancements are designed with the goals of lowering scrap rates, optimizing process temperatures and managing energy consumption. The solutions also aim to support productivity and may contribute to extending the operational lifespan of tooling equipment. Agenda: Innovative undercut and thread-forming components Predesign mold bases and plate control Melt delivery and control solutions Process monitoring and maintenance
Steel supplier discusses high thermal conductivity metal powders that also address the skills gaps via user-friendly materials and promote sustainability via durability and higher cycle counts.
Steel supplier discusses high thermal conductivity metal powders that also address the skills gaps via user-friendly materials and promote sustainability via durability and higher cycle counts.
But at least to some degree, asking what plastic injection molding costs is a lot like asking, “How much is a car?” Will your mold be a Pinto or a Porsche? And don’t forget that the price of a mold is just the beginning. To determine overall plastic injection molding costs for any project, you have to consider raw material, operation, and repair costs later down the road, too.
Gerardo (Jerry) Miranda III, former global tooling manager for Oakley sunglasses, reshares his complete mold design checklist, an essential part of the product time and cost-to-market process.
If your project requires large industrial molding machines that are operated by a service provider and large manufacturers, you’re looking at spending anywhere from $50,000 to $100,000+. Unlike the small desktop injection molding machine, these larger machines require professionals who can operate, maintain, and monitor the machine.
We could put multiple figurines in one mold but injection molding may not be the best process if you are anticipating low volumes. 1,000+ per year may start to make sense for injection molding, otherwise you may want to talk to a plastic prototyper or polymer casting company. We can mold them in any color, but the entire figurine would be the same color. If you have drawings you can attach them to our Quote Now link and we can provide a quote.
After attending IMTS, it's clear that the integration of advanced technologies is ready to enhance precision, efficiency and automation in mold manufacturing processes. It’s a massive event, so here’s a glimpse of what the MMT team experienced firsthand.
Thank you for the inquiry Ali. All of our molds have a lifetime guarantee so even if your mold wears, you won’t see a repair bill from us. Generally speaking a hardened steel mold or insert should last 100,000 cycles or more.
Join this webinar where Hexagon will explore how state-of-the-art CAD/CAM technology can drive your business forward. Learn how to optimize tool paths, enhance design accuracy and reduce lead times with advanced simulation. Discover the power of automation and real-time data for continuous improvement. Tailored for mold and die manufacturers, this session offers actionable insights to boost productivity and quality. Don’t miss this opportunity to gain a competitive edge in progressive die manufacturing. Agenda: Key challenges in progressive die manufacturing Optimizing tool paths Enhancing mold and die design accuracy Reducing lead times with simulation Automating processes for greater efficiency Leveraging real-time data for continuous improvement
When you consider that the speed of the EDM process may vary from 1,000 to 150,000 sparks per second, a machine that helps you choose the correct waveform, select the maximum power allowable by geometry, and automatically adjust the flush and cooling time between sparks is a pretty difficult machine to beat.
Incorporating multiple automation technologies enables Industrial Molds to produce and repair highly complex, precision molds with a very lean team.
The last thing to consider when pricing out your injection molding cost is the cost of service or professional labor you will need. Professionals can help you set up the necessary equipment to create molds and your products. During the process, they’ll be able to replace defective parts and monitor the progress of the overall process.
Great insights on the importance of precision in manufacturing. As a Welding and cutting machine manufacturers , Weldarc India understands the need for accuracy in welding and cutting processes. Our machines are designed to meet the demands of modern manufacturing with enhanced efficiency and precision. It’s exciting to see advancements in the industry that push the boundaries of what’s possible. Looking forward to continued innovations in welding and cutting solutions that contribute to high-quality production outcomes.
Thanks for helping me learn more about plastic injection molds. I didn’t know that molds should be made from harden steel if a product needs a fiberglass filled material. I’m interested to learn how these molds could be made, especially of the steel mold needs to be really precise.
Hi, what are the estimated costs of a mold for a part with snap fit connections compared to the same part but instead of snap fit connections holes for bolts?
I’m doing a project and I was wondering how much would the injection mold cost for a width:10 inch length:15 inch height 3 inches the top lid would be the same dimensions.
Your estimate cost for a steel p20, one cavity, cold runner, polypropylene 30%Gf matrix, with sizes of: 660mm x 220mm x 200mm. Thanks.
Good cleaning habits and care of a wire EDM machine is highly recommended. Regular and systematic cleaning of the machine also can extend the life of some consumable items.
Join MoldMaking Technology Editorial Director Christina Fuges as she gets the latest news on this mold builder's use of VR for mold design education.
Eloi, Thank you for the inquiry. Bottles are blow molded, not injection molded so we couldn’t answer that question. Here is a link to out knowledge base for more information: https://rexplastics.com/knowledge-base/product-development
Yes that is correct. After we build the mold (that you own), we store it here and run parts from it when you send us a PO.
There is a range of machines used for injection molding. The cheapest option is a small desktop injection molding machine perfect for in-house projects. A small desktop injection molding machine is the most cost-effective choice for producing low volumes of parts.
Thank you for the inquiry. That does sound like something we can help you with. If you could please fill out our request for quote page on this site we can provide a quote. You can upload drawings there as well.
The start-up costs for a large run can be expensive, but the price for the project becomes better and better as you continue to produce. If you’re looking at price per unit, plastic injection molding is one of the cheapest, most cost-efficient forms of manufacturing. With injection molding, the more units you create with your mold, the cheaper the price per unit becomes.
In order to understand what the injection molding cost of your project may be, you need to understand the process and factors that will affect the price of your project.
Discover how to enhance your mold design process with the right CAD/CAM tool for parting and cavity design. This webinar will explore CAD/CAM capabilities including how hybrid solid/surface modeling can streamline workflow and improve accuracy. Learn how to confidently tackle parting, runoff, and shutoff, ensuring precision and efficiency in your designs. Agenda: Part analysis QuickSplit techniques Parting and runoff strategies Shutoff solutions
Rienk, Thank you for the inquiry. That’s difficult to estimate without more information, but generally speaking snap fit connections will add $500-$1,000 to the cost of a mold.
The cost of the material you use for your project is usually decided by the design, material chosen, and the amount you need to complete the project. Here is a quick chart explaining more about each thermoplastic material, their features, common applications and price per pound.
I needed 1000 unit of enclosure (approx size 100 x 100 x 23 mm, fillet corner radius 20), Finishing should be fine as much as possible. I have seen the mould manufacturing costs a lot, is there any other way to manufacture enclosures at lower cost.
Burteck LLC experienced significant demand increases due to reshoring and invested in automated machining cells to step up its production output quickly and avoid losing business.
MoldMaking Technology Editorial Director Christina Fuges sits down with Murphy Forsyth, GM – Injection Molding and Director Of Marketing for Zero Tolerance LLC in Clinton Township, MI.
Hello, Just so I’m clear, you would charge for the creation of the mold, and then create the parts as needed/requested? You would see me back a finished product correct – as in you supply the materials, ship, etc? Thank you.
There are several wire EDM machine tool manufacturers, and there are some significant differences in the machine design of each. But the importance and type of basic items that need to be maintained on all wire EDMs are very similar. When planning and scheduling wire EDM machine maintenance, required actions can be grouped into short interval and long interval items.
Using data from a machine monitoring platform, Westminster Tool added almost 75 hours of capacity per week by shortening warmups and starting CNC and EDM machines sooner.
While you don’t need to know every detail about the types of molds available, it’s always a good idea to come prepared. Supplying the basics to your mold builder will help them build the best tool for your project. We recommend that you find a mold maker who also has production capabilities. The production company won’t want to build an inadequate mold because they know they must use it.
Moldmakers rely on electrical discharge machining (EDM) routinely. EDM refers to wire, sinker and small-hole EDM. Sinker includes an electrode and a workpiece both submerged in dielectric fluid; wire uses a thin wire to cut with electricity; and, with small hole an electrode is a cylinder used to machine a hole. Considerations for EDM efficiency include depth, accuracy and finish, and components to consider include drives, generator, programming system and flushing. Other facets include wires, electrodes, graphite, filters and fluids.
First you locate and orient the part in the tool, which mainly depends on where/how you intend to gate it. For all gate types except center, you should have at least 0.75-1.00in of space between the sprue and the edge of the cavity. Once you have a cavity layout (assume centered sprue), determine its bounding box. Any space off-center will need to be mirrored on the other side of the sprue and included in this bounding box. In a sense, you’ll always be sizing a mold for two cavities unless you’re center-gating. For smaller molds under 12in per side (in the parting plane), you can get away with leaving 2in of space all around this bounding box. This space is occupied by the ejector housing, return pins, and leader pins among other things, all of which would interfere with the part cavities and/or their ejection. You may need extra space for cooling lines as well. For larger molds up to 24in per side, you’ll want at least a 2.5in perimeter.
EDM refers to wire, sinker and small-hole electrical discharge machining. Components include drives, generators, programming, flushing, wires, electrodes, graphite, filters and fluids.
Hello, I have designed a product that I believe the best way to manufacture will be through injection molding. I cannot share too much, but for the sake of this comment lets imagine that it is a hollow box with 1/4″ walls, 1 face missing, and that it is 1′ 8″ W x 1′ 11″ L x 1′ 3″ H. Now I understand that pricing is complex so I won’t ask you for a quote without sending the file, and I will assume that the mold will cost no less than $50,000 which is fine. My questions are below: – Considering the dimensions of the extents, is it possible to create a family mold with multiple units? What would be the maximum units per mold? And around how many could be banged out per day (again assume its a 1/4″ wall box as stated above for now)? – How long does the process of making the mold take (assuming the design and specs are ready)? – Do I have to pay the full amount immediately, or can it be paid in installments? – If I were to send over a .dwg file for a quote, are you legally bound by confidentiality? Thank you in advance!
MoldMaking Technology Editorial Director Christina Fuges chats with Steve Michon, co-owner of Zero Tolerance in Clinton Township, Michigan, about the excitement of solving problems, the benefits of showing gratitude, the real struggle with delegation and the importance of staying on top of technology. This episode is brought to you by ISCAR with New Ideas for Machining Intelligently.
Thank you for the inquiry. That does sound like something we can help you with but would need more information. Can you provide drawings or a link to a similar product? If so please send them to [email protected]
Simon, Thank you for your inquiry. It’s difficult to say, but you might be about right. Features that will effect tooling cost are the finish you would like on the parts (polished is more expensive than textured), and where the drilling marks are located. If there are undercuts created by them in relation to the direction the part will need to be ejected out of the mold, moving cores would need to be designed into the molds, which will significantly increase the cost. If these concerns could be worked out, we could probably build two molds to shoot these sets for $30-$60,000. If you would like tighter figures, we would need to see drawings or prototypes. Thanks again for the inquiry.
I have an Idea…know nothing about this process, but here it goes. I wan’t to make a tool that will need Insert Molding? I know it’s a pricey operation, but to make it a durable and lasting tool it will have to be. I’d also like to have 6 to 8 tools made per cycle of the mold. the product would only be approx 5 to 6 inches long and 3/4 inch wide and approx 1/4 inch deep (approx). any idea (general idea) what this process would cost? I know there are many more details for plastic and metal applications, but a round about idea for a the mold would be helpful. Thank you.
We do mold with thermoplastic elastomers, which are still considered a plastic. It is more expensive than a lot of other types, and could add $.50 for a 100 gram part when compared to ABS.
Would like to mold adult male lacrosse stick heads, wondering how much each can cost, or how much a plastic injection machine would cost.
We have not made any golf disc parts specifically but that is well within our capability. Please contact us for a free quote if you are interested.
I’d be interested in finding out about plastic molded 9mm projectiles. There would have to be a denser plastic chosen, so there is enough recoil generated by the exiting projectile to cycle a semi-automatic pistol reliably.
I always enjoy reading quality articles by an individual who is obviously knowledgeable on their chosen subject. I’ll be watching this post with much interest. Keep up the great work…
Thanks for the inquiry. This post helping me understand more about plastic injection mold and estimation on how much it costs. And I learned from your post what an injection mold is made of.
Hi, I am interested in creating 6 different plastic figurines, each one in a 6 and a 12 in size. would I need to purchase a separate mold for each figurine and size? These would be low production, at least in the beginning, for retail and online sales. Are there options to have them manufactured in color? For example, skin tone, clothing and hair color?
Sinker and wire EDMs selected for speed, volumetric accuracy, surface finish, reliability, cost of ownership and extensive warranty.
Thank you for the request for quote, I appreciate the opportunity. I don’t know what that would take. The highest specific gravity for readily available material is around 1.4. I would recommend researching how that compares to what is currently used. I know that some law enforcement agencies are using rubber bullets now but I don’t know if any sort of ejection assistance is used. Please contact us via [email protected] if you’d like to discuss further.
Hi I’m trying to get a project started and luckily I found the guides and explanations here, good stuff. With the guide my estimate is somewhere between 15 000 to 30 000.
Hi, thanks for your contribution on Injection molding . I have basic knowlegde on mold design and would like to know how can I estimate overall mold dimensions based on part dimensions, considering one cavity mold and and no side actions. Also would like to know how can I estimate the approximate size of a slider for a side simple hole. Thanks for you support. Much appreciate. Regards
Would it be possible for me to request solely 2 units for my design initiative? They are quite large with a 1-meter diameter and 1.5-meter length. How much would it cost for the production of this?
After attending IMTS, it's clear that the integration of advanced technologies is ready to enhance precision, efficiency and automation in mold manufacturing processes. It’s a massive event, so here’s a glimpse of what the MMT team experienced firsthand.
Hi am new here, after I submit the CAD file will I pay $60 we part or I don’t understand. after making mold what part will I pay for again?
Since EDM is a thermal process, the melting point/temperature and thermal conductivity of the work metal can create difficulties for the EDM operator. Knowing the elements that make up the material will help determine the optimum melting point/temperature and thermal conductivity.
Thank you for the inquiry. If you submit CAD drawings we will provide a quote for the cost of the injection mold and production. Once the mold is built you own it and will only pay for production parts out of it. If the mold remains in our possession it comes with a lifetime guarantee. Hopefully this answers your questions.
Hi, Do you also provide molding with rubber or any other elastic material? Is it (NRE and price per part) usually more or less expensive than plastic ? tx, offer
how much would a console mold cost and how many would i need? Same with controllers… do i need enough to make 100,000 a month?
George, Thank you for the inquiry. This product is too large for us but I will try to answer your questions. -You can have a multiple cavity mold made for this part. If you built a four cavity mold you would need at least a 5,500 ton molding machine (and about $200,000 for a domestically made mold). -With that mold you would probably get four parts every 2 or 3 minutes. -A single cavity mold would still be over $50,000. -Normally toolmakers will ask for 50% down with the remainder due once samples out of the mold are approved. -Toolmakers and molder are not bound to confidentiality unless you have them sign a non-disclosure agreement. Hopefully this helps, good luck!
Discover how CAD/CAM functionality tailored for the mold industry can significantly enhance the mold design process. In part three of the webinar series, Cimatron will focus on designing waterlines and cooling components. It will demonstrate how CAD/CAM tools can verify drill line depths for water lines and baffles, ensure that minimum steel requirements are met while placing water lines, and provide a complete list of all baffle cutoff lengths. Additionally, it will explore how to confidently design runners and gates using CAD functionality specifically developed for these aspects of mold design. Agenda: Waterlines and verification Conformal cooling Baffles and charts Runners and gates
Without seeing the specific design it’s difficult to give an estimate. Sometimes even small design features can add thousands to the cost of the mold. If you have a drawing we could provide a free quote.
That’s why we’ve compiled the following price guide to help you budget for your mold. The injection molding cost examples are categorized by type (Rapid Prototyping, Insert Tooling, High-Production Tooling), and degree of difficulty (Basic, Intermediate, Advanced).
I’m working on a school project, I was wondering how much it would cost to make a mold that contains 25 cavities, the part is kind of cylindrical and I was planning to have it made out of high density polyethylene. It has a hole straight through the part with an inside diameter of 0.515″ and an outside diameter of 0.670″ for 0.773″ of the height and an outside diameter of 1.340″ for the remaining 0.327″ of the height, the height is 1.100″ total. This is the link to the photo: https://drive.google.com/file/d/0BxyuyPDgKAbnMXdHbE1GeTA5bms/view?usp=sharing https://drive.google.com/file/d/0BxyuyPDgKAbnN0xMSjJkNzdIUE0/view?usp=sharing
Hunter, That product would be too large for us, and would likely need to be extruded. Try searching http://www.thomasnet.com for a large capacity plastic extruder.
Small sidenote, plan on leaving at least 0.250in of metal around all water lines. If not maintained properly they’ll eventually corrode thin walls. This consideration has occasionally led us to quoting larger mold bases.
Thanks a lot for sharing this awesome info. Your article is excellent and informative. I love to read your articles.i personally like all the points you explain and follow it. Everyone should read this awesome post, I will share with my friends. Keep it up with such great content
Thank you for the request for quote, we appreciate the opportunity. The best opportunity we have to help make your project a success is if we have as much information as possible. If you could fill out the request for quote form on our website it will be a big step in that direction. It includes questions about material, annual estimated production quantities, etc. as well as the option to upload drawings or photos.
It’s easy to imagine the advantages automation offers the moldmaking process, but it's challenging to change one’s mindset, develop a plan and invest.
Hi, Thanks for your valuable post… I really appreciate your great work. This post helped me understand more about plastic injection mold and estimation on how much it costs. An injection mold is easily the most expensive part of the project, and can dramatically increase costs for small part runs. The main factors that influence the cost of an injection mold are the size and intricacy of the part, the material used, and the number of parts being produced.
The need for accuracy, finishes and repeatability are the biggest challenges moldmakers deal with. Electrode accuracy is incredibly important for high productivity and good product finishes. If an electrode is off by only 0.2", it will cause metal removal on one side of the cavity to work harder, leading to excessive burn time on the other side. Therefore, electrode manufacturing with better accuracy will help increase productivity and decrease burn times.
Five-axis electrode cutting enabled Preferred Tool to EDM complex internal screw geometry on an insert that otherwise would have had to be outsourced.
The $60-$80,000 is a non-recurring expense to build the mold. Once the mold was built you would just pay for production parts as need. Probably around $1 per set at that point.
A focus on electrode design and automation helps toolroom improve efficiency, reduce tooling costs and deliver higher quality products.
Kelsey, Thanks you for the inquiry. That’s difficult to say without seeing the part. Small details in the design can make big differences in cost to manufacture. If it is a simple design with no undercuts and the surface doesn’t require polishing, you could perhaps get a mold built for $5-$8,000. Here is a link to a pricing guide for further reference. https://rexplastics.com/injection-mold-price-guide
The adoption of Mitsubishi wire and sinker EDMs, along with the OPS Ingersoll five-axis milling machine with automated cells, has enabled unmanned operations and improved precision. As a result, QTD has expanded its facility, grown its workforce and increased its business by 10-15% annually.
Hi, Would you be able to create a mold for a golf bag, and provide a quote? Approximately 35″ tall, with a diameter of 11.5″ x 10″. I’d also like to include dividers in the middle. Thank you.
Engineers use properly preloaded bolts, blocks, springs and side-action cores to enhance functionality and reliability in various mechanical systems.
The work metal’s melting temperature and thermal conductivity require the EDM operator to adjust on-time, amperage, polarity, voltage and off-time parameters, which differ from one work metal to another. If the same EDM approach is used regardless of work metal, the end results could be vastly different.
Material selection is another consideration in determining what plastic injection molds cost. Any plastic product made from fiberglass-filled material, for example, will wear down most common molds. Only a mold made from hardened tool steel can withstand injection molding with fiberglass-filled material.
A connected software solution streamlines the moldmaking process by providing a unified source of design data, enhancing efficiency and reducing errors, with five key steps benefiting from this integration.
After attending IMTS, it's clear that the integration of advanced technologies is ready to enhance precision, efficiency and automation in mold manufacturing processes. It’s a massive event, so here’s a glimpse of what the MMT team experienced firsthand.
“On the other hand, if you are going to need 100,000 xbox controllers every month, we would build a 12 cavity hardened “family” mold which made four Fronts, four Backs, and four Button Trees every cycle, and you’d better have $60-$80,000 or more to invest.” is the 6o-8o,ooo dollars a yearly investment or a monthly investment?
Materials used in injection molding are plastics, specifically thermoplastics. There are hundreds of thermoplastics, but the most common thermoplastics used in injection molding are:
Thank you for the inquiry. Unfortunately this product is too large for us. The largest footprint we can mold is approximately 100 square inches.
I’m considering syringe barrels to be injection molded. About 3 mL and 6 mL (two different sizes) with qty of 20,000 per month for now. Actually syringe barrels without the thread, but with luer male at the end. Just empty straight (slightly tapered). Material PP.
I’m working on a school invention project and I need to know how much a mold for a half-pipe like design would cost. The thickness of the mold needs to be 1.5 inches, it is 1.5 feet high (bottom to top), 5 feet wide (left to right) and is 20 feet long (front to back). If you can estimate the price to the nearest thousand, that would be great. Thank you.
I understand that the small extrustion between the faces of the spheres could be an issue when removing the part from the mold, so they would not be a necessity. The geometrical shapes are just a collection of planar faces which create a sphere.
Riser height will depend on how far the ejection needs to push your part before it’s completely free of the cavity and any cores. Completely free in this case meaning pushed all the way out/off so that there’s no chance it’ll get hung up on anything.
When used for conformal cooling in plastic injection, 3D printing opens a wide range of design freedom. This design freedom enables designers to develop highly-efficient thermal regulation networks. However, this blessing also comes at the expense of not only higher manufacturing cost but also higher design cost as the designer could spend weeks to develop optimal cooling channels. This webinar will explore strategies and tools — including SimForm, a front-end thermal simulation app — to help tool designers and tooling managers maximize the benefits of 3D printing while minimizing manufacturing and design costs. Agenda: 3D printing applied to the plastic injection industry 3D printing pros and cons Tools and methods to facilitate the integration of 3D printing
If you have a target price established for your parts, tell your mold builder. They can design the mold accordingly and plan for the right number of cavities to achieve that price. The more cavities (or parts made per cycle), the less expensive the parts will be, also allowing for higher output.
I really like reading good articles by someone who knows a lot about what they’re writing. I’m excited to see more from you. Keep it up!
What EDM, automation and machining technologies are currently available to the mold manufacturing industry? MMT has compiled a list of some of the latest.
After attending IMTS, it's clear that the integration of advanced technologies is ready to enhance precision, efficiency and automation in mold manufacturing processes. It’s a massive event, so here’s a glimpse of what the MMT team experienced firsthand.
Thank you for the request for quote, I appreciate the opportunity. The best opportunity we have to help make your project a success is if we have as much information as possible. If you could fill out our request for quote form our website it will be a big step in that direction. It includes questions about material, annual estimated production quantities, etc. as well as the option to upload drawings.
IMTS 2024: The four-axis Edmmax818W wire EDM from EDM Network offers a solution for simple 3D cutoffs to precision dies and tooling.
Unfortunately this product is too large for us. The largest footprint we can mold is approximately 100 square inches, and the tallest piece around 10″.
This post helping me understand more about plastic injection mold and estimation on how much it costs. And I learned from your post what an injection mold is made of
For slides, start by sizing the slide face. This is the block which will have the undercut detail cut into it. The face doesn’t need to be much larger than the undercut itself, but it should be rectangular or circular just for ease of manufacturing and assembly. The surrounding part geometry could factor into this too, if the undercut is in a cramped spot or located near/on curved surfaces. Leave perhaps 0.375-0.500in of steel behind the undercut detail (same idea behind determining cavity plate thickness) and assume a 0.50-1.00in perimeter on either side of the face for other hardware like guide rails, and 1.0-2.0in above and below the face for wear plates, heel blocks and bolts. The slide may well take up more space than your cavities, and drive the mold size and plate thickness all by itself.
Hello, When submitting CAD specs to you or any injection mold company, do you recommend a Non-Disclosure Agreement be signed to protect a project?
Do you need design-for-manufacturing (DFM) assistance? Or, are you ready for production? We have a full suite of services to offer and a lifetime mold guarantee.
As a full-service plastic injection molding company that manufactures molds from conception to completion, pricing for each job we fulfill can vary dramatically.
It’s worth looking into the mold base CAD libraries out there, such as through PCS. They’ll generate full, downloadable 3D CAD of their offerings based on the specs you plug into their forms.
In ISO 9001 quality management systems, the Management Representative (MR) plays a crucial role. While the 2015 version of ISO 9001 no longer mandates this position, having a trusted management member serve as an MR remains vital for streamlining operations and maintaining quality standards.
Johnny, Thank you for the inquiry. Non-disclosure agreements are common in manufacturing so any molder you choose should not resist signing one unless it’s determined to lack certain exclusions and the ability of the molder to disclose information to third parties with written permission. Molders will often need to involve third party companies in order to provide a quote.
Chris, Thank you for the inquiry, I appreciate the opportunity. Without seeing the geometry it’s difficult to estimate cost. Our pricing guide can give an indication of cost, although it does not giving multi-cavity pricing.
MoldMaking Technology addresses the complete lifecycle of the manufacture and maintenance of a mold—from design to first shot—by providing solutions and strategies to moldmaking professionals charged with designing, building and repairing molds. About Us
Bottom line in regards to NDA is whether or not you trust the molder. If they are a legitimate company that has been around for a long time, they’re probably not stealing people’s ideas. If you are naturally a cautious person or something doesn’t seem right with the molder, you’ll feel better having one in place. Hope this helps, let us know if you have and NDA you’d like us to review or if you would like to look at the one we use.
Thank you for your inquiry. Here is a link to a pricing guide that will get you headed in the right direction. https://rexplastics.com/injection-mold-price-guide Rex Plastics, Inc
I’m glad you mentioned having a target price ready before designing a mold. I have a few things I want to start molding, but I hadn’t thought about a price yet. I can see how that would make a big difference in how they would plan how many parts to make.
In ISO 9001 quality management systems, the Management Representative (MR) plays a crucial role. While the 2015 version of ISO 9001 no longer mandates this position, having a trusted management member serve as an MR remains vital for streamlining operations and maintaining quality standards.
Understanding and facing the moldmaking industry’s obstacles to growth requires a strategy focused on increased profitability.
To achieve the ultimate capability and level of productivity from your wire EDM on a consistent, repeatable and reliable basis, regular maintenance is a required task.
Injection molding cost can range anywhere from $100 to $100,000+ depending on the scope and intricacy of the project. A small and simple single-cavity plastic injection mold usually costs between $1,000 and $5,000. Very large or complex molds may cost as much as $80,000 or more. On average, a typical mold that produces a relatively simple part small enough to hold in your hand costs around $12,000.
What would be the most logical approach if I wanted to create all four? All on one mold? Each geometrical type with their own mold? Then capacity wise, 10 000 a year? 100 000 a year?
Discover how to enhance your mold design process with CAD/CAM software specifically tailored for the moldmaking industry. In part two of this webinar series, Cimatron will demonstrate how to intelligently design mold components, such as slides and lifters, using powerful CAD/CAM tools to accelerate the design process. Additionally, it will cover how to avoid errors and ensure design accuracy for ejector pins by checking clearance distances, calculating cutoff heights correctly, and thoroughly documenting all ejector components. Agenda: Slides Lifters Inserts Ejection pins and charts
What I have is four different geometrical round shapes of varying face counts with some small extruded borders between the faces. They’d be hollow so they’d be cut in a symmetrical manner so that two printed halves can be glued together to form a whole hollow sphere. All spheres are around 7,5 cm in diameter, about 3 inches, and half that in height due to them being halves. Additionally they’d have holes in specific places on the spherical surface but that could be drilled aftetwards, so just some sort of mark where the holes are supposed to be would be sufficient.
Due to the electro-mechanical nature of wire EDM machines, there are several items in normal operation that routinely wear and require cleaning and/or replacement. If certain machine components are not properly cared for, machining speeds and accuracies will rapidly decay.
Steps to improve data-driven decision-making and key features of a cloud-based system for mold monitoring and asset management.
If you would like to send any drawings you have to our contact email directly we can provide an estimate. [email protected]
The determining factors in the cost of your mold are a combination of the part size, complexity, material, and anticipated quantities. For instance, if you wanted 1,000 washers per year, we would recommend a single cavity mold, meaning it makes one washer per machine cycle. In that case, the mold would probably be $1,000-2,000.
Released earlier, this video remains a valuable recruitment tool and is being re-promoted in celebration of Manufacturing Day 2024.
GETTING A QUOTE WITH LK-MOULD IS FREE AND SIMPLE.
FIND MORE OF OUR SERVICES:
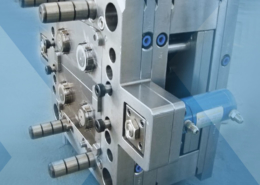
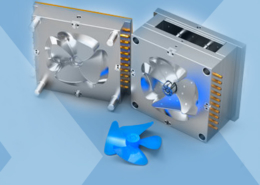
Plastic Molding

Rapid Prototyping
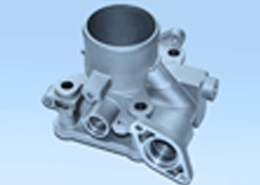
Pressure Die Casting
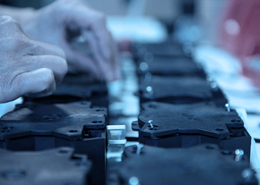
Parts Assembly
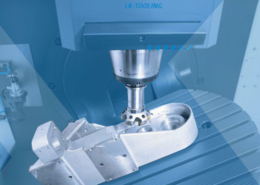