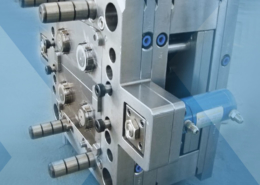
Can an injection molding machine produce PLA caps? - pla plastic injection moldi
Author:gly Date: 2024-10-15
A family-owned company created in 1971, Paulson Training is a global provider of workforce development solutions for the plastics industry.
LDPE is a highly flexible material. Its unique flow properties make it an excellent fit for shopping bags or other applications involving a thin plastic film. When strained, low density polyethylene will stretch, displaying this category’s high ductility and low tensile strength. LDPE melts between 110-130°C.
From the plastic’s point of view there are only 4 basic variables in the injection molding process – plastic pressure in the cavity, melt temperature, plastic flow rate and plastic cooling rate in the mold. These 4 basic variables are what determine the properties of the finished injection molded part.
At HiTech Plastics and Molds, we work with all the main types of polyethylene as an industry-leading injection molding manufacturer. As an ISO 9001:2008 certified company, we have the experience and knowledge to create high-quality custom plastic injection molded products that meet or exceed your strictest requirement.
As polyethylene is a thermoplastic, it responds to heat by becoming a liquid at its melting point. The specific temperature will vary depending on the chosen variety of polyethylene. Polyethylene materials can be melted multiple times, meaning that they are completely recyclable even after being used in an injection molding application. It is not recommended for applications requiring 3D printing.
Polyethylene is a semi-crystalline thermoplastic. As one of the most widely produced plastics in the world, it appears throughout virtually every industry. Polyethylene’s availability, versatility, and affordability make it a popular choice for injection molding manufacturers. PE is divided into categories based on density. In general, the higher the density, the higher the tensile strength, chemical resistance, and surface sturdiness. However, as polyethylene becomes denser, it also becomes more brittle in low temperatures. When solid, polyethylene is a non-toxic material.
As a general rule, the molder should fill the mold quickly to save cycle time. It’s a good rule up to the point where the fill rate is so fast that it starts to cause problems.
HDPE is an excellent option when you need a durable, stiff plastic that features a highly crystalline structure. HDPE is widely used and often chosen to manufacture milk cartons, laundry detergents, garbage bins, cutting boards, and more. High Density Polyethylene melts between 110-130°C.
Our team is involved from the ground up to create a molding solution to meet any requirement. We deliver high-quality products on time, every time. Read our case studies of past custom injection molded plastic projects to learn more about our work and what we can do for you.
Paulson presents at NPE2024's General Education Session and hosts Daily in-booth Molding Simulation demos Join us for...
There are three primary categories of polyethylene for injection molding: Linear Low Density Polyethylene (LLDPE), Low Density Polyethylene (LDPE), and High Density Polyethylene (HDPE). Each category has different characteristics, ranging from flexible to rigid, low impact to unbreakable. Which type is best suited for you will depend on your planned application.
With such a variety in polyethylene available for injection molding, the material can be altered and fit almost any industrial application. If you can imagine it, we can manufacture it. Common uses include:
The problem of jetting (which is also sometimes called “worm tracks”) appears as a line in the plastic part when the injected plastic fails to form a flow front. The plastic reaches the gate then shoots straight through the cavity rather than flowing smoothly with a well formed flow front. The solution to a jetting problem is to reduce the fill rate just as the plastic reaches the gate. Once a small flow front has formed the molder can increase the fill rate.
When plastic flows, the molecules orient, meaning they line up in the direction of flow. This is called molecular orientation . The faster they flow, the more they line up (orient). If the polymer molecules remain oriented, the molded part will be stronger in the direction of plastic flow but weaker in the transverse direction. If the parts crack, the cracks will form between the oriented molecules. The flow rate also affects the surface of the plastic part. A molded part defect called crazing shows up as tiny cracks. Crazing can show up days, weeks or even months after the part is molded. Crazing is caused by highly oriented plastic molecules trapped near the surface of the part.
All modern injection molding machines have fill rate controls on the control panel. The molder can use these fill rate controls to vary the plastic flow rate. Because flow rate is one of the 4 basic variables in molding it has a major effect on the directional properties and surface finish properties of the molded parts. By controlling the fill rate, the molder can solve molded part defects like jetting and burn marks. Fill rate can also be used to reduce the severity of weldlines.
down the final fill speed. In severe burn mark cases, it may be necessary to modify the venting in the mold. But the molder should always try the simpler solution of reducing final fill rate before taking the time (and expense) of modifying the tool.
In addition to injection molding manufacturing, polyethylene is used in many of HiTech’s available services and secondary services. Molding processes that can take advantage of the different polyethylene varieties include:
LLDPE shares many characteristics with LDPE but with several other benefits. Linear Low Density Polyethylene has an easy-to-adjust formula. This characteristic allows for lower energy usage during the overall production process.
Burn marks are created when air inside the mold cavities cannot escape fast enough. The air gets compressed so much that auto-ignition occurs. To fix burn marks using flow rate, the molder should slow
Contact us today to learn more about polyethylene or any other commodity-grade material. If you’re ready to get started on your custom-made polyethylene components, request a quote. We’ll manufacture the mold you need to keep your application producing efficiently.
When any of the defects discussed here occur, the molder who understands the scientific molding principles behind the injection molding process will analyze the problems on the basis of the 4 variables and then decide which machine controls need to be adjusted to solve the problems.
HiTech Plastics and Mold is your go-to trusted injection molding manufacturer when you need polyethylene injection molded products. We work with all the main types of polyethylene as an industry-leading injection molding manufacturer. As an ISO 9001:2008 certified company, we have the experience and knowledge to create high-quality custom plastic injection molded products that meet or exceed your strictest requirement.
GETTING A QUOTE WITH LK-MOULD IS FREE AND SIMPLE.
FIND MORE OF OUR SERVICES:
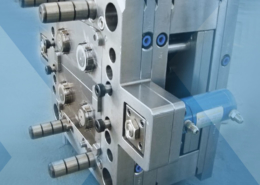
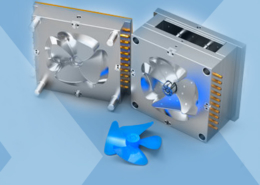
Plastic Molding

Rapid Prototyping
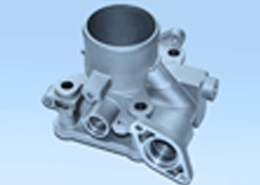
Pressure Die Casting
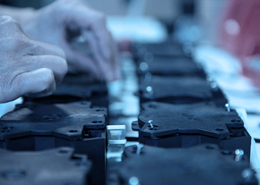
Parts Assembly
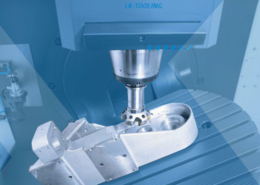