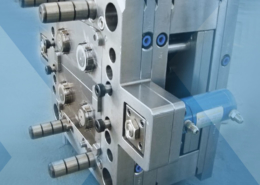
Browndog's Custom Tackle – Browndog's CustomTackle - soft plastic mould
Author:gly Date: 2024-10-15
What’s more, components for the medical field require various chemical properties, such as high tensile strength, resistance to very high temperatures, and others. Plastic injection molding is suitable for this field of applications because the parts have:
Parts used in the food and beverage field must follow stringent health and safety rules and regulations, such as the GMA-safe program and FDA certification. All this is necessary to ensure the wellbeing of individuals using such products. To abide by the aforementioned standards, molded parts have to be BPA-free and completely non-toxic.
The benefit to manufacturers is clear. Even a very successful automobile manufacturer is not going to produce enough cars to justify the expense of setting up an internal p It is not only product manufacturers that require the services of plastic moulding contractors. Many other industries such as in the pharmaceutical sector require supplemental plastic products such as containers for medications. A pharmaceutical company might contract an injection moulding company to produce a range of specialised containers for a new product. Moulds can be kept in storage so that if the product is successful further production runs can be made.lastic moulding production unit. Such a unit might only need to be running for a few months or even weeks out of the year. Having expensive injection moulding equipment sitting idle for long periods of time is far from cost effective and such equipment can require a degree of maintenance.
Comar, Headquarters, Comar, 220 Laurel Road, Voorhees, NJ 08043, US Tel:1-800-962-6627 Email: info@automaticplastics.com
Injection molding various construction and building components is becoming increasingly popular due to the innate versatility of plastic injection molding. There are many reasons why this method is suitable for use in construction:
Some of the most commonly-produced elements in the construction industry include small and large accessories, fasteners, and various hand tools.
The most common parts produced with this process include testing kits, surgical preparation products, dental X-ray components, and many more.
Plastic injection molding is a process so widely used that you can find parts and components made with it in almost any environment and setting. However, this is only one of the amazing facts about plastic injection molding. This manufacturing process is so popular because it offers numerous advantages over other plastic-making methods, and these advantages will only increase with all the current and future trends in plastic injection molding.
Contract moulding is the process whereby a company contracts out the production of specific plastic injection moulded components to a plastic injection moulding specialist company. An example might be where an automobile manufacturer owns and operates the factories that produce and manufacture the mechanical parts of a vehicle such as the engine and gearbox as well as the main structures such as the chassis and suspension they are likely to contract out the production of smaller components such as wing mirror casings and door panels to specialist contract moulding companies.
These components have to be both decorative and functional, which means the manufacturer has to achieve the balance between aesthetics, usability, and durability. The components you can create through plastic injection molding are so varied it’s difficult to name the most common ones. Some of the frequently used parts are product stops, hooks for pegboards, shelf dividers, but also many more.
That’s why you need to act now and find a reputable company to outsource your molding needs to. Wunder Mold is one such company. We create durable and long-lasting plastic components and parts using advanced technology, molds, and materials. We listen to your needs and follow your specs to give you the exact product you require. Send us an email at sales@wundermold.com or reach out to us via phone.
Plastic injection molding is an extremely versatile manufacturing process, meaning the components it produces come in all shapes, sizes, and intricacies. This makes this process very popular and widespread across many applications and industries. The parts made through partnership with a plastic injection molding company near you are strong, durable, long-lasting, and suitable for different uses, some of them more frequent than others.
This website uses Google Analytics to collect anonymous information such as the number of visitors to the site, and the most popular pages.
APL, A Comar Company, School Rd, Lugduff, Tinahely, Co. Wicklow, Y14 HE29 Tel:+353 (0) 402 38231 Email: info@automaticplastics.com
Due to its innate design flexibility, but also high durability and longevity, plastic injection molded parts are very frequently used in the automotive industry. This process makes it easy to design and create various items you find in and on your car every day, such as mirror housings, cup holders, bumpers, but also entire dashboards.
Similarly to the food and beverage industry, plastic parts made for the medical and pharmaceutical field have to follow even more stringent guidelines. In order to meet those standards, manufacturers must use FDA or medical-grade resins and manufacture their components according to ISO certification.
Plastic injection molding has a crucial role in development and manufacturing of numerous products and components, from airplane components to consumer toys and electronics. Here are the most common applications of parts created through this process:
That’s why it’s important to choose the right resins and materials to produce those elements that will be used in this industry. The most commonly-manufactured parts for this industry are:
This website uses cookies so that we can provide you with the best user experience possible. Cookie information is stored in your browser and performs functions such as recognising you when you return to our website and helping our team to understand which sections of the website you find most interesting and useful.
Or another example may be where a medical device company outsources their medical device injection moulding for a specific component.
A contract moulding company will make plastic injection moulded products for several different companies possibly in many different sectors over the course of the year meaning equipment is used constantly and is far more cost effective both for the plastic manufacturer and the companies they supply.
If you consider the typical manufactured product in a person’s house that they may use every day, a washing machine, a television, a vacuum cleaner, each of these products is made from hundreds , if not thousands of different parts. Electrical components, metal components and plastic components are assembled to form one complete product. It would be infeasible for one single company to have manufacturing facilities capable of producing each of these components from raw materials. The structure of global manufacturing means that the use of services such as makes the production process much more efficient.
If you disable this cookie, we will not be able to save your preferences. This means that every time you visit this website you will need to enable or disable cookies again.
Another advantage contract moulders have over in-house moulding is their breadth of experience. Working with many different industries gives moulding companies a greater understanding of the potential pitfalls and difficulties that may be faced by a given project. For this reason many injection moulders provide project management services. This service can be of varying degrees of comprehensiveness. Typically it would include other services such as design and mould flow analysis. Specialised design software allows for the most efficient and cost effective moulds to be produced. Mould flow analysis also uses specialised software that models the way in which polymers will flow through a given mould. This allows manufacturers to see where potential weak points may occur and where greater efficiencies might be made it the design of the mould.
GETTING A QUOTE WITH LK-MOULD IS FREE AND SIMPLE.
FIND MORE OF OUR SERVICES:
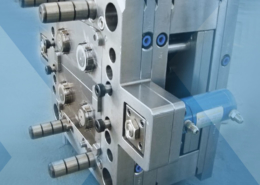
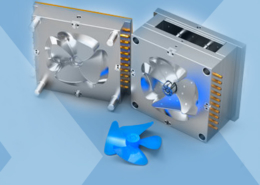
Plastic Molding

Rapid Prototyping
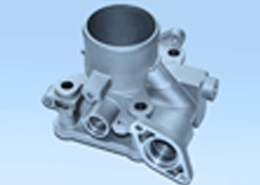
Pressure Die Casting
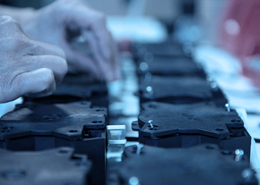
Parts Assembly
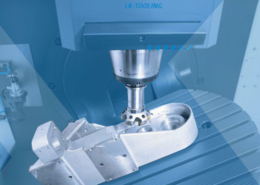