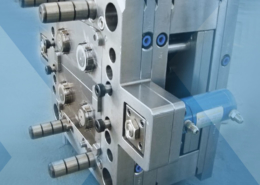
Bulk Injection Molding | Thick Wall Molding | Envirotech - large injection moldi
Author:gly Date: 2024-10-15
Small benchtop injection moulding machines start at around US$1,000, while larger, more complex models can cost as much as US$100,000.
ASA is renowned for its outstanding weatherability and UV resistance, making it highly suitable for outdoor use where it can maintain its color and physical properties over extended exposure to natural elements.
In the numerous plastic applications where mechanical strength and stiffness are essential, ASA and ABS are often the materials of choice.
Despite its lower UV and weather resistance compared to ASA, ABS remains a popular choice for indoor applications where these factors are less critical, and its use continues to be supported by ongoing research and improvements in plastic formulation and processing techniques to enhance its safety profile.
However, the major drawback of ABS is the intense fumes produced during printing, accompanied by issues like warping, hence it’s recommended to print in well-ventilated areas.
ASA can withstand degradation, aging, and fading caused by UV exposure, while also offering robust protection against decomposition or discoloration due to oxidation in the atmosphere and high temperatures during processing.
Sourcing raw materials for injection moulding may also involve customisation and blending of materials to meet customer requirements. These customisations may result in additional costs and therefore need to be carefully considered when contemplating such requests. To optimise the procurement process, companies may choose to establish long-term relationships and contracts with suppliers to reduce costs and ensure continuous supply
The substitution of rubber double bonds plays a pivotal role in defining the subtle yet significant differences in performance between ASA and ABS.
Another important piece of quality control equipment used in plastic injection moulding is the Melt Flow Indexer. This device is used to measure the flow of molten plastic during the injection moulding process. The cost of the MFI meter ranges from US$5,000 to US$15,000.
Additionally, ABS’s composition allows it to be recycled, reducing its environmental impact compared to materials that cannot be easily processed for reuse.
Saving money on injection moulding can be helpful, but it is important to develop a strategy around where you are saving money. In order to maintain a cost-effective strategy for low-cost injection moulding, it is just as important to identify the areas where you want to save money Money can lead to bigger problems as it requires finding areas to reduce costs. The following tips will help you address both issues:
ABS, known for its high impact strength and mechanical robustness, is the material of choice for consumer goods, automotive parts, and electronic housings.
In conclusion, the cost of mould design and development is an important factor to consider when starting an injection moulding business. It is critical to work with a reliable and experienced mould maker who can provide high quality moulds that meet the specific requirements of the product design. The cost of mould design and development can be affected by a number of factors and it is advisable to calculate the total cost per part to determine the profitability of the business.
ASA’s fire resistance is about ten times higher than that of ABS, with a fire rating of B1 level, meeting the basic fire protection requirements for residential housing, which ABS does not achieve.
Pre-purchase replacement components. This will be an additional cost, but you'll end up spending less in the long run. Think of it as a form of insurance because you are preparing for the worst.
As the application scope of ASA and ABS continues to expand, concerns about safety hazards in plastic products have arisen: Is ASA toxic? Is ABS safe?
The acetone smoothing method, known for achieving a high-gloss surface effect on ABS, is equally applicable to ASA materials. ASA injection molding products do not require painting, plating, or other surface protection and can be used outdoors directly.
Raw material costs may vary depending on the supplier, material quality, and quantity ordered. It is important to note that ordering material in bulk will reduce unit costs; however, ordering excess material may increase storage and maintenance costs.
In the following content, we will delve into the performance of these two materials and comprehensively evaluate their performance in specific application scenarios.
One of the most important pieces of quality control equipment in plastic injection moulding is the co-ordinate measuring machine (CMM). This machine is used to measure the dimensional and geometric characteristics of the parts produced. CMMs come in a variety of sizes and complexities and cost from $10,000 to $100,000.
According to a recent industry report, the plastic injection moulding market is expected to grow significantly in the coming years. This growth is attributed to the growing demand for plastic products in various industries such as automotive, healthcare, packaging, and consumer goods. However, despite the increasing demand for plastic injection moulding services, many aspiring entrepreneurs are still hesitant to enter the industry due to high start-up costs. In this blog post, we will discuss the costs associated with opening a plastic injection moulding business and provide some insights on how to manage these costs effectively.
It is important to note that mould design and development costs are one-off costs, as the mould can be reused over many production runs. The cost of mould design and development is spread over the life cycle of the product. Production volume also affects the total cost per part. Due to economies of scale, the cost per part decreases as production volume increases.
Technically, ASA not only retains the main properties of ABS but also incorporates the weather resistance advantages of PMMA plastic, extending its application to outdoor uses.
Webinars and Online Training: Webinars and online training courses can provide cost-effective and flexible training options for employees. These can be live or on-demand courses where participants can access training materials and interact with trainers via the Internet.
Due to its unique structure, ASA offers similar chemical resistance to ABS but with better weatherability and UV resistance, which can translate into better long-term performance and safety in outdoor applications.
One of the biggest expenses when starting a plastic injection moulding business is the cost of the injection moulding machines themselves. These machines are essential for producing a wide range of plastic parts. Depending on the type of machine and its output, the cost of an injection moulding machine can range from a few thousand dollars to hundreds of thousands of dollars.
For medium-sized plastics moulding companies that require a range of injection moulding machines with different capacities and features, costs can add up quickly.
Maximise design efficiency. During the concept phase, it's important to focus on the essential features that ensure optimal part performance. You may come across elements that can be categorised as 'nice to have', but may not contribute to the market value of your part.
We place great value on our relationships with our customers and our team is always committed to providing excellent customer service. We believe that it is only through understanding and meeting the needs of our customers that we can build long-term relationships.
Outstanding UV resistance and anti-aging capabilities mark a significant advantage of ASA and represent one of its largest differences from ABS plastic.
Consider the relevance of the part's appearance. Glossy or shiny finishes look good, but are they critical to your project? If they don't translate into increased sales, you might consider removing them.
Additionally, for general purposes, it can be found in home appliances, hulls, decorative items, toys, and the renowned LEGO bricks.
Mould design and development is another important one-time cost when starting a plastic injection moulding business. Moulds are the tools that shape the plastic and form it into the desired product. The cost of a mould may vary depending on its complexity, design requirements and the number of parts to be produced. Mould costs can range from a few thousand dollars to tens of thousands of dollars.
Reuse plastic waste. Using plastics that harden in the gates and runners and are cut off in reprocessing can help reduce material costs. However, plastics and their additives lose a small percentage of their mechanical properties each time they are recycled, so they cannot be recycled too many times. For example, glass filler fibres become shorter when used in recycled plastics, which can lead to a reduction in properties such as tensile and impact strength. Studies have shown that these two properties can be reduced by up to 40 per cent after multiple recycling steps (eight in the study above).
In addition to the above, other quality control equipment used in plastic injection moulding includes spectrophotometers, hardness testers and density testers. The cost of these equipment ranges from US $500 to US $10,000.
In order to control costs, it is important to carefully assess a business's equipment and infrastructure needs and develop a budget that considers all necessary expenses. It may also be helpful to seek the advice of industry experts and consult with experienced plastic injection moulding business owners to gain insight into the most cost-effective strategies for starting and growing a successful business.
Know your tooling budget in advance. When dealing with a manufacturer, it is best to be open about what you can afford from the start. It is important to remember that plastic injection moulds are expensive, so you are unlikely to save much of your budget on this part of the process. However, the cost will depend on the application and whether you want to make thousands of parts or millions.
Plastic injection moulding companies may choose to obtain raw materials through international suppliers to reduce costs.
The cost of training and development programmes varies depending on the size of the company and its requirements. On average, manufacturing companies spend about $1,000 to $1,500 per employee per year on training programmes. This figure includes costs associated with materials, trainers, and facilities.
In addition to the above costs, you will need to consider the cost of raw material purchases, testing and quality control equipment, factory equipment and infrastructure, employee training and development, inventory management, IT systems for transport and logistics, and marketing and logistics. Advertising costs for customer promotion. These costs can add up quickly, so it's vital to plan your budget effectively and manage your cash flow carefully.
In terms of health and environmental safety, ABS does not contain any known carcinogens and is generally considered non-toxic when it is in its solid form.
This comparison highlights the key differences between ASA and ABS; for more insights into plastic materials, stay tuned to FOWMOULD!
Raw materials play a vital role in the plastic injection moulding process. Raw material procurement includes bulk purchase of granules, powders, additives, colourants and other required materials. A significant portion of the manufacturing cost of injection moulding includes the cost of raw materials. Raw material procurement is a critical aspect that requires careful attention.
Injection moulding machines are the backbone of any plastics moulding business, and their cost can vary greatly depending on their size, capacity and features.
In the United States, the average cost of polypropylene, a thermoplastic commonly used in injection moulding, is $0.55-$0.65 per pound. High-density polyethylene (HDPE) costs about $0.70-$0.80 per pound. Acrylonitrile butadiene styrene (ABS) costs up to $1.50 per pound. For polycarbonate (PC), the cost ranges from $1.50 to $2.30 per pound, depending on quality and grade.
ABS is celebrated for its robust mechanical strength and stiffness, making it suitable for durable products, alongside notable impact resistance, even in cold environments.
The company may also make prior arrangements with local distributors who source materials from multiple suppliers so that they can diversify their supply lines and maintain competitive pricing.
As with any business, staff training and development is vital to the success and growth of a plastic injection moulding business. It's important to invest in regular training programmes to keep your staff up to date with the latest technology, industry standards and best practices. Employees who participate in training and development programmes can increase productivity, efficiency and innovation, which in turn can increase your company's revenue.
Compared to ABS, ASA significantly improves weather resistance by substituting butadiene rubber with acrylate rubber, which lacks double bonds.
ABS has been noted to emit styrene during printing, a VOC with potential health risks in poorly ventilated spaces, while ASA is often regarded as having a less intense odor but still requires proper safety measures.
If you are planning to start a plastic injection moulding business, you need to understand that there are some one-time costs that you will have to pay before you can start operations. These costs may vary depending on the size and scope of your business, but typically include everything from purchasing injection moulding machines and raw materials to hiring and training employees and investing in the necessary equipment and infrastructure.
There are many types of training and development programmes that plastic injection moulding companies can consider. On-the-job training is the most common type of training, where employees learn skills and knowledge while performing daily tasks. For example, a new operator may learn machine functions and safety procedures under the guidance of a trainer or experienced co-worker.
Classroom Training: Classroom training is a formal training method that involves educational activities conducted in a training facility or classroom. This type of training is valuable for theoretical training for new employees as well as for professional training sessions for experienced employees.
It is important to note that the cost of testing and quality control equipment is a one-time investment for an injection moulding operation. However, it is important to ensure that the equipment is of high quality and meets international standards. Investing in high-quality equipment can help reduce production costs and improve the efficiency of the injection moulding process. It also helps in attracting more customers as they can be assured of getting high quality products.
In addition to basic equipment and infrastructure costs, there are many other expenses associated with running a plastic injection moulding operation. These include the cost of raw materials, machine maintenance and repairs, employee wages, and marketing expenses. The total cost of starting a plastic injection moulding business can range from $100,000 to over $1 million, depending on the size and scope of the business.
Opening a plastic injection moulding business may seem daunting, but with the right planning and preparation, it can be a rewarding and profitable venture. By understanding the one-off start-up costs and developing a viable business plan, you can set your business up for success and growth in this rapidly expanding industry.
Investing in employee development opportunities can also include leadership and management training for team leaders and managers. This type of training can help them effectively define goals, set expectations, motivate and lead their teams. Companies can hire outside consultants, coaches or industry experts to provide additional perspectives and insights into leadership, operations and management practices.
It's worth noting that some manufacturers may choose to lease equipment and infrastructure rather than purchase it outright. This can help reduce upfront costs, but may result in higher ongoing costs due to interest payments and the need to return the equipment at the end of the lease term.
Look for reputable companies. Many reputable suppliers have on-site tool repair capabilities, which can be valuable when tools start to wear out and break. A reputable molder can guarantee that your tooling will last for 50,000, 100,000 or even a million cycles, depending on the company.
Consider insert moulding. This works by inserting a product into a mould and encapsulating it in plastic. This gives you the option of applying the injection mould to both products by using inserts. These inserts can then be removed or placed in different areas depending on the given cycle. This is a very versatile technique that can help reduce costs.
Another important cost to consider is the infrastructure required to operate the injection moulding machine. This includes the cost of electricity, water and ventilation systems, which are critical to the safe and efficient operation of the machine. The average cost of infrastructure for a small to medium-sized injection moulding plant is between US$50,000 and US$100,000, while a large plant may require infrastructure costs of up to US$500,000.
If you have any questions about our products or services, please feel free to contact us. We look forward to working with you to advance the plastic bottle manufacturing industry.
Mould design and development is a critical stage in the plastic injection moulding process. The mould determines the shape, quality and accuracy of the final product. The cost of mould design and development may vary depending on various factors such as the complexity of the mould, the materials used and the lead time. However, according to recent statistics, the average cost of mould design and development is approximately US$12,000 to US$50,000.
On the other hand, ASA boasts strong UV and impact resistance, making it suitable for various outdoor installations such as signage, sports equipment, and automotive exterior applications.
ASA shares these strengths but stands out for its enhanced toughness and better integrity under UV exposure, especially in outdoor settings.
In terms of heat resistance, ASA and ABS are relatively similar, with ABS having a heat distortion temperature of 93~118°C and still displaying some toughness at -40°C.
We are convinced that only through continuous learning and improvement can we remain at the forefront of our industry. Therefore, we always keep abreast of the latest technology and market trends to ensure that our products and services remain at the forefront of the industry.
Our product line includes fully automatic bottle blowing machines, injection moulding machines, pre-made moulds and so on, which are designed and manufactured by our professional team. Our team has the experience and expertise to provide our customers with customised solutions to meet their specific needs.
Therefore, it is recommended to use ABS in well-ventilated areas and follow safety guidelines to minimize exposure to these emissions.
Starting a plastic injection moulding business requires significant investment in equipment, employees and infrastructure. The chart below shows some of the major start-up costs associated with launching a plastic injection moulding business, noting that these costs are only estimates and may vary depending on the size and complexity of the operation. It is important to conduct thorough research and develop a detailed business plan to accurately estimate the start-up costs associated with a plastic injection moulding business:
Lead time is another factor that affects mould design and development costs. In the injection moulding industry, lead time is the time between placing an order and delivering the final product. The longer the lead time, the more expensive the mould design and development costs. Faster lead times mean that moulds must be designed and developed quickly, which can affect the quality and accuracy of the final product.
In additive manufacturing, its other common uses include prototyping, gears, and even tools, as it offers better resistance to physical stress than some other common 3D printing polymers.
The cost of mould design and development can be affected by the type of thermoplastic material used. The cost of a mould for a product made from a low-cost material such as polypropylene will be much cheaper than a mould for a product made from a high-cost material such as polyetherimide. Mould design and development costs may also be higher for complex designs with complex geometries.
Its electrical insulation properties also make it attractive for those looking to manufacture casings for electrical components, as well as automotive parts like dashboards or bumpers.
ASA contains modifiers in its composition that enhance its resistance to UV-induced fading and yellowing, making it more suitable for applications where long-term aesthetic appeal is important.
ABS and ASA both exhibit good thermal stability during processing, but ASA’s enhanced resistance to UV light can translate to better long-term thermal stability in outdoor applications.
Testing and quality control equipment is an important part of the plastic injection moulding process. It ensures that the products produced meet the required specifications and are of high quality. The cost of test and quality control equipment varies depending on the size and complexity of the equipment. The cost also depends on the manufacturer and country of origin. On average, the cost of quality control equipment ranges from $500 to $50,000.
ABS plastic is a terpolymer made from acrylonitrile (A), butadiene (B), and styrene (S), combining the properties of PB, PAN, and PS to create a material with a balanced set of mechanical characteristics that are tough, hard, and rigid.
Sourcing raw materials from multiple suppliers allows a company to obtain the best price and ensure a continuous supply.
This is TEPAI, a factory specialising in providing high quality plastic bottle manufacturing machinery. Our goal is to help our customers improve production efficiency and reduce production cost through innovation and excellent service.
As we’ve mentioned, one of the main attractions of ABS is its technical nature, which tends to steer its applications towards industrial uses.
The capital for the equipment depends on what kind of orders are received, and the products that are highly requested depend on whether the equipment to be bought is needed, with expensive injection moulding machines costing hundreds of thousands of dollars and more than a million dollars a piece of the budget. China's production of machinery, then a lot cheaper, you can learn more about a few brands. Plant area depends on how much equipment to buy to do the plan, a lot of equipment factory can also give you some advice on plant planning!
The cost of plant equipment and infrastructure is a key factor to consider when starting a plastic injection moulding business. The cost of equipment varies widely, depending on factors such as the size of the company and the type of machinery required. According to recent statistics, the average cost of plastic injection moulding equipment ranges from approximately US$75,000 to US$300,000. This cost can rise significantly if additional features and customisation are required.
Overall, both ASA and ABS are versatile thermoplastic polymers that, despite their similarities, possess unique characteristics to meet different application needs.
While both materials have the drawback of emitting fumes during processing, especially in 3D printing, this issue can be mitigated with appropriate safety measures.
ACIS®, Autodesk Inventor®, CATIA® V5,Creo™ Parametric, IGES, Parasolid®, Pro/ENGINEER®,Siemens PLM Software’s NX™, SolidEdge®, SolidWorks®, STEP
Yet, printing with ASA typically demands higher extrusion temperatures, and it is pricier compared to ABS, necessitating a balance between cost and application needs when selecting plastic materials.
GETTING A QUOTE WITH LK-MOULD IS FREE AND SIMPLE.
FIND MORE OF OUR SERVICES:
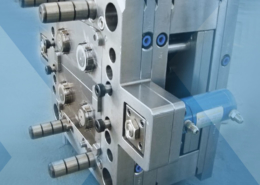
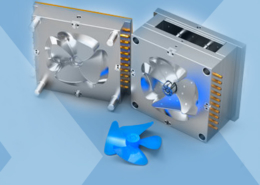
Plastic Molding

Rapid Prototyping
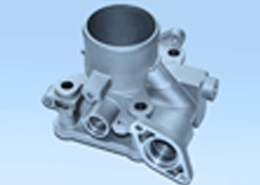
Pressure Die Casting
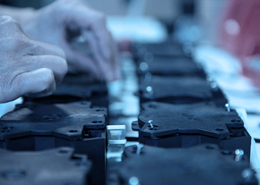
Parts Assembly
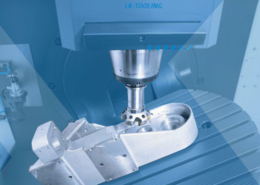