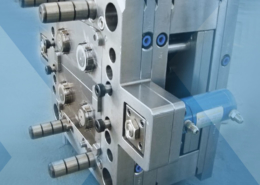
California - Plastic Molding Manufacturers - us injection molding companies
Author:gly Date: 2024-10-15
The rapid advancement of the medical industry necessitates constant innovation and complexity in medical device design. Smaller sizes, more intricate geometries, progressive functionalities, and portability are among the greatest needs in today’s medical equipment — and among the biggest challenges for design and engineering teams.
American consumers want to support companies that prioritize recyclability and sustainability. In a recent survey, 42% identify as eco-friendly purchasers.1 Given that the U.S. consumer products market is valued at well over $600 billion,2 the voice of nearly half of the customer base is an expensive one to ignore.
The paradox in the push for U.S.-based manufacturing is the shortage of skilled labor. An estimated 2.1 million jobs will be vacant in the manufacturing sector by 2030,4 and 54% of manufacturers already report significant difficulties in finding qualified workers.5
The labor shortage is a thorny issue, but it's given rise to forward-thinking solutions that allow for doing more with fewer employees. On the whole, industrial robotics isn't a new innovation. However, technological advancements have robots providing timely assistance and benefits to consumer market OEMs and injection molders alike:
Finding suitable replacements for nylon, acetal resins, polysulfone (PSU), polyphthalamide (PPA), polyphenylene sulfide (PPS), polyphenylene oxide (PPO), and syndiotactic polystyrene (SPS) isn't as simple as swapping out resins. It requires collaboration with your injection molder to qualify and test alternatives to ensure they are true solutions.
“Kaysun exceeded our expectations in all areas. They made a complex, gigantic program easy from an engineering standpoint. Working with the Kaysun engineering team is like a hot knife through butter.”
Leveraging the experience and knowledge of medical injection molders during the design phase of complex applications can help overcome the unique challenges of medical injection molding and improve outcomes.
Understanding the latest plastic injection molding industry trends — and partnering with a custom injection molder to apply them in creating highly differentiated products — translates to sustained success. It also gives you greater control over quality, cost, and time to market.
MedAccred is a Performance Review Institute medical device industry-managed supply chain oversight program dedicated to reducing patient safety risk. It focuses on critical manufacturing processes compliance and device quality and consistency.
Portable medical devices are a mainstay in hospitals, emergency vehicles, and outpatient environments. The devices must remain accurate and functional; however, drops, bumps, and excessive vibration are inevitable as equipment is transported from place to place.Overmolding is a proven solution for shock and vibration reduction, sound dampening, electrical insulation, improved chemical/UV resistance, effective oxygen and moisture barrier protection, and color infusion.
While these resin alternatives mimic many of the characteristics of traditional injection molding materials, their biodegradability also raises some concerns.
Medical device performance is largely dependent on the characteristics of the materials used and application needs such as strength, flexibility, transparency, biocompatibility, safety-enhancing microbe resistance, and temperature and chemical resistance. With thousands of engineered materials to choose from, it's important to work with experts in medical device injection molding.
For more on assessing the injection molding industry for consumer market new product development, download our tip sheet, What Type of Injection Molder Do You Need? Click the button below for your free copy!
Injection molding industry trends suggest that a number of factors influence applications within the consumer market, such as:
Medical OEMs are tasked with providing consistent, high-performance solutions to the challenges posed by a variety of complex applications. Partnering with a custom injection molder that has the experience, knowledge, technical expertise, and certifications needed to adhere to the exacting standards of the medical industry is imperative.Not every molder is qualified, but those who are — like Kaysun — can move your business forward with confidence.
Earning accreditation is a rigorous process, and only a small fraction of medical injection molding companies receive the distinction.
Consumer applications are diverse. Simply having products on the market isn't enough to build a customer base or keep pace with the competition.
Kaysun has carried the MedAccred Plastics accreditation since 2020, demonstrating our ongoing commitment to excellence and assuring medical OEMs of an unparalleled benchmark of production and quality standards.
Of course, reshoring experienced an uptick during the pandemic. Working with U.S.-based suppliers — even local injection molding companies — for the first time, or the first time in a while, reminded OEMs of the benefits of reshoring:
The duration of the resin shortage is unpredictable, compelling Kaysun to take problem-solving to the next level. For OEMs wishing to mitigate regional supply chain disruption, Kaysun offers collaborative global supply strategy development.
As with other industries, the consumer market continues to struggle with the impact of the unanticipated and prolonged resin shortage. The plastic injection molding market size isn't what it used to be.
Enter resin alternatives. Bioplastics made from renewable resources such as sugar, starches, and soy continue to gain traction in injection molding. Popular choices3 include:
Broadly speaking, suppliers from different countries of origin (typically at least one onshore and one offshore plastics supplier) are identified for materials fulfillment. Should a vendor not be able to fulfill an obligation, Kaysun already has a backup vetted and ready to step in to keep production timelines and project costs on track.
Durability can be an issue, as can cooling temperatures and moisture encountered during production. Injection molders with expertise in resin characteristics, behaviors, and selection can counter these measures with particulate fillers, reinforcing fillers, and other additives that change the structure of bioplastics without robbing them of their eco-friendliness.
The same group of American consumers that weighed in on the importance of sustainability also feel strongly about where products are made. "Made in the U.S.A." is a definite decision driver.
As medical device design evolves to provide ever-improving healthcare outcomes, manufacturers are partnering with full-service, experienced custom injection molders to gain increased design freedom and process efficiencies.Partnering with Kaysun — one of the few injection molders in the country to hold MedAccred Plastics accreditation — is a consistent value-add from part and tooling design through material selection and process control. It empowers many medical OEMs to address issues before they impact production or the bottom line.
Kaysun is experienced with medical product design, production, and assembly. We are ISO 13485:2016 certified and MedAccred Plastics accredited.
No doubt about it, new opportunities for consumer market applications present new challenges for manufacturers. Companies with loads of plastic injection molding industry experience, such as Kaysun, help you understand and incorporate the trends, processes, and resins that support your product goals, provide a competitive advantage, and help you innovate for the future.
GETTING A QUOTE WITH LK-MOULD IS FREE AND SIMPLE.
FIND MORE OF OUR SERVICES:
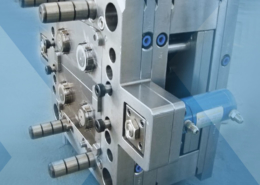
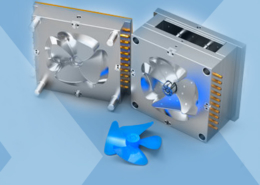
Plastic Molding

Rapid Prototyping
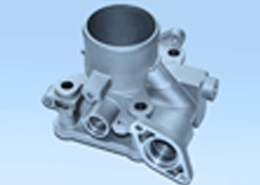
Pressure Die Casting
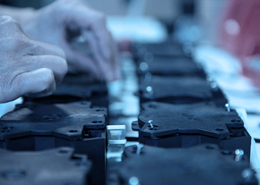
Parts Assembly
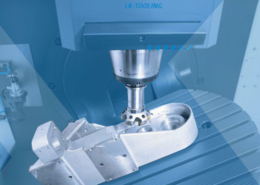